Global Logistics Solution:
Victorinox Opts for Central Distribution
Famous around the world, Victorinox has opted to centralize their worldwide distribution and optimize processes. Orders are no longer processed at more than 17 locations; instead, Victorinox delivers to customers in over 120 countries from one highly automated distribution center. In a series of workshops with KNAPP, the company selected a comprehensive automated logistics concept with the all-in-one software package KiSoft One. The package combines warehouse management, warehouse control and machine control systems into one complete vertically integrated program.
You are currently viewing a placeholder content from YouTube. To access the actual content, click the button below. Please note that doing so will share data with third-party providers.
More InformationTransformation and growth: Victorinox centralizes logistics
Victorinox is famous for their iconic Swiss Army Knife. These knives and the entire range of goods including kitchen knives, perfumes, watches and travel gear from all 17 warehouse locations, have all been consolidated and are now stored in the automated global distribution center. Products are distributed worldwide from the headquarters in Schwyz to wholesalers and stores.
By investing in a highly automated and centralized logistic system, Victorinox has optimized their efficiency, costs, stock management, shipping, and above all, the sustainability of their distribution along every step of the way. Take a peek behind the curtain of this logistics solution and discover how Victorinox is preparing for future growth.
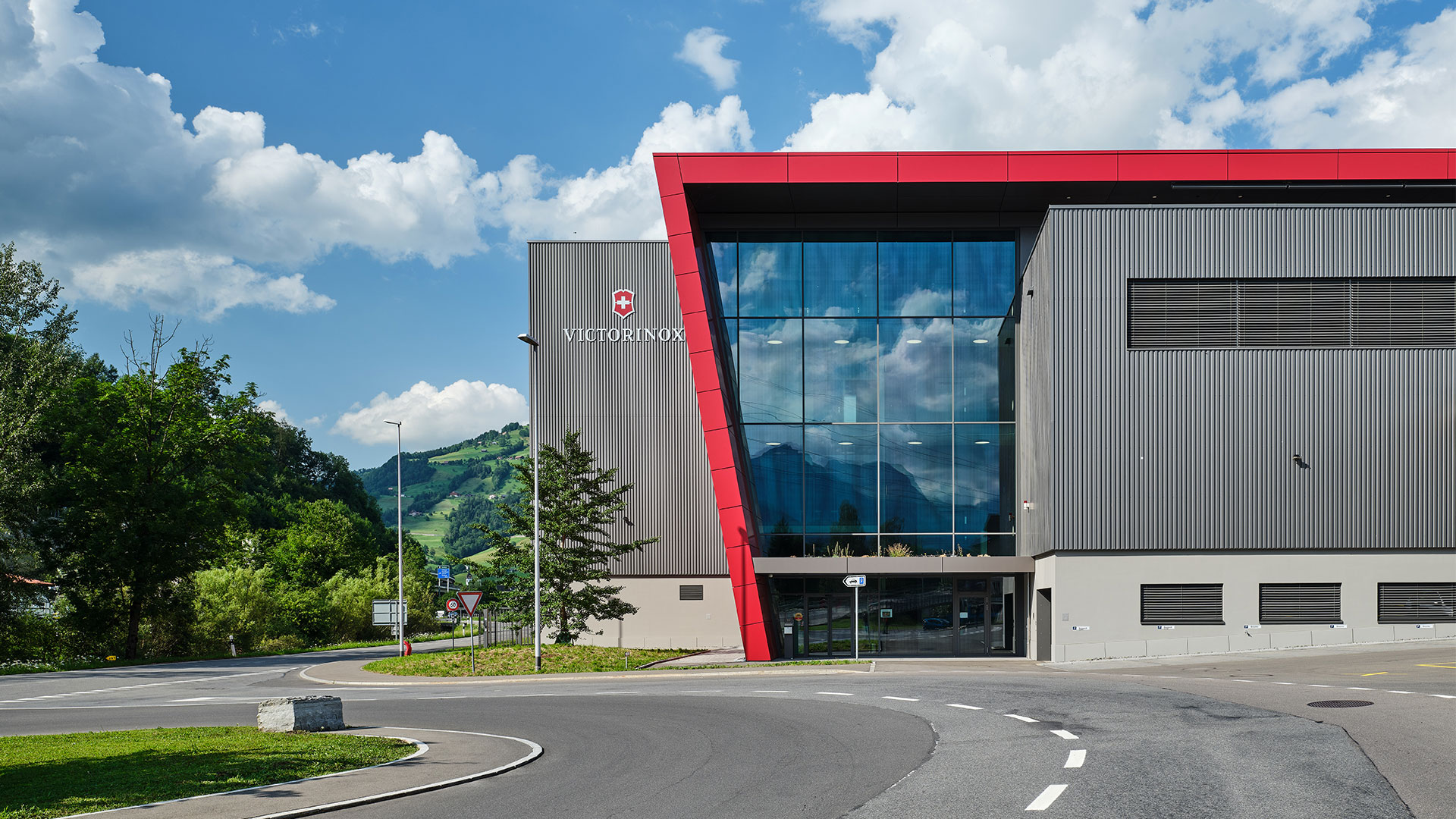
By reorienting our global value chain and using automation technology, we increase efficiency and quality while reducing costs. At the same time, this saves resources, helping us contribute to a sustainable future.
