Fully automatic empties sorting
The trend toward more sustainable use of resources is impacting the beverage industry. Here, the solution is a highly automated sorting system that rapidly processes empty crates and bottles in preparation for refilling. LLS’s installation in Hamm, Germany, features such a sorting system. The empties management solution developed by LLS, LOGIPACK and KNAPP makes it possible to handle all types of empties at a single location with fully automatic sortation.
You are currently viewing a placeholder content from YouTube. To access the actual content, click the button below. Please note that doing so will share data with third-party providers.
More InformationAn Innovative Alliance for Effective Empties Management
Combining the know-how of LOGIPACK and LLS with our Reusables Management Solutions (RMS) creates an economical system that benefits bottlers, food retailers as well as wholesalers in the beverage industry. The system keeps the number of empty crates at the end of sorting to a minimum and increases sorting precision, performance and throughput thanks to the high level of automation.
KNAPP, LLS and LOGIPACK’s business models complement each other perfectly. Our innovative alliance drives the development of Germany’s reusables system.
Are you also interested in innovative empties management?
Get in touch with our experts.
We’re planning and developing and introducing similar concepts in other LOGIPACK centers based on our experiences with the innovative concept in Hamm.
A one-of-a-kind solution
Our Reusables Management Solutions (RMS) make it possible to handle all types of empties at a single location with fully automatic sortation. This ensures that the empties are quickly ready for reuse in unmixed units. This is how we complete the circle in the food industry, making the return of reusables efficient, economical and practical.
million bottles per year
crates per hour
crates per hour
crates per hour
The highlights of our solution
The integrated software tells the system exactly which crates are needed to optimize the sorting process and requests them accordingly at goods-in. Once fed into the system, the automatic pallet recognition checks if the pallet is the correct one and the depalletizing robot unloads the crates. Then they are run through a recognition system, which registers both the crates and the bottles they contain in just a few seconds. Based on this information, the recognition system – the brain of the solution – chooses one of three paths.
- Bottle-sorting robot
- Tray repacking robot
- Detection and check systems for robot control
- De- and Palletizing robot
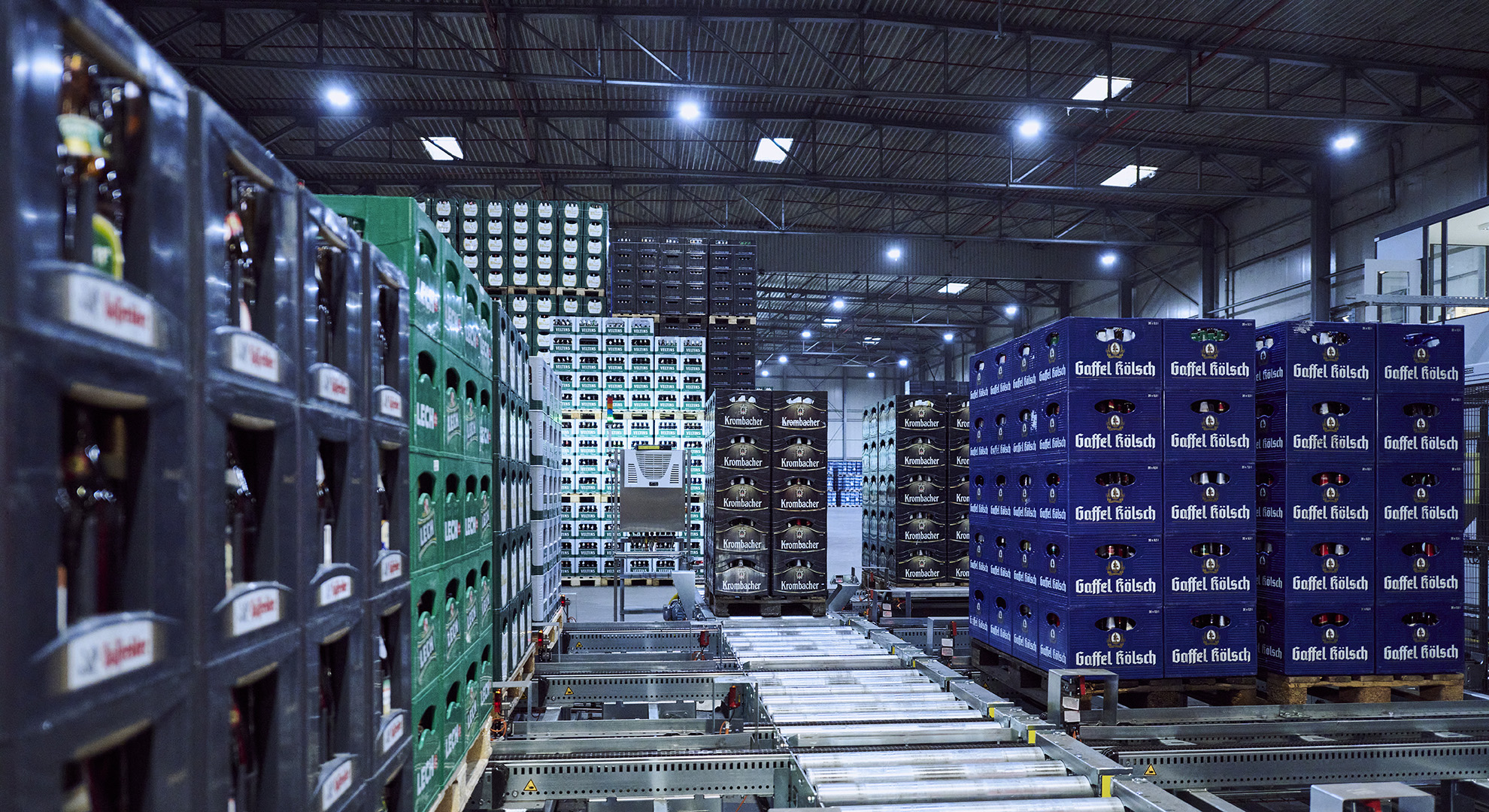
From the time of recognition, we always know where each bottle is and in which crate.
Fully automatic single bottle sorting
