Brodrene Dahl: Sustainability and growth with intelligent warehouse automation
By automating their distribution center LOGSTAR in Randers, Brødrene Dahl not only increased their productivity and efficiency but also the level of quality throughout the entire fulfillment process. Thanks to the new automated warehouse strategy, the company was able to respond to the increased consumer demand and expand their product range by over 10,000 products over a period of ten years.
At the heart of the automation solution is an Evo Shuttle system including 136 shuttles, which is complemented by Pick-it-Easy work stations as well as picking and palletizing robots and many other system components, making warehouse management highly efficient and reliable. Another highlight of the solution is the implementation of reusable plastic containers in an effort to reduce company’s carbon footprint. Employees also benefit from ergonomic work stations, more safety and are relieved of strenuous tasks, such as carrying heavy loads.
You are currently viewing a placeholder content from YouTube. To access the actual content, click the button below. Please note that doing so will share data with third-party providers.
More InformationLogistics is the backbone of our entire business and the most important part of our services.
Lasse Halliday
Logistics Director, Brødrene Dahl
Would you like to boost the efficiency of your value chain?
Our experts are happy to help!
Bye-bye, manual workflows!
The warehouse in Randers is the size of a soccer field, but instead of a ball being kicked around, vast amounts of goods enter and leave the warehouse every day. An average of 1,700 deliveries including 12,000 to 24,000 products are delivered to customers within a 12-hour window on a daily basis. The introduction of the sustainable Blue Tote Project means that goods are now delivered in reusable plastic containers, which has helped reduce carbon emissions by more than 250 t so far.
