Automated guided vehicles (AGVs) and autonomous mobile robots (AMRs) have one task: to transport materials in a warehouse from one location to another. But that’s all the two types of automated guided vehicle systems have in common as these two systems could not be any more different in design. Read on to learn about:
- The differences between AGVs and AMRs
- The pros and cons of both systems
- The costs of AGVs and AMRs
From AGVs to AMRs
For many years, AGVs were the only option for automating internal transport tasks. They came into use in the 1950s and 60s and quickly took over physically demanding, monotonous and repetitive tasks and material flows.
As the industry developed and the demand for mass customization grew, so did the demand for more flexibility and scalability in transport systems. Flexibility requires intelligent systems and the first autonomous mobile robots entered the market in the 2010s. AGVs and AMRs have been a part of everyday life in logistics for years, but explaining the difference between them remains a challenge. Let’s start by defining both terms before we explore the differences.
What is an AGV?
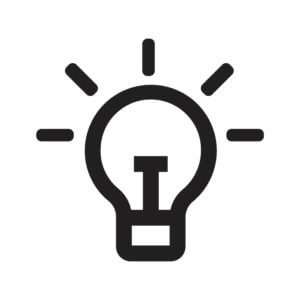
Automated guided vehicles are vehicles with their own drive unit that move on a specific, defined path. They are steered automatically and can therefore transport goods without operator attention. However, AGVs can only drive on a predefined route. They are also equipped with reflectors and sensors and navigate with the help of markings or inductive loops.
What is an AMR?
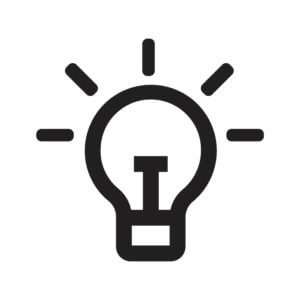
In contrast to AGVs, autonomous mobile robots move independently through their environment and act in real-time thanks to digital warehouse maps paired with cutting-edge sensors and AI that allow them to independently detect obstacles and avoid them.
AMRs vs. AGVs
AGVs and AMRs both fulfill the same tasks. Both systems are a quick and easy way to connect different warehouse areas and provide them with materials. However, AGVs and AMRs are equipped differently and have their own pros and cons depending on their areas of use.
We’ve compared the following aspects of the two transport systems:
Navigation: autonomy vs. set routes
The biggest difference between AGVs and AMRs is in how the systems navigate. AGVs transport goods on set routes and cannot deviate from them. They orient themselves using artificial landmarks such as wires, magnetic strips, optical markers or reflectors that allow them to localize. This makes planning transport routes very labor-intensive and frequently requires modifications to the warehouse.
AMRs, on the other hand, move autonomously. They navigate using maps that are either uploaded to the AMR or are produced by the AMR itself. Cameras, sensors, laser scanners and intelligent software allow AMRs to automatically calculate the shortest route to their destination while adapting to the information they receive in real time.
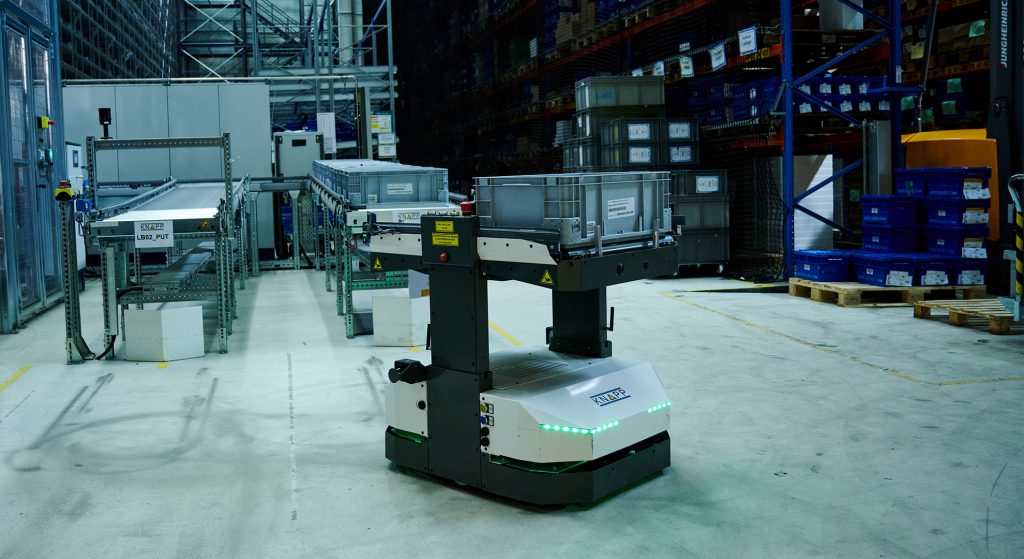
Safety: avoiding obstacles vs. automatic stops
Thanks to their technologies, both AGVs and AMRs are completely safe to use in warehouses. Both systems have safety scanners and are often also equipped with cameras and numerous other sensors.
