Manufacturing is facing growing challenges: Greater efficiency, increased flexibility and optimal use of space are in high demand. Autonomous mobile robots (AMRs) offer an innovative solution for simplifying internal transport and automating rapidly. Discover more about AMRs, their possible applications and the advantages they bring.
Key Takeaways
Definition of an autonomous mobile robot (AMR)
Autonomous mobile robots are a type of driverless industrial truck. Without the need for human control, they navigate within a defined environment and respond in real time. An AMR robot uses a digital map of the warehouse, sensors, cameras, and artificial intelligence to independently identify and avoid obstacles.
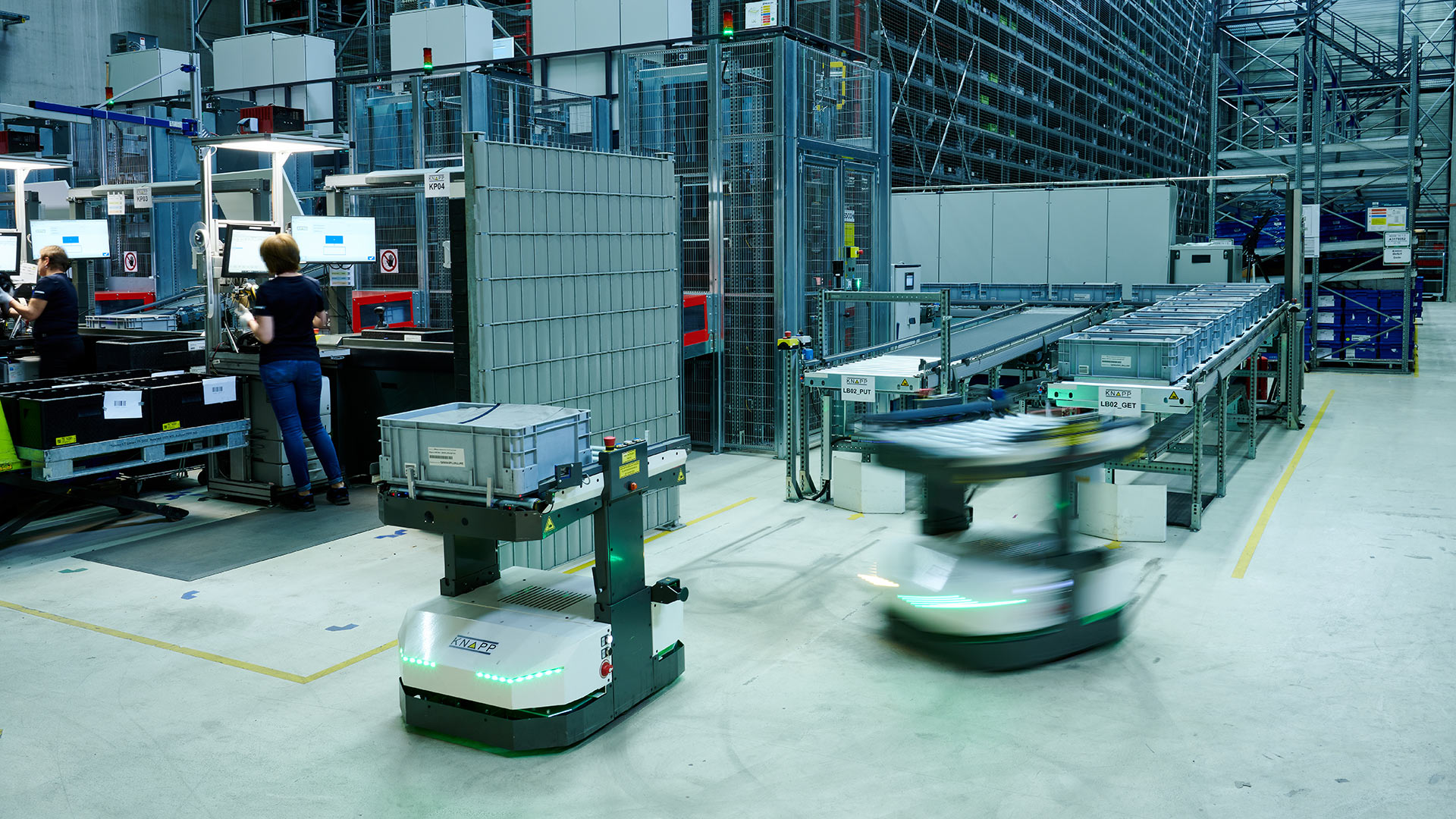
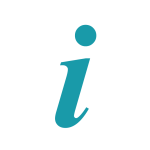
Find out how AMR robots differ from other automated guided vehicles (AGVs) in our blog, AMRs and AGVs: Two Automated Guided Vehicle Systems, Compared.
