Fronius Opts for Automated Pallet Transport Using AMRs
for Flexible Production Supply
Fronius is a worldwide leader in battery charging, welding systems and solar energy. The proprietor-owned company was established in 1945 and has 37 subsidiaries on five continents. In 2022, Fronius employed 6,100 people worldwide. Along with their headquarters in Pettenbach and further locations in Wels, Thalheim, Sattledt and Steinhaus in Austria, the company also has a production location in the Czech Republic.
In Sattledt, Fronius manufactures welding systems for industry, inverters for photovoltaic systems and charging devices for warehouse vehicles. In 2022, the existing production hall was expanded by 28,000 m² (301,000 ft²) with the addition of another hall. To efficiently integrate the new hall, Fronius automated their pallet transport using our AMRs, the Open Shuttles.
You are currently viewing a placeholder content from YouTube. To access the actual content, click the button below. Please note that doing so will share data with third-party providers.
More InformationOpen Shuttle Fork optimally supplies production with pallets
At Fronius at the Sattledt location, the existing production hall of 41,000 m² (441,000 ft²) was expanded with another 28,000 m² (301,000 ft²) hall. The company wanted a solution to connect the new hall and to flexibly supply the production cells with pallets. Additionally, they wanted an automated connection between the production cells and goods-in and goods-out.
Fronius’s requirements for the solution
We chose KNAPP because their system allows us a very high level of autonomy. The new automation system sets us up for making changes at our location independently, as well as being able to expand our production cells. This makes our overall operation faster and more cost-efficient than it would be with other systems.
Technologies used at Fronius
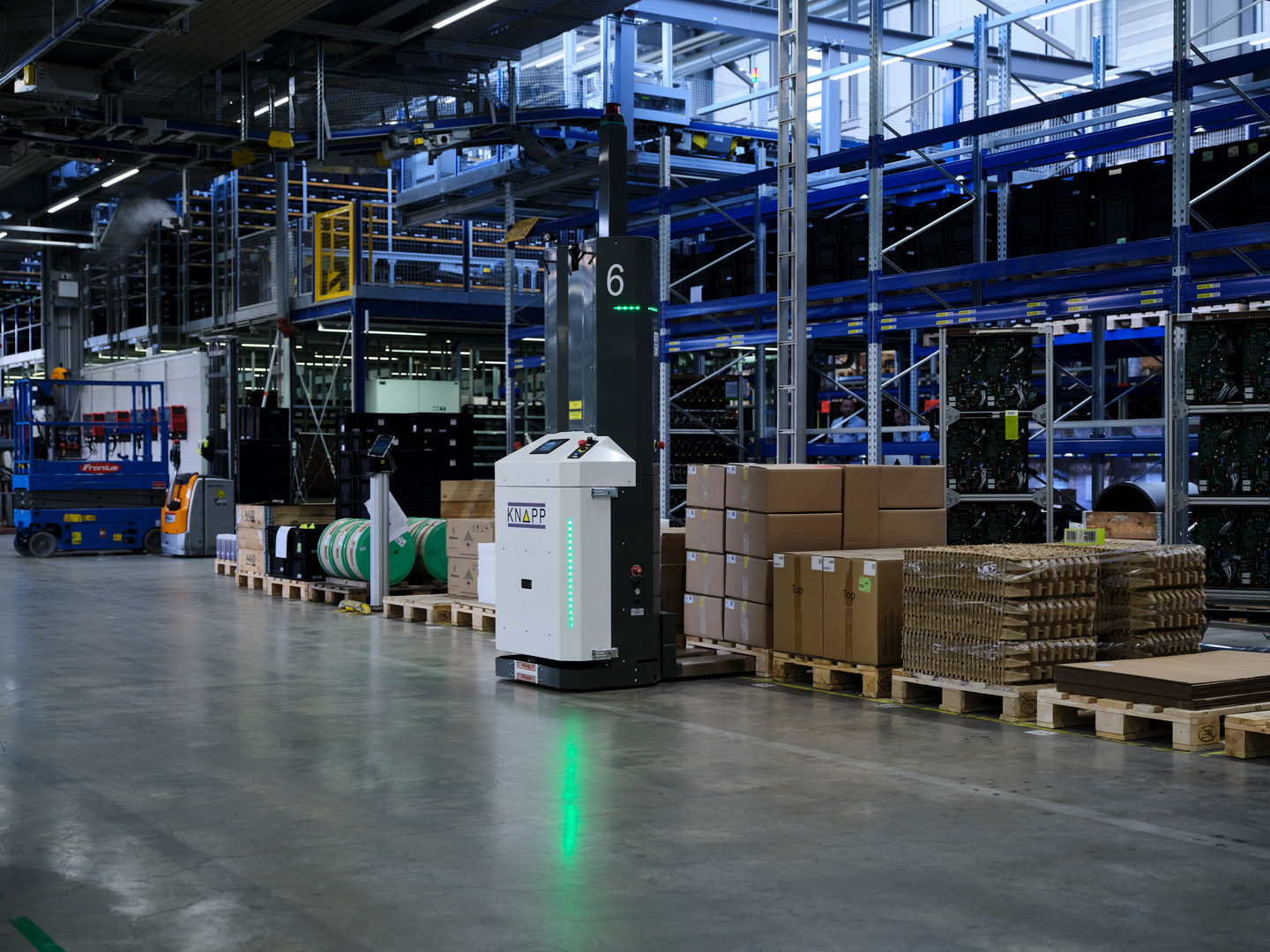
Open Shuttle Fork: Automated pallet transport AMR
The compact construction and agile maneuverability of the Open Shuttle Fork were prime factors in the decision to use the autonomous mobile robots. Their design made it possible to reduce the width of aisles, gaining additional space for manufacturing. The Open Shuttle Fork not only automates pallet transport (EUR-pallets and plastic pallets); it also transports the trash containers.
