Modern storage and retrieval systems make optimal use of warehousing space, improve stock management and boost productivity. Companies can deploy technologies such as automated warehouse robots and intelligent software to optimize their warehouse processes and stay competitive. Currently, two such technologies are dominating the market: shuttle systems and autonomous mobile robots. But which solution is the right one for your warehouse?
Intralogistics automation - a tale of two technologies
In this blog post, we look at how both technologies work and at their specific strengths and use cases. We then showcase how these KNAPP solutions come into play, empowering you to make the right decision for your business.
What are shuttles?
Shuttles are intelligent warehouse robots that are used in automated storage and retrieval systems (AS/RS). Gliding along fixed tracks, they move rapidly up and down the storage aisles as well as between aisles to efficiently store and retrieve containers. Shuttle systems are primarily used where high performance is needed to deliver high throughput. They achieve this by working in parallel on multiple levels and connecting with the rest of the warehouse through a powerful lift system, maximizing throughput and overall performance.
How they work
A classic shuttle system consists of shuttles within the racks and lifts at the front of the racks. Each individual shuttle works only on one level. Shuttles in each aisle and level put away and retrieve items using a load-handling device. Since each shuttle is assigned to a specific level and a specific aisle or aisles, shuttle systems are generally used for high-throughput applications. They directly handle containers, trays and cartons stored up to quadruple-deep in the system.
You are currently viewing a placeholder content from YouTube. To access the actual content, click the button below. Please note that doing so will share data with third-party providers.
More InformationThe latest innovations and developments in shuttle technology
Shuttle systems have changed a lot since their introduction. Today, shuttles can change aisles, allowing them to access and retrieve all items on a rack level to create a perfect sequence for other processes. The pre-zone is eliminated, which makes building a more space-effective storage system possible.
To offset the rising cost of land, rack systems are now commonly built up to 30 meters (98 ft) high to use existing space as efficiently as possible. High-performance lift systems deliver throughputs of over 1,000 double cycles per hour, per rack line system. Thanks to intelligent construction methods, shuttle systems can be used in many different applications. For example, they can handle the Arctic temperatures required in freezer warehouses with ease. Furthermore, the number of storage locations can be scaled by installing additional rack line systems.
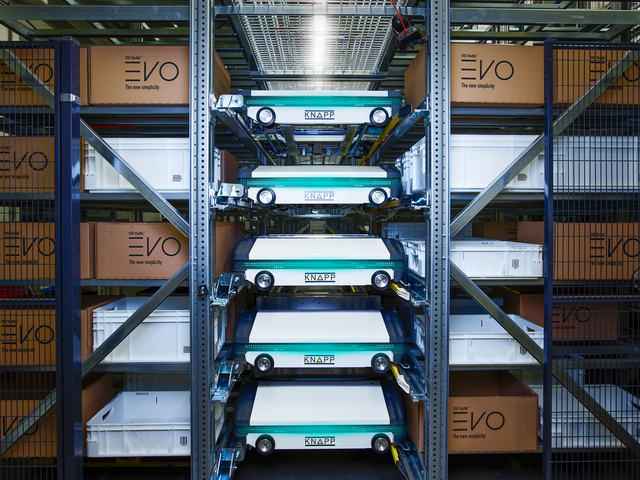
What are bots?
While shuttles can move only on fixed tracks, the more flexible bots are fully autonomous, a feature gaining ground in the market. They move freely through the warehouse and are extremely agile thanks to their slender construction, which also contributes to their flexibility, scalability and ability to fit well into different warehouse layouts. There are two different approaches with this technology. The first is cube storage systems, where load carriers are directly put away or retrieved from the rack either from above or below. The second approach uses bots that climb racks and store and retrieve from there.