Would you like to re-align your value chain?
Get in touch with our experts today.
Structured methodology for tailor-made logistics
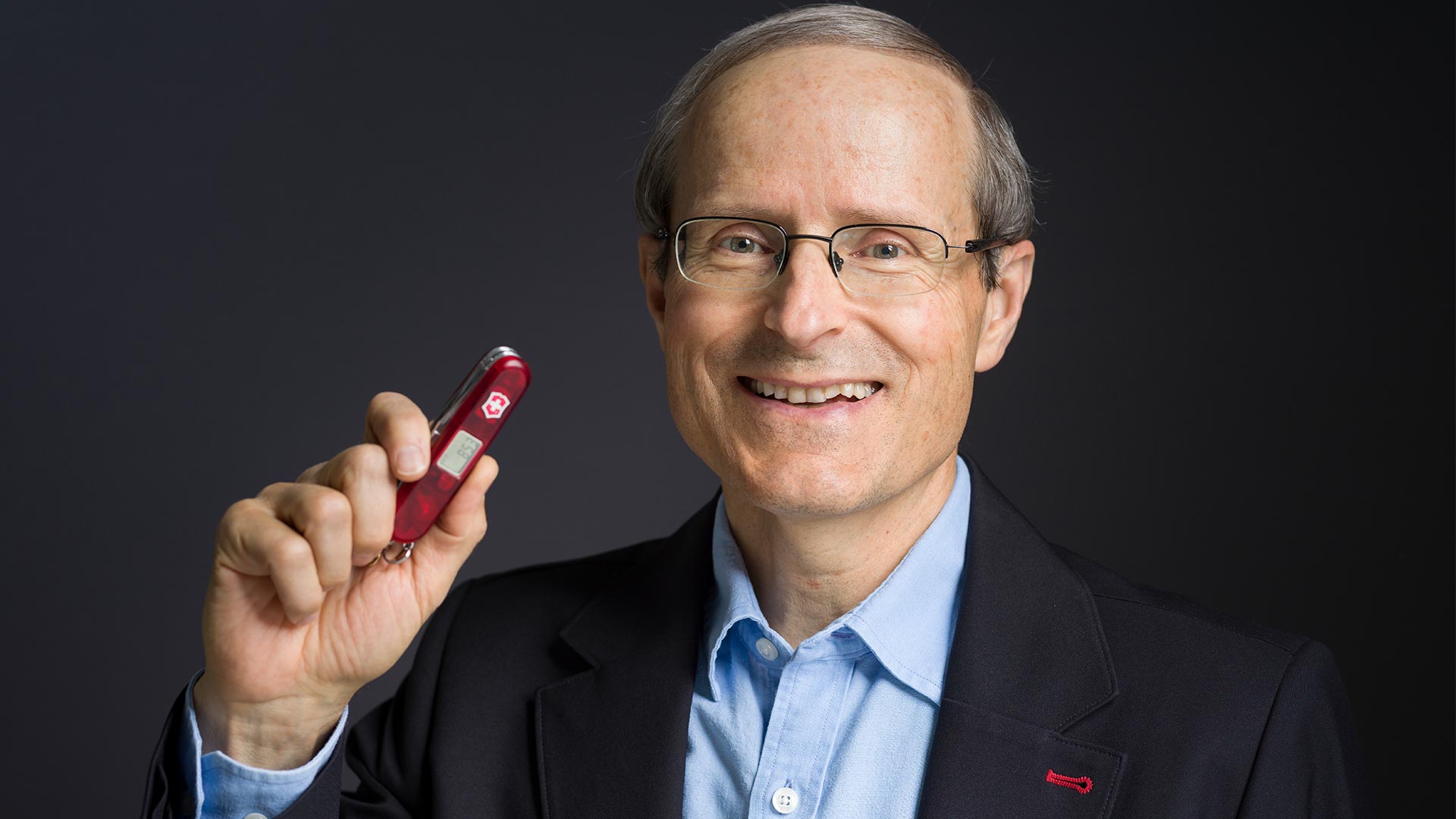
Understanding the requirements, the business cases and the goals:
To ensure that the automated, centralized logistics provide optimal support for our customers’ operations, we take plenty of time to understand the project goals, requirements, and the business case itself at the start of each project. To accomplish this, we conduct collaborative workshops and follow a structured methodology.
