PC Electric is a worldwide leader in the development and manufacturing of industrial plugs and sockets, with an export rate of over 80 percent. Despite comprehensive automation in production, the company had been transporting empty containers manually for the past 20 years. In order to automate their empty container transport, PCE decided to implement the Open Shuttles, which involved building a special load-handling device for the Open Shuttles. By using AGVs, the new automation solution simplifies processes, makes work more ergonomic and frees up resources for value-adding activities.
We caught up with Daniel Lechner, Director of Automation and Tobias Aichinger, Head of PLC Programming and Robotics at PC Electric (PCE) to talk about working together on development and the new solution.
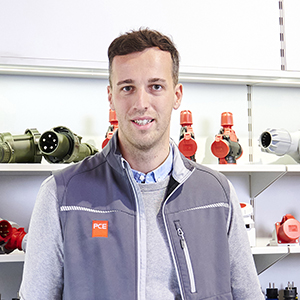
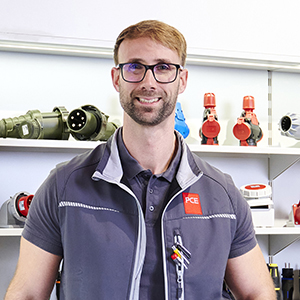
PC Electric focuses on connecting people to technology
PC Electric is an Austrian company with a product range of more than 22,000 items. Their export rate is over 80 percent. What makes PC Electric so successful around the world?
Lechner: Our success is thanks to our one week lead time in production. This makes us very strong in the market, with our numbers speaking for themselves. At our St. Martin location in Upper Austria, we produce about 700,000 plugs and sockets a week in our highly automated production plant. This includes CEE plugs and sockets, Schuko items, wall distribution boxes and everything needed for the distribution of power. Our subsidiaries at six other locations sell related items. Our Austrian location is our central hub and home to our research and development activities.
What is the company strategy? What does PC Electric focus on?
Aichinger: PCE is a family-run company with a flat hierarchy. We are very demanding when it comes to the quality of our products and, of course, the safety of our employees is very important to us. Working ergonomically is always in focus, which goes hand in glove with a greater emphasis on sustainability. We want to automate processes, link people with technology and work as comfortably as we can. The automation solution is a perfect example of optimizing strenuous tasks and how it benefits employees.
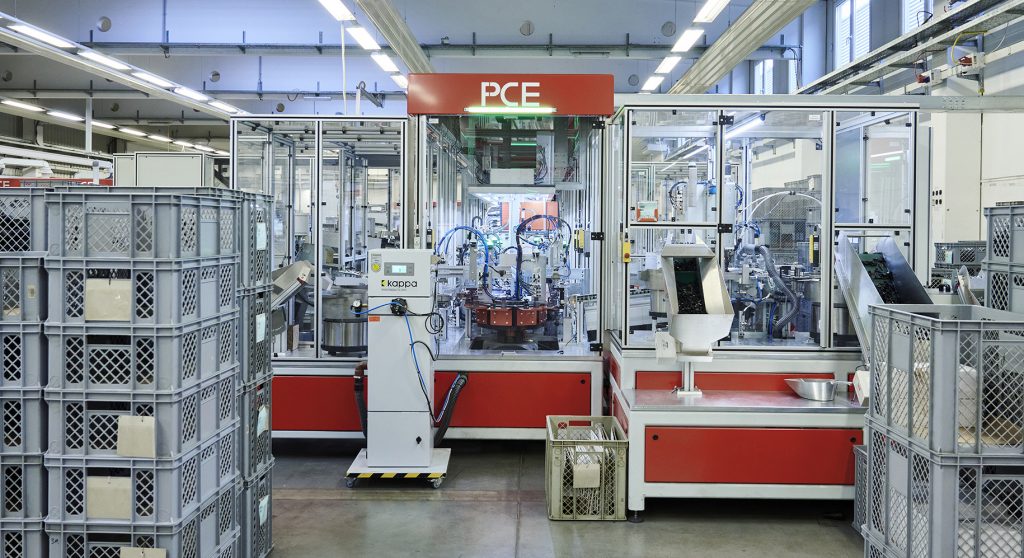
New automation solution featuring Open Shuttles is flexible and space-effective
What was the challenge in production that necessitated a new automation solution?
Lechner: In the past 20 years, nothing was undertaken to adapt the empty container transport from the packing area back to production. Because the aisles were narrow, only half the container transport distance could be covered by a forklift truck. For the first half of the distance, employees were pushing stacks of containers along a roller conveyor with no electric drive. Order volume, however, has gone up significantly, to about 1,200 boxes a day. It’s obvious just how much work was involved in transporting the containers manually.
It was important to us to simplify the empty container transport, to move forward with making work more ergonomic and to free up resources. So we optimized the entire transport process, in this case, with KNAPP.
