Numbers allow us to measure success, growth and potential. But they can do even more. They can tell stories. Come along with us today on a tour through our company, headquartered in Hart bei Graz, Austria, and get to know our company culture.
19,800 visitors per year at the headquarters
Barbara Liebmann works at the KNAPP reception desk and welcomes countless visitors. She is often the first person who our visitors meet. Her job involves registering visitors, opening the barrier for trucks delivering goods, forwarding phone calls and sometimes simply lending a colleague an umbrella. “It’s always busy but that’s exactly why I like my job. I love the variety in my job and that I get to meet different people from all corners of the world. What’s really important to me is that each visitor feels comfortable here and travels back home with a positive impression of KNAPP,” explains Barbara.
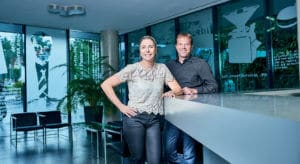
Markus Rock is waiting at the reception desk as well. He works as a project manager and assists customers from the installation phase to the acceptance of an automation project. Today, however, Markus is on a different mission. He also enjoys working as a tour guide, taking curious visitors on a tour through our company as part of the “Erlebniswelt Wirtschaft” project, and answers questions such as “What does KNAPP actually do?” and “What’s logistics?”. Markus explains, “I have been working for KNAPP for many years, which is why I can tell the visitors fun little anecdotes and give them an insight into the incredibly dynamic world of logistics.” He goes on to say, “My number one priority is to convey the KNAPP spirit to visitors. Every one of us contributes so much each day and we can achieve this because we stick together as a team and can rely on each other.”
The founding year 1952
1952 is a significant number for us. That’s when Günter Knapp founded his business as a sole trader in the basement workshop of his house, employing just two people. Günter Knapp was a visionary and inventor – his motto being “anything is possible”. His mission was to overcome the challenges of his time with innovative developments and to improve people’s lives. He developed a special oil burner, for instance, which could atomize the thick Austrian heating oil more efficiently than conventional oil burners. Another major invention of his was the automatic doughnut-filling machine for a bakery which was designed to fill several doughnuts with jam simultaneously.
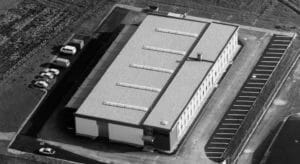
One of the most significant innovations by Günter Knapp was the autopicker he designed for the pharmaceutical wholesale. He came up with the idea as early as in the late 1950s when he realized that both the population and prosperity in general were on the rise and the fast supply of medicines was becoming increasingly important. 1988 was the beginning of the success story for the so-called central belt autopicker with which orders could be fulfilled in next to no time. Equipped with intelligent camera systems and special software, this classic is still a vital tool in automation today in order to meet current demands such as the zero-error strategy or Track & Trace.
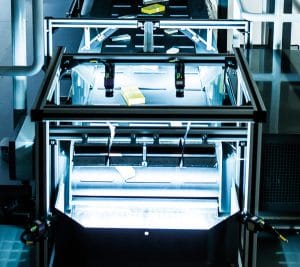
4,500 employees worldwide
Company founder Günter Knapp would be astonished at what has become of his small business – an international technology company with over 4,500 employees worldwide, 2,900 of which working in Austria alone. What has never changed over the years is our drive and passion for developing new solutions for the demands in production and logistics.
Marc Pendl is one of our 4,500 employees working as a design engineer in Design Engineer Construction. He was involved in the mechanical development of our latest automated storage system, the OSR Shuttle™ Evo, starting from the initial idea through to the serial production of the system. Marc even designed the eye-catching LED strip, which gives the shuttles a cutting-edge look. “Our goal was to get our corporate design to come alive in the product. Bringing together both construction and design was a challenge. As a design engineer, you want to create as much space as possible for the installation of the components. This usually results in a rather boxy or chunky design. Form generally follows function but the designer in me was still unsatisfied with this shape. That’s why I searched for ways to create a design with as much volume as possible in an appealing shape. As for the LED strip on the shuttles, my goal was again to find a balance between the functionality of the status display and design,” Marc explains.
