Automated Omnichannel Logistics Solution for DSV
As a third-party logistics provider, DSV’s role is to organize supply chain solutions for companies across the globe. In 2021, DSV began operating an automated omnichannel logistics solution for a famous sporting goods manufacturer. The solution focuses on next-day delivery and the highest quality in order processing, and handles a tremendous volume of orders for wholesale, stores and e-commerce every day. On average, 10,000 orders comprising about 100,000 items are shipped across Europe from the warehouse each day.
You are currently viewing a placeholder content from YouTube. To access the actual content, click the button below. Please note that doing so will share data with third-party providers.
More InformationDSV and KNAPP understood each other brilliantly from the beginning. The two companies complement each other very well with respect to their values and corporate cultures.
Remco Innemee
Vice President, Division Lead, Consumer DSV Solutions, the Netherlands
Would you like to discover more about an automated omnichannel logistics solution?
Our experts are happy to advise.
The results of the automated omnichannel fulfillment solution
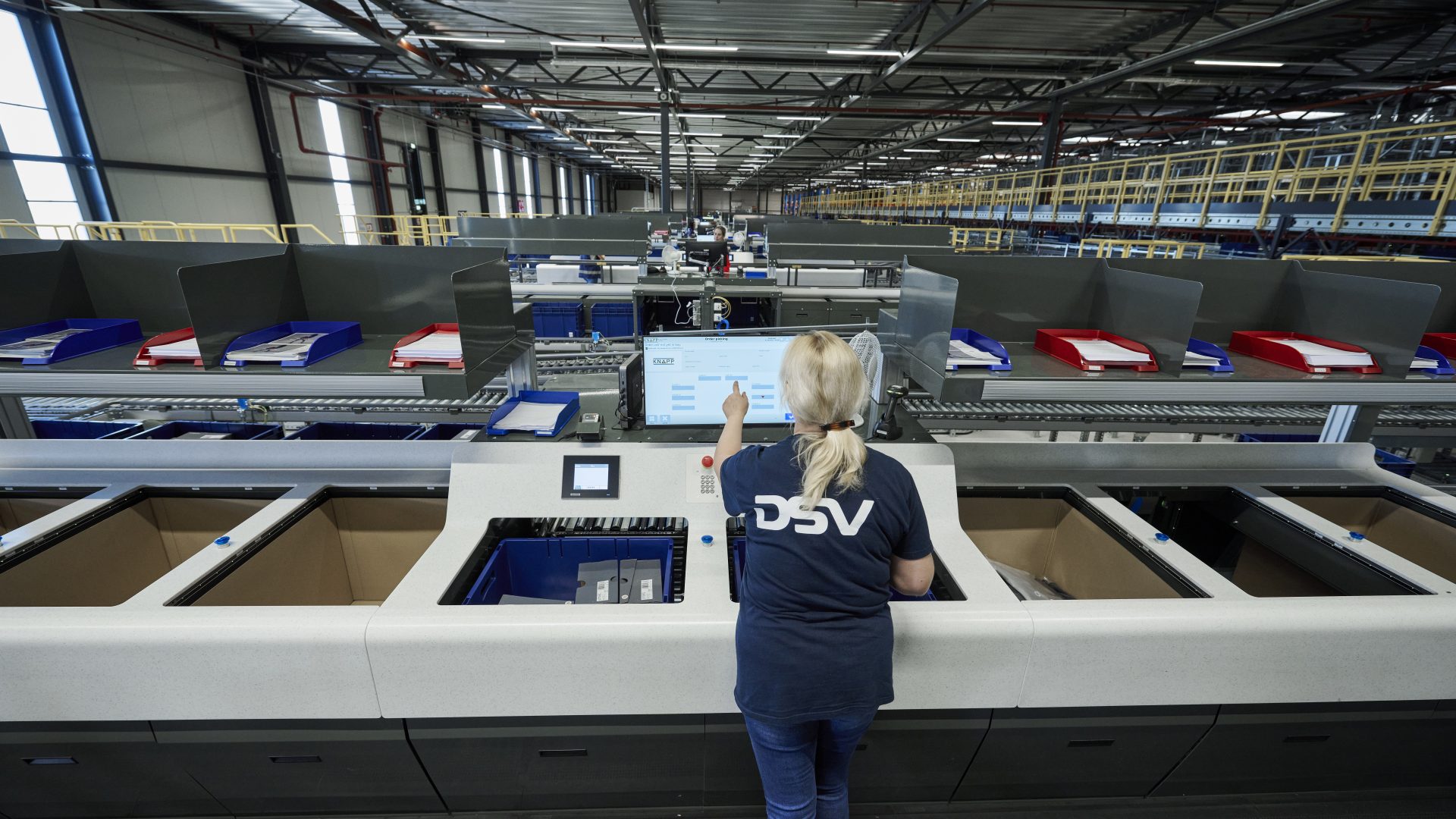
People are really happy when their shipments arrive on the next day. It really brightens their day.
