The production of the future is automated, intelligent and sustainable. But what exactly lies behind the concept of smart manufacturing? Which technologies will be used? What benefits come with them? Join us for a deep dive into the smart factory of the future.
What is driving the development of smart manufacturing?
Smart production processes are key to staying competitive in the manufacturing industry. Automation and digitalization enable companies to act sustainably, work cost-effectively and keep production in their own country. These are all vital advantages, especially because manufacturing is on the verge of change.
Manufacturers everywhere are facing political instability, scarce resources and cost pressure. The shortage of skilled labor and constant changes in the market and environment are also omnipresent factors. At the same time, however, the call for demand-driven and sustainable manufacturing with customized serial production is louder than ever.
Automation in manufacturing and warehousing has become indispensable, not just for large companies, but also for small- and medium-sized enterprises. It’s bringing revolutionary new change to production processes, making them extremely efficient.
What is smart manufacturing?
Smart manufacturing, manifested in the smart factory, uses the most advanced technologies to perfect and automate manufacturing processes. Thanks to the smart integration of people, machines and systems, the efficiency, flexibility and sustainability of a company all increase.
What are the features of an intelligent production facility?
Technologies used in smart manufacturing
In the past, production companies manufactured items in advance and in batches but today, it’s the consumers who set the pace. Planning is therefore more difficult, and the manufacturing processes require a great deal more flexibility. To achieve customized serial production, it takes integrated smart processes and there are a number of solutions that can help companies get started on the path towards their own smart factory.
To implement a smart factory, it takes more than changing or restructuring individual processes. Only when companies automate and digitalize their entire chain of processes can they exploit the full potential of the smart factory.
1 | Data intelligence forms the foundation for success
Smart data is fundamental to success in smart manufacturing. The following three technologies are key to making your business more efficient:
These technologies are used in smart factories to efficiently coordinate the flow of goods. The right information has to be available for every component or item in each process step. A fully integrated software solution such as our logistics software suite KiSoft functions as the “mind” of smart factories.
All the various implemented technologies constantly gather information that is then pooled in a cloud. The software converts this information into smart data, which it then provides to the right user, at precisely the right time. For resource planning or predictive maintenance, this data is incredibly valuable.
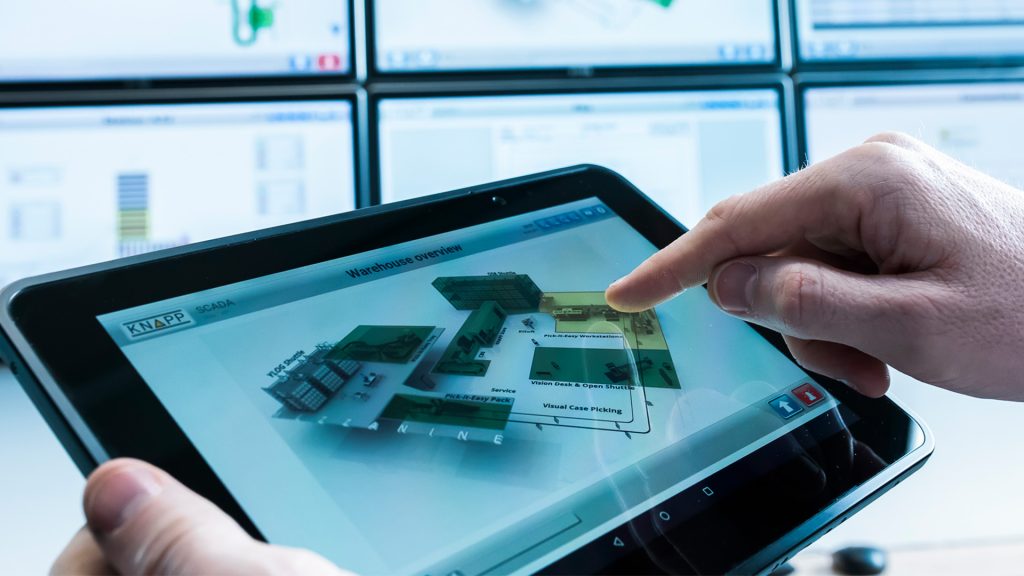
2 | Automation and robotics translate into flexibility and scalability
Where can we store raw materials, semi-finished and finished products, as well as deliveries? How can temporary work stations and production lines be interconnected and supplied with items flexibly? Here, automation plays a pivotal role in ensuring efficient, flexible and reliable production processes. At the heart of an intelligent production facility is a central, automated storage system.
