Making smart production logistics a reality by using dynamic and interconnected systems
Global supply dependencies and increasing customization have a growing influence on production. What do manufacturing businesses need to operate efficiently in terms of costs and resources despite the resulting complexity in production? Dynamic, networked systems as well as locally organized warehouses are the solution. Smart production will always involve an intelligent and networked logistics solution. Discover more about how a networked production might look like and which processes are especially suitable for automation in the following article.
Translating requirements into solutions
At our manufacturing customers, we see four major criteria that must be fulfilled: First, an incredibly diverse range of items that must be handled efficiently. This is a central issue, especially for many luxury brands. Second, the efficient handling of many different load carriers is important. We often see this issue at automobile manufacturers. Handling and space-effective storage of many small load carriers is also important, for example, for electronics producers. The third important issue is the perfectly timed supply of production lines with all the necessary materials. In this context, exact sequencing and complex creation of routes for in-house transport are vital. The fourth criterion is achieving top quality in all steps of production and assembling. Our solutions provide intelligent, integrated and reliable production processes. This is how we optimize supply flow and availability, use storage capacities even better and reduce error costs
What might such solutions look like in detail? Here are 4 concrete examples from different sectors.
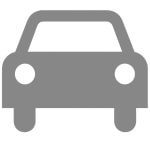
1. Automotive: Flexible and reliable assembly line supply
The right parts in the right quantity and sequence, all at the right time and place – that is what truly matters in flexible assembly line supply. Here is one possible solution:
- Space-effective storage with access to every item: The heart of the solution is our intelligent automated OSR Shuttle™ Evo storage system. The OSR Shuttle™ Evo is a multi-deep storage system capable of storing many different types of small load carriers. The parts are therefore stored space-effectively and can be retrieved at any time. The special design allows each load carrier to be accessed at any time.
- Planning the tugger train paths: The in-house orders for required parts are fulfilled in line with the production sequence of the individual products on the production line. The time required to move the components to the line must also be considered. The intelligent KiSoft software makes light of this difficult calculation. It calculates which small load carriers are required in which sequence and plans the allocation of the tugger train.
- Provision at tugger train station: The OSR Shuttle™ Evo then retrieves the small load carriers according to the calculated values and provides them in the exact sequence to the exit line at the tugger train station. The small load carriers are provided multiple-deep on separate levels according to the planned arrival time at the target location and the possible routes.
- Supply of the assembly line: To ensure a rapid and ergonomic unloading at the target locations along the assembly line, the small load carriers are automatically transferred to the tugger train in an exact, pre-defined sequence. Not only is the sequence of the target locations considered but also the side from which the handling unit must be removed. This guarantees that the manual unloading situation for the tugger train driver at the line is as ergonomic as possible.
The distinctive feature of this solution is the exact sequencing directly from the OSR Shuttle™ Evo storage system at maximum performance. Further advantages are: The reduction of buffer space, the increased efficiency of the routes and an increase in quality through correct supply because the only manual process is unloading.

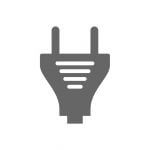
2. Autonomous transport solutions for the electronics sector
Our autonomous mobile robots – the Open Shuttles – carry out in-house transports from storage locations to assembly lines or work stations. They can automatically pick up and put down different types of small load carriers, entire roll containers or small portable racks. In doing so, they navigate freely through the production facility. Thanks to the Open Shuttles’ swarm intelligence, urgent and special orders can be distributed and processed immediately. What’s more, by adding more shuttles, it is possible to balance out peak times in production. All it takes is a special leasing model, as the integration of more shuttles is easy.
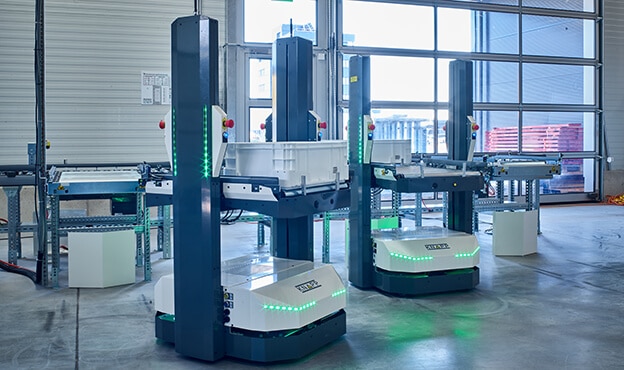
Production in the electronics sector is highly automated. So-called pick-and-place machines are used to place very small electronic parts onto printed circuit boards in a highly efficient and automated process. These parts are provided on tape reels that must be stored and provided to the pick-and-place machines just in time. Our autonomous mobile robots are ideally suited for the in-house transport of these tape reels as well as the completed PCBs. To meet the special requirements, we have equipped our Open Shuttles with a few add-ons.