Remco Innemee
Vice President, Division Lead, Consumer DSV Solutions, the Netherlands
Goods-in
Goods enter the warehouse on pallets and are repacked into containers or reused cartons at the 16 decanting stations. Some of the goods go on pallets to the high-bay pallet racks.
Storage
The small parts warehouse, the Evo Shuttle, has space for a total of 257,070 containers. These are stored triple deep on the 19 levels of the 31 modules until it’s time for shipping. The 361 shuttles allow 4,752 double cycles per hour in the automated storage system and convey the items to the picking stations when they are needed.
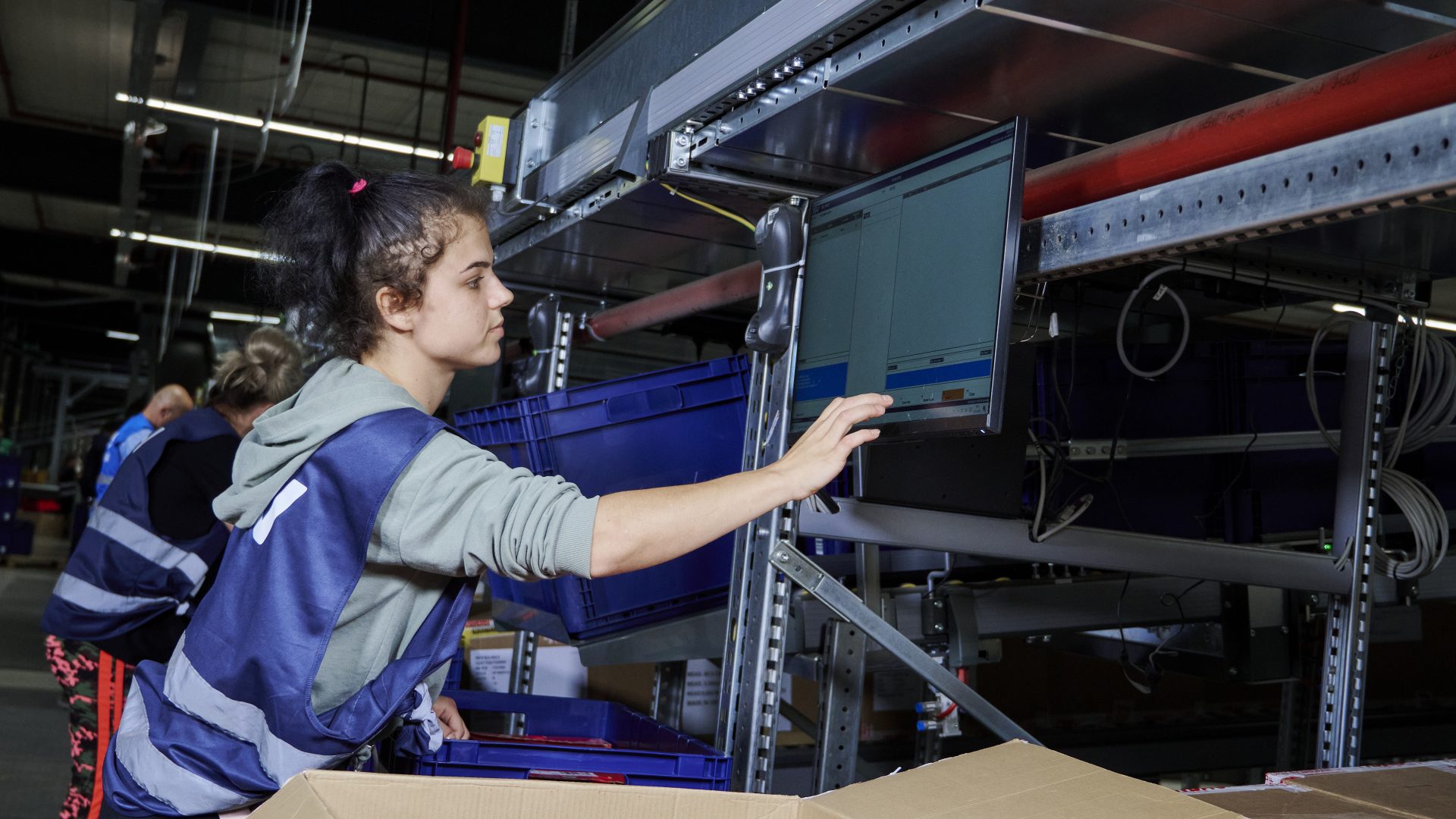
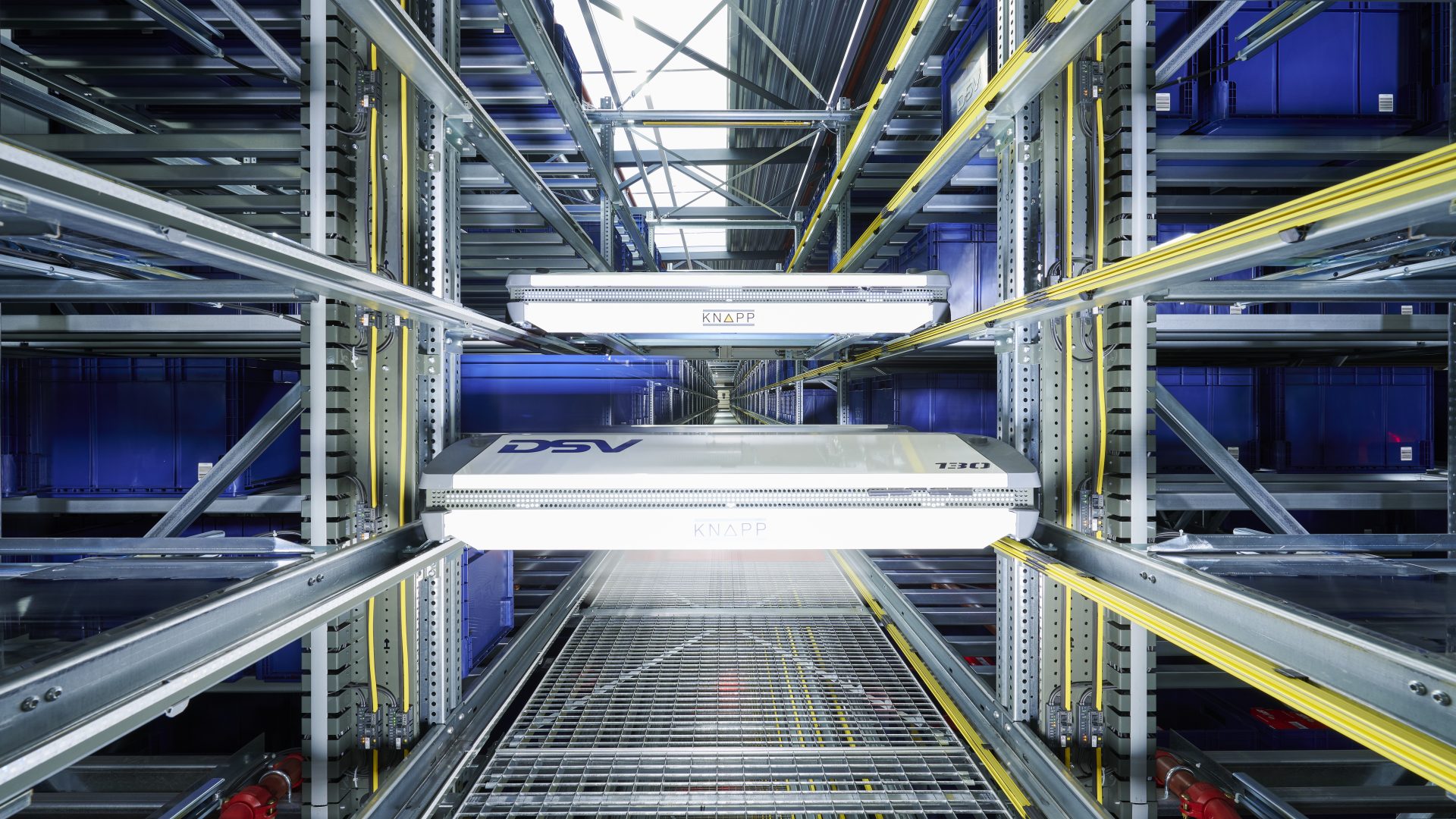
Picking
At the central distribution center, picking takes place at the goods-to-person work stations of the Pick-it-Easy Evo series, where the orders are assembled directly in the shipping cartons. In parallel there are 28 more manual work stations, where value-added services are handled.