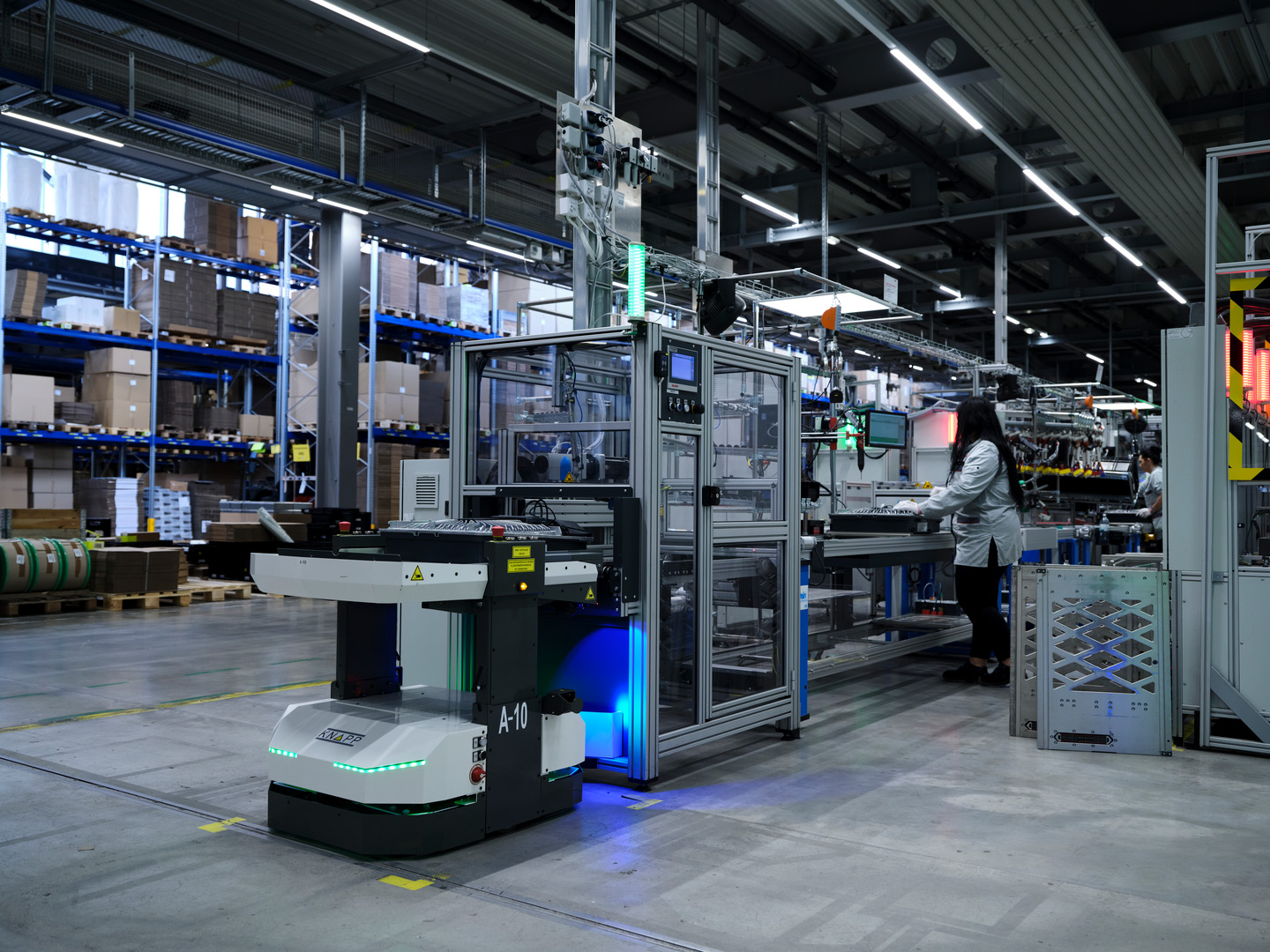
Open Shuttles: AMR times inverter transport perfectly
Since 2020, the Open Shuttles have played an integral part in producing Fronius inverters. They handle the timed transport of the inverters to the testing bays and packing lines and provide Fronius with a high degree of flexibility. Eleven Open Shuttles connect directly with the production lines, the testing bays and the packing lines. They supply the testing bays with inverters from the production lines for short-term and long-term tests and bring them to the packing line once the tests have been successfully passed.
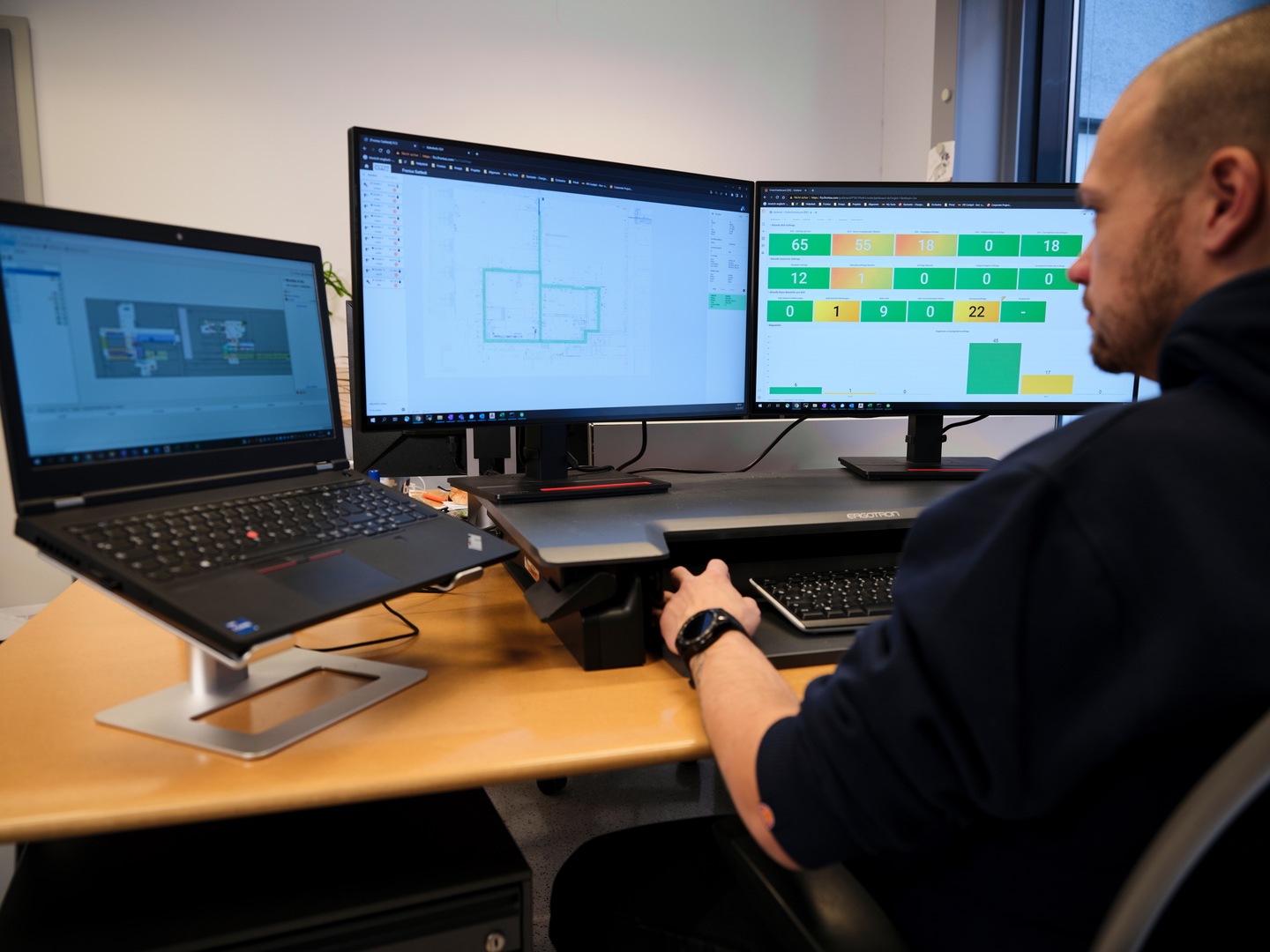
KiSoft FCS: Innovative software for AMRs