Since 2023, a Pick-it-Easy Robot has raised the degree of automation, providing fast, accurate and reliable picking.
Storage
Incoming goods are repacked into storage containers at a total of 8 decanting stations. These storage containers are then automatically stored in the Evo Shuttle system. When the warehouse receives a purchase order, a small or large carton or plastic container is prepared depending on the order volume. After the load carriers have been labeled, they are ready for picking.
Picking
For picking, the cartons and containers are transported to one of the 5 manual stations or to the Pick-it-Easy Robot. Pick-to-Light technology makes manual picking easier. Orders can also be picked by the robot in advance and completed manually afterwards. The load units are then sent back to the Evo Shuttle for intermediate storage before delivery.
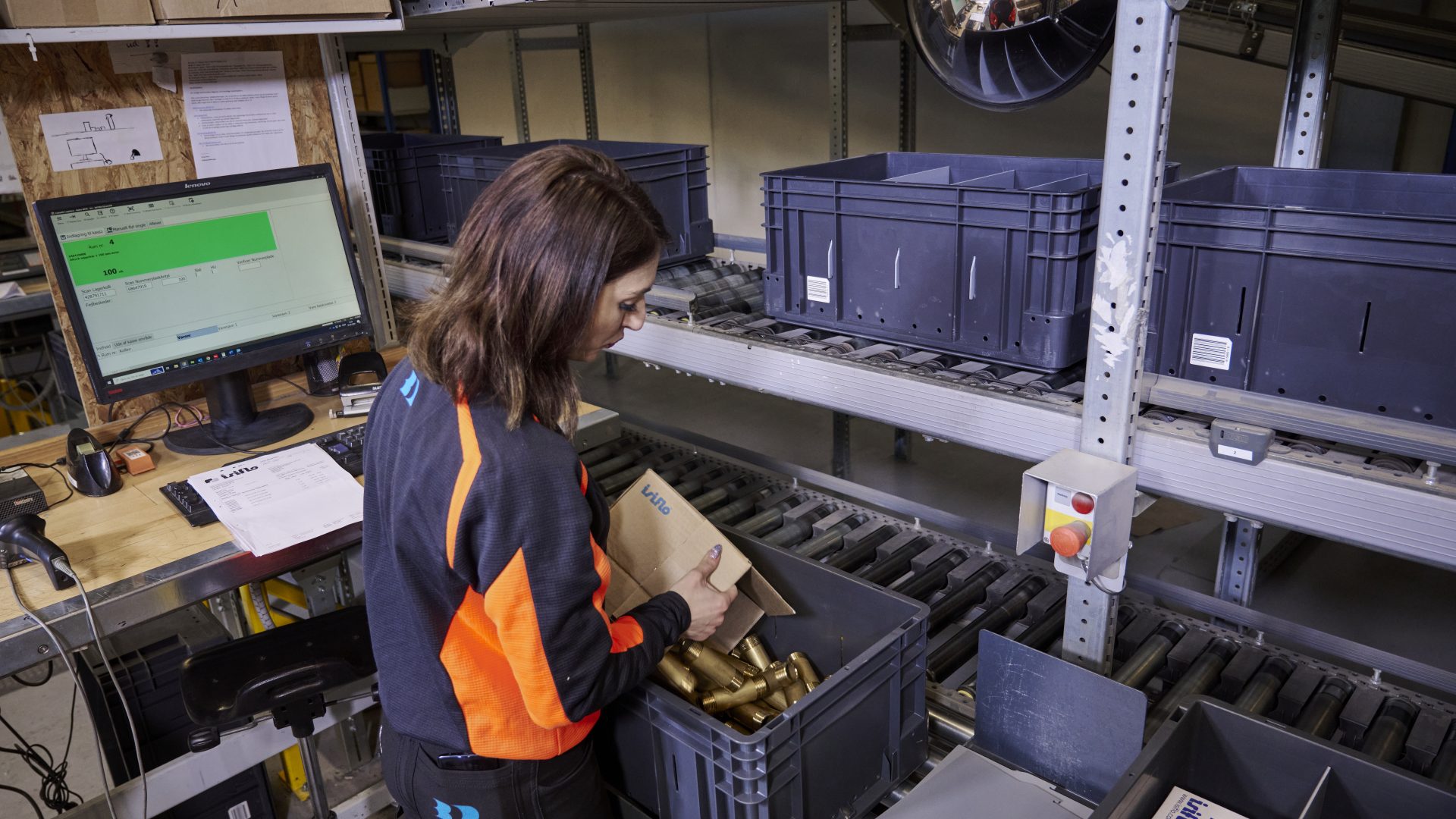
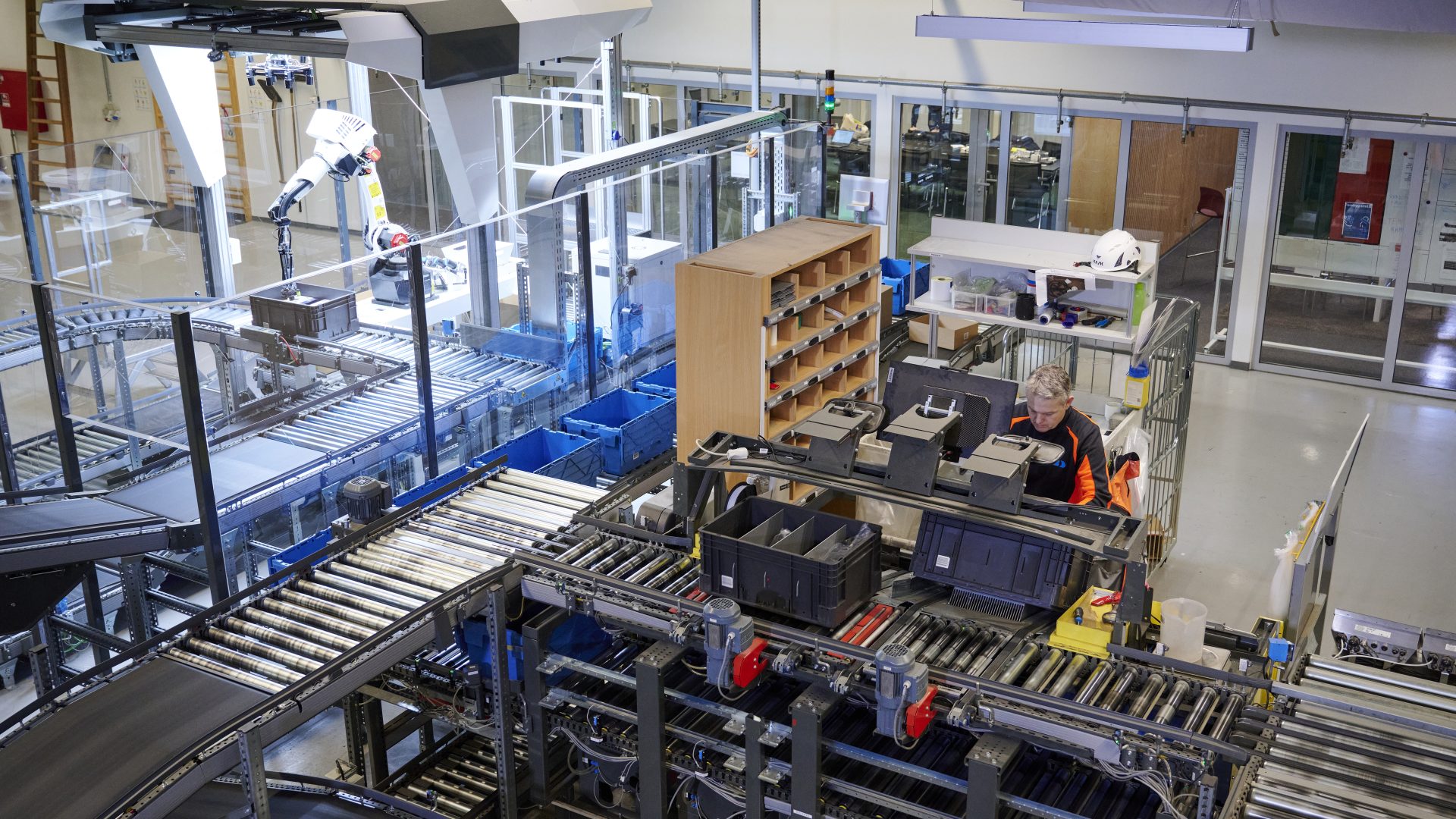
Closing and palletizing
The cartons are simply closed, while the plastic containers are lidded and sealed with a strap. Then, the load units move on to the palletizing robot where they are placed on different conveyors depending on their type. The robot first places the plastic containers on the pallet followed by the cartons. Similarly, replenishment orders for stores are placed on the bottom of the pallet, while purchase orders from customers are placed on top.
Delivery
When stacking is complete, the pallets are transported to the automatic pallet wrapping machine and then on to their allocated terminal for delivery.
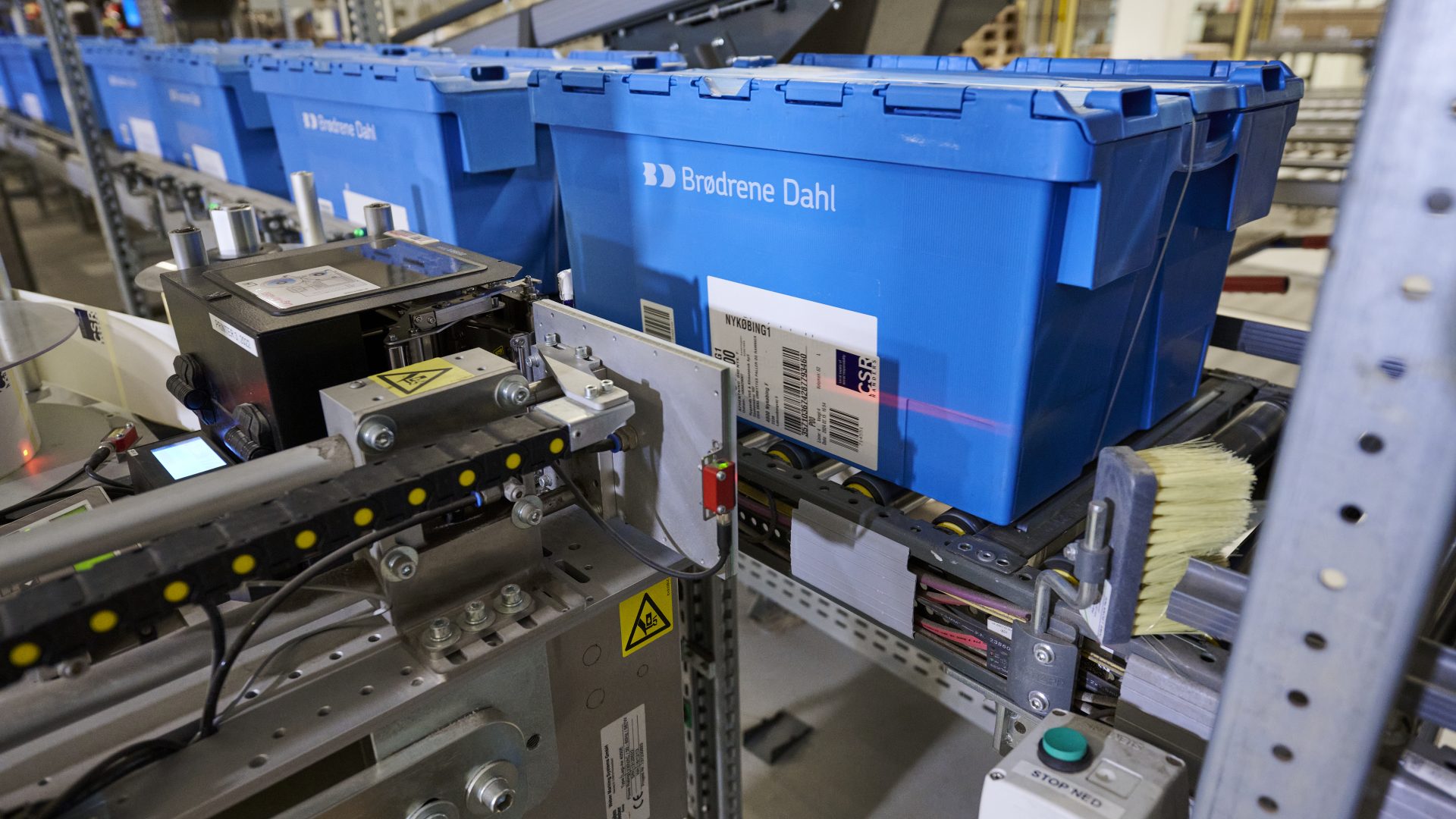
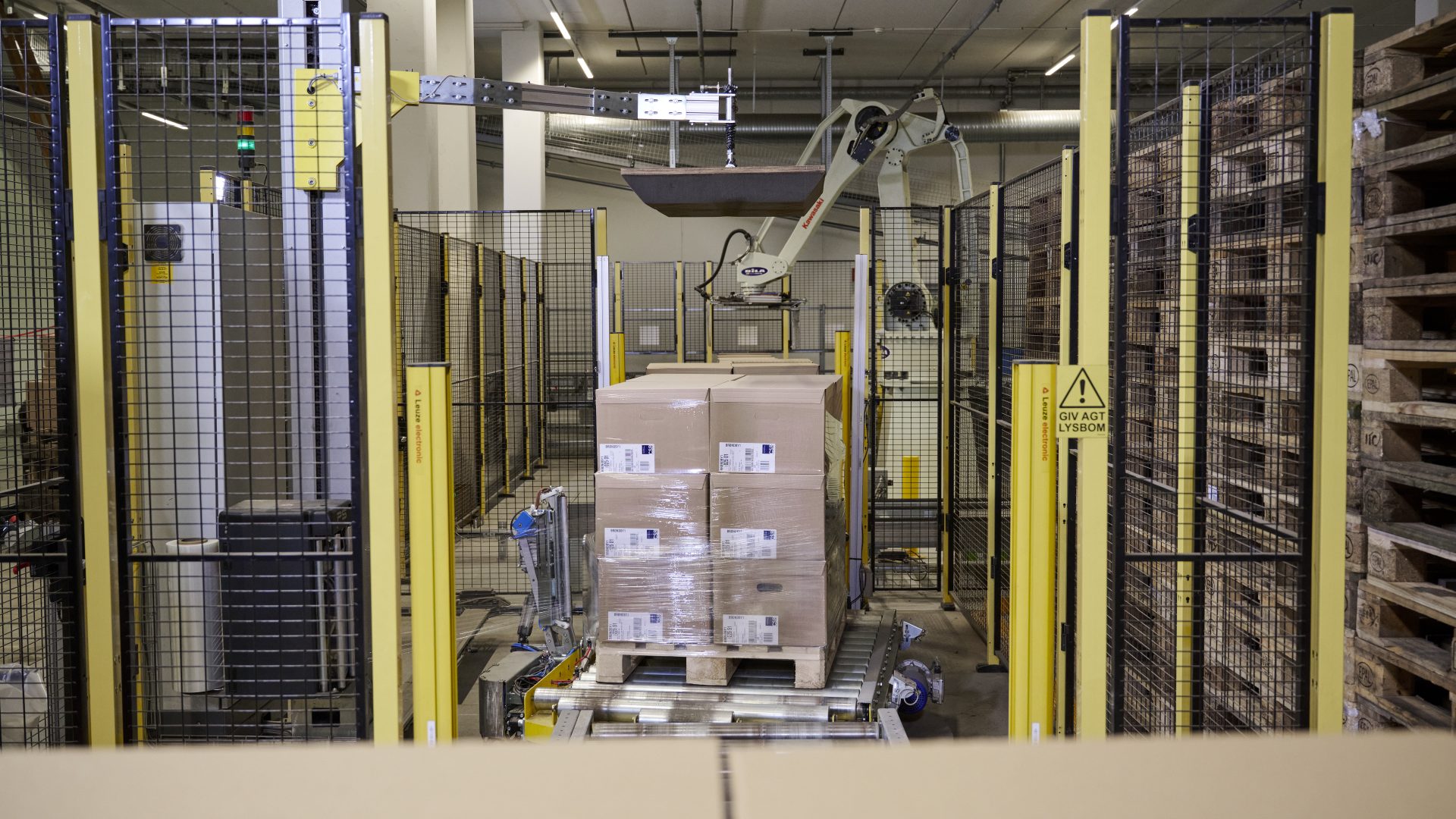
It is fair to say that LOGSTAR has allowed us to expand our product range, which has improved the selection for our customers.