What makes them different is how each system handles obstacles. AGVs stop when an obstacle blocks their path and waits for the path to be cleared, while AMRs drive around obstacles before finding a new path to their destination thanks to their artificial intelligence.
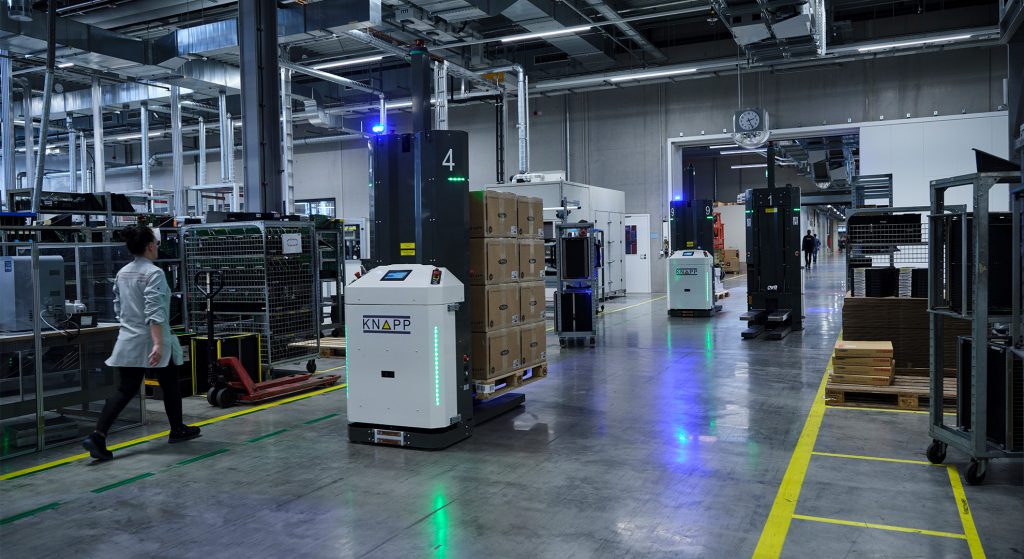
Installation: during operation vs. construction required
AMRs’ ability to navigate, paired with their intelligent software, means they place very few demands on their environment. They can be integrated into internal transport processes quickly and without any need for construction or modifications, even during on-going operation. They don’t need much space to perform their transport tasks and can even navigate very narrow passages.
AGVs, however, are a different story. Planning the route network requires a lot of work and additional construction often has to be performed in the building, which means installation can only be done if operation is interrupted.
Flexibility: scalability vs. fixed system
Thanks to their autonomy, AMRs are much more flexible than AGVs, which travel on fixed paths. The paths and fleet size of AGVs are difficult to change without additional construction.
AMRs, on the other hand, adapt their routes and processes using intelligent software. The fleet size can also be changed as required, such as to cover peaks or react to changes in the market.