The software KiSoft FCS (Fleet Control System) centrally controls the robots. It connects to the customer system through an interface and controls the fleet, managing the storage and retrieval movements of the pallets as well as the supply to the production cells. Thanks to KiSoft FCS, Fronius is able to adapt their paths and add stations. The software also includes a dashboard that visually depicts all the key transport figures, meaning that Fronius always has an overview of all the robots in operation.
Orders for the Open Shuttle Fork are generated on tablets, with an input mask that was specially developed for Fronius. Both the AMRs and the manual forklifts are mapped in KiSoft FCS, making coordination between automated and manual transport activities extremely flexible.
Overview of efficient transport processes with AMRs
Open Shuttle Fork robots
Open Shuttles
km traveled / day
(249 mi)
testing bays
pallet locations
m² hall space
(742,710 ft²)
Automated pallet transport
Goods from the central warehouse are set down at the pallet station prior to transport to the production cells.
Pallet storage locations are located right next to the individual production cells. The Open Shuttle Fork robots pick up the semi-finished products and transports them to the next production step.
The robots also supply completed machines and devices on pallets to the pickup locations and transport them to the goods-out warehouse, where they are put down, packed and then stored in the automated pallet warehouse.
The Open Shuttle Fork robots also handle special transport jobs, such as transporting trash containers to their storage location.
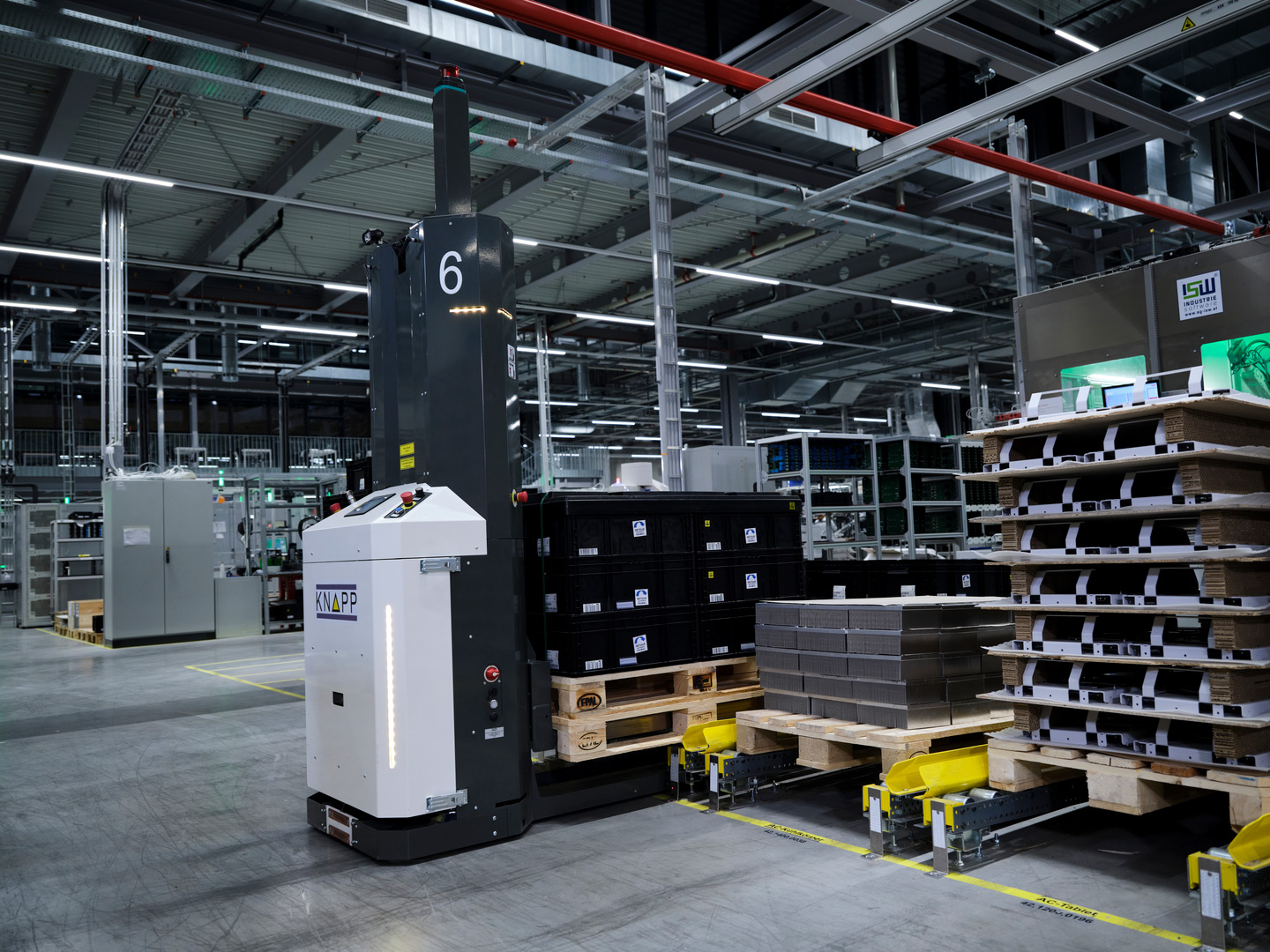
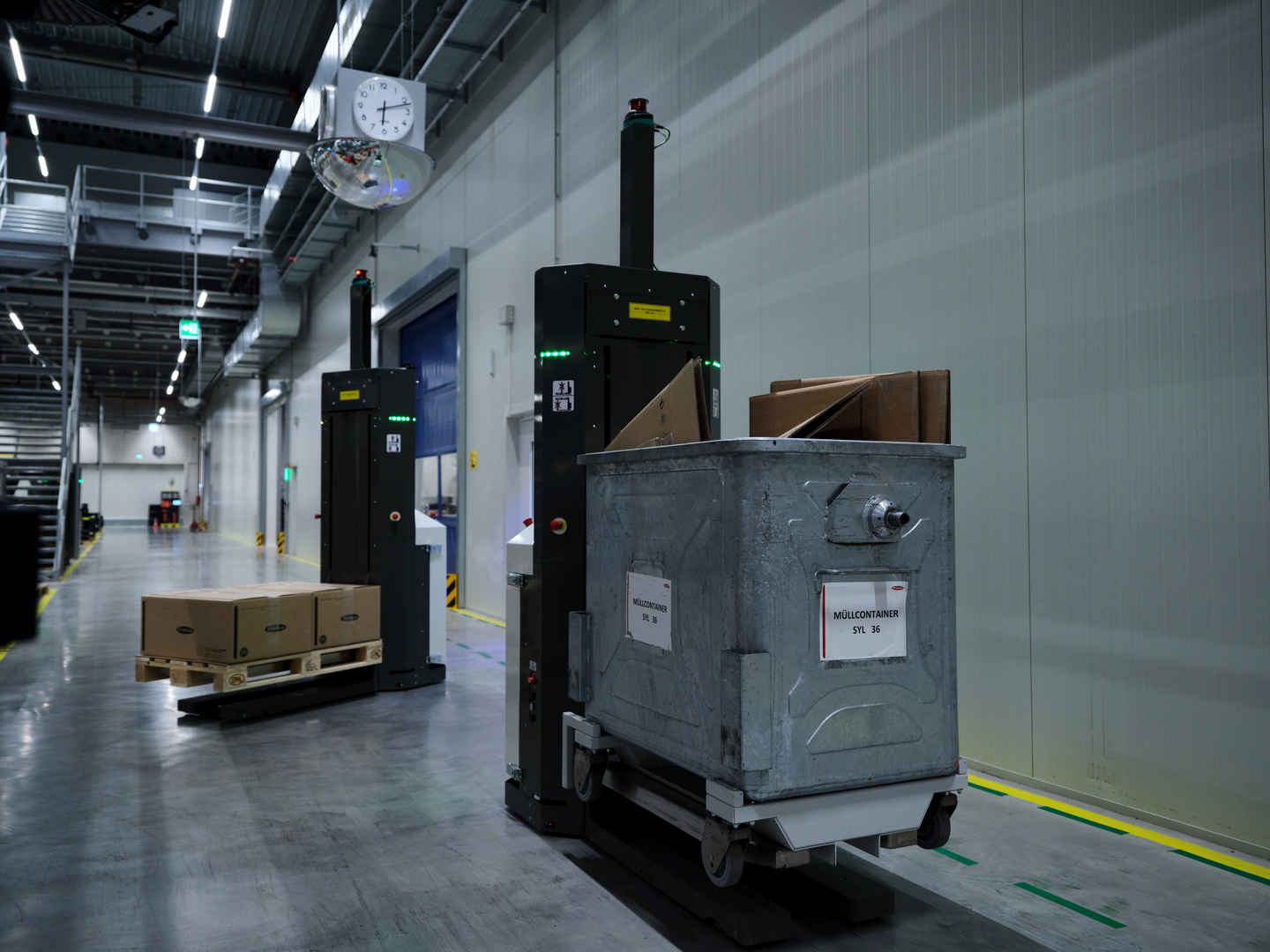
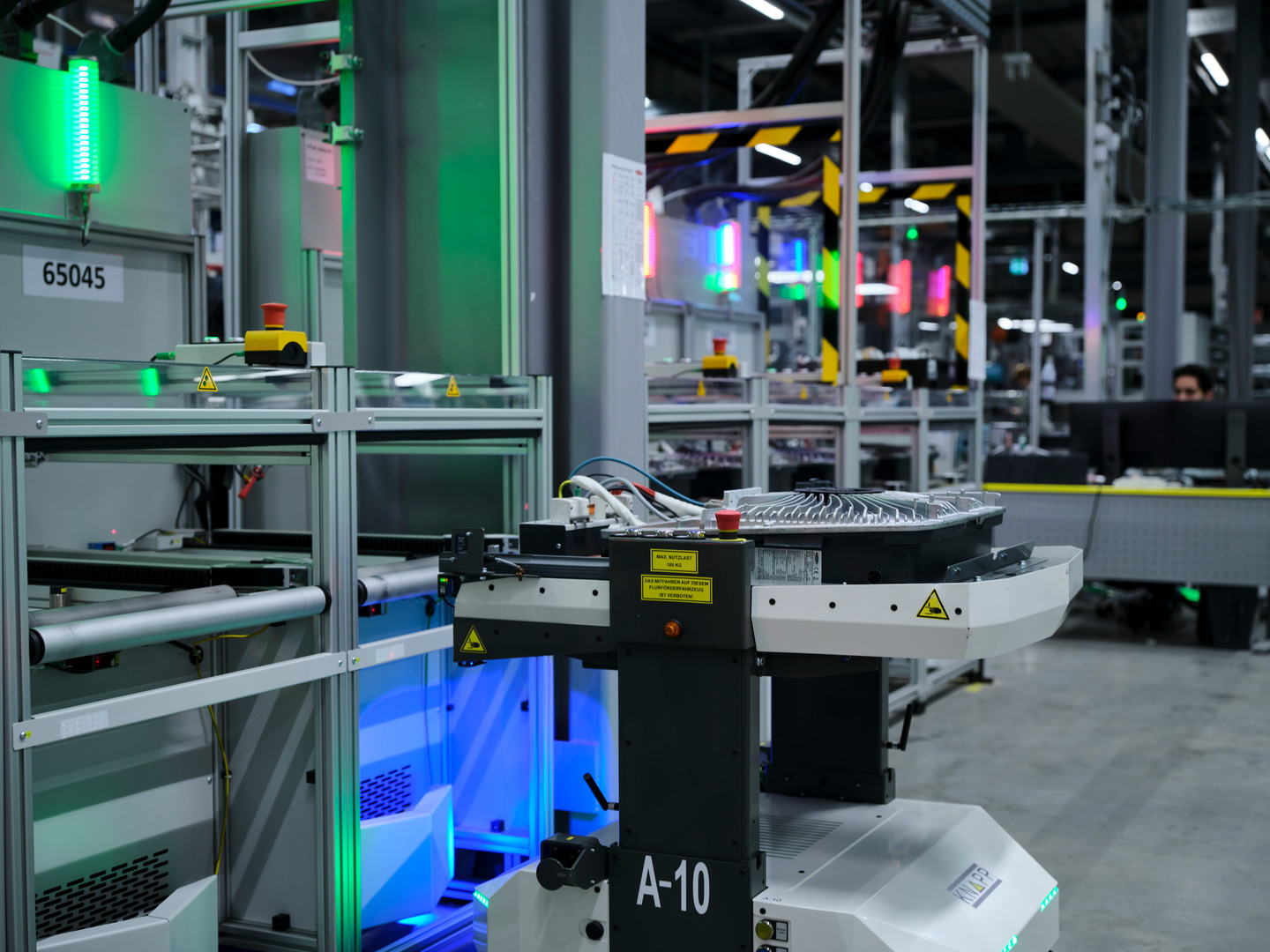
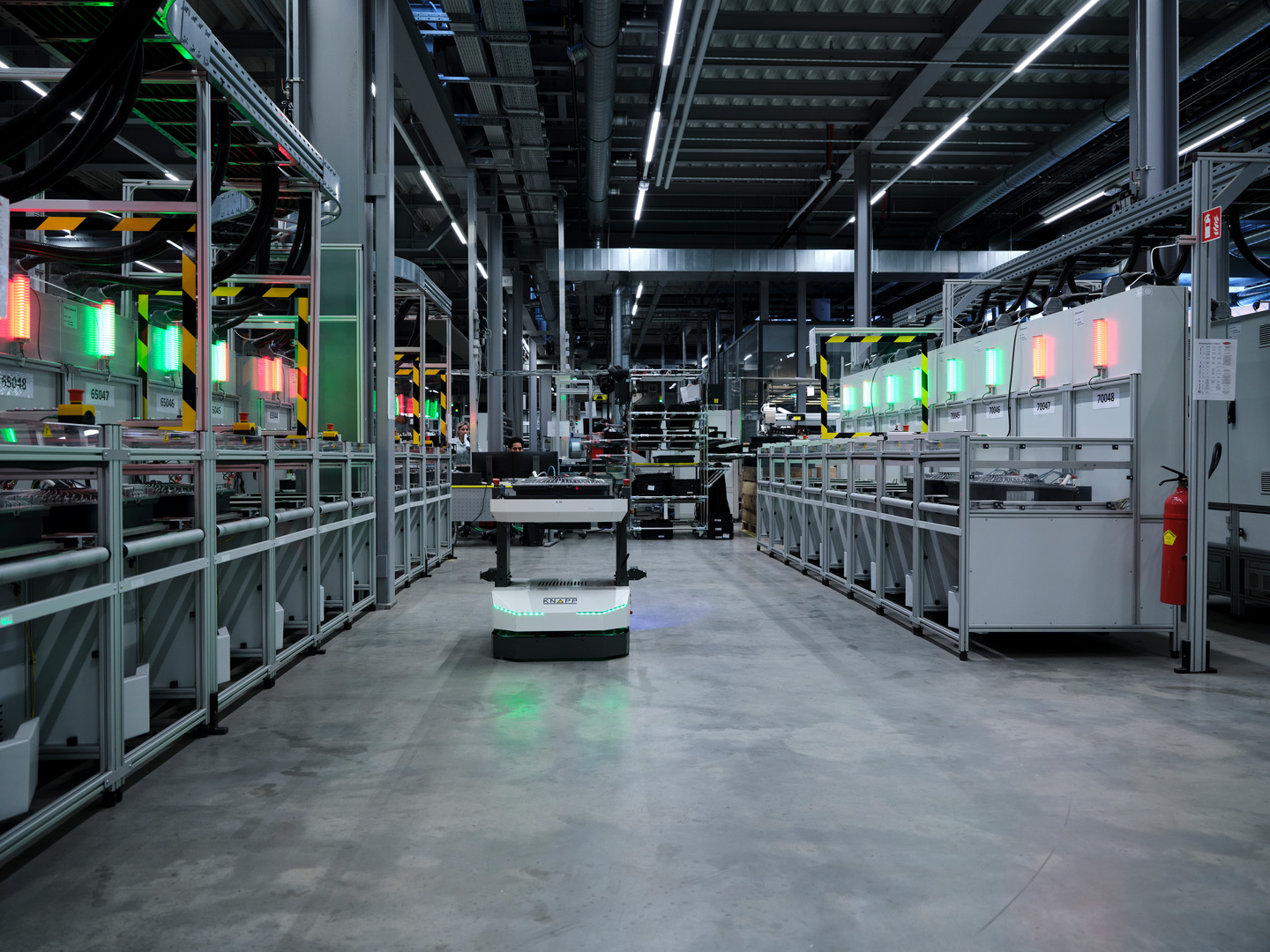
Timed transport of inverters
The inverters are produced on the production lines and mounted on carrier plates. When an inverter is completed, it is picked up from a short conveyor by an Open Shuttle and transported to a free testing bay for automatic short-term testing.