Shipping
Cartons from the Pick-it-Easy work stations are closed to optimize volume, then are labeled and conveyed with the manually packed cartons to the 14 shipping ramps.
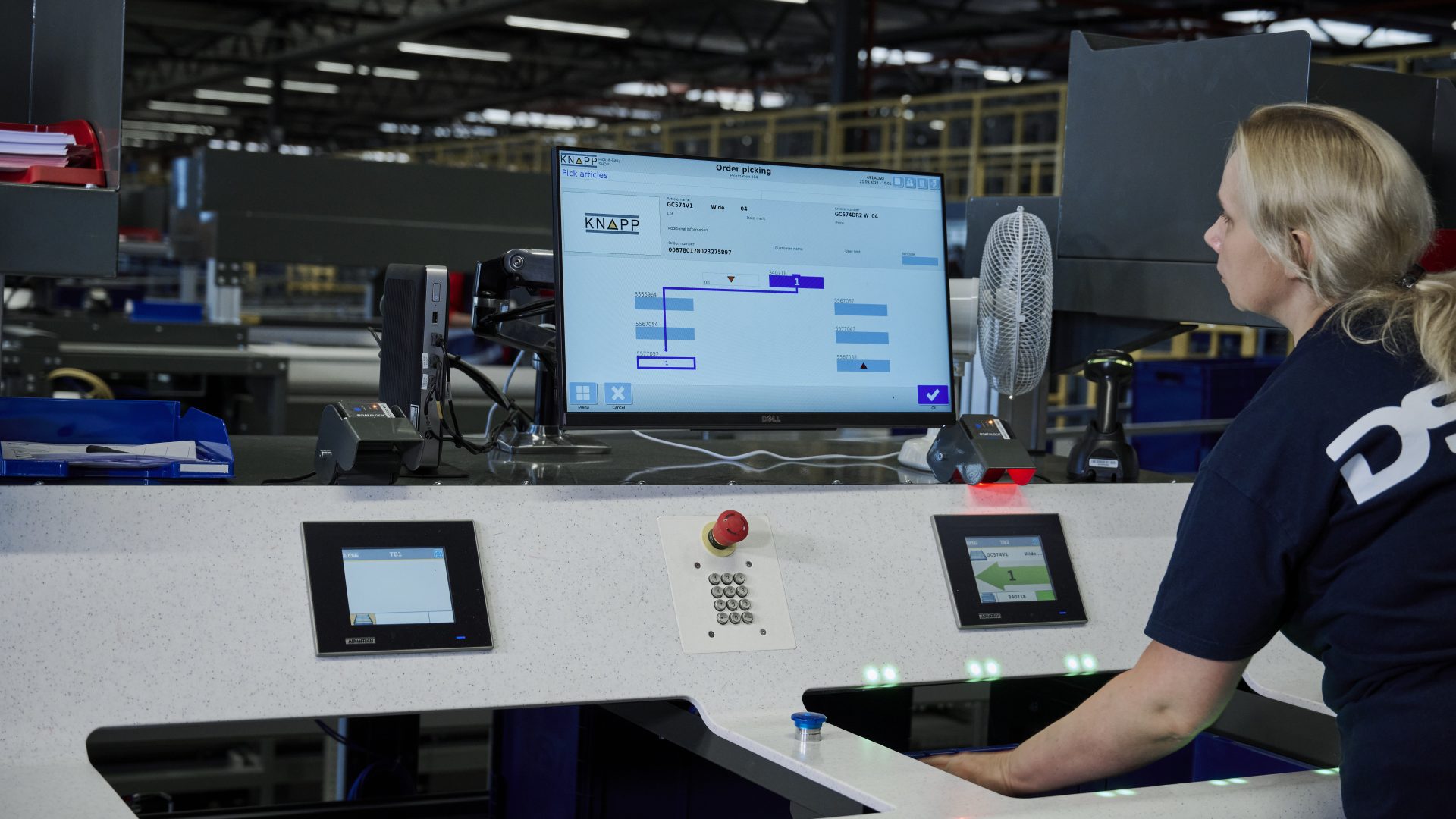
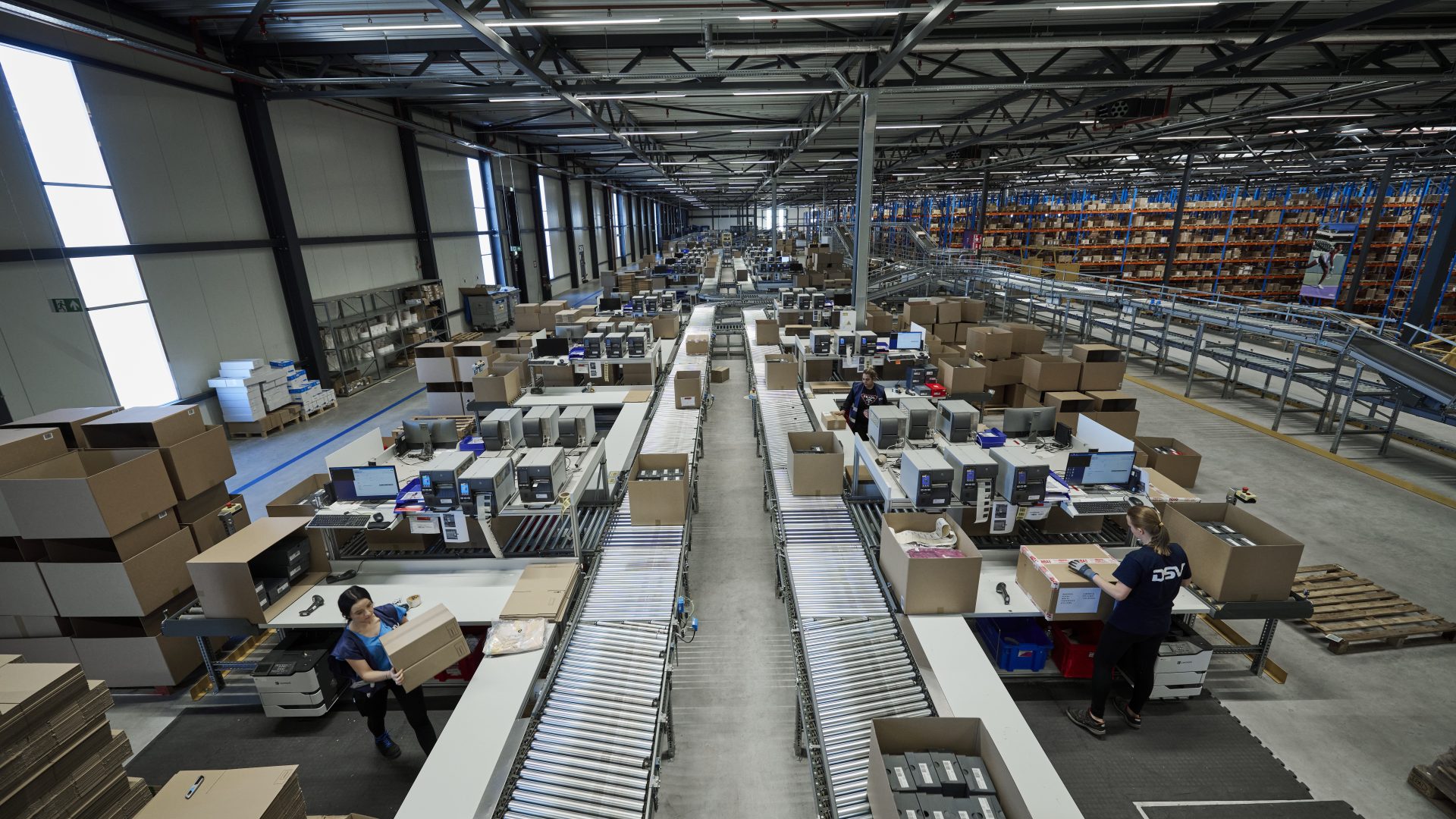
storage locations
active SKUs
order lines per hour
shuttles
Smarter service for optimal system operation
KiSoft CMMS software provides additional digital support for the important topic of maintenance. This means that maintenance decisions are data-driven and can be planned intelligently.
