Optimized distribution platform for global business model
Luxottica manufactures and sells luxury eyewear all around the globe and relies on a global growth strategy. The company made the strategic decision to build a new distribution center in Sedico, Italy to centralize the logistics for partner retailers, Luxottica stores and end customers. Luxottica and KNAPP have worked together for years to optimize the complex processes involved in distributing their products. Luxottica is the parent company of luxury brands such as Ray-Ban and Oakley and of licensed brands such as Giorgio Armani and Versace. In 2018, Luxottica merged with Essilor to form EssilorLuxottica and today employs 180,000 people worldwide.
You are currently viewing a placeholder content from YouTube. To access the actual content, click the button below. Please note that doing so will share data with third-party providers.
More InformationFor us, KNAPP is just the right technology partner. For every process step, they’ve managed to find the right balance between cutting-edge technology and simple procedures.
Andrea Lombardo
Head of EMEA Logistics and Distribution
Would you like to boost the efficiency of your value chain?
Our experts are happy to help!
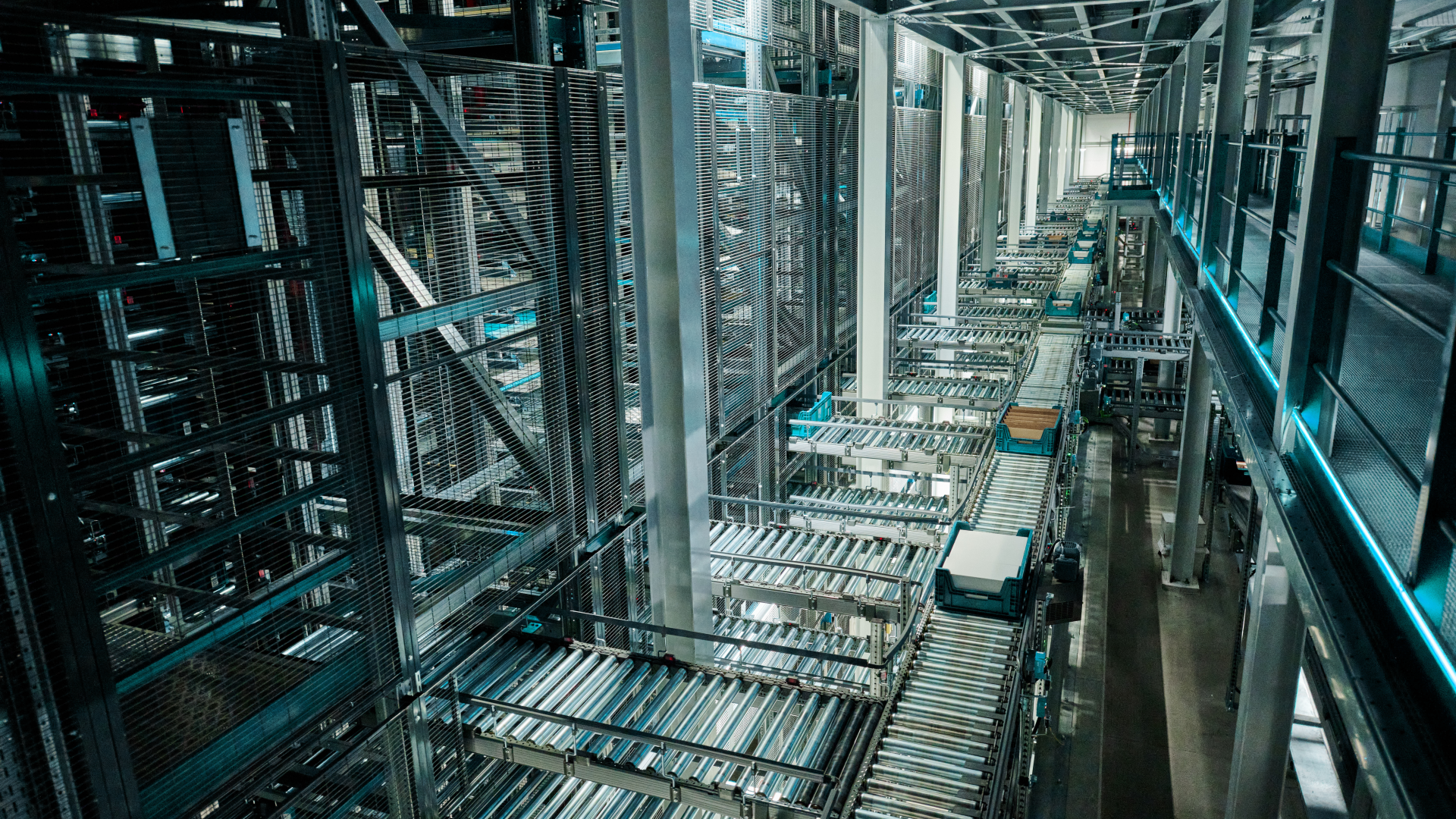
Goods-in and storage
In the goods-in area, all items are recorded by the KiSoft WMS software and stored in the Evo Shuttle, KNAPP’s automated picking and storage system. Out of the 500,000 storage locations available, the software allocates every item to its ideal storage location.
