Tempe Inditex: AutoPocket for efficient store fulfilment
Tempe, a member of the Inditex Group, has been a leader in the footwear sector since the late 1980s. Since then, the company has been developing, marketing and distributing footwear and accessories for the brands Zara, Pull & Bear, Massimo Dutti, Bershka, Stradivarius, Oysho and Zara Home. Each year, more than 100 million shoes leave the distribution centres in Elche, Spain, which supply more than 5000 stores in 212 countries.
Their mission? Never be satisfied with less. Tempe is continuously searching for new, innovative and original ways to get their products to their customers. The flexible automation solution helps the company to provide customers across the globe with high-quality fashion quickly and efficiently, with short delivery times between 24 and 48 hours.
You are currently viewing a placeholder content from YouTube. To access the actual content, click the button below. Please note that doing so will share data with third-party providers.
More InformationThe challenge: Automation for more flexibility and performance
Raise production capacity
Innovation and continuous improvement is what the company is all about. Over the past years, the Inditex Group has recognized current trends in fashion, resulting in steady growth. This has made it necessary to increase production capacity at the logistics site. With the new logistics solution, the company can now provide rapid, efficient distribution to their stores worldwide.
More orders and variable order sizes
The warehouse had to be flexible in order to handle the increasing number of orders as well as the variable order sizes.
Broad range of goods and seasonal changes
The customer’s broad product range turned out to be a special feature of the project, and quite a challenging one, comprising accessories, footwear and handbags. The system needed to sort and sequence as many different types of goods as possible, without any limits.
The AutoPocket, the new pocket sorter solution, has all the answers to these challenges.
The high degree of automation ensures that goods are supplied to the employee at the pack station in sequence, reducing walking and increasing employee productivity in the packing process.
The challenges at a glance
+
Handle oversized goods
+
Handle the wide range of items across various categories of merchandise
+
Warehouse building was already planned
+
Increase employee performance
The AutoPocket is already being used successfully by customers for fashion items, especially for packaged objects and soft items such as clothing. The solution at Tempe successfully expands the application area for the AutoPocket to include footwear, accessories and handbags.
Intelligent sorting at lightning speed
The intelligent software and control system keep the two AutoPocket sorters perfectly attuned to Tempe’s high-performance requirements. Like a sophisticated traffic concept, the intelligent software actively supports and optimizes sortation and the flow of goods, providing high-powered sorting that raises the performance of the entire warehouse.
The trip around the world begins in Elche:
The solution at a glance
How do the processes work at the warehouse in Elche? What route do the accessories take from goods-in to their delivery to stores worldwide? Let’s begin our journey and follow the path taken by almost 12,000 items each hour step by step.
The goods are delivered to the distribution centre and automatically stored in a mini-load warehouse system.
Repacking into the AutoPocket pockets: The mini-load provides the AutoPocket loading stations with the source cartons containing the required accessories or shoes. At two manual and 16 automated loading stations, 1,000 items per hour per station are then loaded into the pockets of the AutoPocket. Goods for the current and subsequent sorting runs are also picked.
Sorting takes place in two processes that run in parallel:
From the loading station, the pockets move to sorting at the pre-buffers. These two buffers each have capacity for 9,400 items. Here the goods are buffered, sorted into a precise sequence and then supplied to the employees in the pack area.
Goods to be subsequently sorted are then moved to the dynamic buffer. Here, up to 32,000 items can be buffered until the current sorting run is finished and a new one starts. The dynamic buffer ensures rapid and efficient order throughput. The intelligent warehouse control system automatically sorts goods from the dynamic buffer into the current sorting run and transports them to the sorter pre-buffer. There the sorter sequences the goods precisely and transports them to the pack station.
The AutoPocket unloads items from its pockets precisely and automatically at the pack station, without slowing down or stopping. Each employee is only provided with the contents for the carton they are currently packing. At 16 pack stations, single items are packed in a carton or an envelope, depending on the volume. An employee can handle 850 items per hour.
Completed cartons are conveyed away on the conveyor system and the items for the next carton are provided to the employee at the pack station.
