AutoPocket takes the Elmsall Drive DC to the Next level
Next plc. is a leading British retailer of high-quality women’s, men’s and children’s fashion as well as of beauty products and modern furniture and decor. Products from Next and third-party companies are available in over 500 stores across the UK and Ireland, with their online presence growing tremendously. On the international stage, the Next group offers their products in around 200 brick and mortar stores, as well as on their online store for customers abroad. Their extensive range of products meets the demand for a wide product portfolio from around 8.6 million customers across the globe.
Let’s take it on is the guiding principle on which Next plc. banks all their areas of business. With around 45,000 employees, the company continually develops their range of products and processes. Having already specialized in fast order processing for years, Next pioneered the next-day delivery segment – deliveries for customers making orders by 11 p.m. arrive at their doors the next day. Only a well thought out and cost-efficient logistics concept makes this service possible.
Pocket sorter module
You are currently viewing a placeholder content from YouTube. To access the actual content, click the button below. Please note that doing so will share data with third-party providers.
More InformationModernization at the highest level
Over the past years, Next plc. has grown at a stunning rate, tackling new business areas, expanding sales channels, increasing requirements and the growing demand for online shopping. To achieve more efficiency in the warehouse and save personnel hours, the company decided to upgrade their existing system in the Elmsall Drive distribution center from the split tray sorter to the newest AutoPocket. The AutoPocket solution was specifically designed to simplify the complex requirements in warehouses and to reduce the time needed for processing customer orders. This ensures smooth and fast delivery to end customers.
For the KNAPP team, this meant integrating the system into the existing infrastructure of the DC. Selecting KNAPP for this project, Next trusts in our innovative technology and relies on our experience in conducting projects such as this one.
Next’s needs at a glance
AutoPocket, our new generation of pocket sorter systems, helps us greatly reduce lead times for orders. I’m very pleased that this innovative solution from the KNAPP group contributes immensely to the future development of Next.
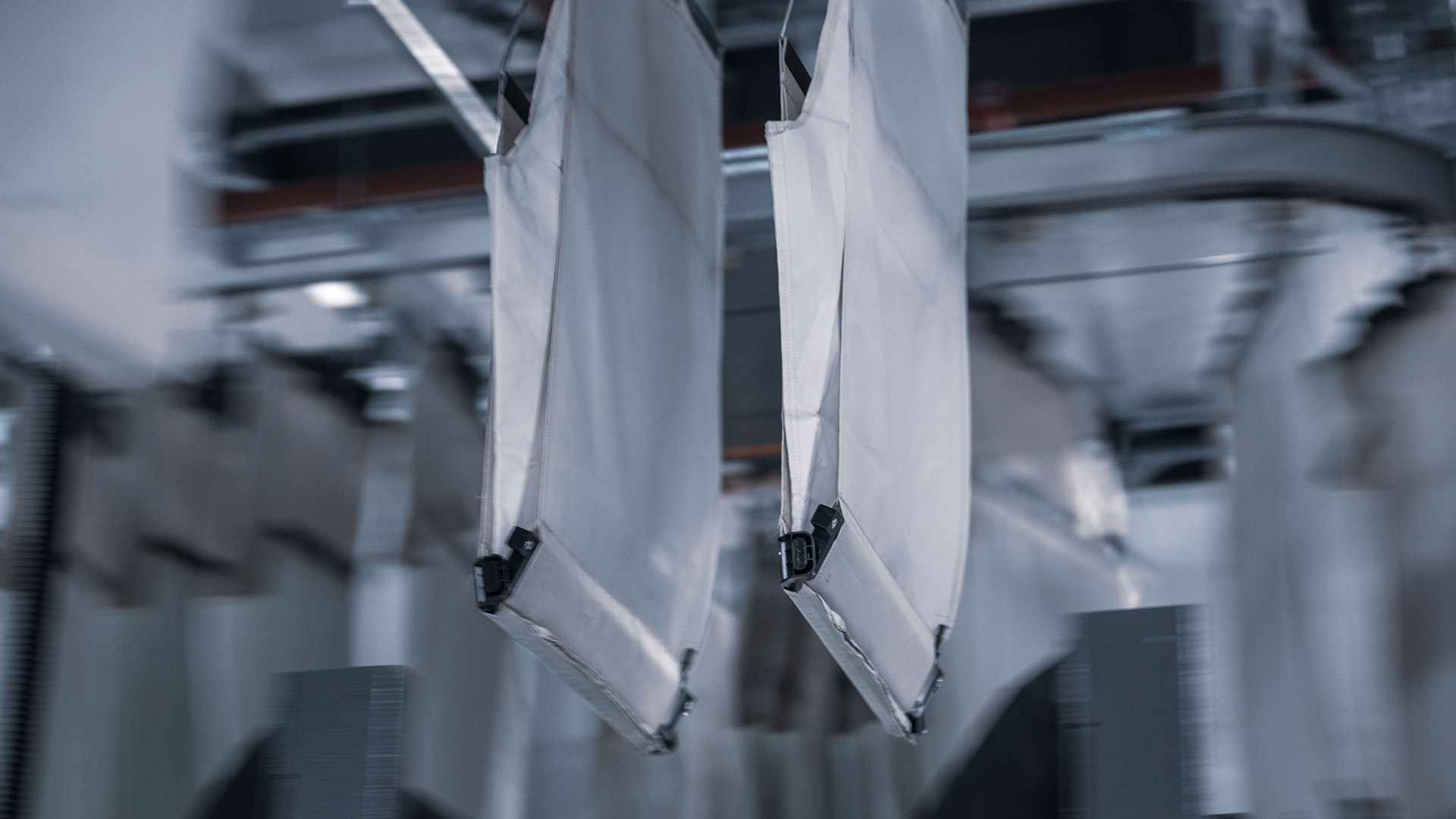
Two challenges, one pocket: order processing and outbound sorting made easy