DSV has also opted for Resident Engineering service at their central distribution center and enjoys the support of experts on site. This outsources technical system operation risk, while the company benefits from many services such as incident management, spare parts management, reporting and even the introduction of system optimizations.
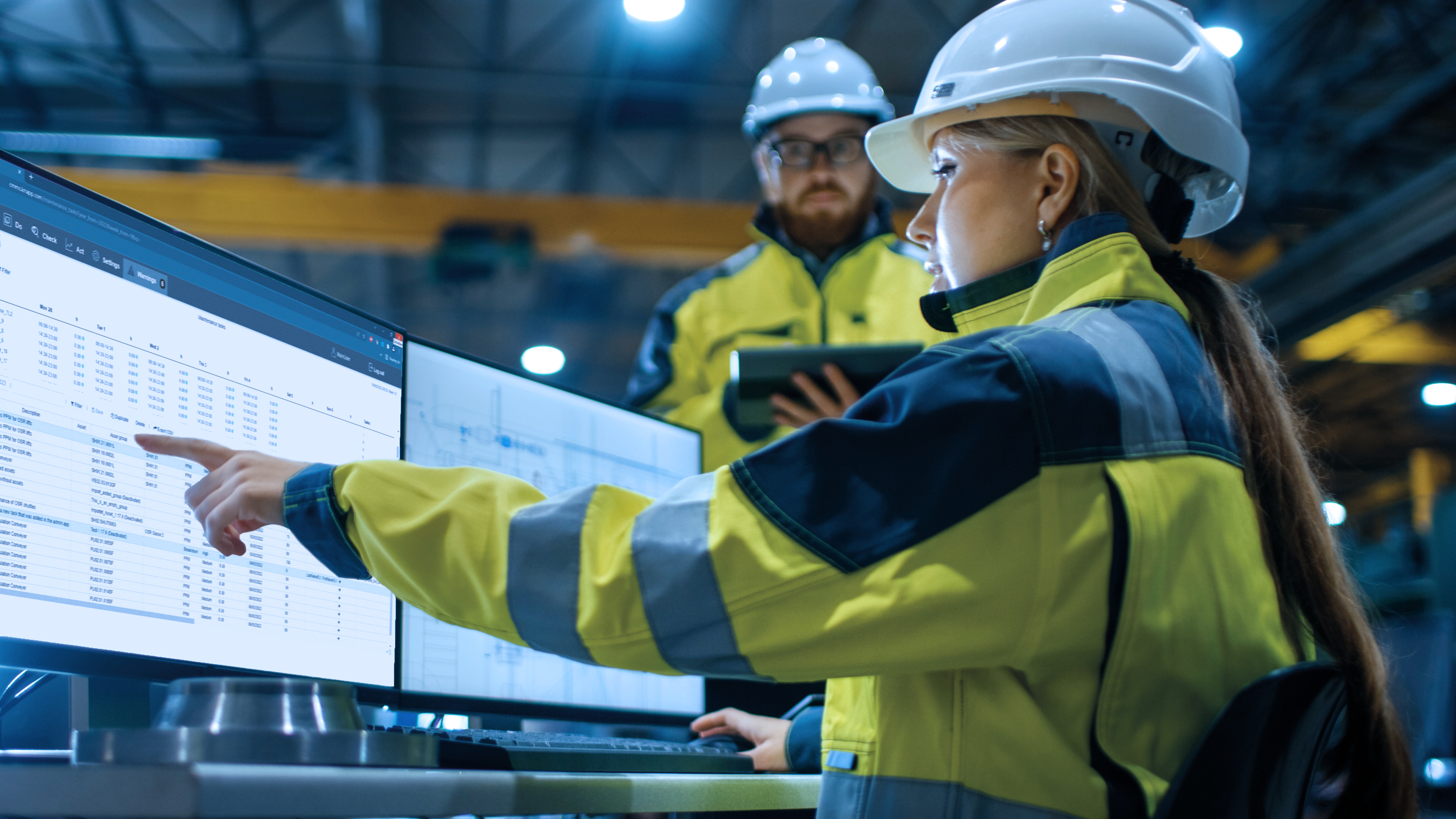