Autonomous mobile robots: Application and requirements
AMRs are established as indispensable helpers in many different sectors. They are widely used in the manufacturing, automobile and electronics industries as well as in the food, pharmacy, mail order and e-commerce sectors. In this blog, we concentrate on how autonomous mobile robots are used in manufacturing. Here, AMRs are involved in many types of transport work thanks to their innovative technology, advanced sensor systems and intelligent software.
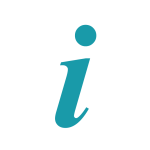
On the road to smart factories, AMRs are indispensable. A smart factory uses automation solutions such as AMRs and automated storage systems to optimize the production processes. Read more about it in our blog Smart Manufacturing: The Future of Production.
Before deciding to use an AMR in your production or storage facility, the following criteria should be considered:
Criterion | AMR well-suited | AMR less well-suited |
Environment | Dynamic work environment and variable workload | Static or very simple environment with permanent transport paths |
Tasks | Routine tasks and tasks prone to error | Highly complex, unique tasks |
Transport requirements |
Many transport tasks and safety requirements | Few transport requirements, easily handled by a person or using other technologies |
Flexibility | Flexibility is needed for future changes and permanent conveyors should be avoided | No flexibility needed, conveyors as a permanent element |
Infrastructure | Structured building with sufficiently wide paths and an available IT infrastructure | Complex grounds with unstructured spaces, outdoor transport, insufficient Wi-Fi in the halls |
Throughput | Medium to low throughput, long distances | High throughput in small spaces |
In summary, the use of autonomous mobile robots must always be adapted to the respective operational requirements and environmental conditions. AMRs offer significant benefits in a dynamic work environment with repetitive and physically demanding tasks. In a warehouse with highly complex tasks and high throughput, however, they are not the best solution.
Top 5 advantages of autonomous mobile robots
But what makes AMRs so unique and attractive for companies, regardless of their size? Here are the advantages of AMRs summed up:
The great advantage is that, compared to traditional industrial robots and static conveyors, our AMRs can be adapted to changing processes quickly. They optimize the workflow, reduce costs and improve work safety.
Types of autonomous mobile robots at KNAPP
The future of automating production processes is promising thanks to autonomous mobile robots. At KNAPP, the name we’ve given our AMRs is the Open Shuttle. Our broad product portfolio allows us to offer customized solutions for a wide variety of requirements.
Our broad AMR portfolio includes:
Autonomous mobile robots for transporting containers
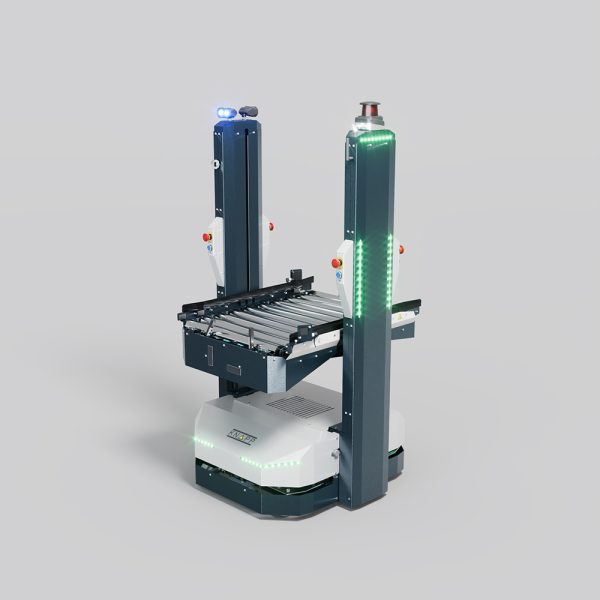
Do you want to transport goods or raw materials in containers, cartons or on trays? Depending on type, our AMRs can transport one or two containers with a total payload of up to 120 kg (265 lb).