At Next, AutoPocket provides the solution for two challenges. While two AutoPocket modules consolidate and sort e-commerce orders highly efficiently, an additional module handles sorting in the goods-out area. Combined with intelligent software, AutoPocket meets Next’s high performance requirements and optimizes their goods flow from picking all the way to shipping.
Handling 240,000 items a day
The modernized Elmsall Drive distribution center has been in operation since 2022, from where Next delivers to customers worldwide. But which path do the around 240,000 products take in the warehouse between picking and shipping? Let’s take a closer look at the solution.
The containers filled with items are automatically conveyed to the employees at the pocket loading stations. Both modules have 10 loading stations where around 750–1,000 products are picked out of the containers per hour. Their barcodes are scanned for identification and then loaded into the automatically provided pocket.
From the loading station, the pockets are forwarded to the module distributor, which allocates the pockets to one of the AutoPocket modules depending on the workload. The two modules handle 15,000 items per hour and the distributor ensures that the modules’ workload is balanced, boosting flexibility and order throughput.
Depending on how the distributor allocates the pockets, they are subsequently conveyed to the order consolidation area, with each of the two modules having 14 buffers across two levels. They store individual items temporarily until all parts of the order have been processed and are consolidated. Completed orders are automatically diverted from the rotating buffer to the pack loops by the intelligent warehouse control system.
The filled pockets are buffered in a rotating buffer consisting of six pack loops and a total of 240 packwall chutes until their contents are automatically released at full speed. Across the chutes, the items slide to the pack station.
At 60 work stations supplied with items from a total of 240 chutes, employees pack all the items of an order into a polybag. The polybags are then fed into a take-away conveyor, which is then inducted into the outbound sorting system.
At six loading stations, the completed customer orders are again inducted into the AutoPocket pockets and conveyed to the outbound sorting system, which sorts up to 5,000 packs per hour.
The packs are directly distributed across the 40 courier-specific drop-off points via a separate outbound loop. From the drop-off points, the customer orders are shipped to all corners of the world.
