Fronius setzt auf automatisierten Palettentransport mit AMR
für eine flexible Produktionsversorgung
Fronius ist weltweiter Technologieführer für Batterieladetechnik, Schweißsysteme und Solarenergie. Die eigentümergeführte, österreichische Firma wurde 1945 gegründet und hat 37 Tochtergesellschaften auf fünf Kontinenten. Im Jahr 2022 beschäftigte das Unternehmen 6.100 Mitarbeiter:innen weltweit. Neben dem Firmensitz in Pettenbach und weiteren Standorten in Wels, Thalheim, Sattledt und Steinhaus besitzt Fronius einen Fertigungsstandort in Tschechien.
Am Standort Sattledt fertigt Fronius Schweißgeräte für die Industrie, Wechselrichter für Photovoltaikanlagen und Batterieladegeräte für Flurförderzeuge. 2022 wurde die bestehende Fertigungshalle um eine weitere Halle mit 28.000 m² erweitert. Um die Halle effizient zu erschließen, automatisierte Fronius den Palettentransport mit unseren AMR, den Open Shuttles.
Sie sehen gerade einen Platzhalterinhalt von YouTube. Um auf den eigentlichen Inhalt zuzugreifen, klicken Sie auf die Schaltfläche unten. Bitte beachten Sie, dass dabei Daten an Drittanbieter weitergegeben werden.
Mehr InformationenOpen Shuttle Fork für die optimierte Produktionsversorgung mit Paletten
Bei Fronius am Standort Sattledt wurde 2022 die bestehende Fertigungshalle mit 41.000 m² um eine Halle mit 28.000 m² erweitert. Gesucht wurde eine Lösung, mit der die neue Halle erschlossen und die Produktionsinseln schnell und flexibel mit Paletten versorgt werden können. Zudem wollte man den Wareneingang und -ausgang automatisiert mit den Produktionsinseln verbinden.
Die Anforderungen von Fronius an die Lösung
Wir haben uns für KNAPP entschieden, weil deren System ein hohes Maß an Autonomie für uns zulässt. Mit der neuen Automatisierungslösung sind wir in der Lage, flexibel und selbständig Standortänderungen sowie -erweiterungen von Produktionsinseln vorzunehmen. Dadurch sind wir im Gesamtbetrieb schneller und kosteneffizienter als mit anderen Systemen.
Die Technologie im Einsatz bei Fronius
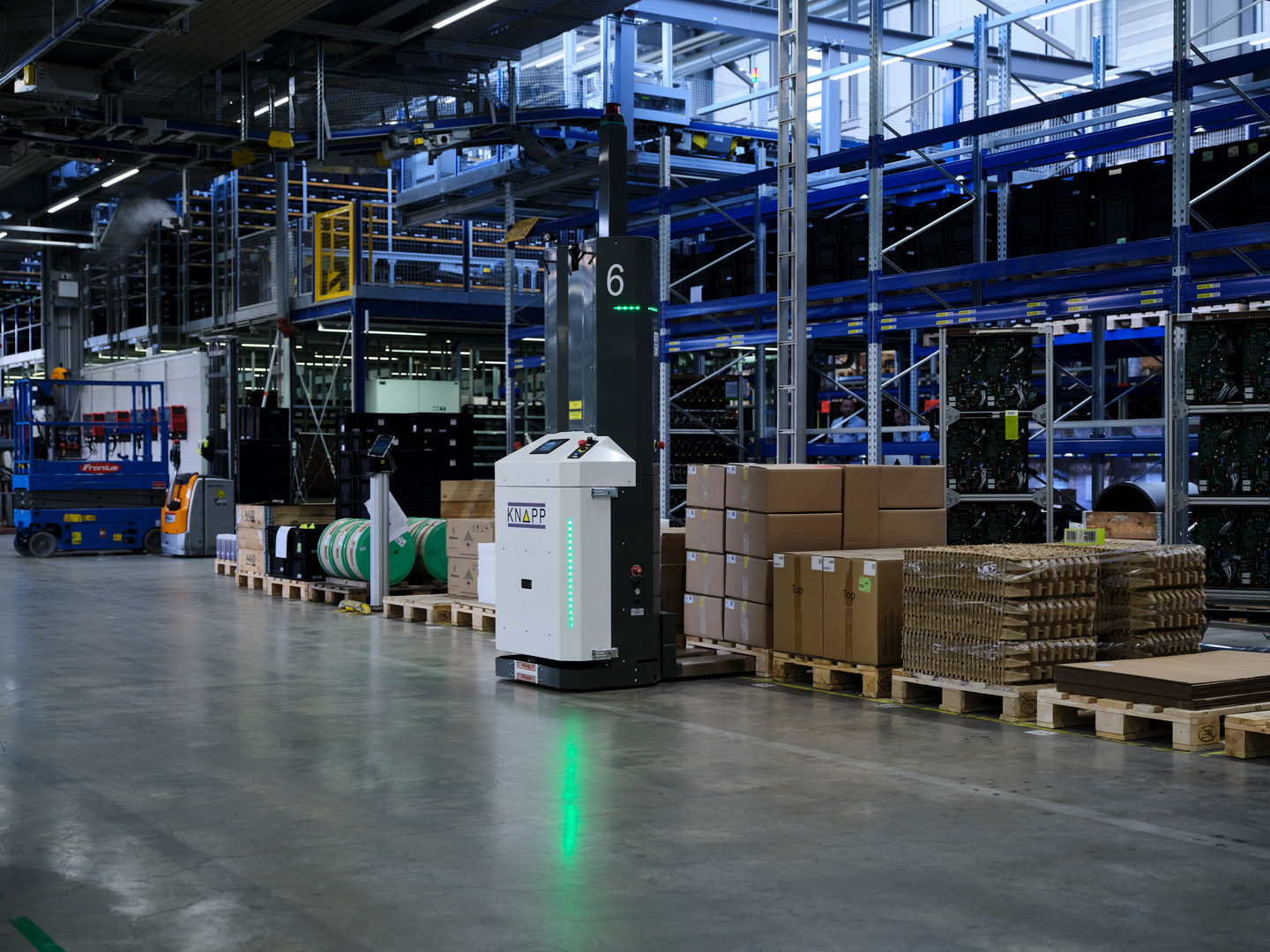
Open Shuttle Fork: automatisierter Palettentransport mit AMR
Die kompakte Bauweise und die wendige Lenktechnologie der Open Shuttle Fork waren ausschlaggebend für die Entscheidung, diese autonomen mobilen Roboter einzusetzen. Dadurch konnte die Gangbreite der Logistikwege verringert und zusätzliche Fertigungsfläche gewonnen werden. Die Open Shuttle Fork automatisieren nicht nur den Palettentransport (Euro-, und Kunststoffpaletten), sondern auch den Transport von Müllcontainern.