- Tilt protection that secures the PCB magazines during transport
- Direct docking on the material tower: In the material tower, magazines are filled with tape reels in the set-up sequence which are then transferred to the Open Shuttles for direct transport to the pick-and-place machines.
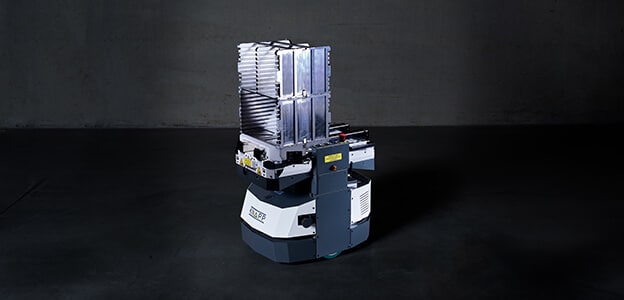
The link provides more information on the innovative Open Shuttles and their variants.
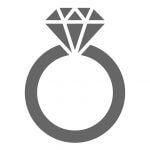
3. Solutions for storing very small parts
In jewellery making, for instance, systems are needed that can reliably handle very small products such as watches and their components. The handling units and small load carriers used often weigh very little and have varying dimensions. The sequenced supply of the required parts also plays an important role in jewellery production. Our intelligent INDU-Store offers the right warehouse technology for this purpose. The space-effective, automated storage system stores small and micro parts in various small load carriers. Single items, assemblies, semi-finished products or finished jewellery can all be stored or buffered in the system. Inside the INDU-Store, two robot grippers store and retrieve the items. For optimal production processes, several INDU-Stores can be filled with different products or parts and connected with each other. This can smooth out capacity peaks and ensure a continuous supply to the work stations. Open Shuttles can also transport the parts to the work stations automatically. This provides all the required parts while freeing up the employees to concentrate on their value-creating tasks.
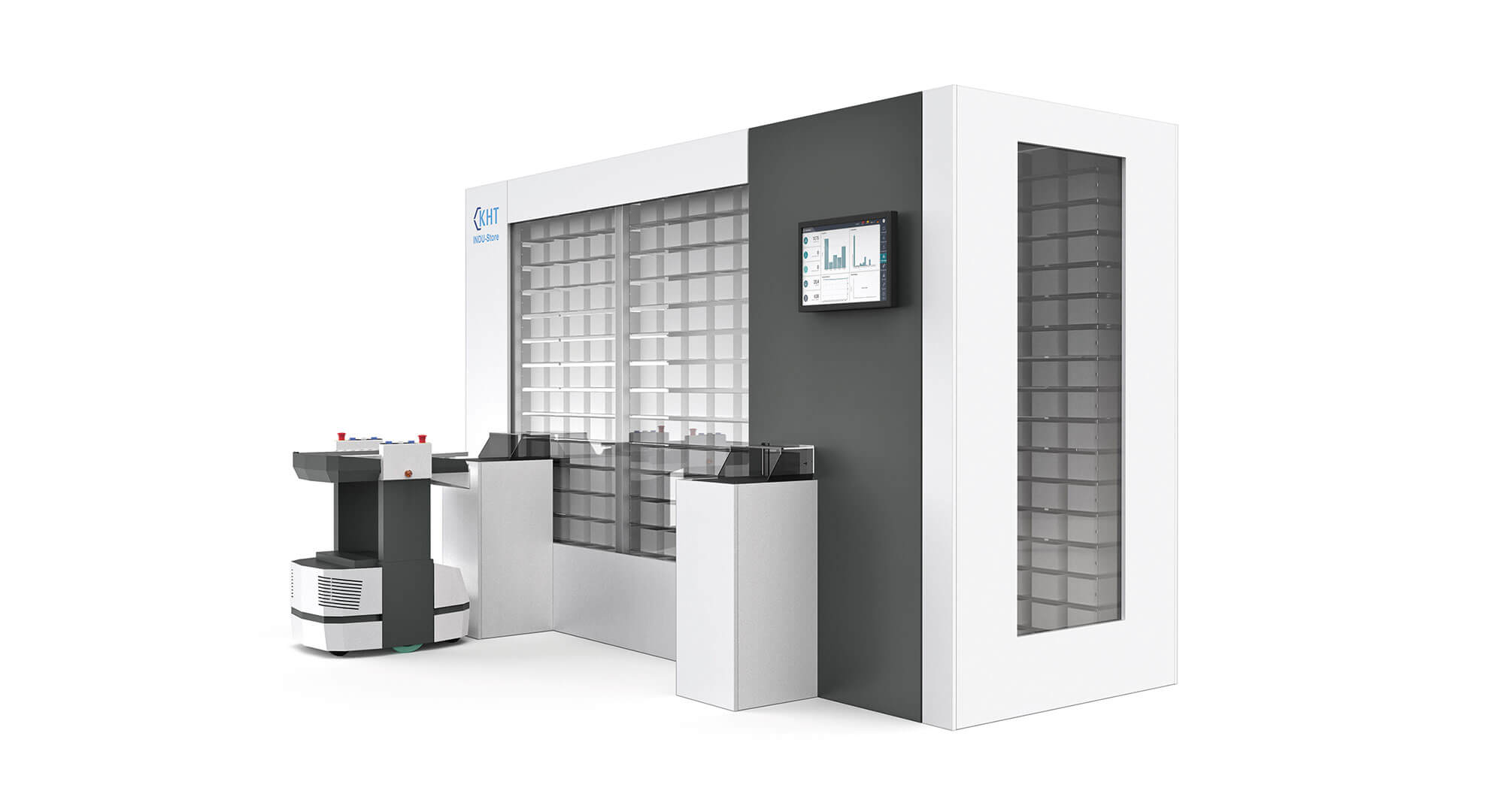
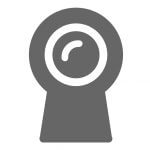
4. Zero defect solutions for assembling and picking
Errors in assembling and picking can have severe consequences and cause high costs. If, for example, a part is assembled with errors and then installed somewhere, the cost and effort involved to correct the error is high. Achieving a defined quality rating is very important, especially in the OEM field. We are using intelligent image processing technology to achieve maximum quality and efficiency in assembling and picking processes.
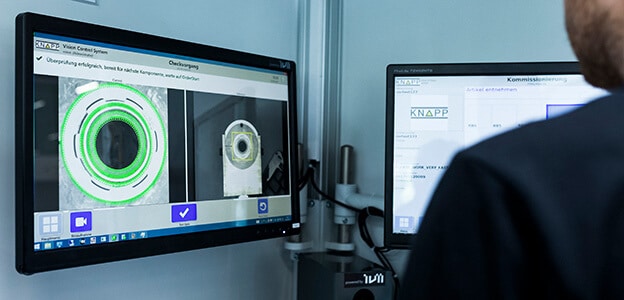
Thanks to this technology, every work step is automatically verified. If an error occurs, the system alerts the employee, who can then respond immediately. Direct feedback during the work process allows the employee to learn and improve. At the same time, new employees can be trained rapidly and work productively from the start.
In the field of medical technology in particular, picking errors can have serious consequences. Therefore, the German company implantcast uses intelligent technologies for picking their prostheses. Find out more in the following video.
Further reading recommendations

What does the smart factory of the future look like? Find out more about our vision for smart manufacturing!

Especially in times like these, supply plays a central role. Which trends and market developments are influencing the manufacturing industry? How can we respond to these challenges? The first part of this post on intelligent production supply will focus on these issues.
Additional Information
Take a look at our zero-defect solutions at Pankl.
Would you like to learn more about our solutions focussing on security of supply and industry solutions?
Click here to find out more about our technologies and references.
Wir bei KNAPP freuen uns darauf, mit Ihnen Ihre Ideen und Anforderungen zu diskutieren und neue Lösungen zu schaffen. Schreiben Sie uns auf blog@knapp.com.