Legislation for safe medicines focusses on the patient. The burning question for logistics partners in the supply chain is just how to completely and safely integrate into the existing supply chain the seamless traceability from producer to the patient of every single medication.
What affects the sector also affects KNAPP. As industry partner, KNAPP constantly takes on the trends, demands and issues in the sector and delivers the right answers with specially tailored solutions. One example of this is the zero defect warehouse which combines quality and process reliability with the highest efficiency.
Error-free – the key to a successful supply chain
In the interplay between quality, efficiency and performance, KNAPP relies on a mix of established technologies, such as:
- Reliable Central Belt Systems for high-performance order picking
- Smart shuttle solutions for central, secure and space-effective storage of the article range
- Versatile KNAPP-Stores for efficient picking, automated goods-in handling, and easy handling of returns
- Innovative Vision systems for quality assurance and checks
- Modern work station design: Intelligent picking robots and ergonomic goods-to-person work stations for optimal use of resources
- Completely integrated warehouse management and warehouse control software for the control and optimization of all processes.
By combining these intelligent technologies into tailored solutions for the demands of the healthcare sector, error-free warehouse operations become a reality, creating added value for patients.
End-to-end traceability for patient safety
The zero defect warehouse also forms the foundation for legal conformity for improving patient protection based on the Drug and Supply Chain Security Act (DSCSA) of the FDA in the USA, and, particularly in Europe, on the implementation of the Falsified Medicines Directive (FMD). Coupled with this are new restrictions that apply from the manufacture of a medicine to the acceptance by the patient at the point of sale.
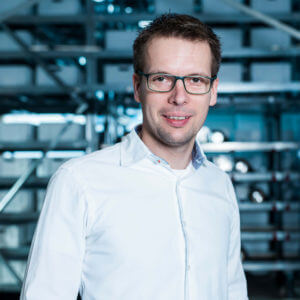
„All prescription drugs and certain non-prescription medications must be marked with security features by the manufacturer. This includes machine-readable 2D Data Matrix codes that hold information on the article in addition to a unique serial number. This serial number is saved in a database by the manufacturer, and, as long as the article does not leave the secure supply chain of authorized partners, is checked again at the point of sale when given to the patient, usually at the pharmacy. This ensures end-to-end traceability.“
Security features and the duty of documentation
Under the FMD, in force in all countries of the EU since February 2019, the Good Distribution Practice (GDP) has become even more significant. In addition to the regulations applying to warehouse processes with respect to storage, protection from light or temperature, these guidelines lay out a duty of documentation for all medicines that have a security feature. Date mark, the name of the medicine, quantity, supplier, customer and the lot number of the medicine must all be recorded.
Lot tracking begins with the first data entry in the warehouse and continues through picking and goods-out:
- The warehouse management software KiSoft records all inbound deliveries and integrates them in to the warehouse stock. At this point, the first check for quality is carried out: The goods are counted and their quality is checked.
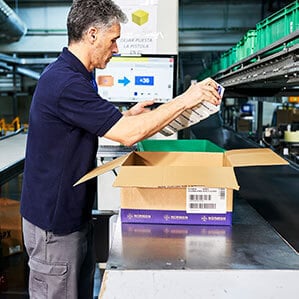
- Only one variant of the article with respect to article type, lot and date mark is stored in each storage container.
- Since every storage container in the system can be clearly identified, from this point on, the tracking of the article in the warehouse is ensured.
- During picking at the OSR Shuttle™ Evo or during manual picking, for example, using RF terminals, the warehouse worker assigns the recorded article information to a customer order.
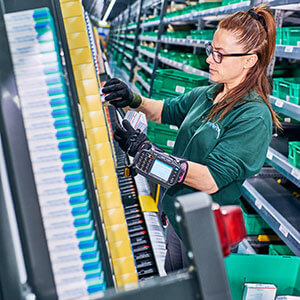
- All processes for quality assurance in the warehouse, such as error correction or quality checks also offer the opportunity to check article information and to correct it if necessary.
Seamless tracking throughout the entire warehouse and on to the patient
Seamless tracking of lots is guaranteed throughout the warehouse: Article data is recorded during goods-in and autopicker replenishment and picking by KNAPP systems are completely guided. Track & Trace can also be used as the system for tracking picked orders from the moment the orders leave the warehouse to the moment they are handed over to the patient.
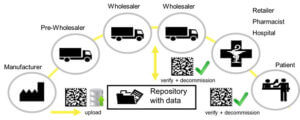
With the right mix of smart technologies and software, KNAPP can fulfil all the needs with respect to serialization and lot documentation for small manual warehouse as well as for fully-automatic warehouses, without the customer suffering any loss of system performance. Freedom from errors in the warehouse also creates sustained added value for patients.
Further reading recommendations

The Voigt group is undertaking an ambitious project in an effort to set the right course for the future. Voigt chose SAP EWM in line with their SAP IT strategy, with KNAPP as their implementation partner.

Pick-it-Easy Evo: The all-in-one work station promotes the warehouse worker to the role of smart worker. Furthermore, it turns a simple work station in storage and production into an experience.
Additional Information
Would you like to know more about our solutions for the healthcare sector? For more information, please visit: Healthcare Solutions