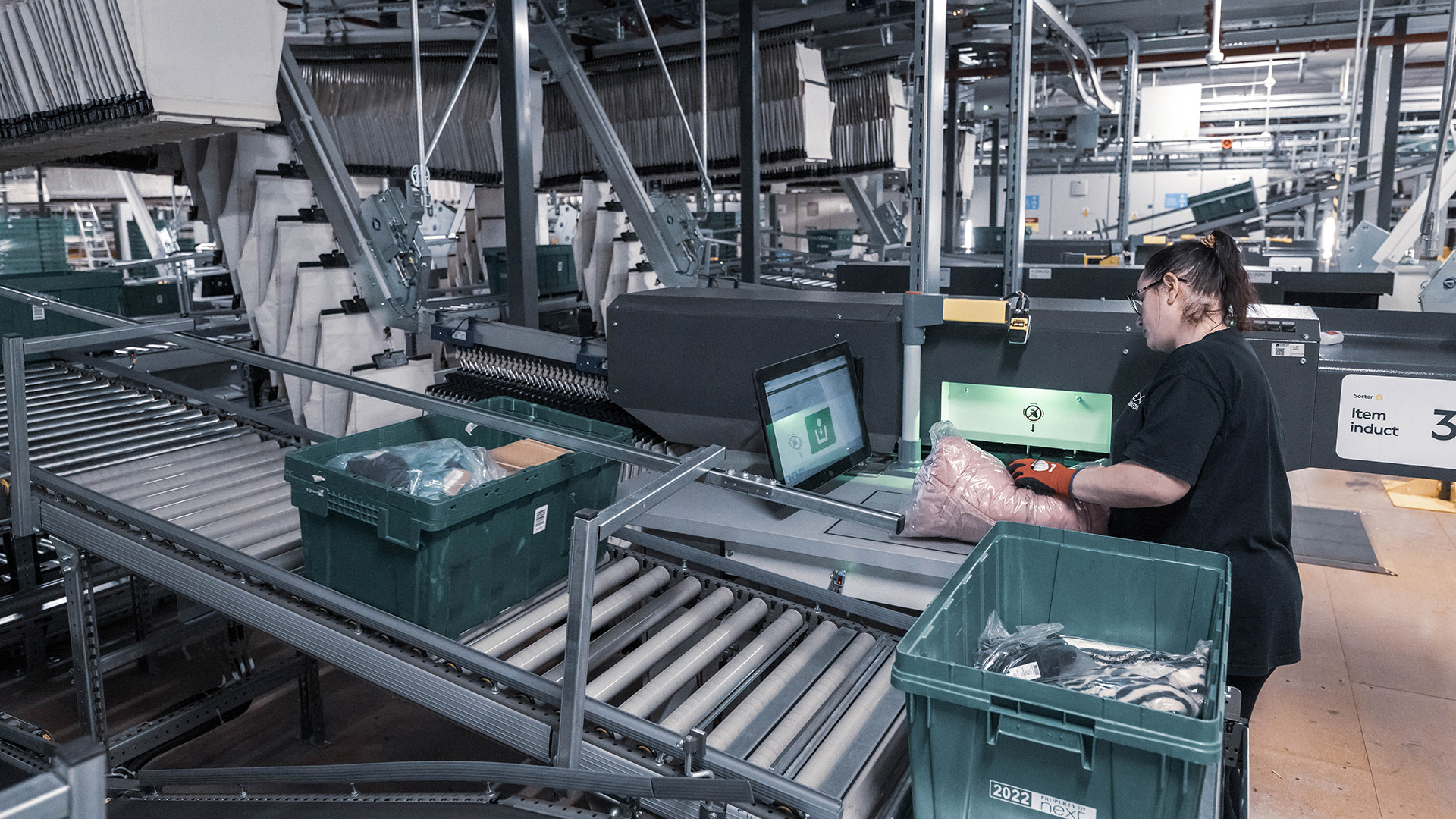
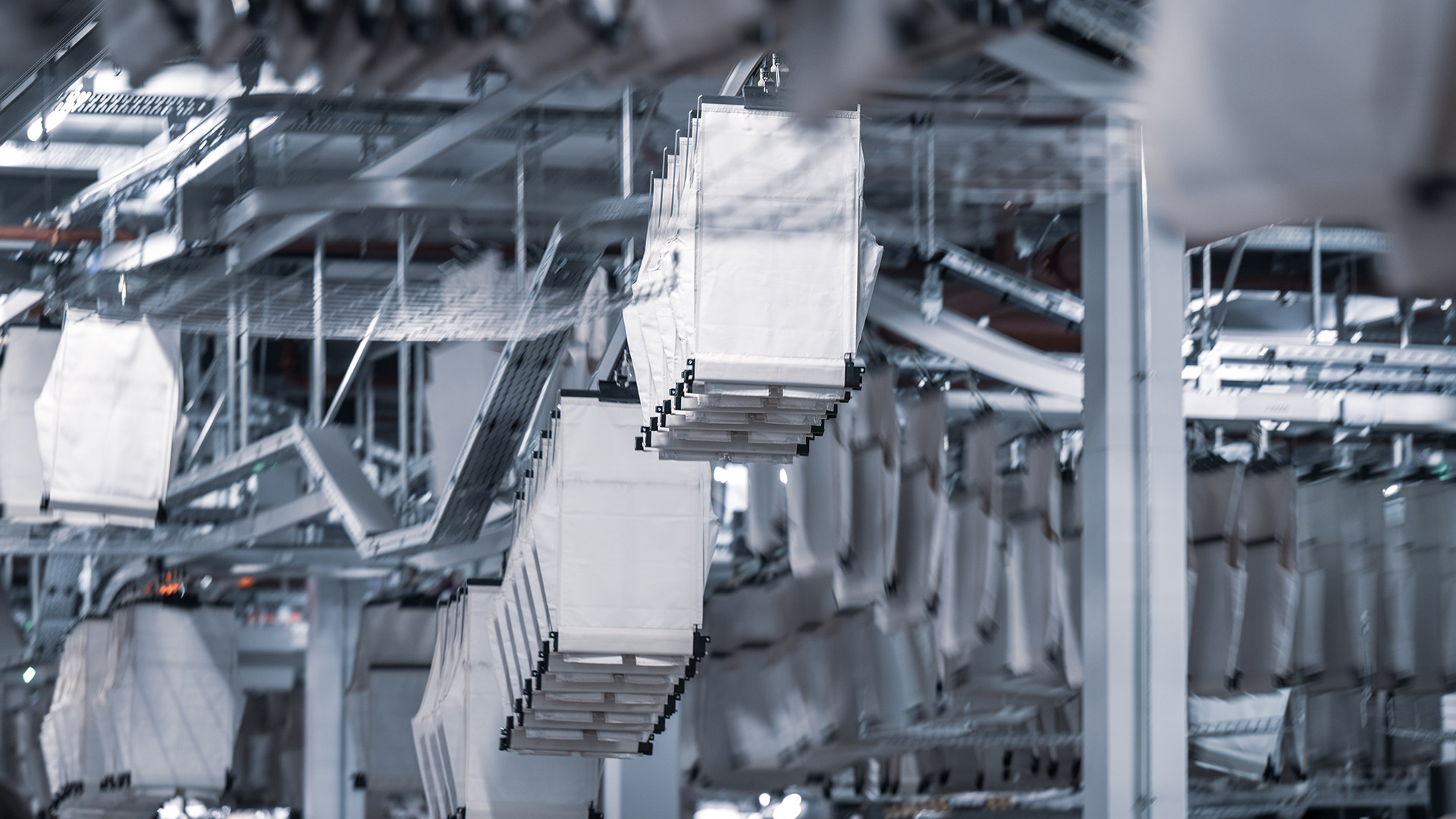
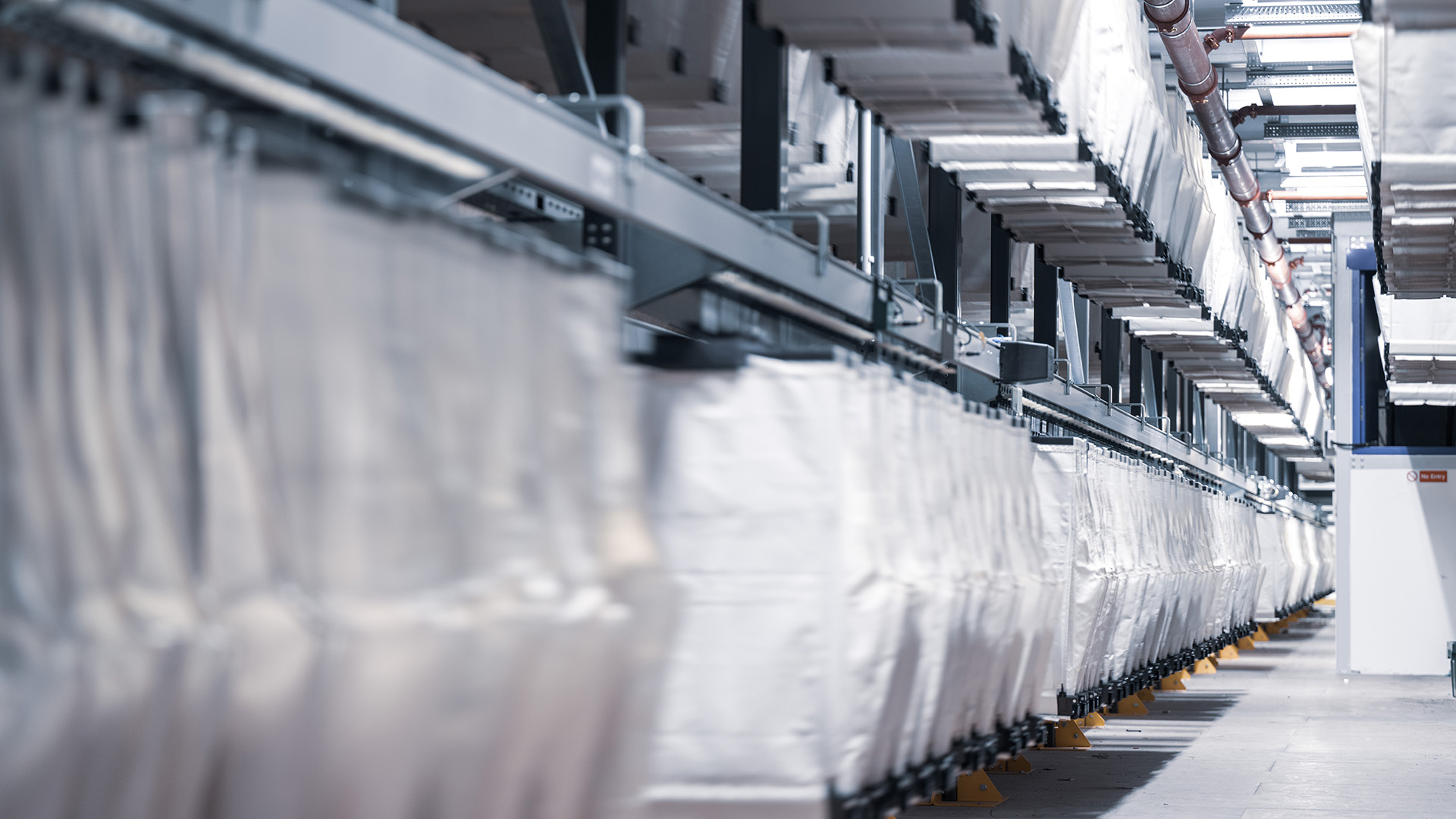
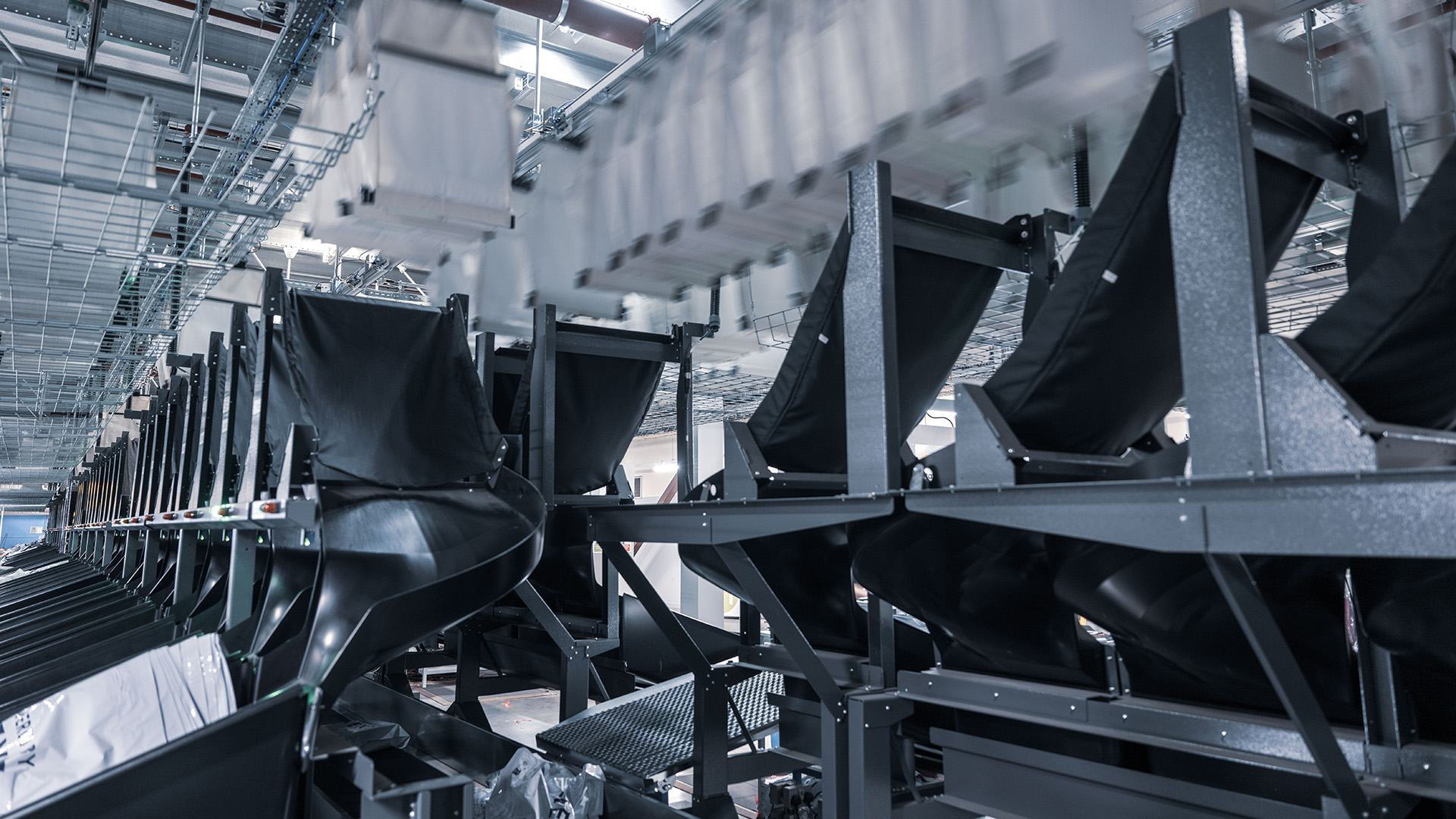
