Erich is 80 years old and a keen golfer. Ten years ago, he had knee-replacement surgery. Since then, he has been able to live his life free from pain. But how can we be sure that the right medical product gets to the right place at the right time? In areas where every single error has the potential to cause considerable suffering, quality is absolutely key. Our zero-defect solutions guarantee the utmost quality and error-free patient care.
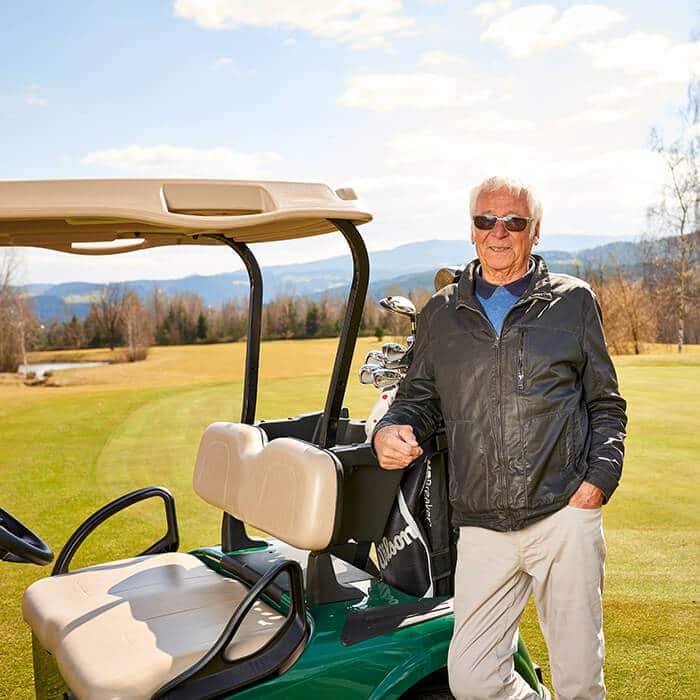
Logistics is key to error-free patient care
Optimal care of patients means that numerous processes behind the scenes have to run efficiently and without any errors. The end customer in a case like Erich’s is completely unaware of this. Only the results count – the necessary medications must be given in the correct dose or the right joint for the operation must be at the right place at the right time. For this to happen, both quality assurance and the logistics must be perfect. The German company implantcast is highly specialized in medical technology and focusses on the development, production, sterile packaging and sale of medical products, especially artificial joints. In addition to production, cleaning, packaging and sterilization, the entire flow of goods to 80 countries is coordinated from the headquarters in Buxtehude.
At implantcast, endoprostheses are shipped worldwide either to business partners or directly to clinics. One special element of this process is that often a doctor can only decide which endoprosthesis to use as late as during the operation itself. This means that a selection of endoprostheses must always be available in the operating theatre at the time of the operation. It’s crucial that the selection and quality are just right. But what happens afterwards to the parts that aren’t used? They are returned to implantcast, where they are sterilized once again and stored. Naturally, this involves a myriad of logistical processes.
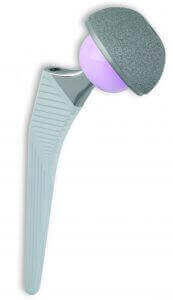
Zero errors and a good dose of flexibility
We produce medical products that are implanted in people. There is no possibility of sending out a recall as you would for a car to replace a faulty part. Every replacement of an endoprosthesis involves a great deal of pain. Not only does the patient have to undergo surgery again, they are also subject to the risks involved in another operation. This is an extremely sensitive area in which any error, any quality defect, can have a major impact on the company. Therefore, we absolutely have to work in an error-free way
The company’s strong growth meant that the existing warehouse no longer provided sufficient space. Person-to-goods picking had employees walking long distances that really added up and spending a considerable amount of time searching for goods. Stock management was manual and prone to errors. Checking the date of minimum durability was also difficult.
It was therefore very important to implantcast that the new solution fulfil the following requirements:
- Flexibility in terms of both size and performance
- Reduction of the error rate and thereby improvement in quality
- Ergonomic and easy-to-operate work stations
- Increased picking performance
The flexibility of KNAPP’s concept was what really convinced us. It’s a system that we can adapt to our company growth bit by bit. This meant that we didn’t have to invest in a large system in advance. Instead, we can extend the system and boost performance by adding shuttles and lift systems.