Unsorted empties are brought to the heart of the solution: the bottle-sorting robot. It automatically removes single bottles and places them in the correct crates based on the data collected by the recognition system, optimizing the movement of crates and minimizing the number of empty crates that exit sorting. At the end of in-depth sorting, the empties leave the robot in unmixed crates.
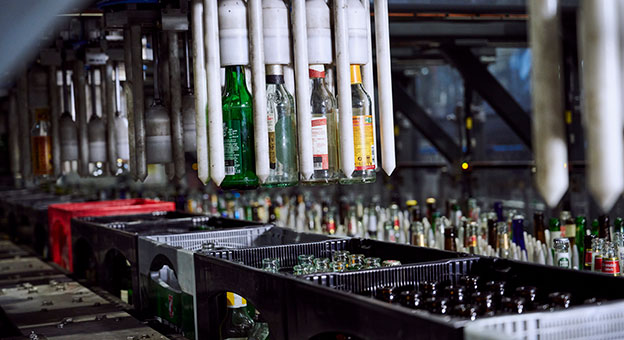
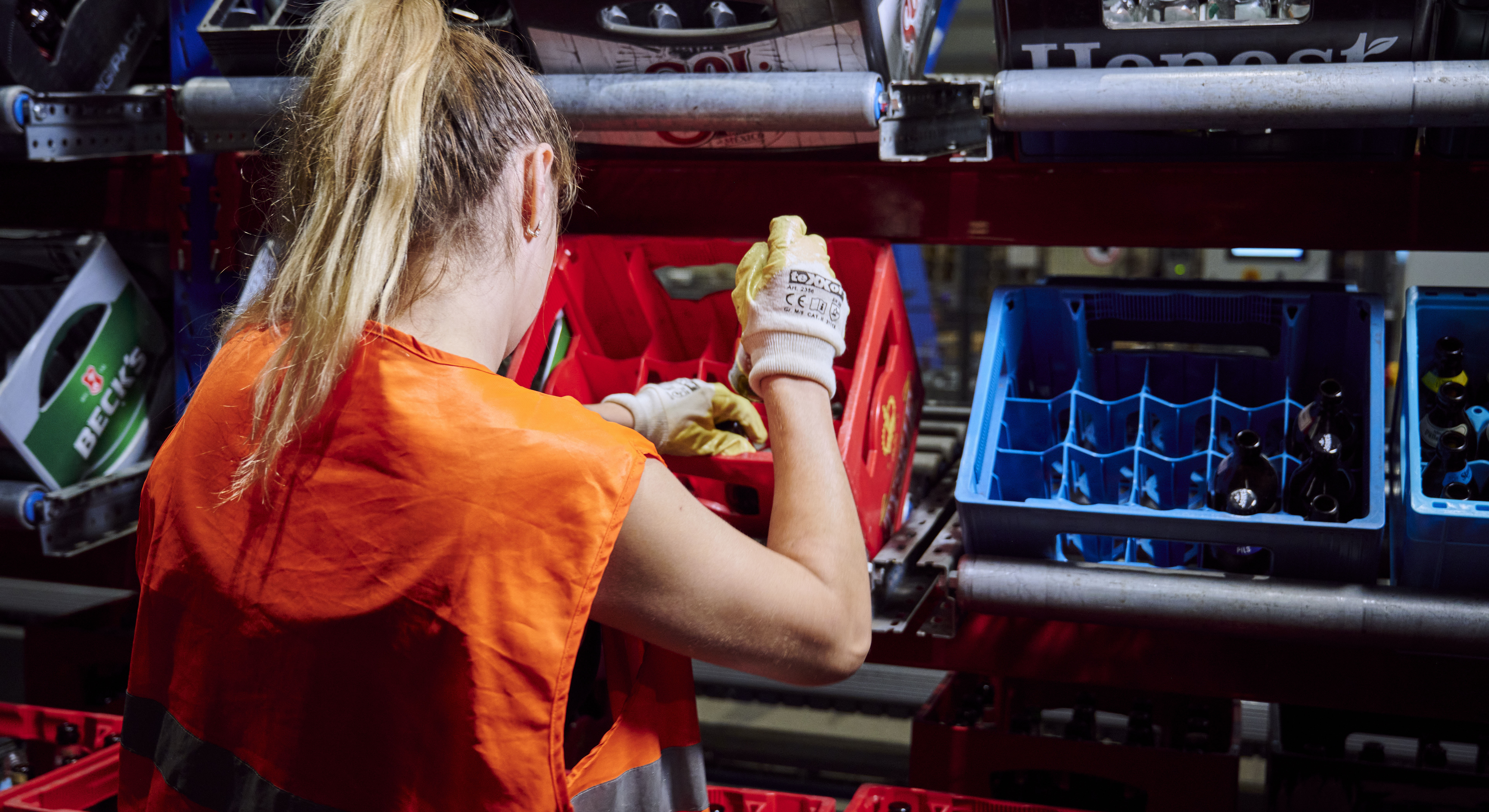
Manual crate sorting
Crates that could not be recognized by the recognition system or are not intended to be automatically sorted are instead automatically brought to a manual sorting area. After processing, these empties are returned to the main sorting system.
Checking for uniformity
All crates containing sorted empties from goods-in or sorting are then brought to a control system that checks for uniform content in the crate. At the end of the process, the palletizing robot retrieves the sorted empties and places them on pallets. The one-of-a-kind, fully automatic process rapidly fills the reusable crates with unmixed empties, which are then ready for refilling.

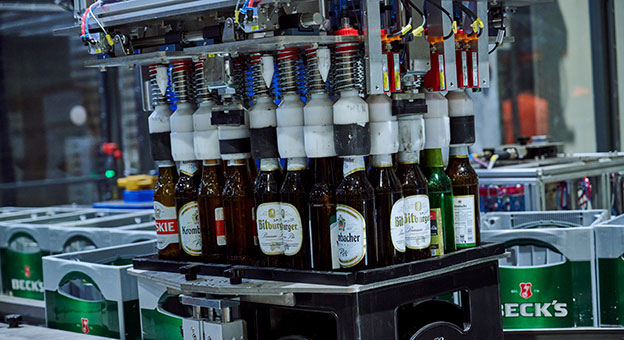
Repacking robot fills empty crates with empties from trays
A repacking robot completes the unique system. It processes LOGIPACK’s empties on trays completely automatically. The robot removes single bottles from the trays and places them in the empty crates from the upstream sorting process. The system then returns the filled, unmixed crates to the sorting process to be stacked on pallets.