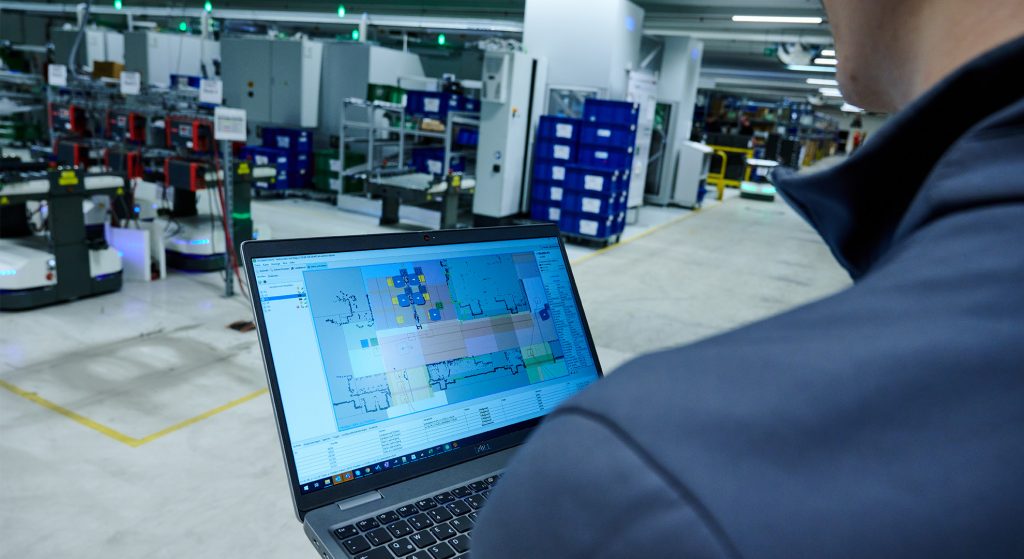
Reliability: difficult to predict vs. easy to predict
The tasks carried out and paths taken by AGVs are very simple and straightforward. Transports are always carried out the same way, travel paths don’t change and the vehicle stops if an obstacle is in the way. These factors means that AGVs are very predictable; their actions are plannable. They are punctual and highly efficient in performing their transport tasks.
Meanwhile, AMRs’ travel paths are often harder to predict. Their autonomy means people cannot predict how they will go around obstacles or what new route they are planning. As far as predictability is concerned, AGVs definitely have the upper hand.
Applications: flexibility of both systems
Originally, AMRs were used to transport lighter loads, while AGVs transported pallets. Today, their areas of application hardly differ at all. Both automated guided vehicle systems perform a variety of internal transport tasks. The most frequent uses include supplying work stations and production lines, supporting the picking process and providing connection to conveyor systems or automated storage systems.
Both AGVs and AMRs can be adapted to meet the customer’s needs. Autonomous mobile robots have also experienced tremendous development in the past few years. The intelligent transport robots can even transport pallets, as our Open Shuttle Fork shows. Here you can see our solution for internal pallet transport in action at Fronius.
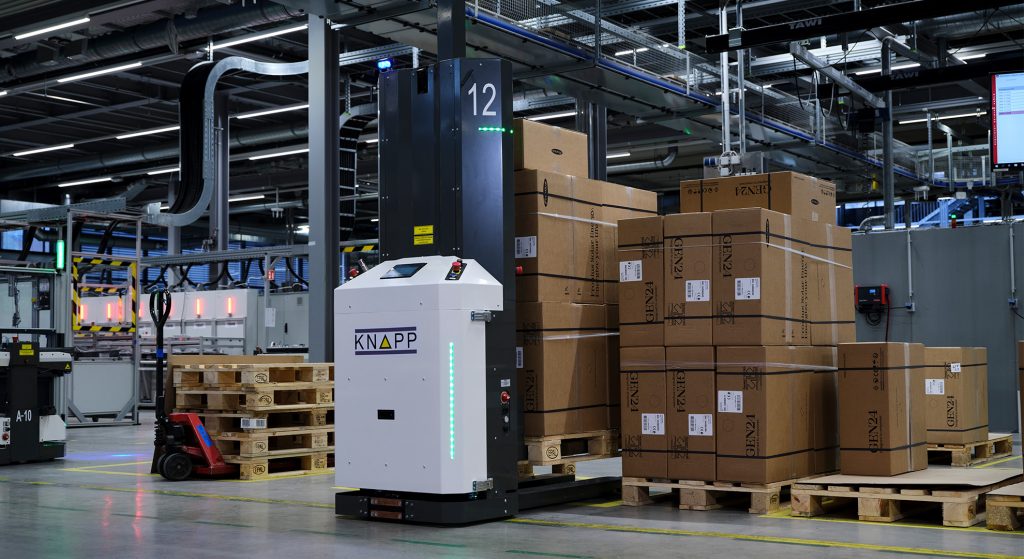
Investment: intelligence vs. price
Which automated transport system is more cost-efficient? At first glance, the acquisition costs of AGVs are often lower than those of AMRs, which are more expensive due to their intelligence and complex sensors. However, once the costs of modifying the warehouse to accommodate the AGVs are taken into account, including the more complicated planning and commissioning, costs are frequently higher.
In addition, startup often requires production to be stopped if the AGVs are not being built into a new system. These interruptions can be costly. AMRs, on the other hand, can be implemented quickly and increase efficiency immediately. Later changes made to an AMR system are also much faster and easier to carry out.