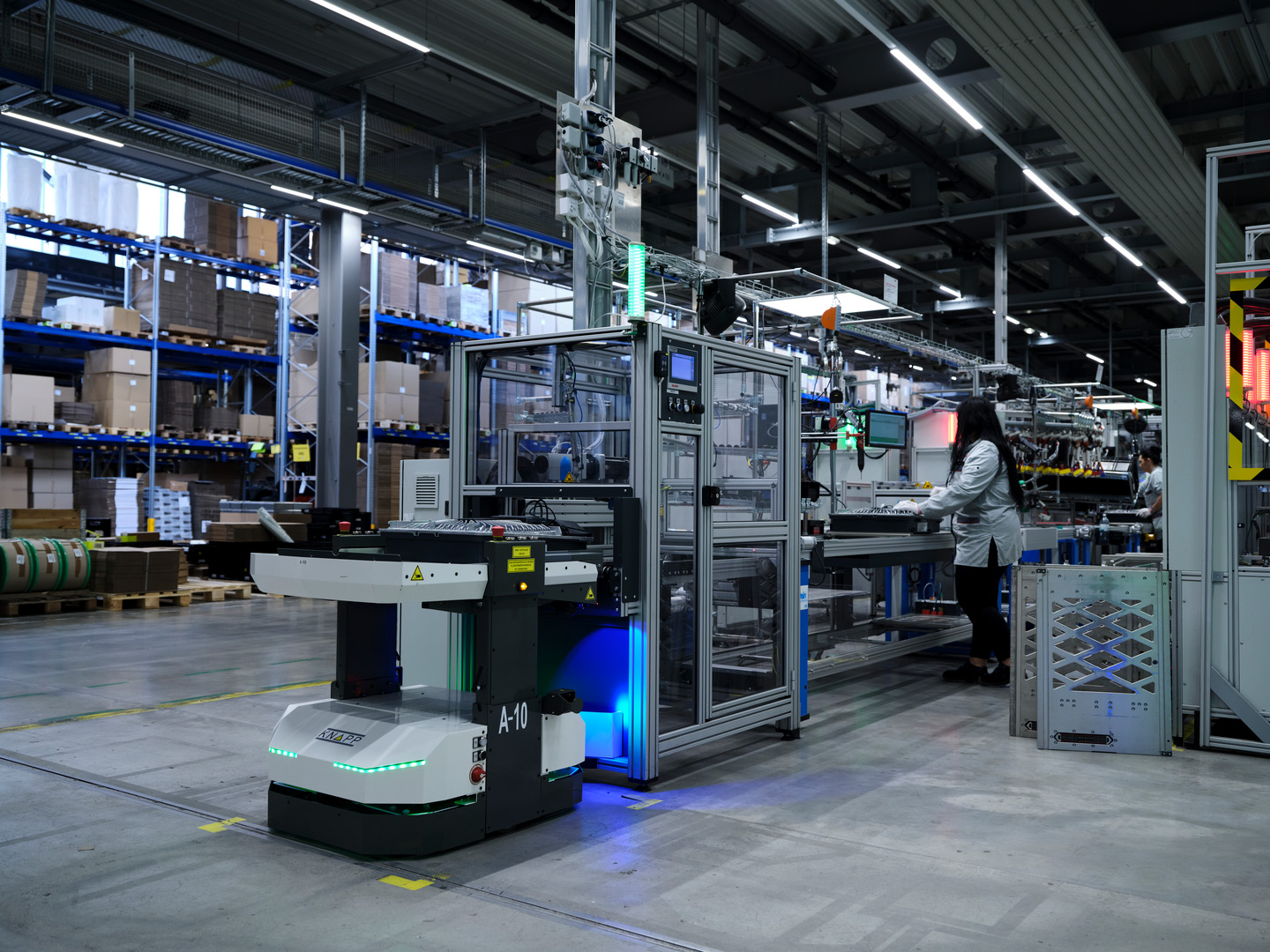
Open Shuttles: getakteter Transport von Wechselrichtern mit AMR
Die Open Shuttles sind seit 2020 integraler Bestandteil der Fertigungslinie der Wechselrichter bei Fronius. Sie übernehmen den getakteten Transport der Wechselrichter zu den Prüfstationen und zur Verpackungslinie. Sie bieten Fronius ein hohes Maß an Flexibilität. 11 Open Shuttles sind direkte an die Produktionsline, die Prüfstellen und die Verpackungslinie angebunden. Sie versorgen die Prüfbuchten für Kurz- und Langzeittests mit Wechselrichtern aus der Fertigungslinie und bringen sie nach erfolgreichen Tests zur Verpackungslinie.