After the short-term test is successfully completed, the Open Shuttle transports it to long-term testing.
Once both tests have been passed, the Open Shuttle picks up the inverter and automatically brings it to the packing line. Empty load carriers are also returned to the manufacturing area by the Open Shuttles.
If any inverters do not pass the short-term or long-term tests, they are automatically transported to the reworking station, where they are reworked before being picked up again and sent back to testing.
Automated pallet transport
Goods from the central warehouse are set down at the pallet station prior to transport to the production cells.
Pallet storage locations are located right next to the individual production cells. The Open Shuttle Fork robots pick up the semi-finished products and transports them to the next production step.
The robots also supply completed machines and devices on pallets to the pickup locations and transport them to the goods-out warehouse, where they are put down, packed and then stored in the automated pallet warehouse.
The Open Shuttle Fork robots also handle special transport jobs, such as transporting trash containers to their storage location.
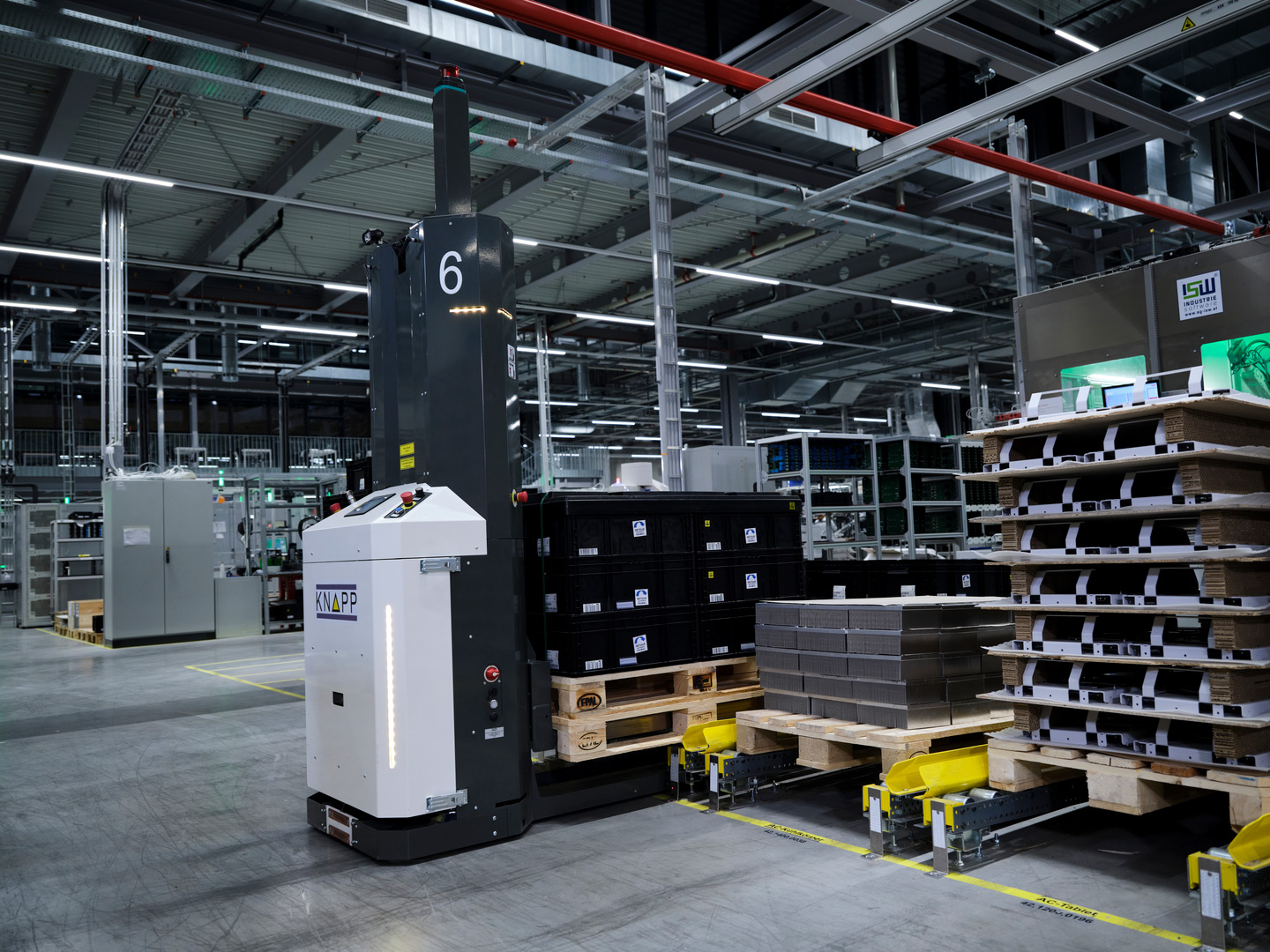
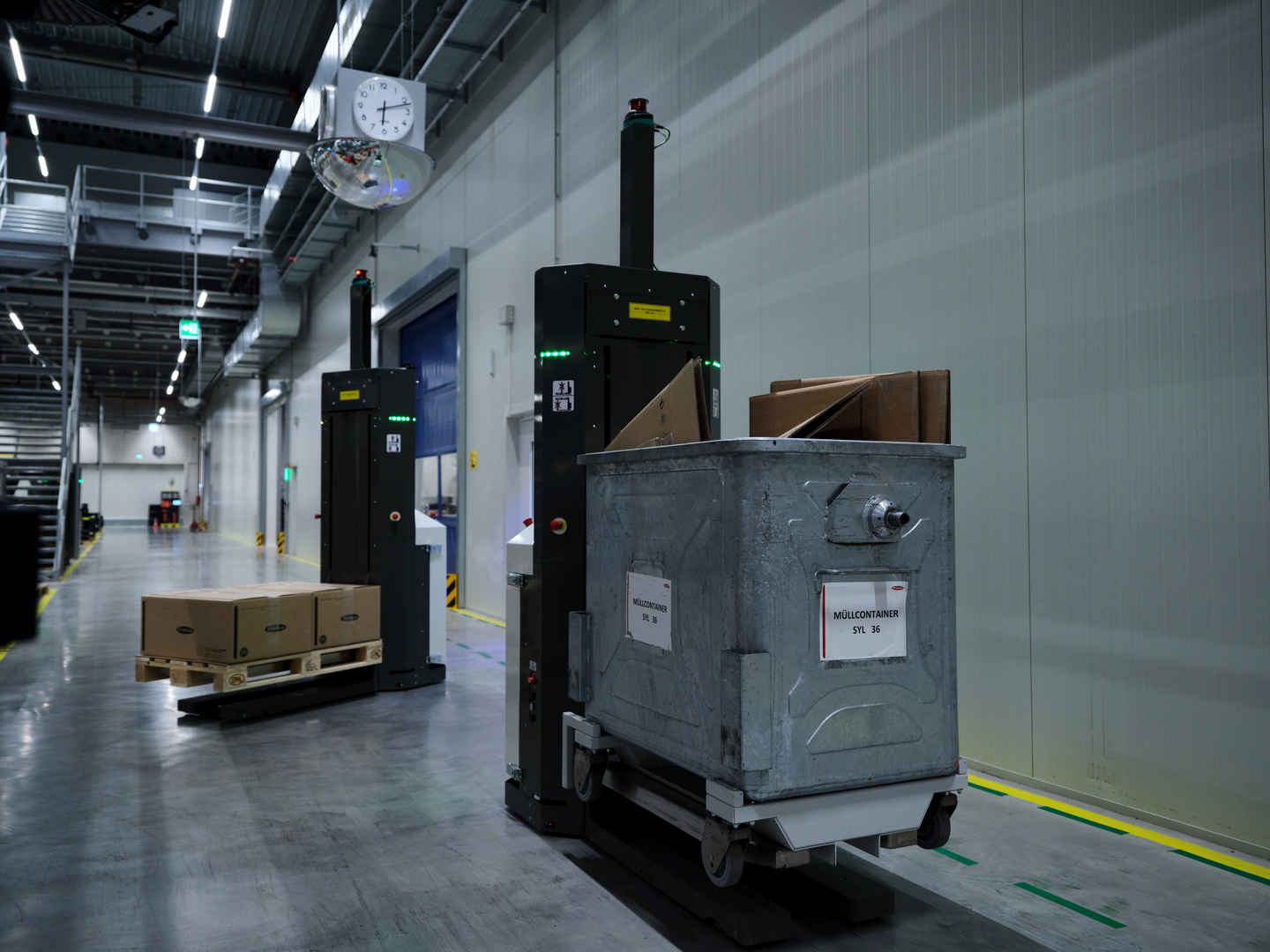
Getakteter Wechselrichtertransport
The inverters are produced on the production lines and mounted on carrier plates. When an inverter is completed, it is picked up from a short conveyor by an Open Shuttle and transported to a free testing bay for automatic short-term testing.
After the short-term test is successfully completed, the Open Shuttle transports it to long-term testing.