You decided to handle empty container transport using the Open Shuttles. Why did you choose this solution?
Lechner: We considered how we could make empty container transport simpler, easier. We thought about a conveyor belt that would run through the entire assembly area. However, we are growing very rapidly. The halls are always being rebuilt and work in the assembly area is already in full swing. A conveyor belt here seemed to offer too little of the flexibility we needed. We wanted a flexible, space-effective automation solution for the future.
AGV automation solution - overview
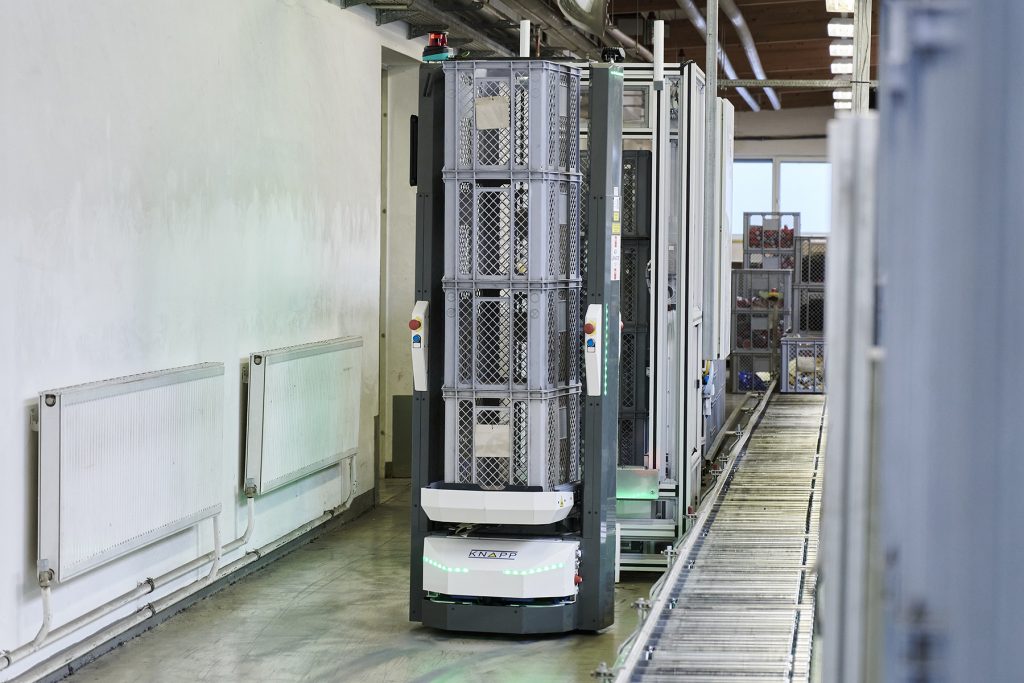
Partners for developing optimal internal transport
The new automated guided vehicle system offers a high degree of flexibility. The system can be expanded indefinitely, and you can easily integrate new processes yourself. Furthermore, a new solution for empty container transport resulted from close collaboration during the development phase. What does it look like?
Lechner: The development departments of KNAPP and PCE worked together closely during the automation project. For transporting empty containers, a special load-handling device (LHD) was developed to stabilize the stacks on the Open Shuttles at PCE. Thus equipped, the autonomous mobile robots can transport stacks reaching up to 1.6 m (5 ft 3 in) in height.
How is it going with the new Open Shuttle solution? How satisfied are you with the new system?
Aichinger: The process is very stable. During startup, the process was continually optimized and regular updates flowed in. We’ve now reached the point where we can say that it’s a very good system. Now the challenge is to find other processes to implement together with KNAPP.
Lechner: As we said: We wanted to do a flagship project where we could delineate everything well, without a lot of influence from external factors. The transport of empty containers was perfect because it was simply about transporting boxes from point A to point B. It was relatively easy, the path was straightforward and the aisle widths were sufficient. We tested the system successfully with one shuttle. We’ve already ordered the second and there are likely to be more in the future.