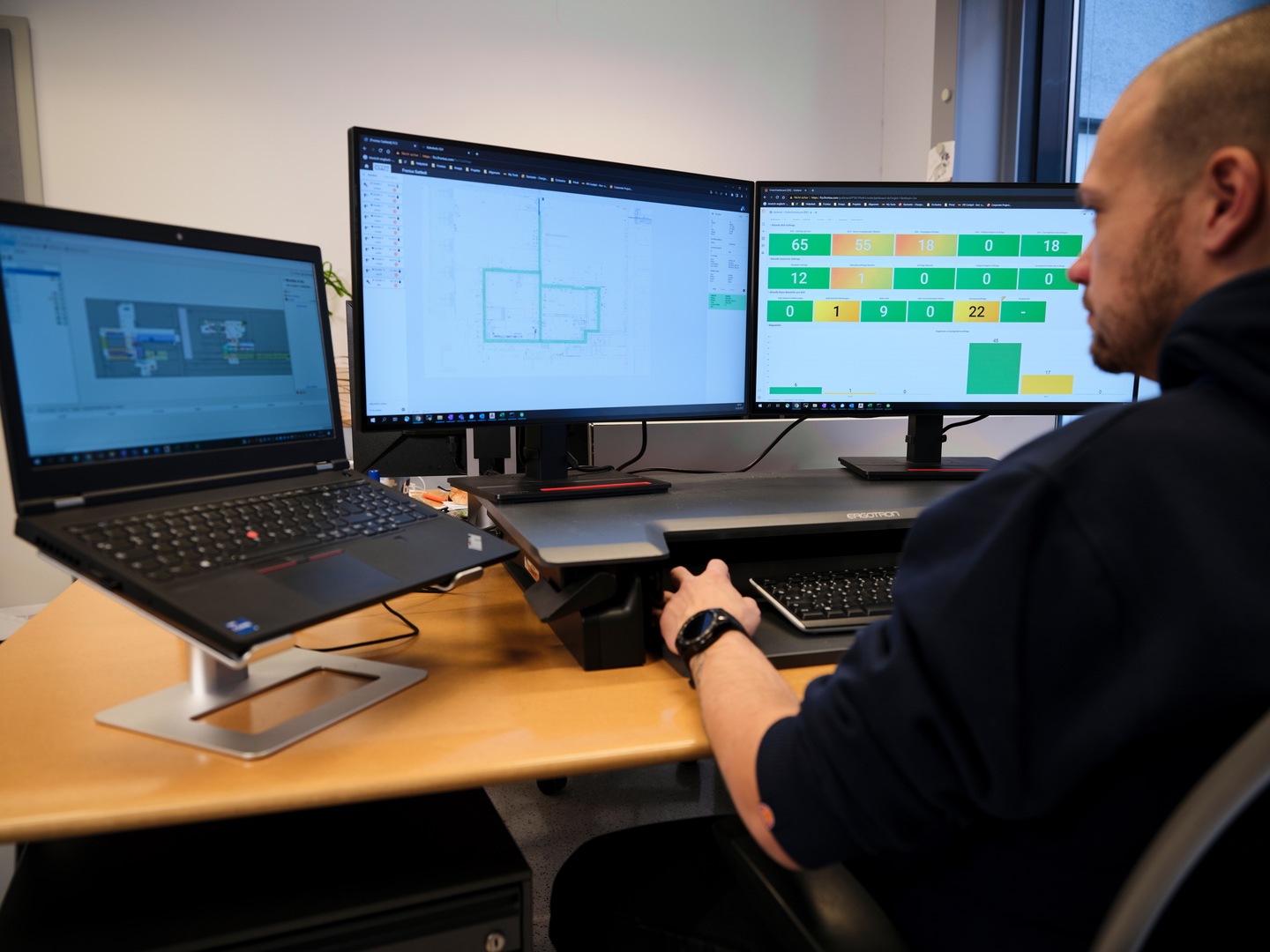
KiSoft FCS: Innovative Software für AMR
Die Software KiSoft FCS ist das zentrale Steuerungselement der autonomen mobilen Roboter. Sie ist durch eine Schnittstelle mit dem Kundensystem verbunden, steuert die Flotte und verwaltet die Aufträge. Dank KiSoft FCS ist Fronius in der Lage, Wege selbst anzupassen und Stationen hinzuzufügen. Ein Dashboard mit einer Übersicht aller Kennzahlen zu den Transporten verschafft Fronius jederzeit einen Überblick über die eingesetzten Roboter.
Die Auftragsgenerierung für die Open Shuttle Fork erfolgt über Tablets mit eigens für Fronius entwickelten Bedienmasken. Neben den AMR werden auch die manuellen Stapler in KiSoft FCS abgebildet. Das ermöglicht eine sehr flexible Koordination von automatisierten und manuellen Transporten.
