What if you could know today that a component will need to be replaced in two weeks? Our maintenance management tool does and automatically schedules maintenance and servicing tasks based on knowledge that goes beyond the manufacturer’s recommendation using data from built-in sensors and seamlessly integrated software solutions. Intelligent digital tools make this possible, and in combination with our holistic smart service concept, provide real value in servicing your systems. This year, see for yourself how our KNAPP Digital Services interact at LogiMAT from March 11–13 in Stuttgart.
Content
What are indirect maintenance costs?
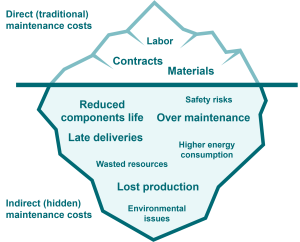
There is no way around it: Regular maintenance is key to ensuring the availability and long service life of your logistics system. Costs directly associated with this such as for labor and spare parts are easy to account for, but what about other costs that are often ignored but can also have a significant impact on your operating results? These are the hidden costs in maintenance. They can amount to up to five times more than direct maintenance expenditures.
These cost categories include, for example:
- Standstill costs, because your system is stopped for a short time during maintenance.
- Time that your employees spend idling during these standstills.
When the system stops, they can’t do their work, which can delay deliveries to your customers. - When components are only replaced in line with the manufacturer’s directions instead of according to their actual condition, higher costs can result for spare parts, not to mention a greater environmental impact.
A proactive maintenance strategy reduce these indirect maintenance costs.
Smart service is the solution
With an intelligent maintenance strategy, it is important to evaluate the components according to their actual condition and to get this information into a digital maintenance management tool that deals with spare parts management. Thanks to this type of information, components are only replaced when their condition requires it.
With KNAPP Condition Monitoring, for example, data is collected from the operational system and saved in the KNAPP cloud, allowing the condition of the system components to be evaluated. When a replacement is needed, KiSoft CMMS, our maintenance management tool, automatically creates a task for a team of Resident Engineers or service technicians. The most convenient maintenance window is also determined based on the data and taking the current and future capacity utilization of your system into consideration.
Condition Monitoring does not follow static maintenance schedules but follows the actual condition of the components. Components are only replaced when really necessary, which is what we mean by smart spare parts management and use. By the way, even systems that are a little longer in the tooth can be retrofitted with our smart service products.
This type of intelligent approach can be seen in the following maintenance schedules: For standard maintenance with planned preventative maintenance intervals (PPM), the actions are carried out more often and cyclically, which results in higher labor costs and increased spare parts usage.
By comparison, intelligent maintenance is data-based and evaluates the current condition of a component. If anomalies are detected, the maintenance management tool generates a check task. In summary, a proactive maintenance strategy promotes not only the evaluation of the current component condition, but also directly connects to a digital maintenance management tool with an integrated spare parts management tool. Technicians are then responsible for carrying out the tasks on site.
Our intelligent maintenance strategy at KNAPP Customer Service includes three areas:
Overview of our Smart Maintenance Approach
What follows is a summary of the type of data collected for our Smart Service approach and how you benefit from it:
Condition monitoring
- Optional condition monitoring using sensors
- Warning messages for wear
- Calculation of component service life
- Reduction in downtimes, low maintenance
- Evaluation of the actual service life of components
- Avoidance of unnecessary replacement work
Anomaly tracking
- Detailed depiction on the component level
- Statistical depiction of anomalies and anomaly message timelines
- Tracking of increasing error rates
- Worldwide comparison of components
- Repair effectiveness tracking
Process stability
- Performance level per component
- Transparent system efficiency
- Visualization of component performance drop
- Raising the maximum throughput
- Minimizing the spread of errors
- Monitoring of maintenance effectiveness
LogiMAT 2025 in Stuttgart: Our smart services on site!
As a service partner, we are no stranger to innovation and it is our goal to provide new digital services for the entire life cycle of your system, integrating them in our holistic smart services. See for yourself how these digital service solutions interact in an ongoing operation. Our experienced colleagues will demonstrate various use cases for you on site at LogiMAT 2025. Furthermore, we will be introducing you to the following service products:
- Smart Resident Services for condition-based maintenance of your system by a qualified team on site
- IT services for more stability and to protect your system as well as
- Retrofit concepts to renew the life cycle of your products
What’s more, you can see our broad product range for yourself, including a live demonstration and the many software tools in our mission control center, at our fair exhibit.
New Dimensions of Knowledge

Love a technical challenge? Are you an open and communicative person? Then check out this interview with our colleague Seldin: He tells us all about his job as a Service Delivery Manager.

Your SAP® EWM has gone live. What’s next? What 6 questions should you ask yourself about SAP® EWM support after your system goes live? Read on and find out in this blog post.

Exciting, varied and challenging – the job of a software developer in KNAPP Customer Service is never dull. We sat down for an interview with our colleague Andreas Kraßnig. In this interview, Andreas tells us what his job entails and why he is so passionate about what he does.
Further reading recommendations


Love a technical challenge? Are you an open and communicative person? Then check out this interview with our colleague Seldin: He tells us all about his job as a Service Delivery Manager.

Exciting, varied and challenging – the job of a software developer in KNAPP Customer Service is never dull. We sat down for an interview with our colleague Andreas Kraßnig. In this interview, Andreas tells us what his job entails and why he is so passionate about what he does.