Lasse Halliday
Logistics Director, Brødrene Dahl
orders per day
items per day
storage locations
shuttles
More picks with Pick-it-Easy Robot
Picking is carried out at 5 manual Pick-it-Easy work stations and 1 Pick-it-Easy Robot. The fact that Brødrene Dahl’s product range has grown by 40 % over the past 10 years has also lead to an increase in picks in the warehouse. That’s why the company opted for a robot that works around the clock without the need for more personnel, thereby increasing warehouse capacity. Every order is either picked manually or automatically by the robot. The manual stations provide space for 5 order containers and 2 storage containers, with the Pick-to-Light system supporting manual picking. The robot picks into 4 order containers (cartons or plastic containers) and 1 storage container. Around 1,100 order lines, which corresponds to roughly 7,000 items, are processed by the robot daily.
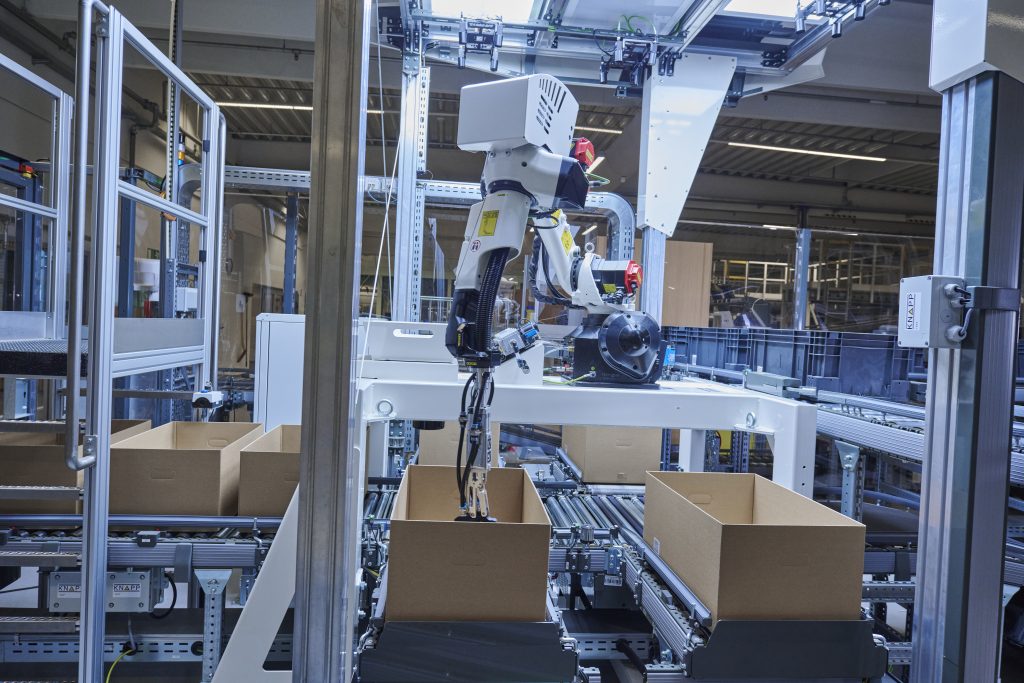
Better together
The collaboration between Brødrene Dahl and KNAPP began in 2013 when KNAPP convinced Brødrene Dahl of their expertise, which was the decisive factor for choosing KNAPP as an automation technology provider and partner.
Together, they will continue to further develop the current solution and increase robotization, for example, in the goods-in area. If needed, the Evo shuttle system can also be expanded to offer even more storage capacity.
KNAPP is a supplier of top-quality products. Their hardware is some of the best we’ve seen.
Mathias Elkjær Nielsen
Project Manager, Brødrene Dahl
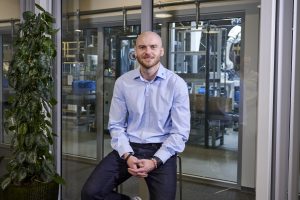