Die effizienten Transportprozesse mit AMR im Überblick
Open Shuttle Fork
Open Shuttles
km Wegstrecke/Tag
Prüfstationen
Palettenstellplätze
m² Hallenfläche
Automatisierter Palettentransport
Waren aus dem Zentrallager werden an einem Palettenbahnhof für den Weitertransport zu den Produktionsinseln abgestellt.
Direkt neben den einzelnen Produktionsinseln befinden sich Palettenstellplätze. Das Open Shuttle Fork holt die Halbfertigprodukte ab und transportiert sie weiter zum nächsten Bearbeitungsschritt.
Die fertig produzierten Maschinen und Geräte werden ebenfalls auf Paletten an Abholplätzen bereitgestellt. Mithilfe der Open Shuttle Fork werden diese in das Warenausgangslager transportiert, dort abgestellt, verpackt und in das automatische Palettenlager eingelagert.
Weiters übernehmen die Open Shuttle Fork auch Sondertransporte, wie zum Beispiel den Transport von Müllcontainern zum Abstellplatz.
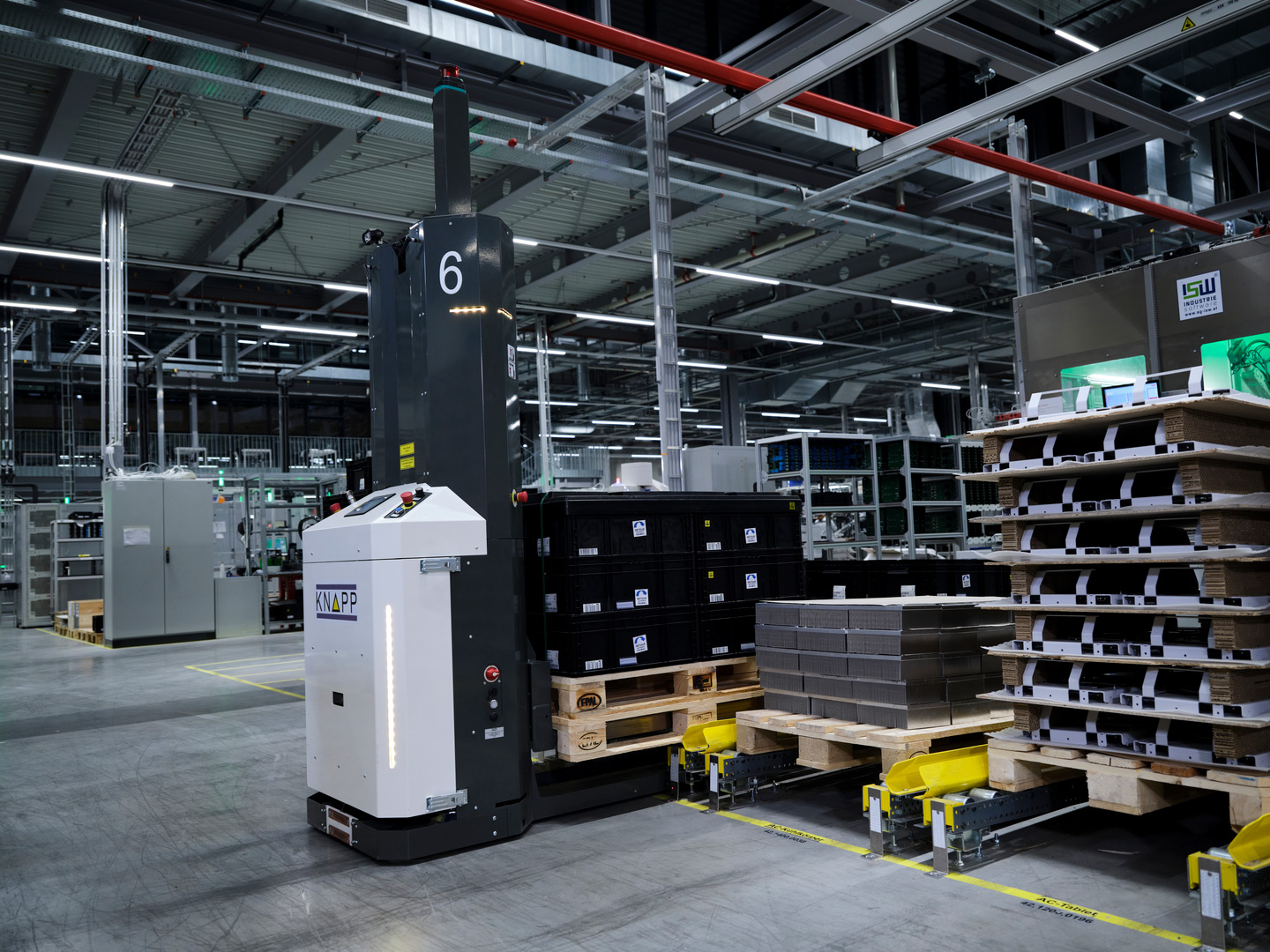
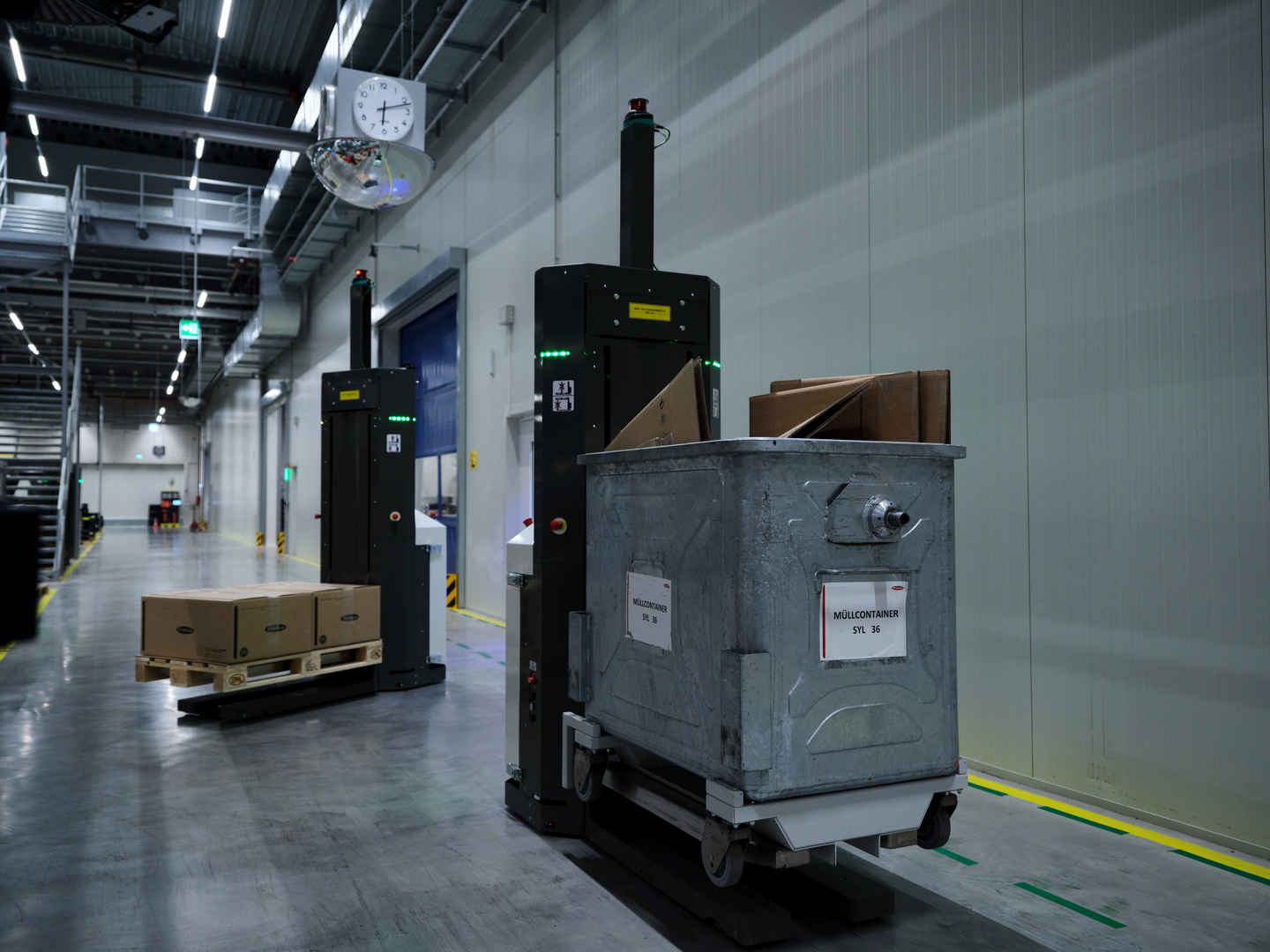
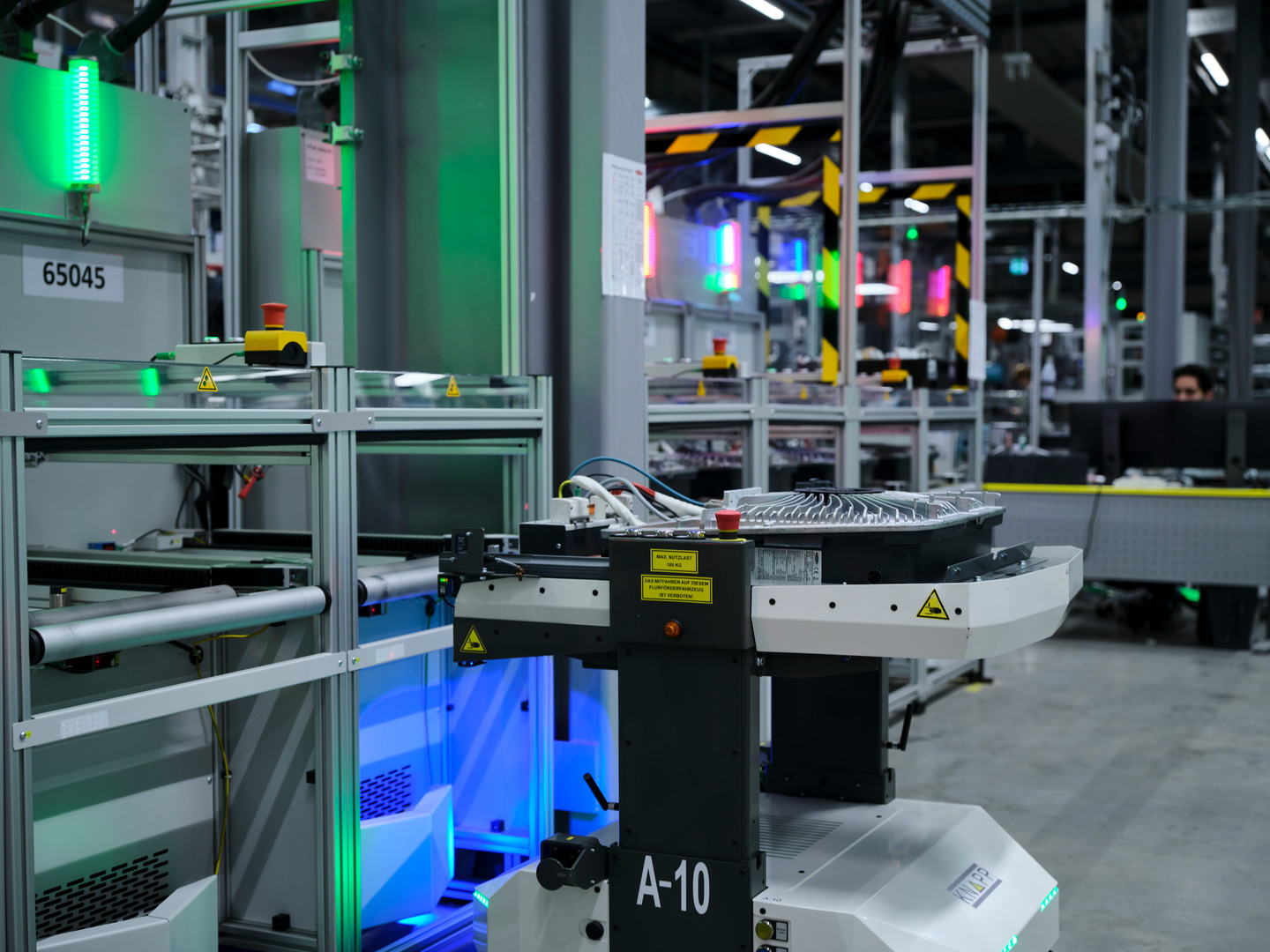
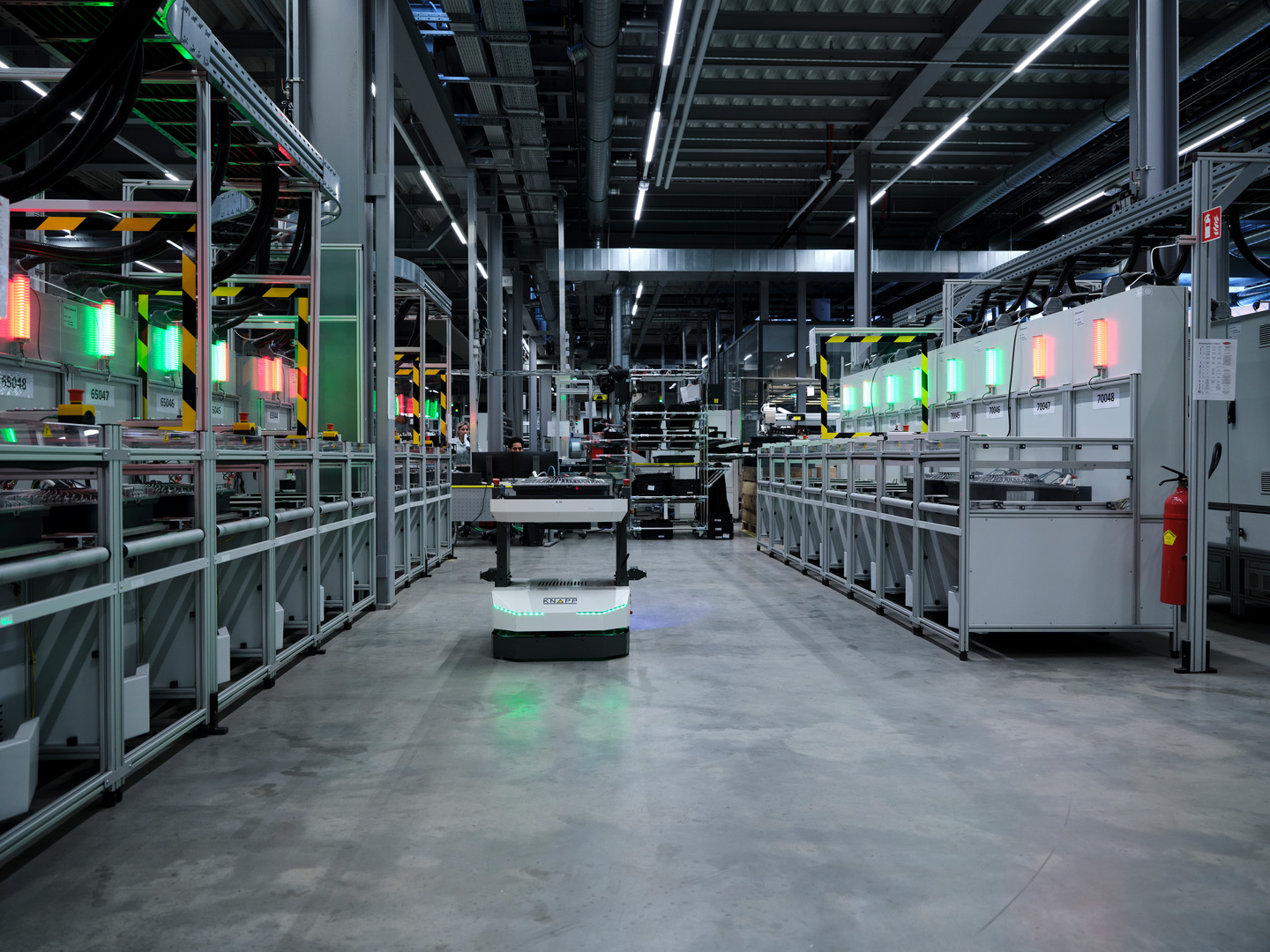
Getakteter Wechselrichtertransport
Die Wechselrichter werden in der Linie produziert und auf Trägerplatten montiert. Ist ein Wechselrichter fertig wird er über eine Fördertechnik vom Open Shuttle aufgenommen und zu einer freien Kurzzeittest-Bucht gebracht, wo er automatisch überprüft wird.