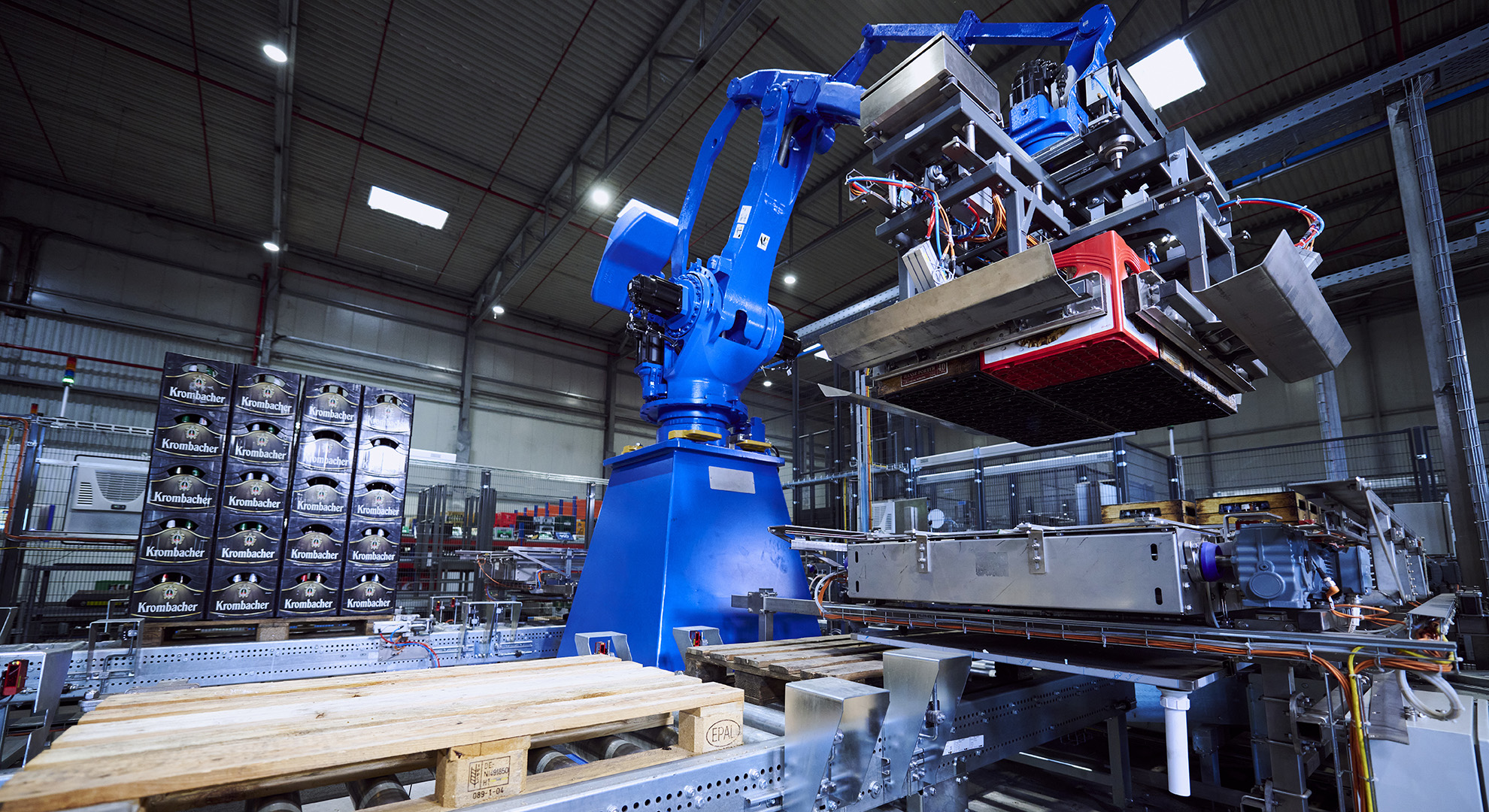
Are you interested in innovative empties management?
Get in touch with us.