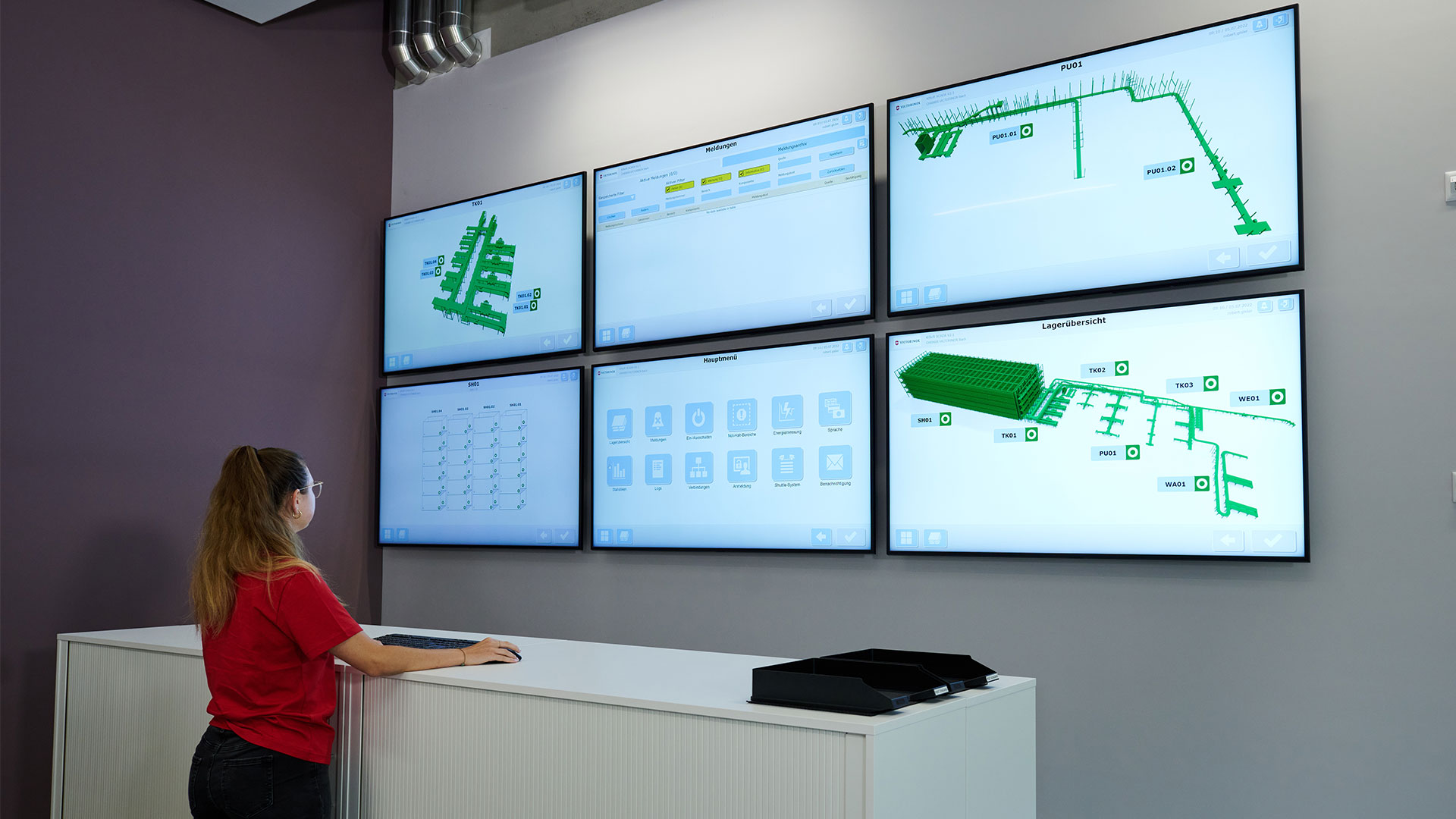
Software at the center of warehouse design:
During the design phase, all the software processes are first defined based on the business cases and the requirements. Afterwards, we select the right automation technologies and dimension according to the requirements.