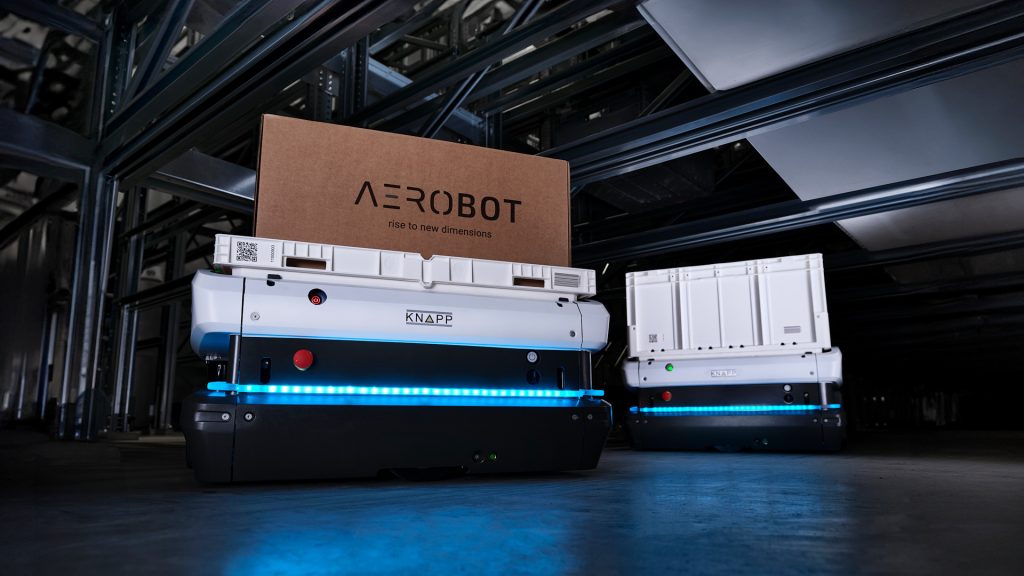
How they work
Bots’ high flexibility and agility make them unique. They navigate the storage system fully automatically, whether they’re moving autonomously on the floor or up and down the rack – or a combination of both.
Since they’re not limited to moving on a track, bots have a major advantage: they can adapt to new warehouse layouts and are easy to scale. New bots can be simply added to the system without changing any existing infrastructure, making the technology particularly relevant for dynamic warehouse environments where seasonal fluctuations and changes to the product range play a role.
The latest innovations and developments in bot technology
Current bots use high-tech algorithms to analyze and react to their environment. Advances in lidar and camera technology allow the bots to precisely “see” their environment and avoid obstacles. These innovations enable bots to make decisions in real time and carry out their tasks with maximum precision.
You are currently viewing a placeholder content from YouTube. To access the actual content, click the button below. Please note that doing so will share data with third-party providers.
More InformationShuttles or bots – a head-to-head comparison
When comparing shuttles and bots, there are plenty of different aspects to consider:
Integration:
How easy is it to integrate these technologies into existing systems?
Whether shuttles or bots,
KNAPP is your one-stop supplier
KNAPP is one of the pioneers of shuttle technology and their Evo Shuttle is still the gold standard in the field. The AeroBot system represents a new addition to KNAPP’s portfolio of storage solutions. The new bot-based technology ensures that KNAPP can offer the right solution for each use case and for each customer.
But which solution is right for you?
To help you make the right choice, here’s an overview comparing the design parameters of the two technologies, along with a detailed introduction to each solution:
AeroBot |
Evo Shuttle |
|
Max. construction height | Up to 12 m (39 ft) | Up to 30 m (98 ft) |
Length, width | Freely scalable
Racks can be arranged flexibly |
Freely scalable |
Number of storage robots | Freely scalable | One per level (for Evo Shuttle 1D, one per rack line system)
For Evo Shuttle 2D, flexibly scalable by level |
Load carriers | Containers, trays | Containers, trays, cartons |
Temperature range | +4 °C to +40 °C
(+39 °F to +104 °F) |
-28 °C bis +40 °C
(-18 °F to +104 °F) |
Max. load unit weight | Up to 35 kg (77 lb) | Up to 50 kg (110 lb) |
Evo Shuttle 1D: High-performance order fulfillment
The Evo Shuttle 1D is designed as a high-performance system for applications in, for example, online retail, e-commerce or in the pharmaceutical sector. One shuttle runs on each level in a rack line, storing and retrieving goods solely from these storage locations. This approach keeps fulfillment times at their fastest and maximizes throughput in the warehouse. A high-performance loop supplies items to the connected work stations and processes, making the Evo Shuttle 1D ideal for warehouses with a high throughput and a high inventory turnover rate.
Both the throughput capacity and the robust design are advantages you get with the Evo Shuttle 1D. When combined with a super-charged lift system capable of more than 1,000 double cycles per hour per rack line system, the Evo Shuttle 1D represents high-performance storage and retrieval at its best.