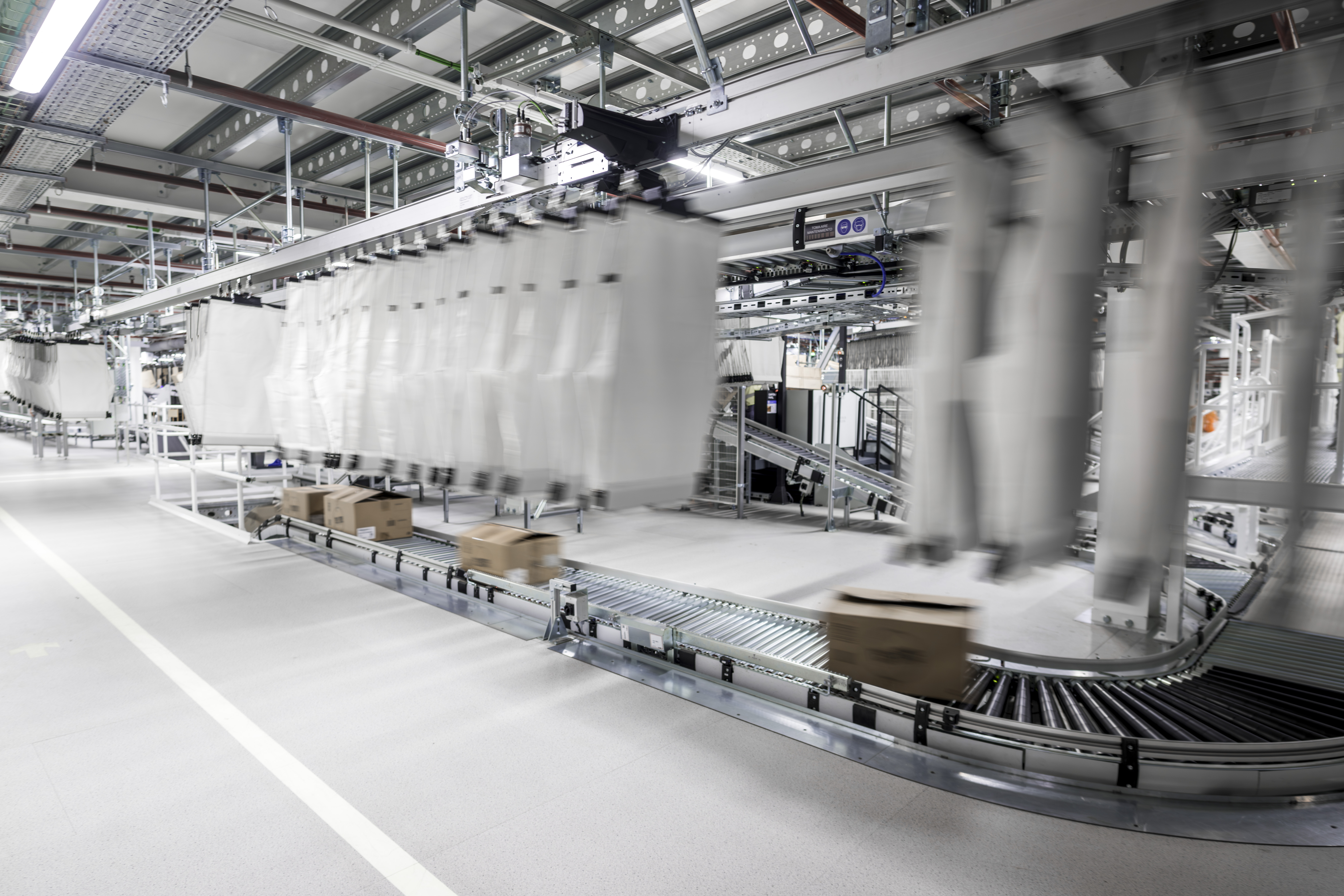
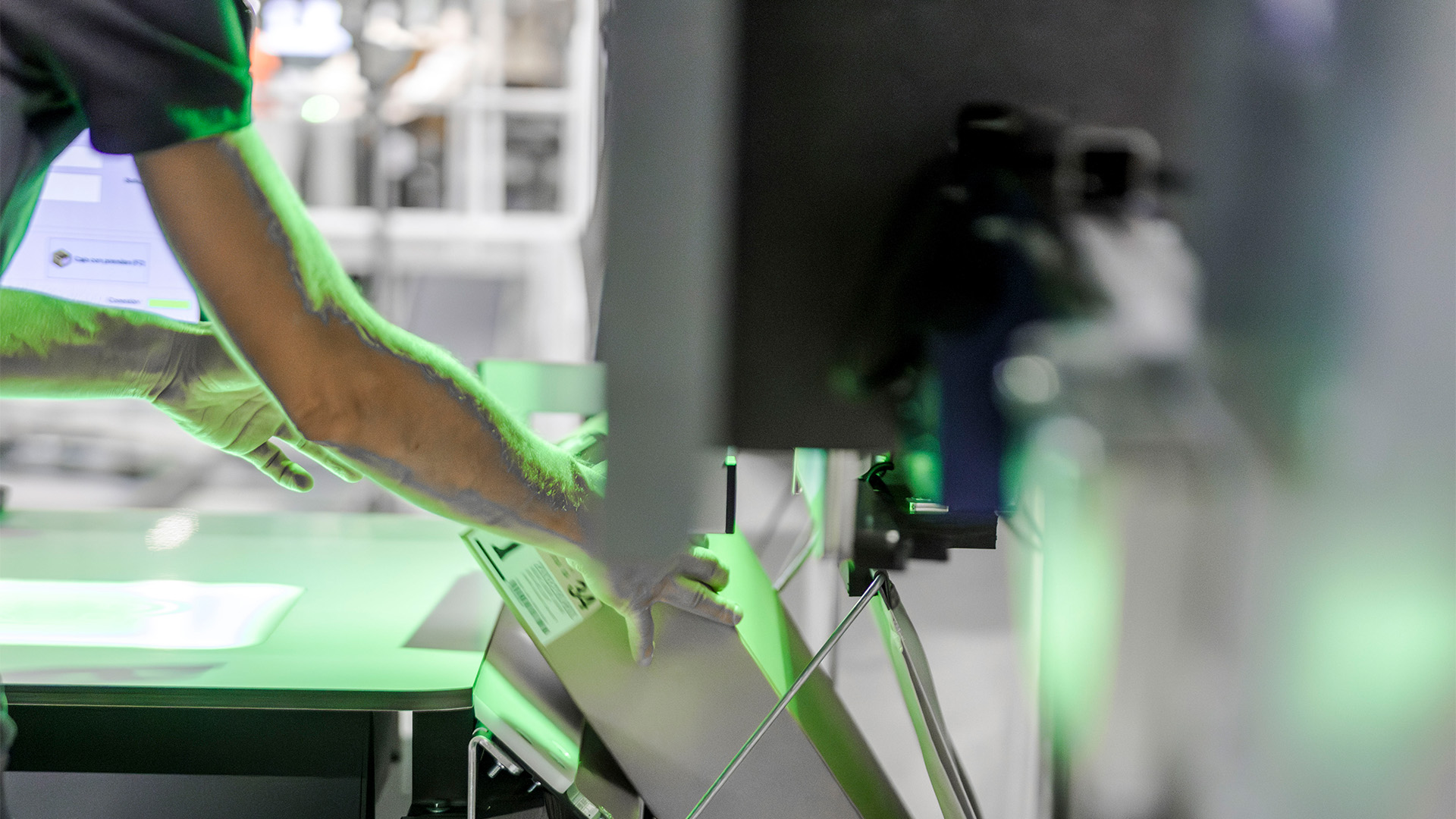
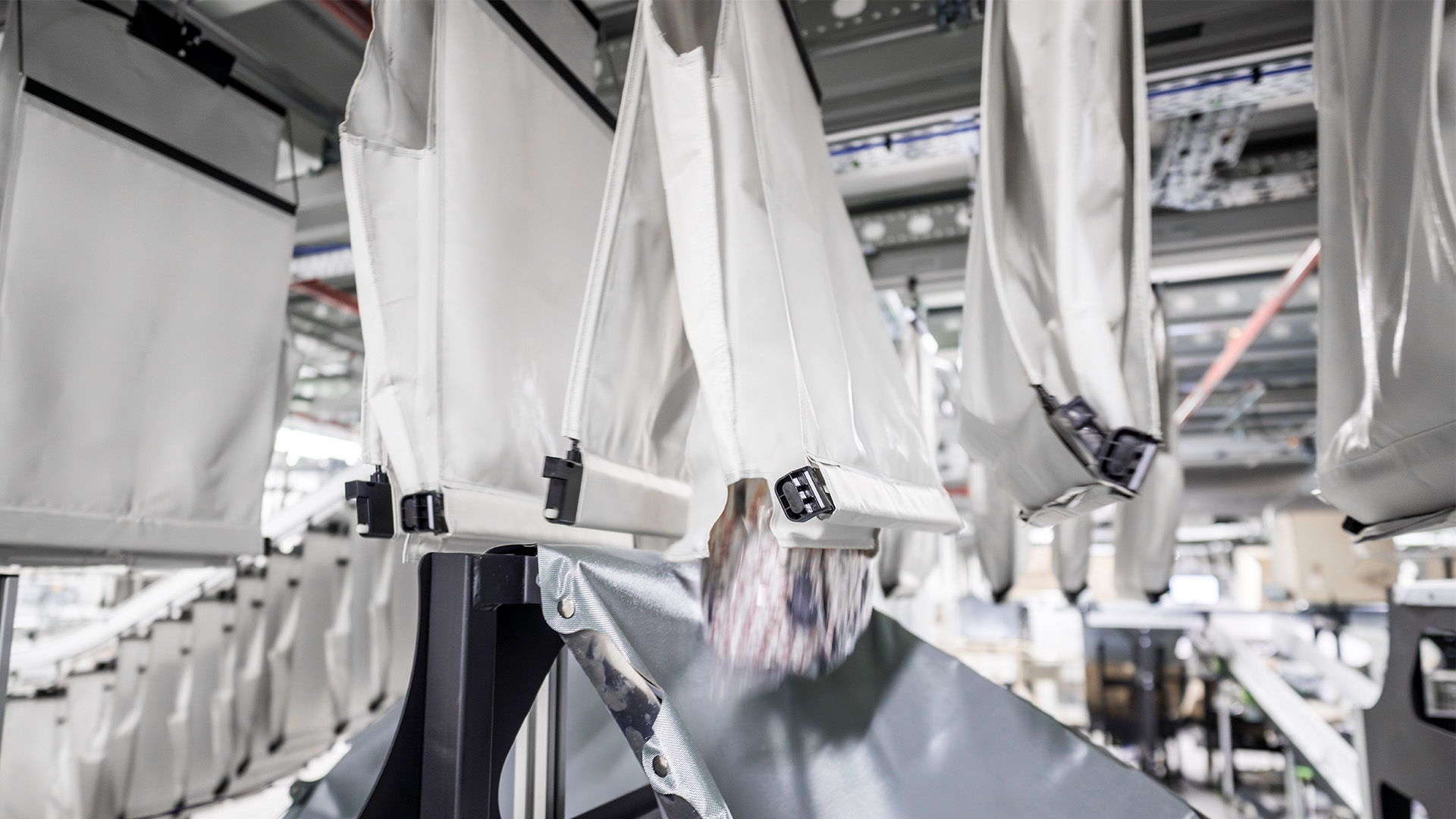
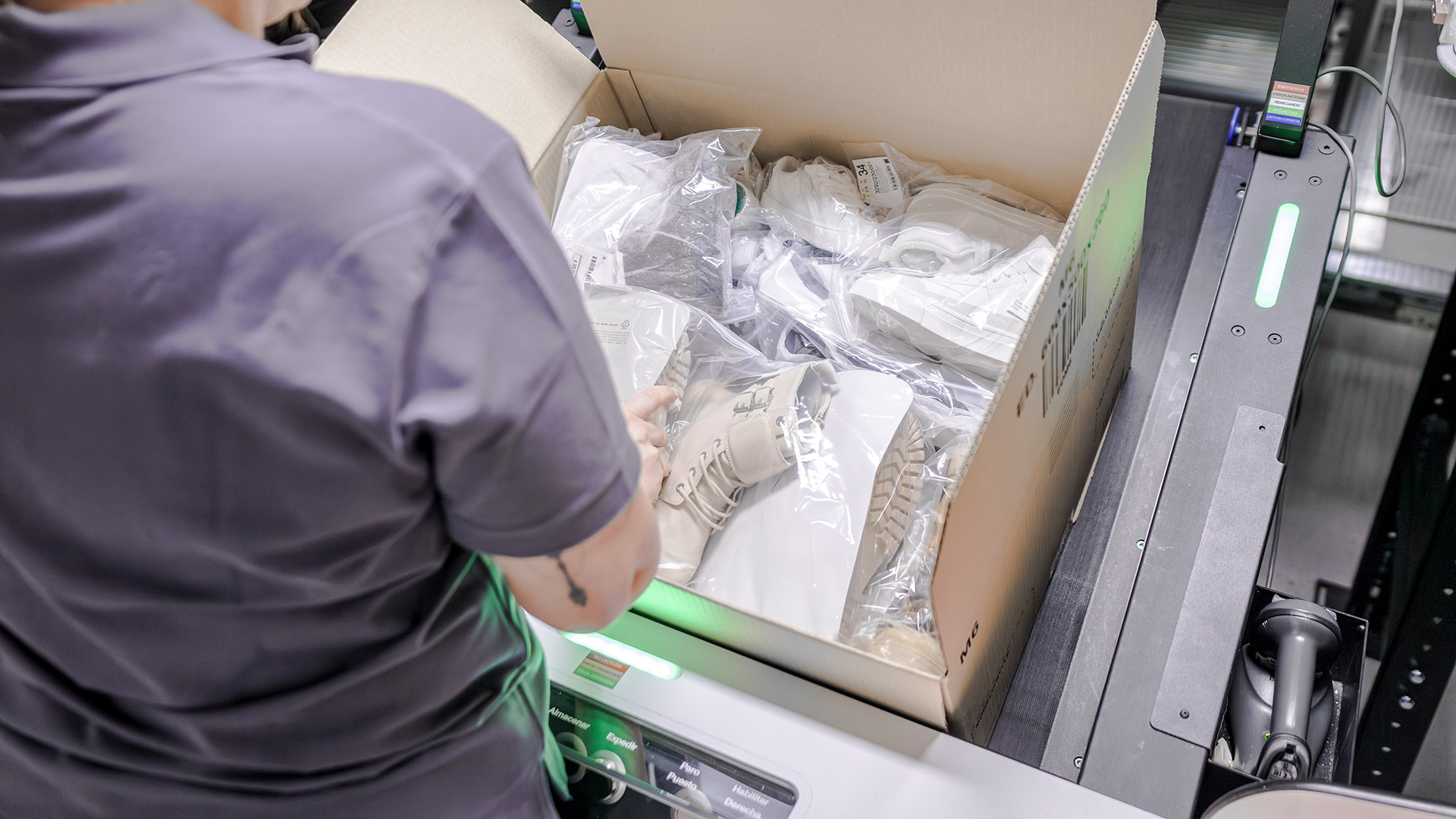