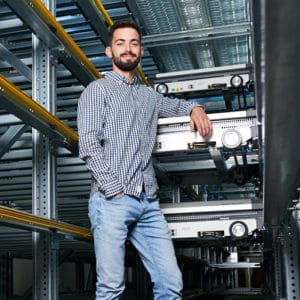
Blink of an eye
That’s about how long our logistics software KiSoft needs to calculate the perfect location for an article in the warehouse, for instance, in the central storage system, the OSR Shuttle™ Evo, or in a KNAPP-Store. This may sound simple but if you have several hundred thousand locations available, this is actually a major mathematical problem to solve. Fortunately, the software takes over this task, and many more. “We can no longer imagine a life without software, it’s everywhere: in our smartphones, cars and even in our refrigerators. Software helps us to organize and simplify our lives. The same applies to a logistics system. The system is responsible for smooth, trouble-free operation in the warehouse. In addition, our analysis software is able to filter all the relevant information from the enormous volume of data that exists in the warehouse. This information is used to optimize warehouse operation, plan resources in advance and for predictive maintenance. That’s why we put great emphasis on discussing software processes with our customers as early as during the initial phases of a project. We know that software is the key to success for a logistics business,” explains Mario Rauch, Software Consultant and specialist for digitalization at KNAPP.
Sounds exciting, doesn’t it? KNAPP is the largest IT employer in Styria and host of the annual KNAPP Coding Contest where programmers can show off their skills.
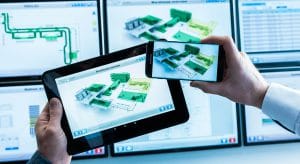
106,667 kilowatt hours
This is how much electricity our own photovoltaic plant, which is installed on the roof of one of our production halls, produces from solar energy. The amount of electricity it provides is equivalent to the annual electricity consumption of 65 family homes. “Installing a photovoltaic system was the next logical step towards sustainability. For several years now we have been pursuing the idea of being completely self-sufficient when it comes to our energy supply. The photovoltaic system was especially designed to cover the majority of the base load at the Hart bei Graz site. In conjunction with our KNAPP goes green mobility initiative, in future, all the charging stations for our electric vehicles can be supplied with solar energy as well,” enthused Christian Grabner, Chief Financial Officer.
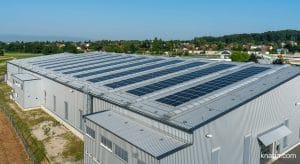
“KNAPP goes green” mobility initiative
In total, there are 28 charging stations for electric cars available on site. As part of the “KNAPP goes green” mobility initiative, KNAPP provides their employees with an electric car free of charge if they are a carpool of least 3 people. Electric cars are also available for employees who have to run errands. One colleague, Murat Yalcin, who works in Facility Management, often uses the electric car for running errands, “I really like the idea of KNAPP goes green. I have a young daughter and I want to leave behind a clean and healthy environment for her to live in.” Another way to commute to work in an environmentally-friendly manner is to use public transport. Our site in Hart bei Graz can be easily reached by bus or train. KNAPP provides employees who use public transport with an annual ticket to travel to the company. “That’s really a great opportunity. Being able to get to work with public transport is convenient and it protects the environment,” enthuses Lydia Kulmer, in-house Translator at KNAPP.
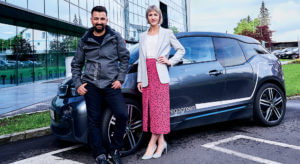
At your service 24/7
When our workday comes to an end in Austria, our colleagues on the other side of the globe are just getting started. That’s the case in Atlanta, for example, where our North American headquarters is located. The KNAPP group has a total of 43 sites all around the world. This is important as it ensures that our customers always have competent contacts in their vicinity. Our multi-language Hotline service is also available around the clock. It’s based on the follow-the-sun-principle, which means that 170 employees work on 4 different continents in 3 different time zones. Customers can reach a contact through a personal telephone number who speaks their language. One of these so-called First Level Agents is Viola Apreutesei-Riebl who communicates with customers in German, English, Italian, Russian and Spanish. “I enjoy working in the Hotline. Every day I talk with colleagues and customers from all over the world and can apply both my knowledge as well as learn something new. The best moments are, of course, when I can quickly and efficiently help the customer solve a problem,” explains Viola.
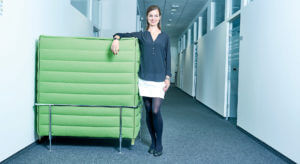
As you can see, every number tells a story. Every story involves people who do their best every day to make our vision of making complexity simple a reality.
Further reading recommendations

New technologies are changing the workplace of people in logistics and production. Smart workers is what we call this new generation of workers. In the following blogpost, a smart worker takes us on a trip through tomorrow’s world of work.

Invisible. Essential. Underestimated. Software. Software – it’s invisible, essential and yet all too often completely underestimated. Though we are mostly unaware of it, software accompanies…