Additionally, autonomous mobile robots equipped with artificial intelligence handle both the monotonous tasks and do the legwork. They bring supplies to various work areas just-in-time and just-in-sequence – fully independently.
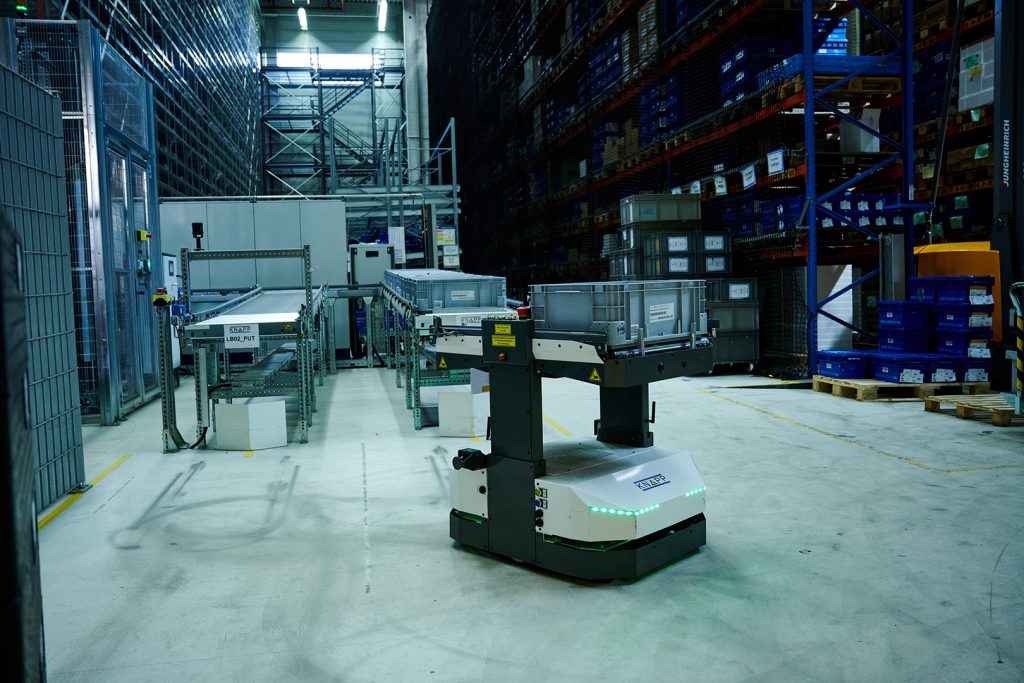
Our autonomous mobile robots, the Open Shuttles, open up new opportunities for designing the flow of goods in smart manufacturing. They automatically move containers, cartons, trays and pallets around the warehouse.
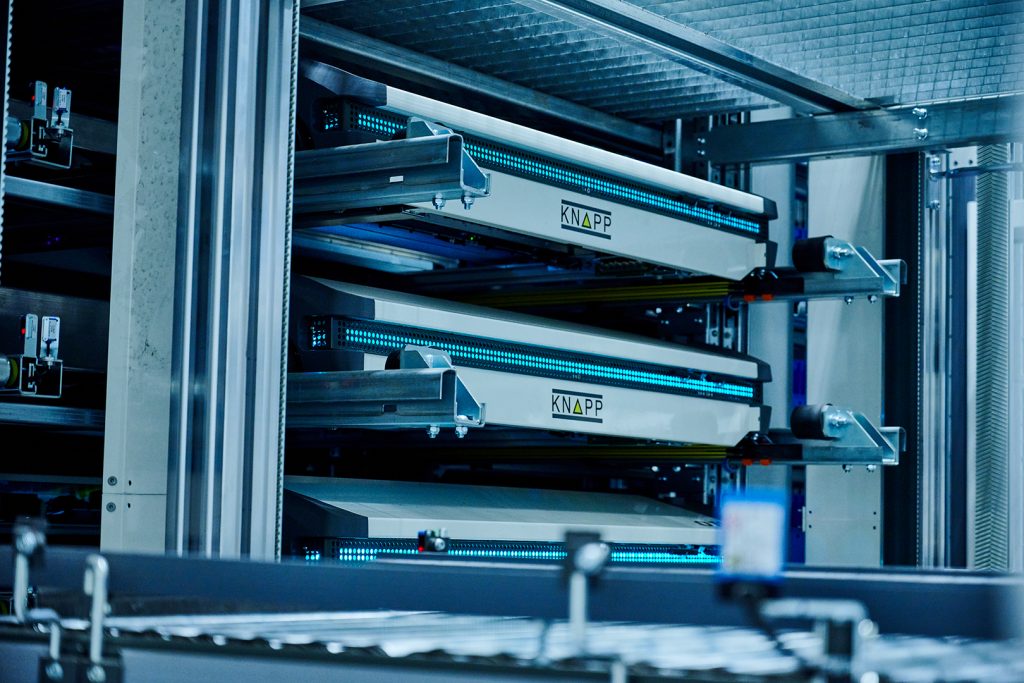
The Evo Shuttle system covers all the central processes in production and distribution automatically. The system centrally unites storage, picking, buffering, sequencing as well as the supply to work stations and work areas.