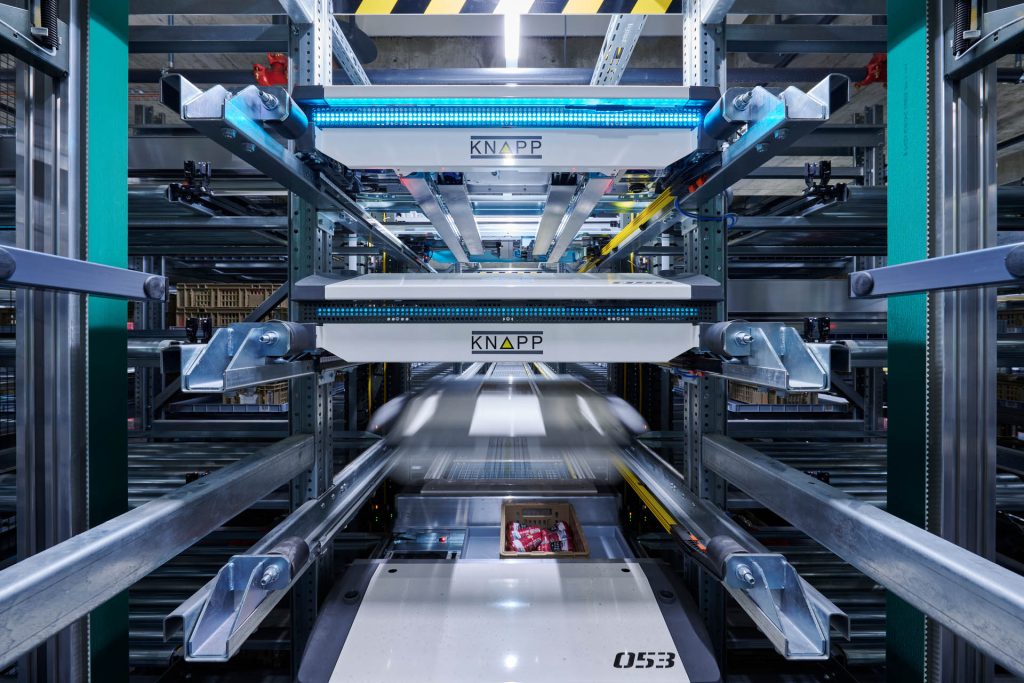
Evo Shuttle 2D: Perfect sequences every time
When it comes to extra flexible warehouse processes, the Evo Shuttle 2D is your best bet. The shuttles in the system can switch rack line systems, allowing them to reach every high-performance lift in the overall system. This allows perfect sequences to come out of the system directly – no pre-zone needed – for trim construction and optimal use of space. Furthermore, the system can be expanded flexibly since the number of storage locations can be scaled separate from performance. Need higher throughput? Add more shuttles. Need more storage capacity? Add more rack lines.
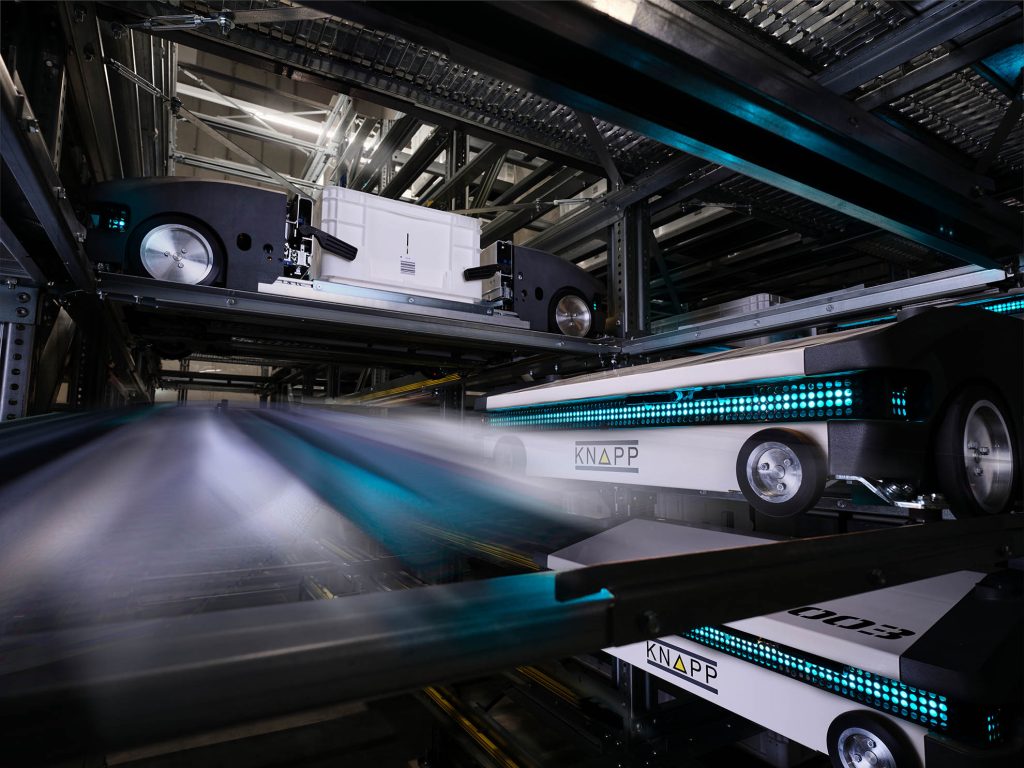
AeroBot: A new dimension of flexibility
For the AeroBot system, the name of the game is simplicity and flexibility. The most recent development in the history of automated storage and retrieval systems by KNAPP is a perfect addition to the technology portfolio. The autonomous mobile robots move about freely on the floor and then vertically climb the rack system. Load carriers are moved in and out of storage on the SatBot, a satellite robot that hitches a ride atop the AeroBot.
The AeroBot system is ideal for more than just rapid automation. Thanks to its scalable design, it continues to support you as your company grows. The flexible storage system is ideal as a combined storage and picking solution for e-commerce, micro fulfillment and omnichannel fulfillment in various sectors and is also ideally equipped for applications in manufacturing and industry. Its advantages include maximum storage density and optimal use of space as well as high redundancy and system reliability – all with the greatest degree of flexibility.