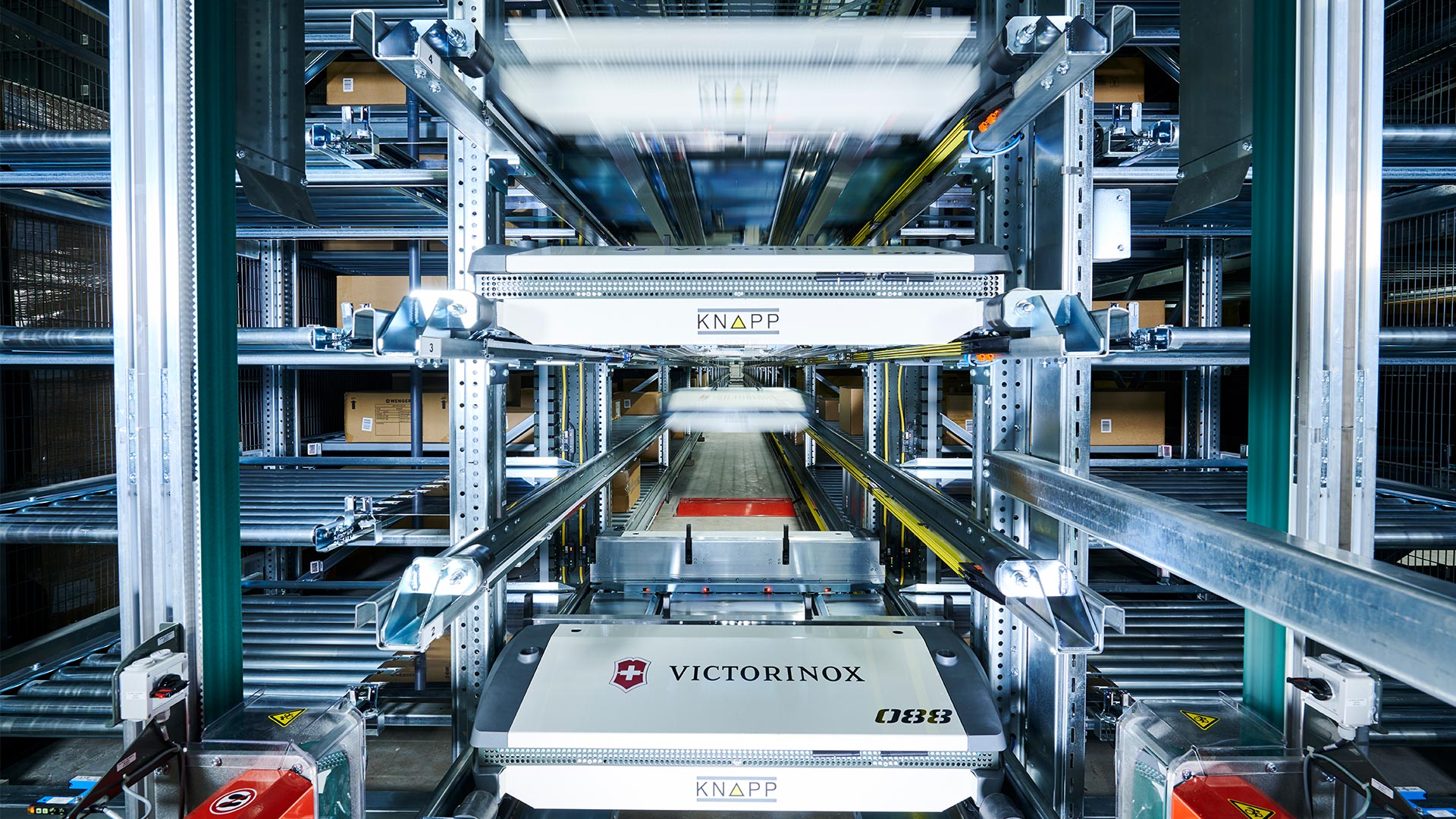
Implementing the physical warehouse:
The knowledge of these processes now had to be translated into a physical warehouse. The greatest challenge was consolidating all the available material data from all 17 separate locations and merging it to create a single common material flow.
We always start by analyzing the customer’s business case, which we use to model the warehouse processes and software functions. Once we’ve done that, we decide which warehouse technologies to use.