3 | Digital twin for more planning reliability
The digital twin, aka the avatar of the real system, is the key to greater efficiency in intelligent production facilities. Before startup, systems and processes can be simulated, tested and perfected over the long term. It also is great for optimizing the system during ongoing operation.
Using a digital twin saves time and costs, reduces risk, raises efficiency and perfects quality on all levels. At KNAPP, we have been using digital twins to plan and start up our new automated systems since 2021. We use it primarily for the following applications:
Would you like to know more about how digital twins work? Take a look at our blog post Digital Twins in Logistics.
4 | AI and machine learning ensures absolute quality
Artificial intelligence and machine learning, as already mentioned, are used for predictive maintenance and the autonomous control of the AMR. Furthermore, AI offers even more applications for smart manufacturing such as automated data analysis, decision-making and process optimization.
Here, it is important to mention the quality assurance and quality optimization that AI can provide since every manufactured part must be precisely traceable along every step in the production process. This zero-defect goal is achieved with the help of intelligent software combined with image recognition and image processing technology. Our vision smartdesk, for instance, is a smart work station equipped with an intelligent camera system and is the perfect answer for quality issues.
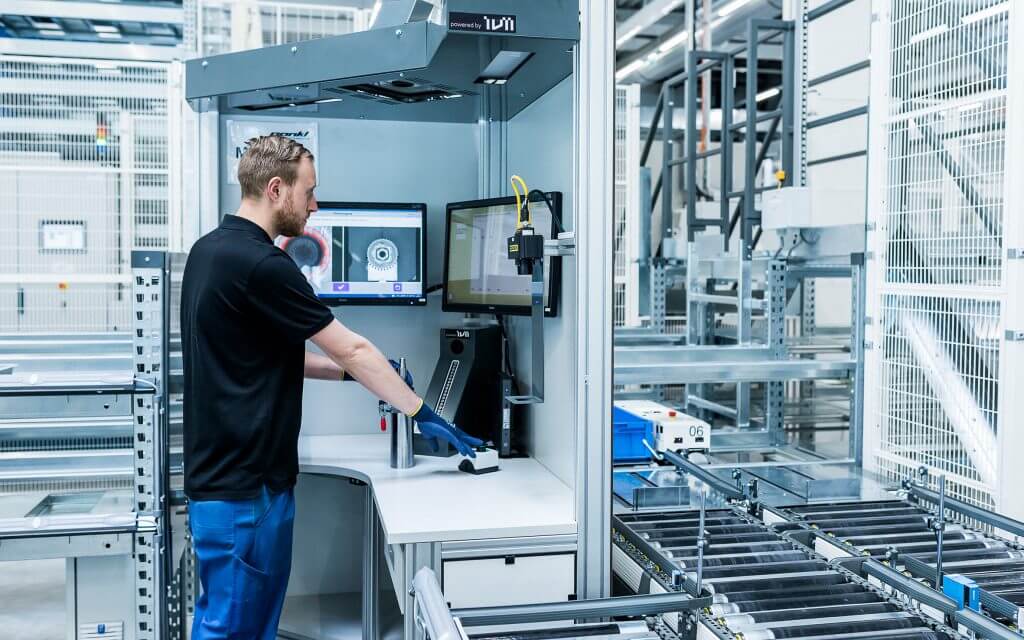
Benefits of smart manufacturing
What advantages might smart production processes have for your company? Here is a short summary of what smart manufacturing can do:
The magic word for the future is ‘demand-driven production’. Today more than ever, consumers want their goods to be customized according to their wishes, which is why items are now mainly produced as needed. In order to supply these new production lines, dynamic systems are needed with stronger integration and interconnection between production and logistics.