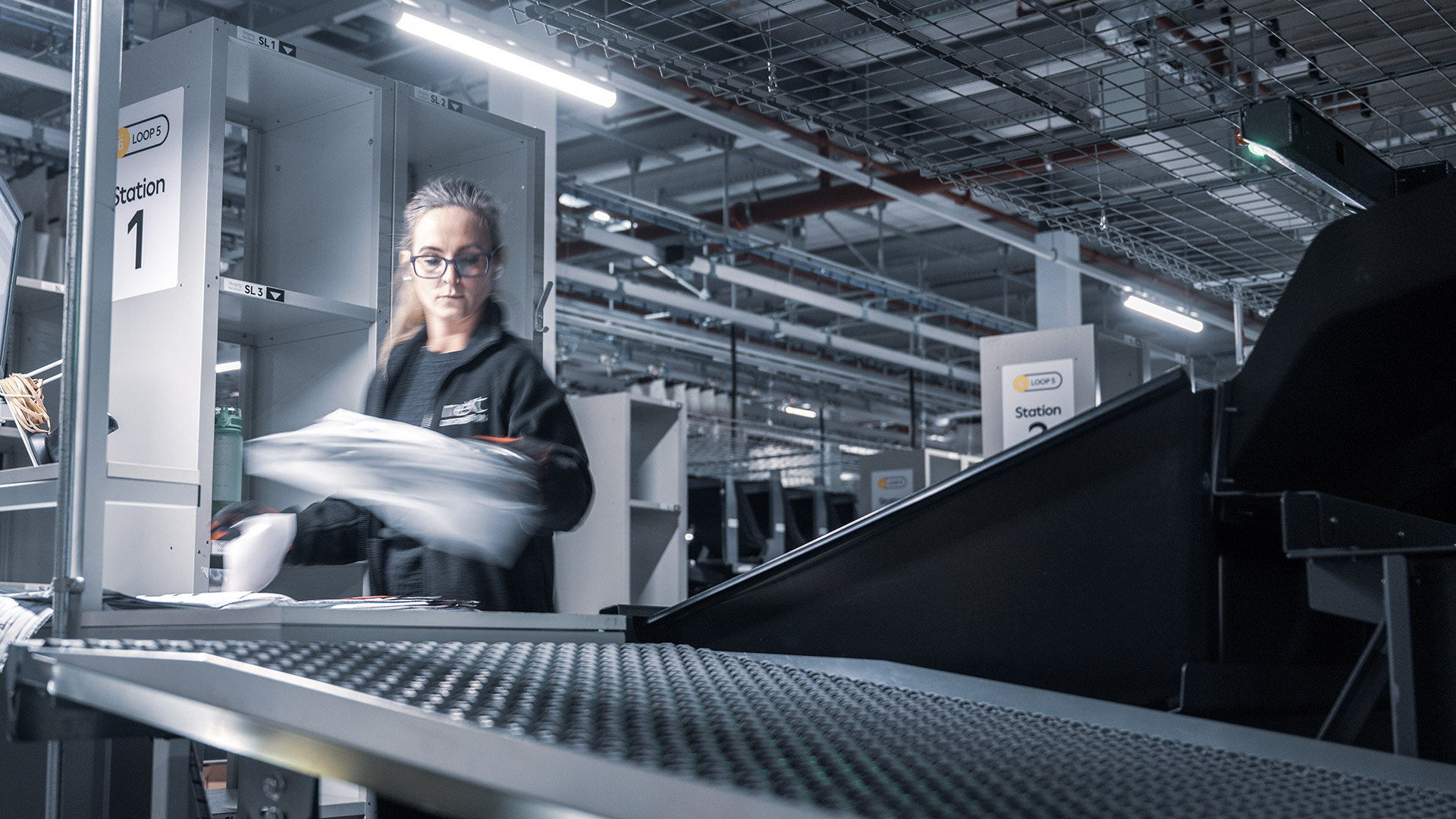
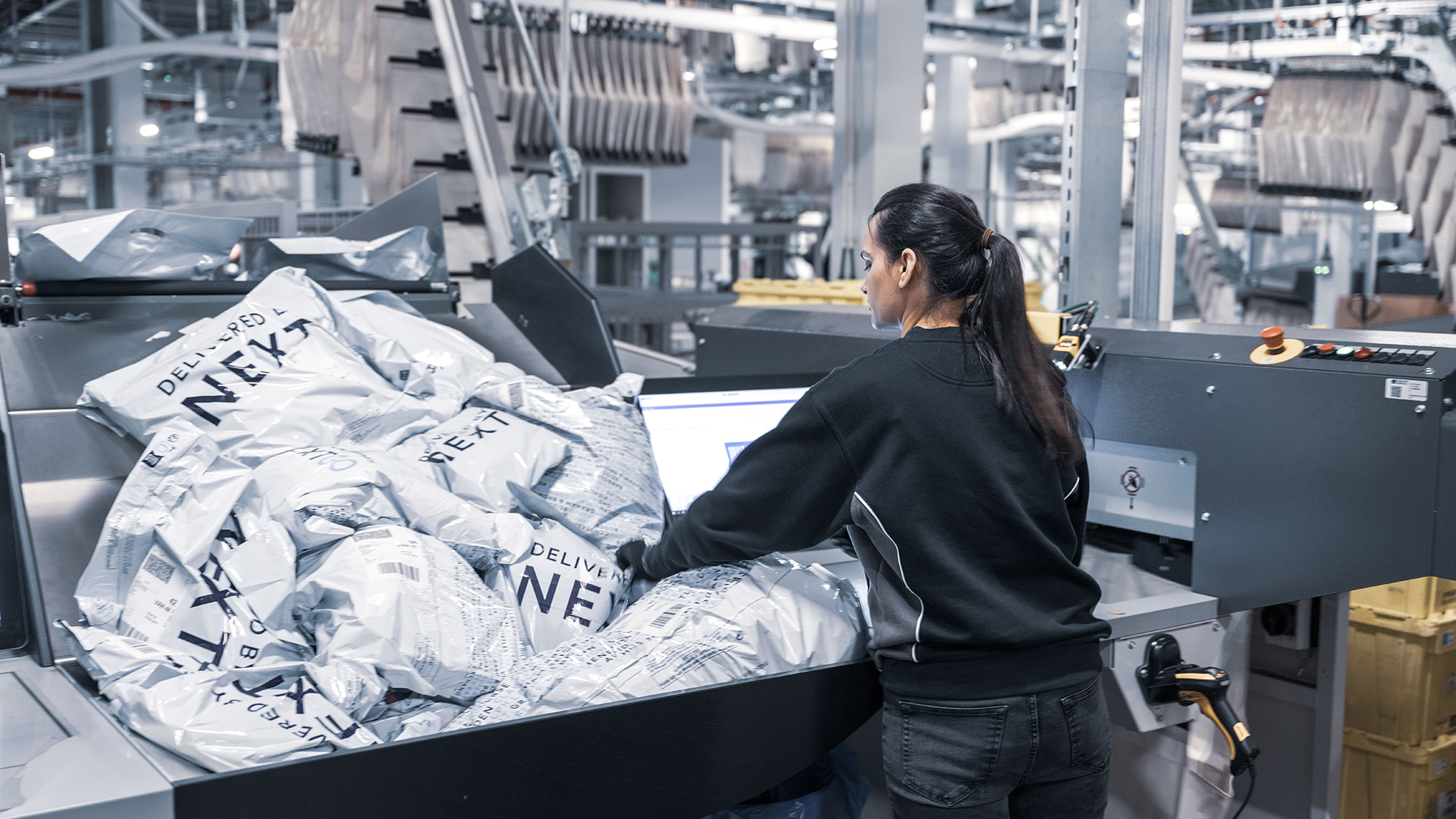
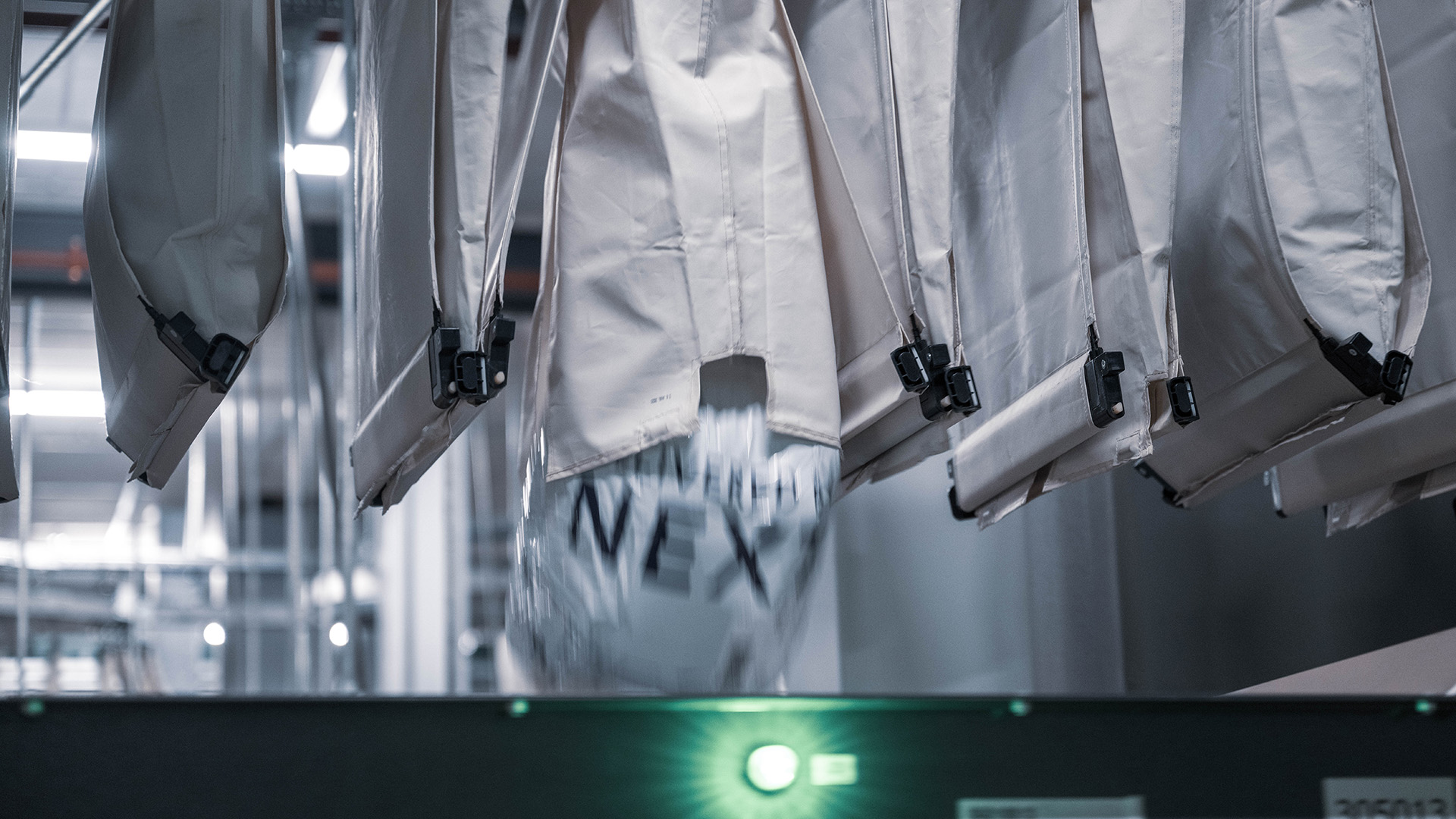
With Next, we share a fantastic, long-standing partnership that is based on mutual trust and reliability. The fact that we have successfully completed another project to continue to support our partner Next in the future makes me proud.
The result: shorter processing times
AutoPocket has become indispensable for Next’s distribution network. The numbers speak for themselves: The two AutoPocket modules handle 15,000 items per hour and, in combination with a separate module, also assist sorting in the goods-out area. The outbound sorting system handles 5,000 packs per hour, shortening lead times all the way from picking to shipping. Next also saves around 35 % in weekly personnel hours in comparison to traditional cross belt sorters.