Autonomous mobile robots for transporting pallets
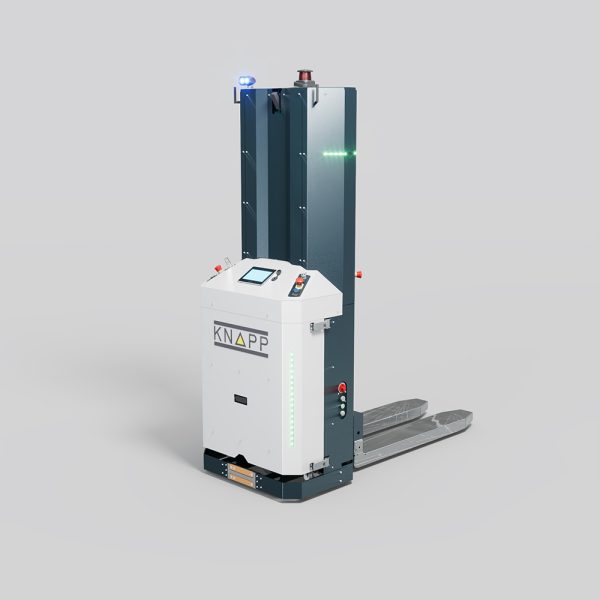
Would you like to transport pallets, frames, racks or special load carriers efficiently and automatically? The Open Shuttle Fork is at your service, carrying loads up to 1,300 kg (2,866 lb).
Autonomous mobile robots for transporting magazines and trays
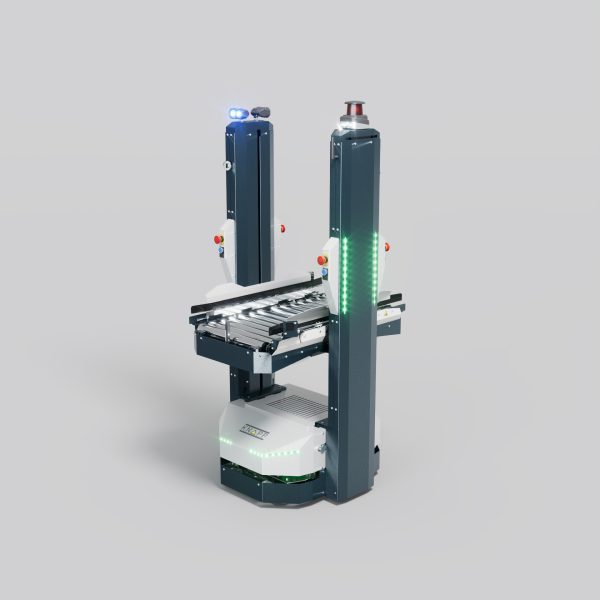
Are you in electronics and looking for an autonomous mobile robot? Our Open Shuttles transport magazines and trays weighing up to 50 kg (110 lb).
Special features of the KNAPP AMRs
The Open Shuttle by KNAPP boasts a range of standard features and add-ons that are tailored to the requirements of the manufacturing, food retail and distribution logistics sectors.
1 I Integrated lifter for different drop-off and pickup heights
Our autonomous mobile robots can be equipped with a lifter that allows them to pick up and drop off loads at different heights. Open Shuttles manage 550 mm to 1,500 mm (21.65 to 59.06 in) or 0 to 1,200 mm (0 to 47.24 in) and act as a direct link to automated storage systems, such as our Evo Shuttle.
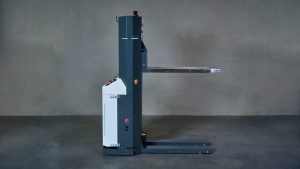
2 I Comprehensive safety systems for highest standards
AMRs feature state-of-the-art sensor technology and safety systems. The Open Shuttles in particular feature a blue light that indicates the shuttle’s direction of travel, 3D obstacle detection for identifying objects in its path and a top scanner for dynamic production environments.
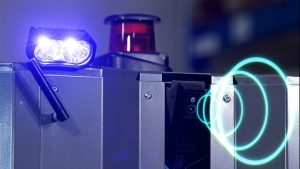
3 I Magazine transport including width adjustment and load stabilizer
For transporting circuit board magazines in electronics manufacturing, our AMRs include a special load stabilizer that secures the magazines during transport.