Industry 5.0: Humans and technology – the team of the future
What then is the role of the human being in the intelligent production facility that is paving the way for Industry 5.0? Automated production lines already feature heavily in today’s manufacturing. Heading into the future, teamwork between human workers and smart technologies will be needed to meet new demands.
While robots take care of monotonous and strenuous work, and smart software aids in processing and displaying the enormous volumes of data, humans will be smart workers – who use their problem-solving skills and creativity to act as the decision-makers in production. Human motor skills are unmatched, which means that workers will handle machine maintenance but will also assemble complex products with the support of intelligent personal assistance systems.
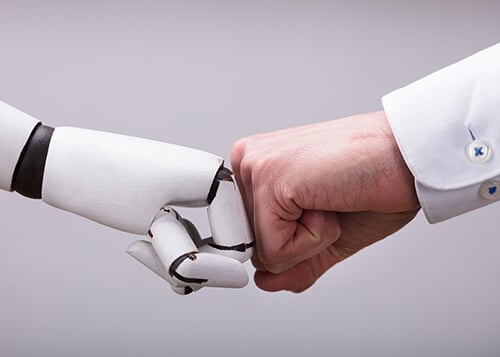
I am sure that in 10 years, it will be normal to have a robot as a colleague. In this respect, it is important to get everybody on board and make it clear that such robots are not the competition but will instead make their work easier.
Smart manufacturing: From vision to reality
Today, a number of companies in diverse sectors are already relying on our intelligent technologies for their smart factory.
Would you like to learn more about these companies? Take a quick look at our case studies:
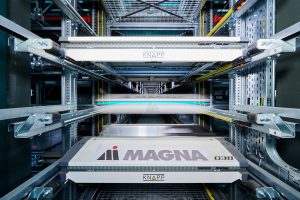
Magna Spiegelsysteme:
Optimizing supply to production and assembly
Thanks to the automated solution, Magna achieved faster availability of parts, a reduction in internal transport and hands-free warehouse operation. An intelligent software package rounds out the smart manufacturing solution.
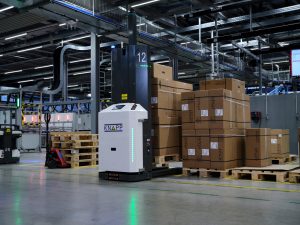
Fronius:
Smart pallet transport by AMRs
The innovative Open Shuttle Fork has automated production supply and internal transport at Fronius. The new solution gives the company the necessary autonomy to flexibly make changes as needed and to manage both manual and automatic transport orders in the same system.
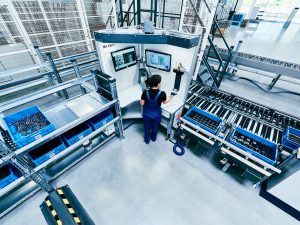
Pankl Racing AG:
End-to-end quality control thanks to intelligent image processing
An automated small parts warehouse supplies Pankl’s assembly work stations according to the goods-to-person principle. Modern image recognition and processing technologies check each step of work, which results in error-free assembly and seamless traceability. Pankl’s manufacturing logistics is a textbook case in smart manufacturing.
We’re happy to tell you more!
Further reading recommendations


Especially in times like these, supply plays a central role. Which trends and market developments are influencing the manufacturing industry? How can we respond to these challenges? The first part of this post on intelligent production supply will focus on these issues.

The demands placed on production and logistics today are manifold. Combining an automatic storage system and autonomous mobile robots allows you to automate countless processes intelligently and flexibly.
Additional Information
Find out more about our solutions for warehouse automation for manufacturing >