AMR vs. AGV fact box
AMR |
AGV |
|
Navigation |
Autonomous; artificial intelligence |
Line-guided navigation; no artificial intelligence |
Safety |
Navigates around obstacles |
Stops for obstacles |
Installation |
Fast and easy |
Requires construction |
Flexibility |
Fast and easy to change/scale |
Difficult to change/scale |
Reliability |
Difficult to predict |
Very reliable |
Scope of application |
All types of internal transport tasks |
All types of internal transport tasks |
Investment |
Higher acquisition costs; no construction required |
Acquisition costs low; additional construction costs |
AGVs vs. AMRs – which is the better choice?
Are you now wondering which criteria need to be taken into account when choosing an automated guided vehicle system? The following questions are decisive when deciding between AGVs and AMRs:
- Which transport tasks does the system need to perform?
- Does the system need to be changeable and scalable?
- Are goods flows constant or highly dynamic?
If travel paths remain the same, if material flows are constant and if there is a low number of obstacles, AGVs are preferable. They are lower-cost and perform all their tasks precisely and reliably. However, if paths and transport tasks vary, AMRs are definitely the better choice.
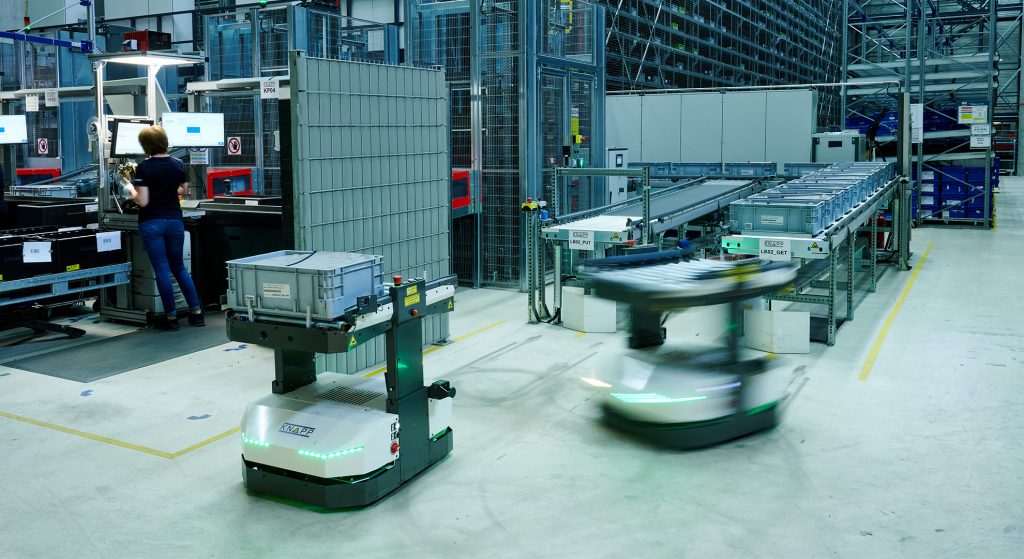
And change is a fact of life, especially in today’s market. We’re all struggling with decreasing plannability, the shortage of qualified personnel and resource shortages. As a result, it’s of utmost importance that today’s automated guided vehicle systems are fast to integrate and adapt. A modern production environment should not make itself dependent on inflexible technology. In short, AMRs are superior to AGVs in terms of flexibility, scalability, installation time and profitability.
However, planning a complete automation solution is much more than just deciding between AGVs and AMRs. They’re often part of a hybrid solution consisting of a mixture of automated guided vehicle systems, manual and automated conveyor systems, state-of-the-art picking systems and mixed traffic. And of course, an automation solution cannot succeed without its key component – intelligent software. To see how a complete automation solution might look like in practice, check out our case study on Magna Assamstadt.
Interested in autonomous mobile robots?
We’re happy to tell you more!
Further reading recommendations

Optimize intralogistics processes and increase performance using automation. What is the right degree of automation for your operation? In this post, we present various levels, from innovative manual warehouses up to fully automatic systems.

Flow meter manufacturer Digmesa automates production using an Open Shuttle. Learn more about the flexible solution in an interview with managing directors of the Digmesa Group.

Especially in times like these, supply plays a central role. Which trends and market developments are influencing the manufacturing industry? How can we respond to these challenges? The first part of this post on intelligent production supply will focus on these issues.
Additional Information
More information about the Open Shuttles from KNAPP: