In logistics, the last mile is the distance a package has to cover from leaving the warehouse to arriving at customers’ homes. This is just like the last stretch of a marathon. The last bit just before the finish line may be short, but it’s often the most challenging. Today, it’s important that the last mile is covered in a sustainable way and that the customer always knows where the delivery is. Customers expect an omnichannel shopping experience with a choice of delivery options, such as click and collect or home delivery at their preferred time.
These direct touch points make the last mile essential to customer satisfaction – getting it right is paramount. To overcome this daunting challenge, it takes innovative solutions and meticulous planning. In this blog post, we will spotlight this critical delivery stage and show how you can ensure that every package reaches its destination the way it should.
Content:
Five key facts on last-mile logistics
What is the last mile in logistics?
In logistics, the term “last mile” means the last step in the delivery chain – how goods travel from the DC or warehouse to where they are needed. This link in the value chain is often seen as highly critical, because it involves several steps and actors: pickup, transport and on-time delivery to the customer are handled by forwarders, couriers and retailers. Last-mile logistics can also involve services such as returns management or assembly as extra benefits for the customer.
The pandemic lockdowns have made online retail a must for all businesses, but especially for general retail. Many customers who got used to shopping online while self-isolating did not drop this new habit when restrictions were lifted. A mix of habit, convenience and cost-consciousness still drives demand for online retail today. This means getting last-mile logistics right is more important than ever to achieve perfect customer service.
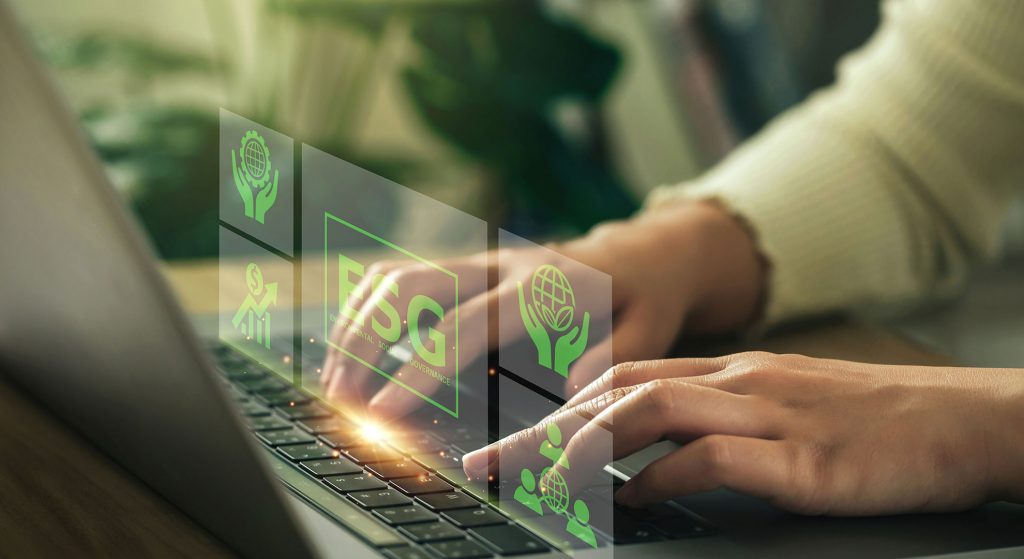
Challenges on the last mile
The challenges and problems on the last mile are pervasive and multi-faceted. Growing urban populations and increasing environmental awareness mean that transport vehicle capacity must be used as efficiently as possible. But even perfectly loaded vehicles can get stuck in heavy traffic, have problems with inferior infrastructure or tricky access to delivery locations. Despite all this, customers still expect prompt and reliable delivery. A perfect storm of challenges for companies, requiring new concepts for distribution. The key to meeting all these challenges is the optimization and evolution of warehouse resources.
How the last mile can be sustainable in urban environments
Optimizing the last mile is hugely important for tackling the climate crisis. This is especially difficult in urban environments – the challenge is to deliver a large volume of orders efficiently in an area that is already experiencing heavy traffic. Intelligent and dynamic solutions are necessary to pave the way for green logistics that minimizes carbon emissions.
Personnel shortage as a major stumbling block on the last mile
Conventional delivery solutions for the last mile are often costly, requiring special fleets or specially trained personnel. Even the first link in the value chain, the warehouses, sometimes struggle with a lack of staff. Innovative technology can pick up the slack here. In particular, logistics robots come in handy, filling in where personnel are in short supply, or allowing valuable qualified team members to make better use of their time.
Yet another challenge: people tend to order more frequently, but fewer things at a time. This leads to more packages overall, but particular at peak times such as before Christmas, for Black Friday and Cyber Monday, where all retailers have to ramp up their logistics performance at once to satisfy customer demand.
Potential warehouse logistics solutions for the last mile
How to address all the manifold challenges of the last mile efficiently?
As usual, there is no one-size-fits-all solution. Automation and various intelligent digital technologies offer helpful approaches to mastering the puzzle of the last mile. There are many such approaches: contactless in-store experiences at the point of sale, micro hubs and dynamic route planning. From order receipt to delivery to the customer, each phase of the value chain can be tweaked to optimize it.
Data analysis is the key to making the distribution network, order fulfillment and the last mile interact seamlessly
Thoroughly analyzing performance data can show where there is room for improvement and how delivery procedures can be optimized. This helps to lower cost and improve service quality. Using clever tools to optimize delivery routes is also a big step towards making the last mile more sustainable. Intelligent software, such as our KiSoft software suite, calculates the most efficient and most environmentally friendly route for delivery to the consumer. On the way, the delivery route is also recalculated flexibly to take current traffic conditions into account, further reducing carbon emissions.
Our KiSoft software considers different parameters for a consumer-oriented supply of the ordered goods. Using KiSoft customer orders can be planned and tracked in real time, all the way from the online store to the customer’s doorstep.
Innovative warehouse technology for more efficiency on the last mile
Delivery management platforms and tracking systems can help to rationalize procedures and lower costs for manual labor involved in delivery management. Functions for real-time tracking and automation can improve efficiency and minimize errors. Another important factor is the availability of goods in the warehouse and the ability to access the entire stock at any time. Automated warehouse solutions such as the Evo Shuttle make quick and precise picking possible, tailored to the particular requirements of the last mile.
Micro fulfillment center: using available space optimally and im-proving customer satisfaction
Smaller warehouses can play to their strengths in urban areas: They are closer to where the customers live, use fewer resources and significantly shorten delivery times. All this in turn improves customer satisfaction, making micro fulfillment centers close to cities an integral part of modern logistics networks. Our automated picking systems bridge online stores and brick and mortar stores. The solutions we offer are tailored perfectly to various industry requirements. Automated picking systems are a perfect tool for the point of sale, combining highest storage density on minimal space with absolute product security.
Conclusion:
The last mile presents many challenges to logistics companies, ranging from growing customer expectations to sustainability issues in urban areas. The solution to all these challenges is using innovative technology, automation solutions and data-based optimization to best effect. Micro fulfillment centers and flexible, customer-oriented approaches also help to improve delivery processes and boost customer satisfaction. Careful planning and continual adaptation are the key to success in the dynamic world of the last mile.
New Dimensions of Knowledge

In logistics, the last mile frequently includes many hurdles to jump that require significant resources. Perfect planning and flexibility can make the difference between success and falling flat. And environmental sustainability is becoming more important in the home stretch of the value chain, too. In our blog post, we share four strategies for more sustainability in food logistics.

What challenges are retailers currently facing in the value chain? And why is automation playing an increasing role? Read on to find out what our experts have to say about today’s retail technology trends in the following interview.

Together with our partners Leergut Logistik Services GmbH (LLS) and LOGIPACK, we developed a unique solution for empties management with a great economic benefit. Read on to discover what our fully automatic empties management system – single bottle sorting included – can do.
Further reading recommendations


The grocery industry is transforming its way into the future. Grocers using MFCs will be the ones getting it right first.

More grocery shoppers are preferring to fill their virtual carts online than in-store. To accommodate this demand, retailers have a couple of fulfillment options, both supported by a scalable automation solution.