Once both tests have been passed, the Open Shuttle picks up the inverter and automatically brings it to the packing line. Empty load carriers are also returned to the manufacturing area by the Open Shuttles.
If any inverters do not pass the short-term or long-term tests, they are automatically transported to the reworking station, where they are reworked before being picked up again and sent back to testing.
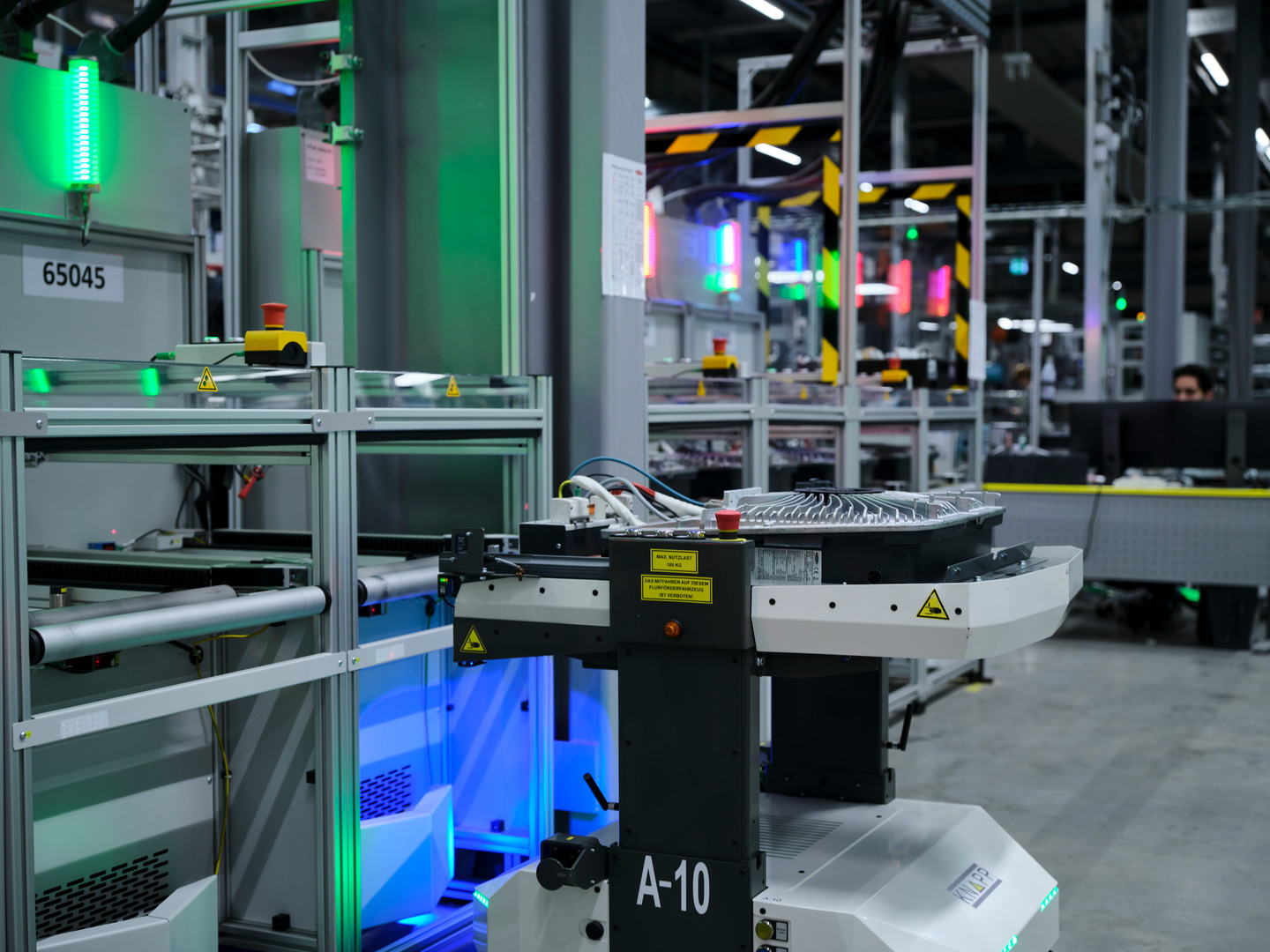
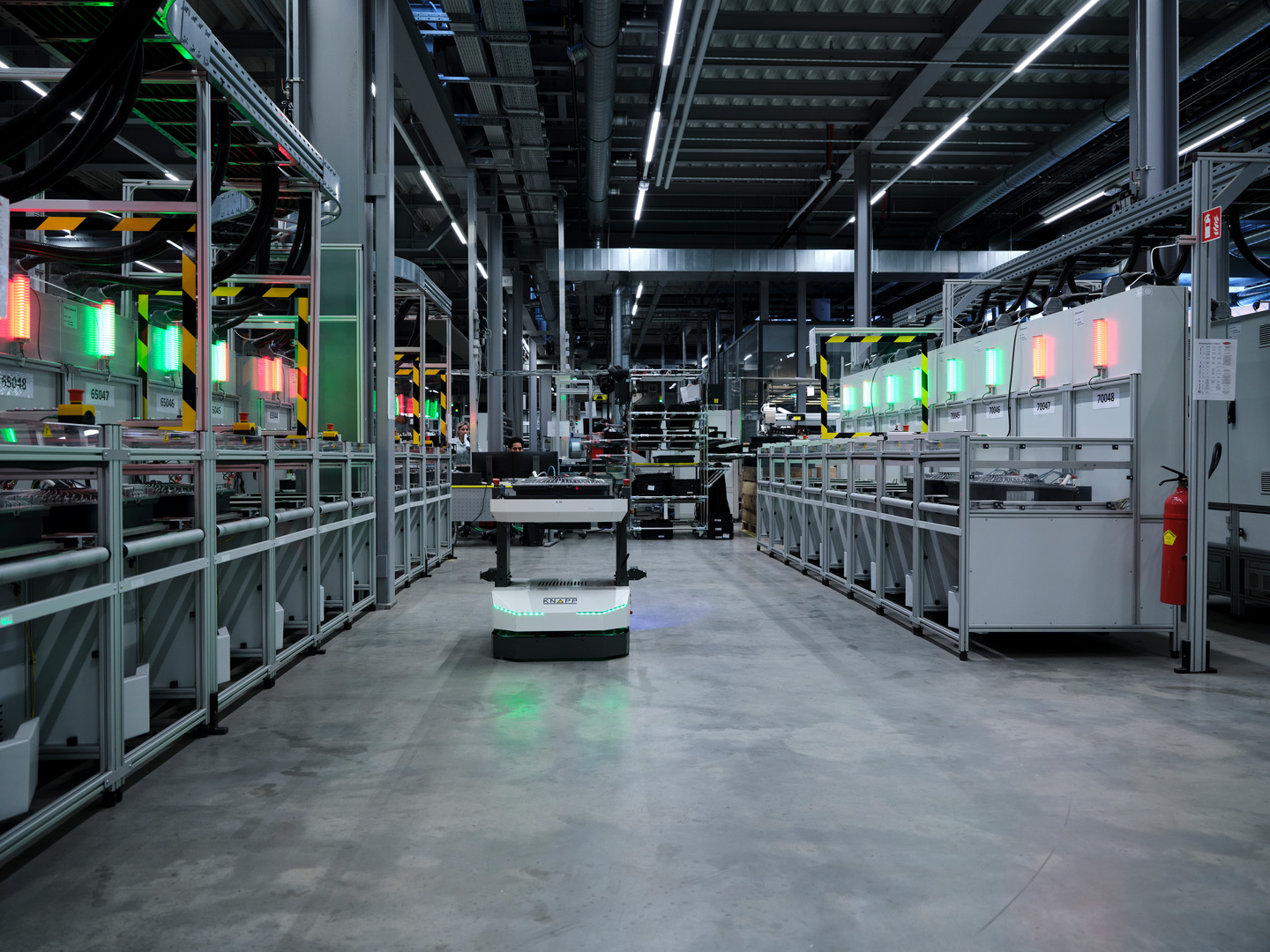
Another great feature of the system is the efficient battery management. The Open Shuttles charge their batteries when there are no transport jobs. The charging device for the Open Shuttles is naturally a Fronius product, reflecting the long-standing partnership between the two companies.