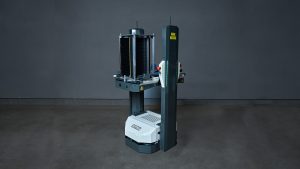
Over the past years, we have successfully automated and optimized our customers’ transport processes within their warehouses in over 150 AMR projects. The Open Shuttles excel thanks to rapid startup and easy configuration, and having applications in all types of sectors.
Controlling autonomous mobile robots with software and AI
The performance of an AMR depends directly on the software that controls it. Modern AMRs use AI and machine learning to analyze their environment and make decisions in real time. These technologies allow the robots to adapt to new situations without requiring manual reprogramming. The most important software elements are:
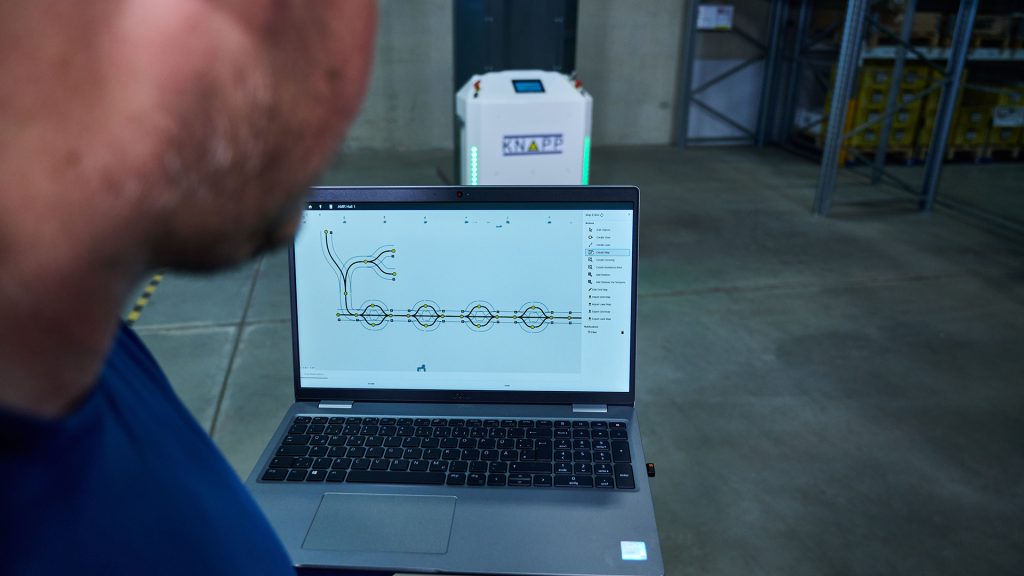
We chose the KNAPP AMRs because their system allows us a very high level of autonomy. The new automation system sets us up for making changes at our location independently, as well as being able to expand our production cells. This makes our overall operation faster and more cost-efficient than it would be with other systems.
Reality check: AMRs in practice
Would you like to find out how AMRs are being used by real companies? Take a quick look at the following solutions:
Fronius: Smart pallet transport by AMRs
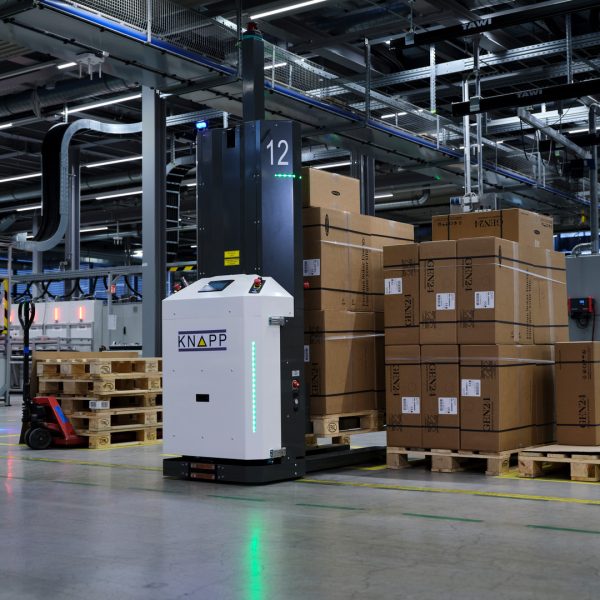
The innovative Open Shuttle Fork has automated production supply and internal transport at Fronius. The new solution gives the company the necessary autonomy to flexibly make changes as needed and to manage both manual and automatic transport orders in the same system.