Hansjürgen Walter
Head of Software Consulting
KNAPP
central storage system
orders per year
high-performance shuttles
goods-to-person work stations
A custom solution designed for unique requirements
For the new automated global distribution center, Victorinox defined a series of goals to achieve with a tailor-made logistics solution:
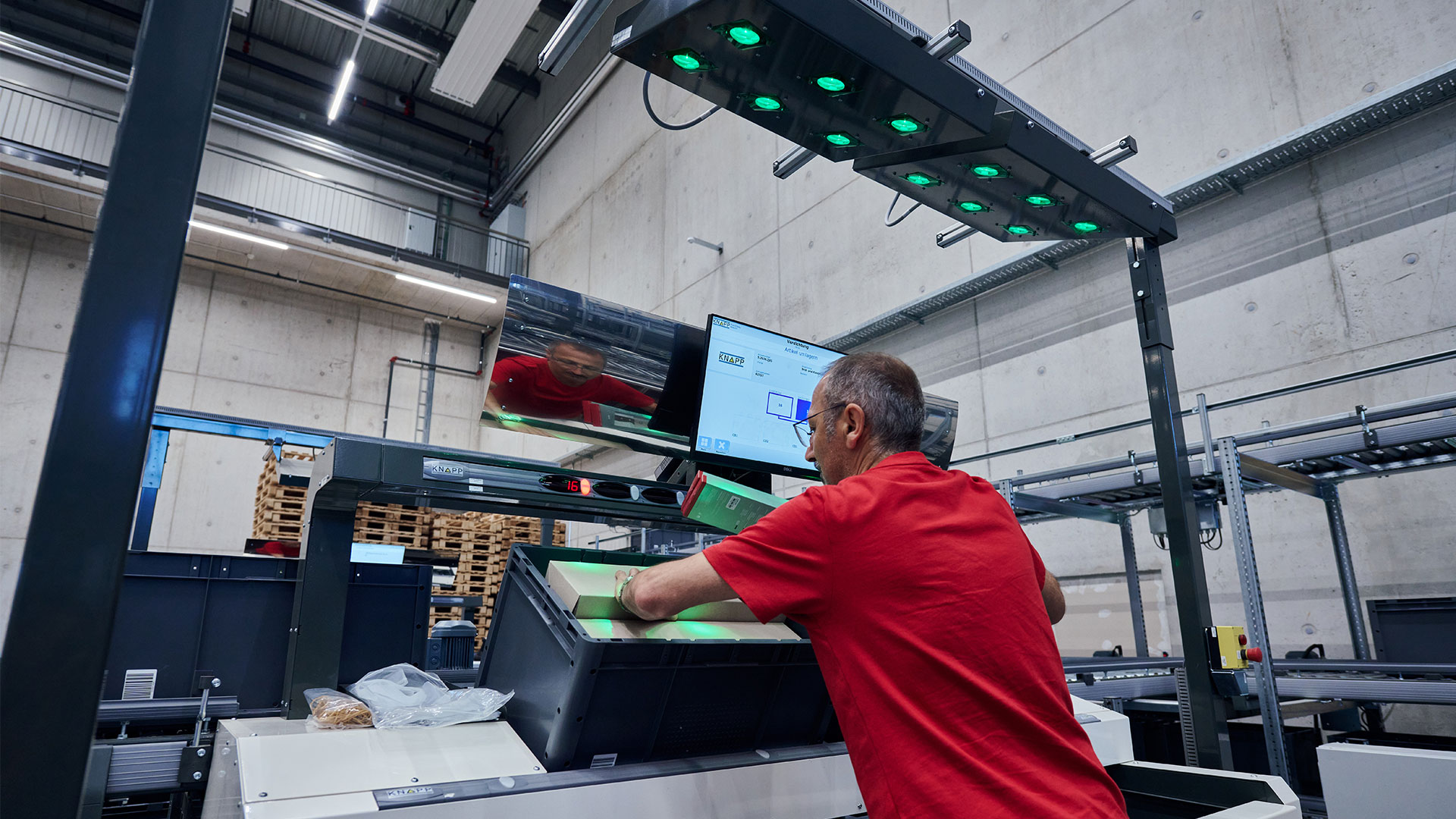
Are you interested in a tailor-made logistics solution?
Our experts are here for you.
Greater efficiency with vertically integrated software
To handle their business cases and functional requirements, Victorinox opted for the all-in-one KiSoft One software. The comprehensive software solution takes care of all warehouse management, warehouse control as well as machine control tasks. This end-to-end, vertical software architecture offers plenty of advantages for Victorinox, both in their daily warehouse operations and along their entire supply chain.
KiSoft One provides a simple and transparent overview of:
With KiSoft One, we have a completely transparent, real-time view
of not only our supply chain, but all our processes.