Nach erfolgreichem Kurzzeittest transportiert das Open Shuttle den Wechselrichter weiter zum Langzeittest.
Wurden beide Tests positiv absolviert, holt das Open Shuttle den Wechselrichter wieder ab und bringt ihn automatisiert an die Verpackungslinie. Leere Ladungsträger werden vom Open Shuttle von hier wieder in die Fertigung rückgeführt.
Fallen Lang- oder Kurzzeittest negativ aus, werden sie automatisch zur Nacharbeitsstation transportiert, dort überarbeitet und anschließend wieder abgeholt und dem Prüfprozess zugeführt.
Automatisierter Palettentransport
Waren aus dem Zentrallager werden an einem Palettenbahnhof für den Weitertransport zu den Produktionsinseln abgestellt.
Direkt neben den einzelnen Produktionsinseln befinden sich Palettenstellplätze. Das Open Shuttle Fork holt die Halbfertigprodukte ab und transportiert sie weiter zum nächsten Bearbeitungsschritt.
Die fertig produzierten Maschinen und Geräte werden ebenfalls auf Paletten an Abholplätzen bereitgestellt. Mithilfe der Open Shuttle Fork werden diese in das Warenausgangslager transportiert, dort abgestellt, verpackt und in das automatische Palettenlager eingelagert.