PC Electric: Internal processes optimized with AMRs
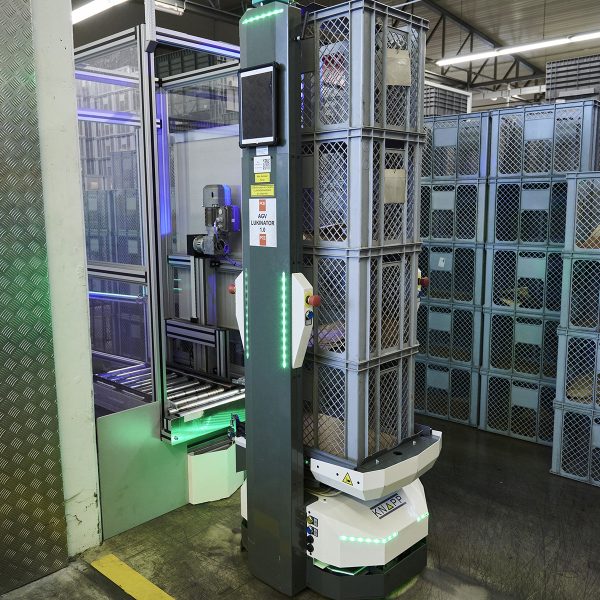
Aiming to optimize the transport of empty containers, PC Electric opted for our autonomous mobile robots, the Open Shuttles. The new automation solution simplifies processes, makes work more ergonomic and frees up resources for value-adding activities.
Digmesa: AMRs supply production just in time
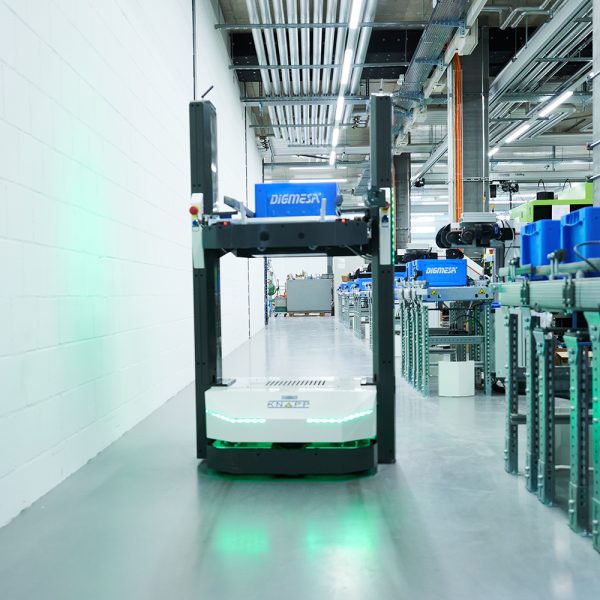
At Digmesa, we implemented an Open Shuttle solution in just four months. Our AMRs supply the production machines with empty containers efficiently and return finished parts on the way back.
Frequently asked questions
What is an autonomous mobile robot (AMR)?
Autonomous mobile robots are driverless transporters that are able to navigate within a defined work environment independently and without human intervention.
What is the difference between an AMR and an AGV
Automated guided vehicles follow specified, pre-set routines and processes, while autonomous mobile robots process information from their environment and autonomously make decisions. This blog post provides more information on the topic of AMRs and AGVs: Two Automated Guided Vehicle Systems, Compared.
How much does an AMR cost?
The base price for an Open Shuttle starts at about 45,000 euros and will vary depending on the type and the equipment needed. There are also expenses associated with integration which depend on the project.
How much space is needed to integrate AMRs?
The space required for AMRs depends on the size of the fleet and the required throughput. The KNAPP AMRs are some of the most space-effective on the market. For more information, get in touch with us at: kin.sales@knapp.com
Further reading recommendations

What does the smart factory of the future look like? Find out more about our vision for smart manufacturing!


Automated Guided Vehicle Forklift for Pallets
With the Open Shuttle Fork, our portfolio now includes an autonomous mobile robot for pallet transport. Find out more in our interviews with the product manager and development manager.