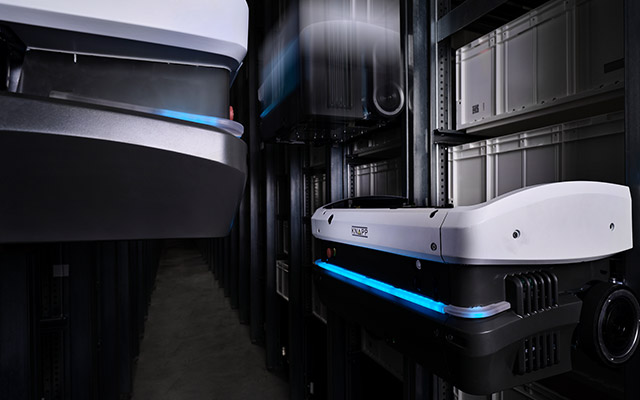
The takeaway
Whether a shuttle system or autonomous bots are right for you depends on your own individual requirements. In general, shuttles are well suited to companies with high throughput who are looking to invest in speed and efficiency. They offer maximum performance with the trade-off that implementation time is a bit longer. Bots, on the other hand, are ideal for companies with changing storage requirements who need flexibility, simple scalability and quick implementation.
That’s all to say: Regardless of the solution you choose, it has to fulfill your requirements and provide optimal support for your processes.
For both systems, taking the overall solution into account is key. The combination of goods-to-person work stations, robotics, intelligent software, pocket sorters and integrated applications such as buffering and sequencing will help determine which storage and retrieval solution is right for you. At KNAPP, we are a one-stop provider of complete solutions. We help you find the optimal automation solution for your business. Get in touch with us to receive your personal consultation!
New Dimensions of Knowledge



Today’s logistical challenges require innovative solutions. Find out now how you can shape the future of your logistics with the help of robotics and AI.
Further reading recommendations

What are 11 questions should you absolutely ask yourself before carrying out an SAP® EWM implementation project? Read on and find out in this blog post.


Machine learning is everywhere. But what exactly lies behind this future technology? Is it really possible to teach machines to learn? What advantages does it offer– and where does KNAPP come into play? Let’s take a closer look.