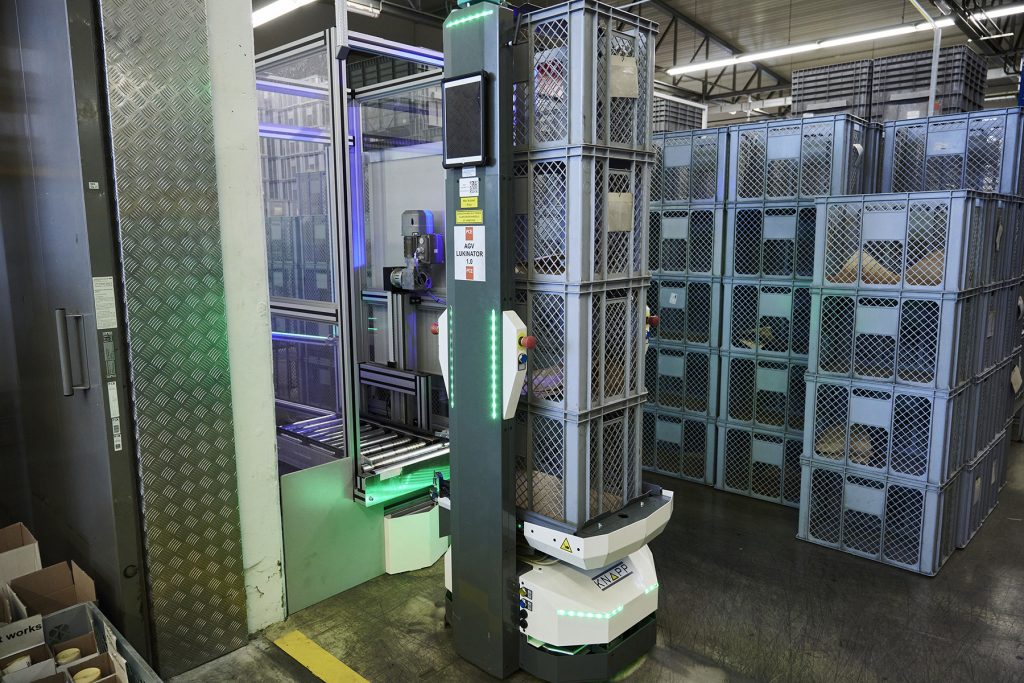
An automation solution with AGVs for the big picture
There are many automated guided vehicle systems on the market. Why did PCE decide on a KNAPP logistics system?
Lechner: The main advantage was that KNAPP really saw the big picture. While shuttle system startups are everywhere, these businesses are selling shuttles without support and without a solution, which is just not the right approach for us. Sure, you can get a shuttle installed, but then you’re missing the experience as to what really does or does not work with it. We wanted a renowned company offering good service and with KNAPP, we got all the information we needed. Working together went really well, and right from the start, we were communicating on the same level, technically speaking. And that’s how you end up getting a really great solution. It’s the reason why we decided that KNAPP was the right partner for the implementation of the solution.
It was important for us to have a partner who would continue to assist us beyond project completion. KNAPP is a prestigious company and a stable, secure partner.
How would you describe your collaboration with KNAPP? How did the project progress?
Lechner: It was very clear that project management was taken very seriously. We had a representative and it was always clear to whom we could direct our questions. When processes and interfaces are clearly defined, everyone benefits. Of course, there were a few complications here and there, but we were never left hanging. In the end, what matters in a project is success and performance.
Aichinger: KNAPP definitely delivers on service, customer care and support and we are very satisfied
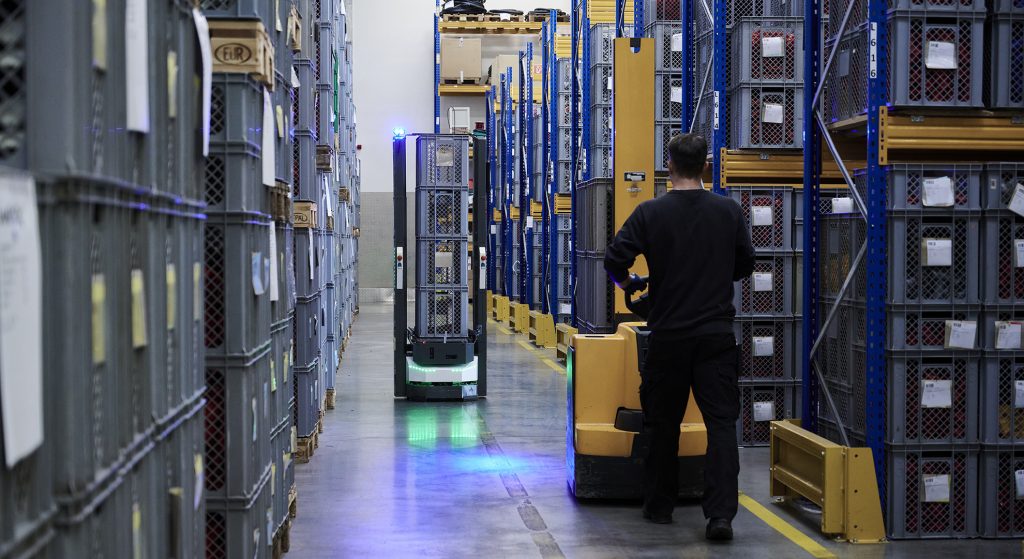
Further reading recommendations


Flow meter manufacturer Digmesa automates production using an Open Shuttle. Learn more about the flexible solution in an interview with managing directors of the Digmesa Group.

Especially in times like these, supply plays a central role. Which trends and market developments are influencing the manufacturing industry? How can we respond to these challenges? The first part of this post on intelligent production supply will focus on these issues.