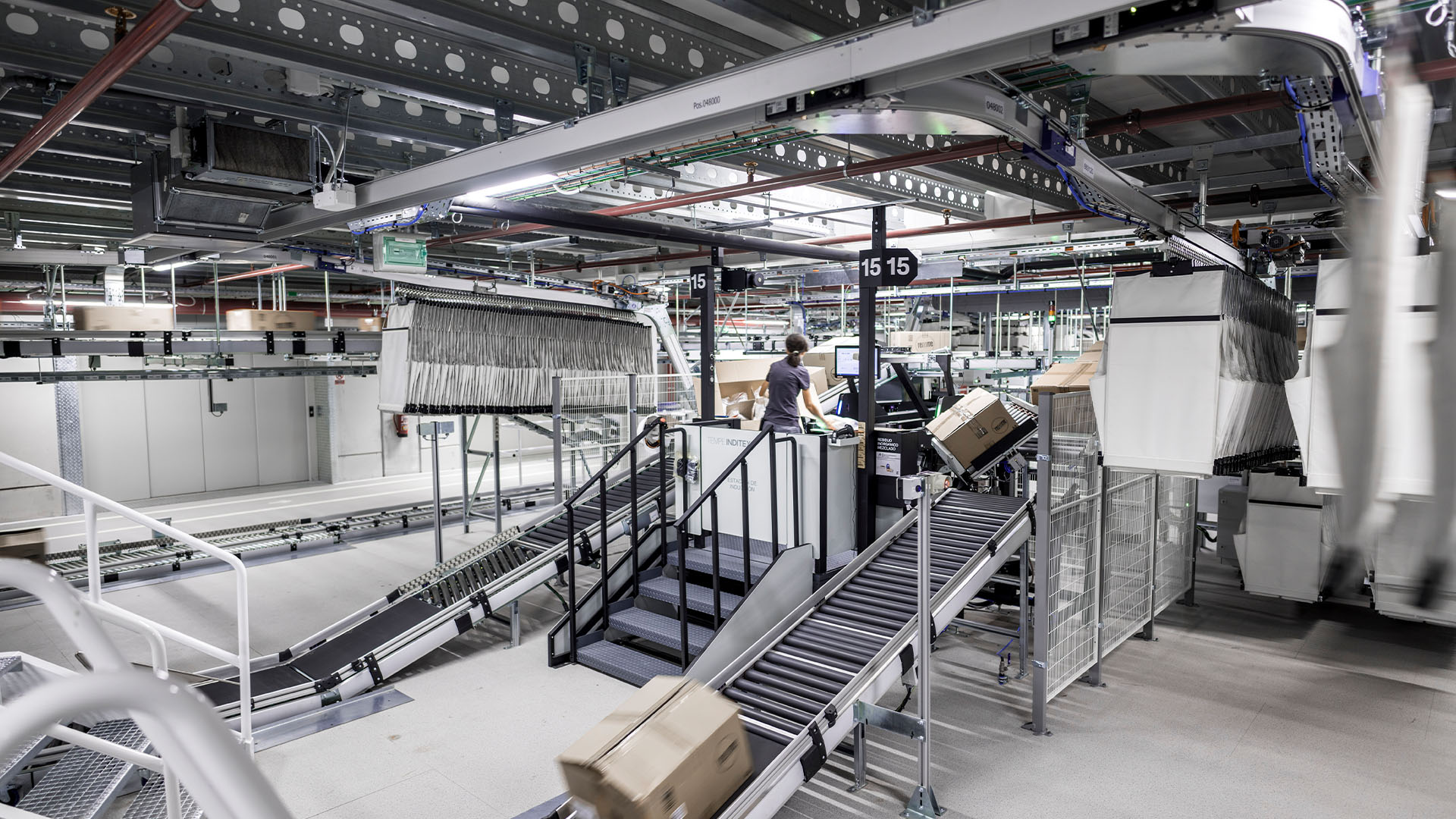
Our long-standing partnership with the Inditex Group is built on mutual trust. From the successful projects of the past, we know Tempe’s requirements and needs, so we can provide optimal support as they work to attain their goals.
Using intelligent automation to prepare for the future
Thanks to the scalable nature of the AutoPocket module, the Inditex Group is well-prepared for future growth. Together, the two sorters process 12,000 items per hour, enough to supply 4,800 stores per day. Tempe also has the option to add another sorter and increase throughput by an additional 6,000 items per hour.
Curious about logistics automation?
Get in touch with our experts today.