A new solution for implantcast
In the end, implantcast opted for a system solution with flexible, 3D-capable shuttles and integrated RFID technology. The solution includes ergonomic work stations from the Pick-it-Easy series that are equipped with integrated image processing technology developed by the KNAPP subsidiary, ivii. Find out more about the technologies from KNAPP!
What does this look like?
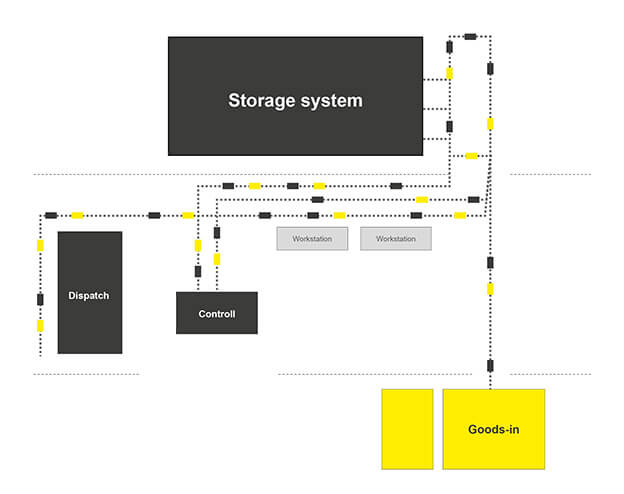
Goods-in and storage into the automatic small-parts warehouse
New endoprostheses are sterilized after production and automatically given RFID codes. The articles are allocated to a container via the codes, then conveyed to the small-parts warehouse for storage.
Unused endoprostheses that come back from an operation are checked for damage, re-sterilized and entered back into the system.
100 % check using innovative image processing technology
The Pick-it-Easy work stations are equipped with Pick-to-Light displays, RFID gates and image processing technology. If medical products such as instruments or prostheses are needed, the warehouse system automatically delivers the goods directly to the work station. On the package along with a barcode and an RFID code is a Data Matrix code that contains the date of minimum durability and other data.
Every work step is designed to ensure the highest level of quality:
1) The optimized image processing system recognizes and interprets the goods in the storage container in real time. On a monitor, the employee is shown which parts should be picked for the order.
2) A beamer also shines a cone of light on the exact article to pick. Moreover, the system ensures that the employees find and pick the article with the earliest date of minimum durability.
3) The articles are also scanned when they are picked.
As a result, the picked parts are checked in three ways. This provides a comprehensive check process that reduces the error rate to 0.
It’s just not possible to detect a defective RFID, barcode or QR code with the naked eye as we’re talking about a transmitter file. This system offers twice the security, which means that the wrong parts never leave the warehouse,
explains Jens Saß, Managing Director implantcast.
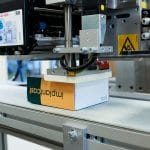
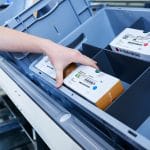
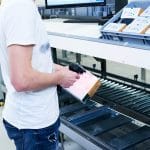
Additional checks in dispatch
At the dispatch work stations, employees check the orders again using the RFID tags, then pack them. Before being placed in the transport vehicle, the goods are run through an RFID gate. This check ensures that the shipment includes all the parts for the order.
Advantages at a glance
- Increased productivity
- Scalability and flexibility for the storage system
- Increased picking productivity
- Increased delivery quality
- 100 % quality assurance, zero defect
Are you curious and would you like to see the zero-defect solution at implantcast? Take a look at this video!
You are currently viewing a placeholder content from YouTube. To access the actual content, click the button below. Please note that doing so will share data with third-party providers.
More InformationFurther reading recommendations

The demands placed on production and logistics today are manifold. Combining an automatic storage system and autonomous mobile robots allows you to automate countless processes intelligently and flexibly.

Die Automobil-Branche ist im Wandel. Im nachfolgenden Beitrag lesen Sie wie man mit innovativen Arbeitsplätzlösungen die Qualität in der Produktion von Autos steigert.
Additional Information
Would you like to learn more about our zero-defect solutions? At KNAPP, we look forward to discussing ideas and requests with you to create new solutions. Write to us at blog@knapp.com.