Weiters übernehmen die Open Shuttle Fork auch Sondertransporte, wie zum Beispiel den Transport von Müllcontainern zum Abstellplatz.
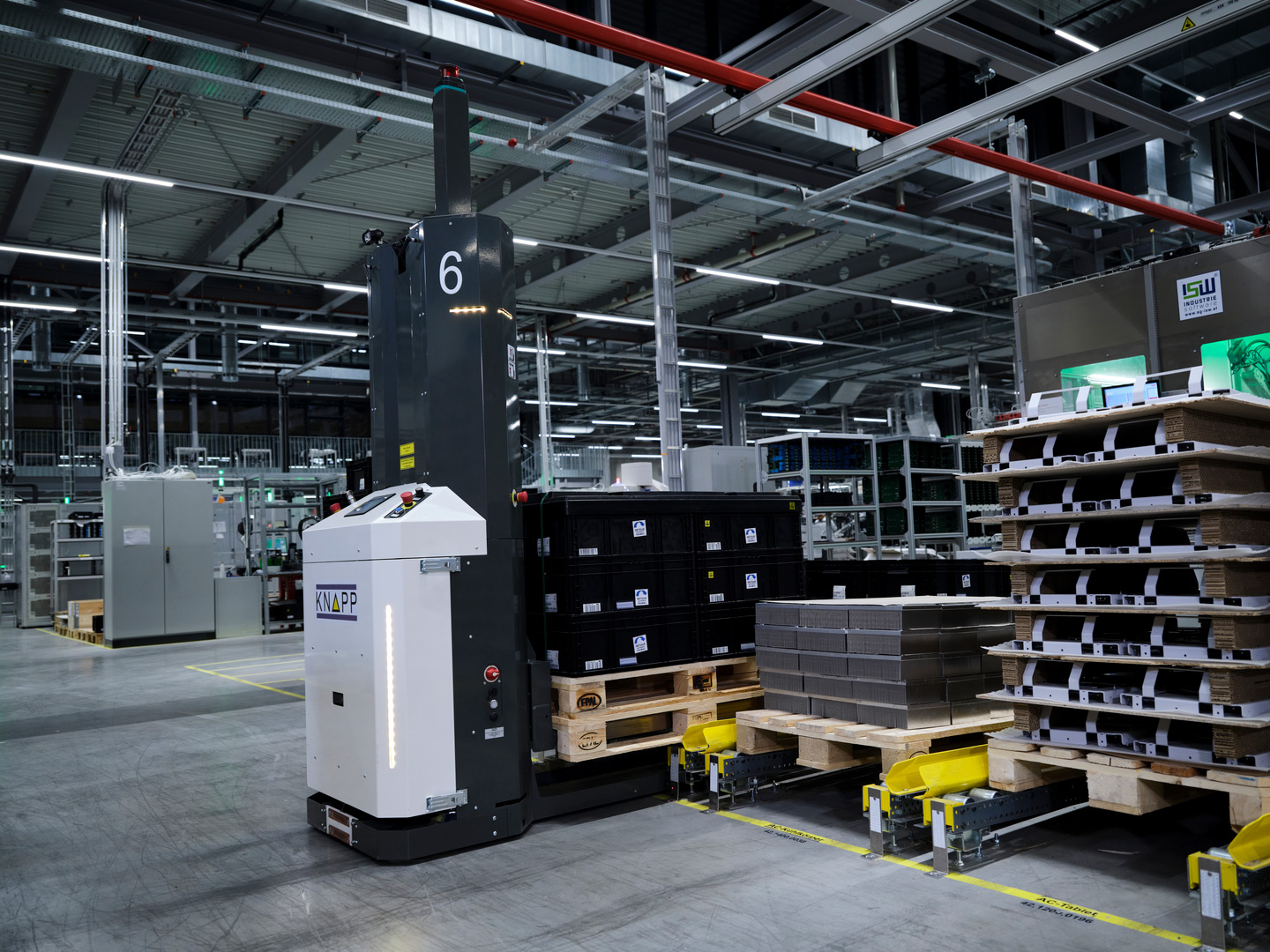
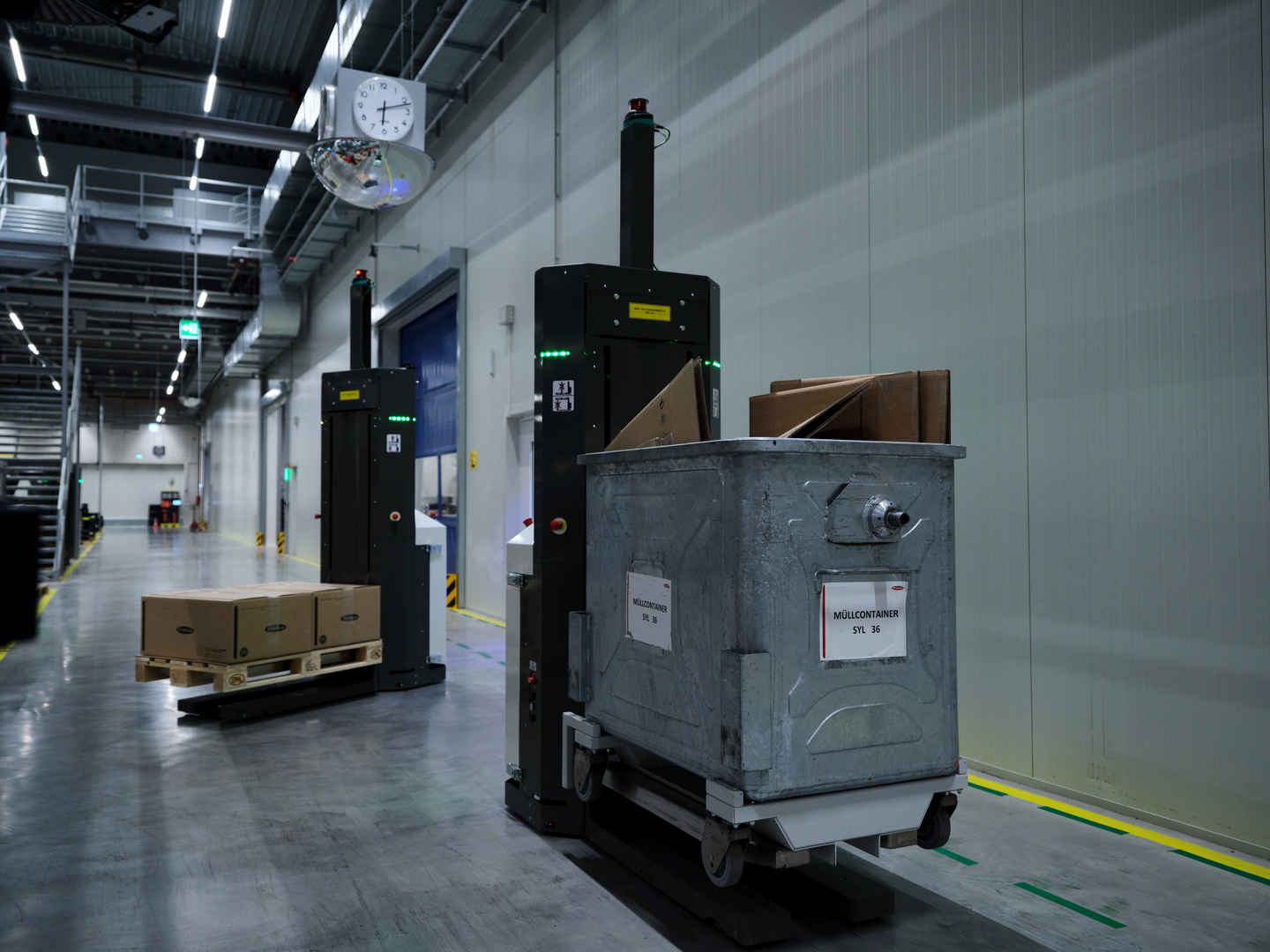
Getakteter Wechselrichtertransport
Die Wechselrichter werden in der Linie produziert und auf Trägerplatten montiert. Ist ein Wechselrichter fertig wird er über eine Fördertechnik vom Open Shuttle aufgenommen und zu einer freien Kurzzeittest-Bucht gebracht, wo er automatisch überprüft wird.
Nach erfolgreichem Kurzzeittest transportiert das Open Shuttle den Wechselrichter weiter zum Langzeittest.
Wurden beide Tests positiv absolviert, holt das Open Shuttle den Wechselrichter wieder ab und bringt ihn automatisiert an die Verpackungslinie. Leere Ladungsträger werden vom Open Shuttle von hier wieder in die Fertigung rückgeführt.
Fallen Lang- oder Kurzzeittest negativ aus, werden sie automatisch zur Nacharbeitsstation transportiert, dort überarbeitet und anschließend wieder abgeholt und dem Prüfprozess zugeführt.
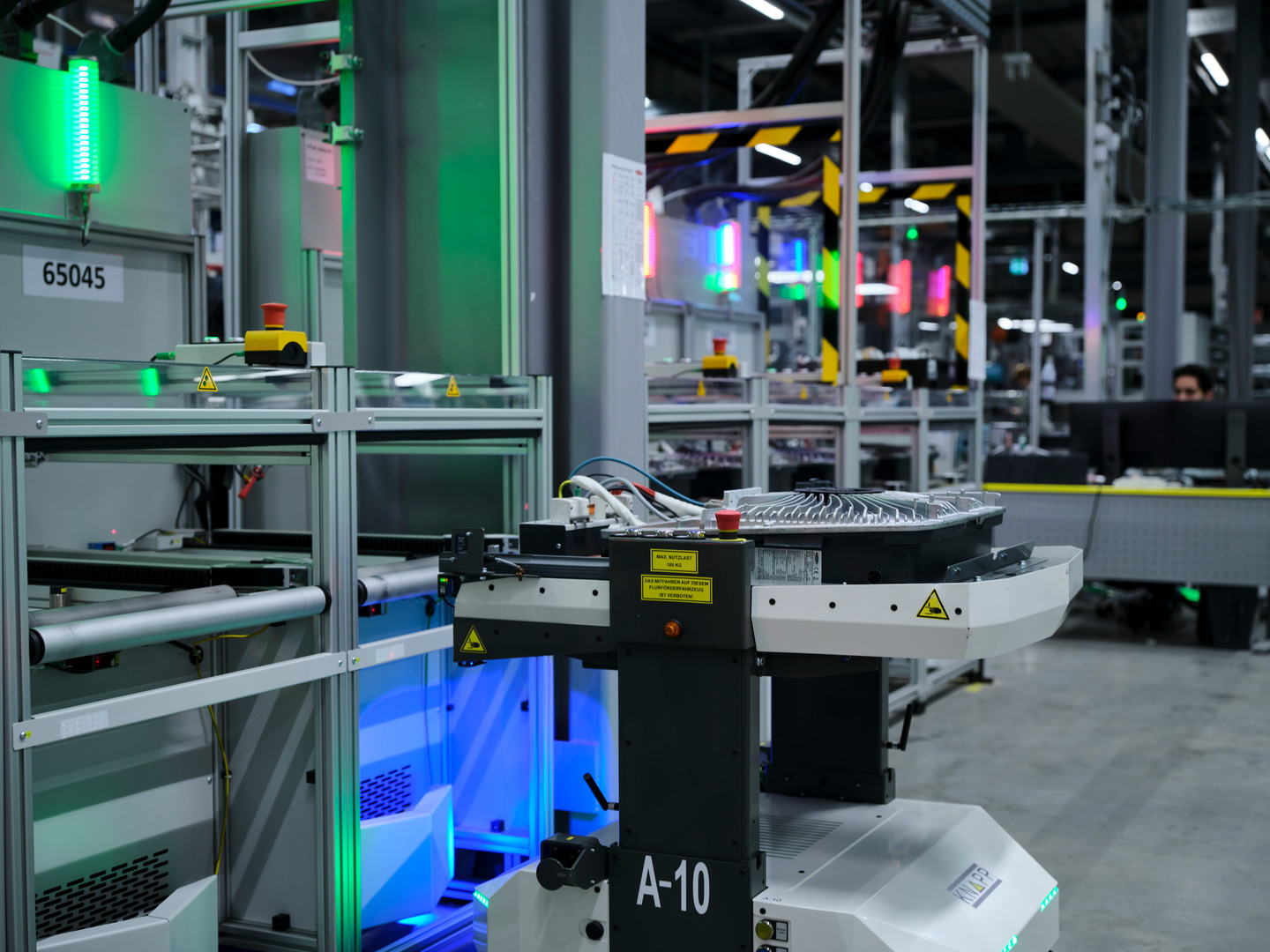
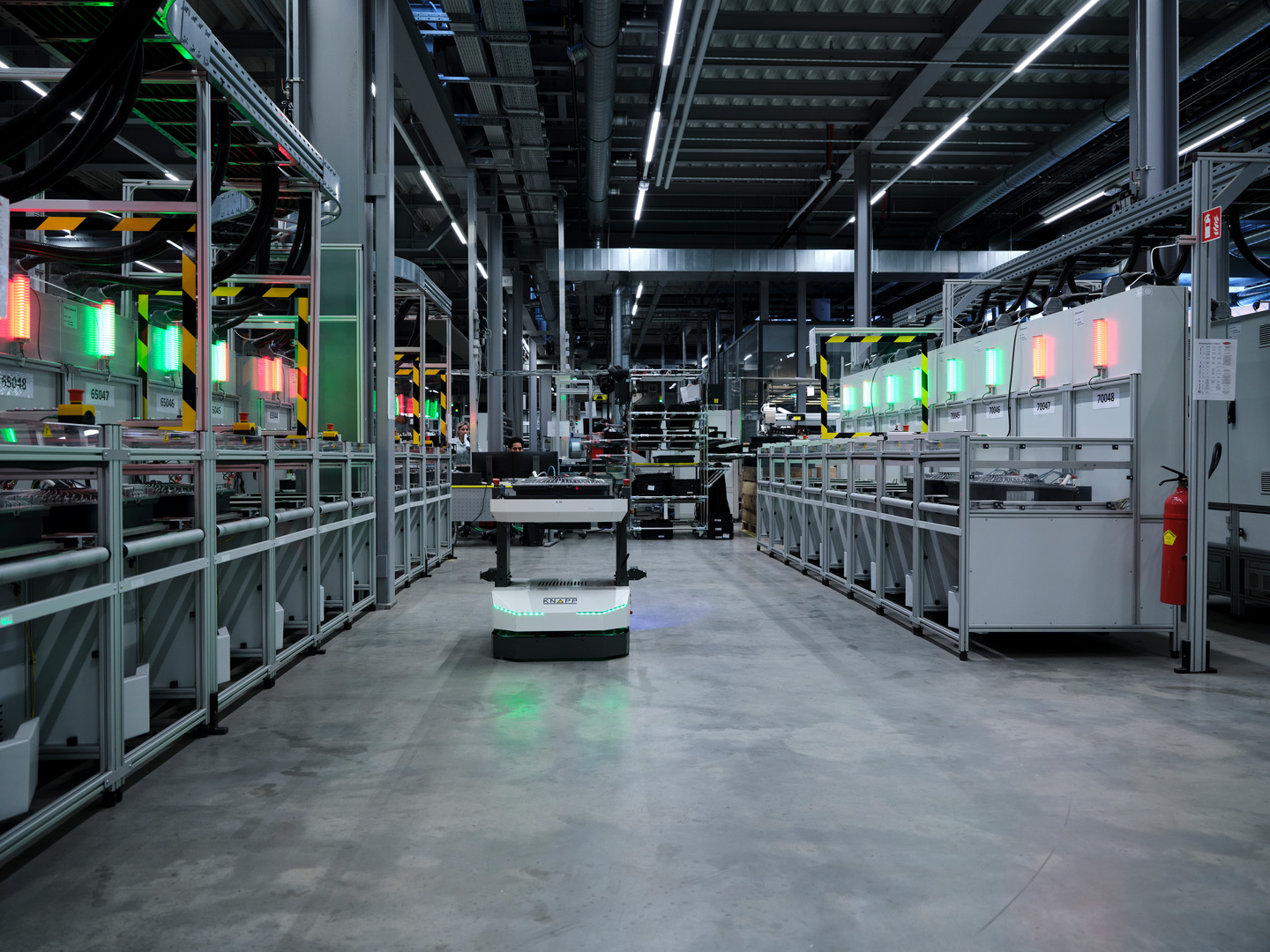
Ein weiterer Vorteil des Systems ist das effiziente Batteriemanagement. Hier wird transportfreie Zeit zum Laden verwendet. An den Ladestellen spiegelt sich die langjährige Partnerschaft zwischen KNAPP und Fronius wider, da auch hier unsere Fronius Ladegeräte verwendet werden.