Order start
Besides managing the warehouse processes, KiSoft takes care of order management, calculating the right start time of every order and the best route through the warehouse. There are 11 possible carton sizes available for processing the orders. The cartons are automatically erected and then placed on a tray.
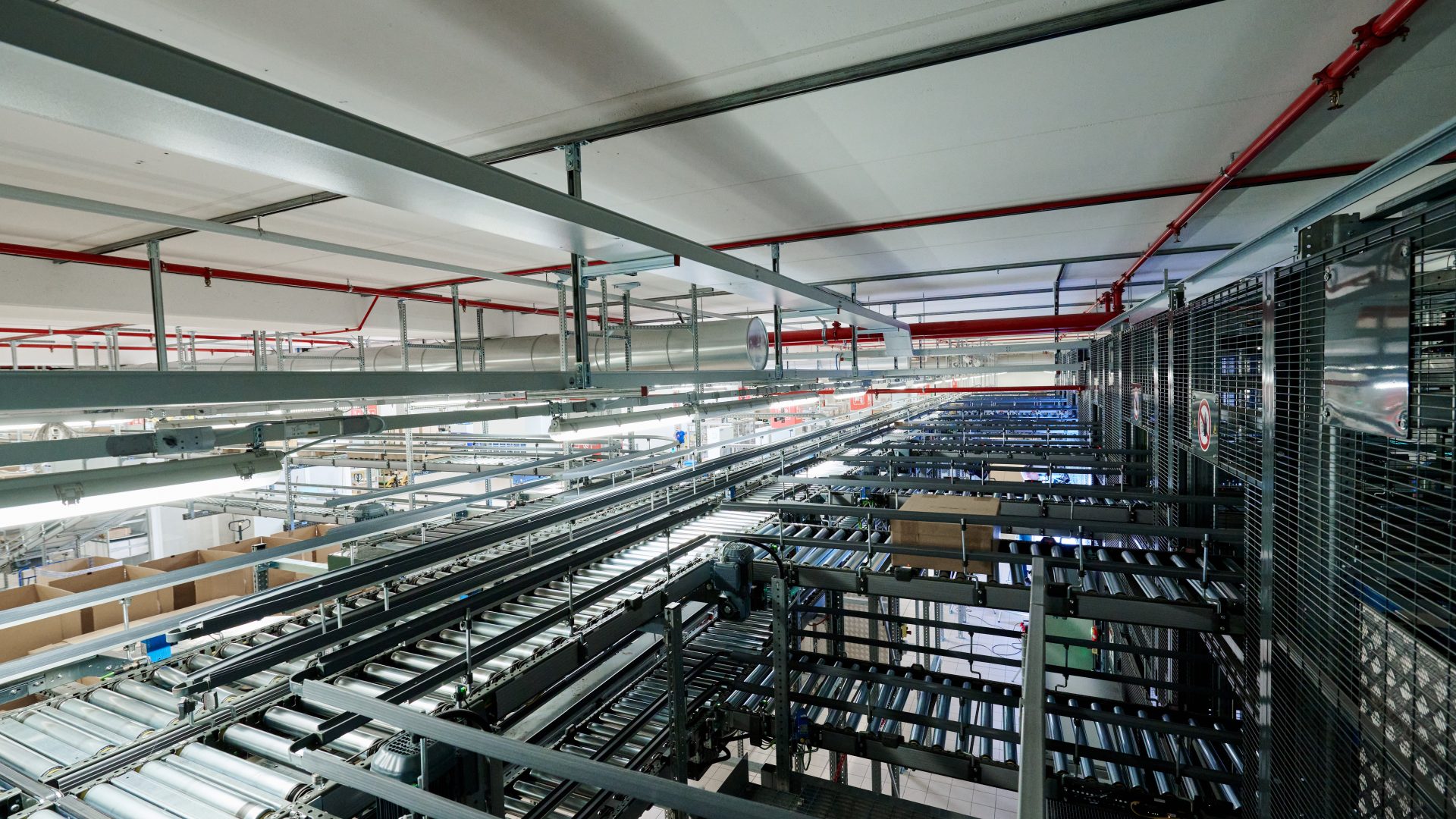
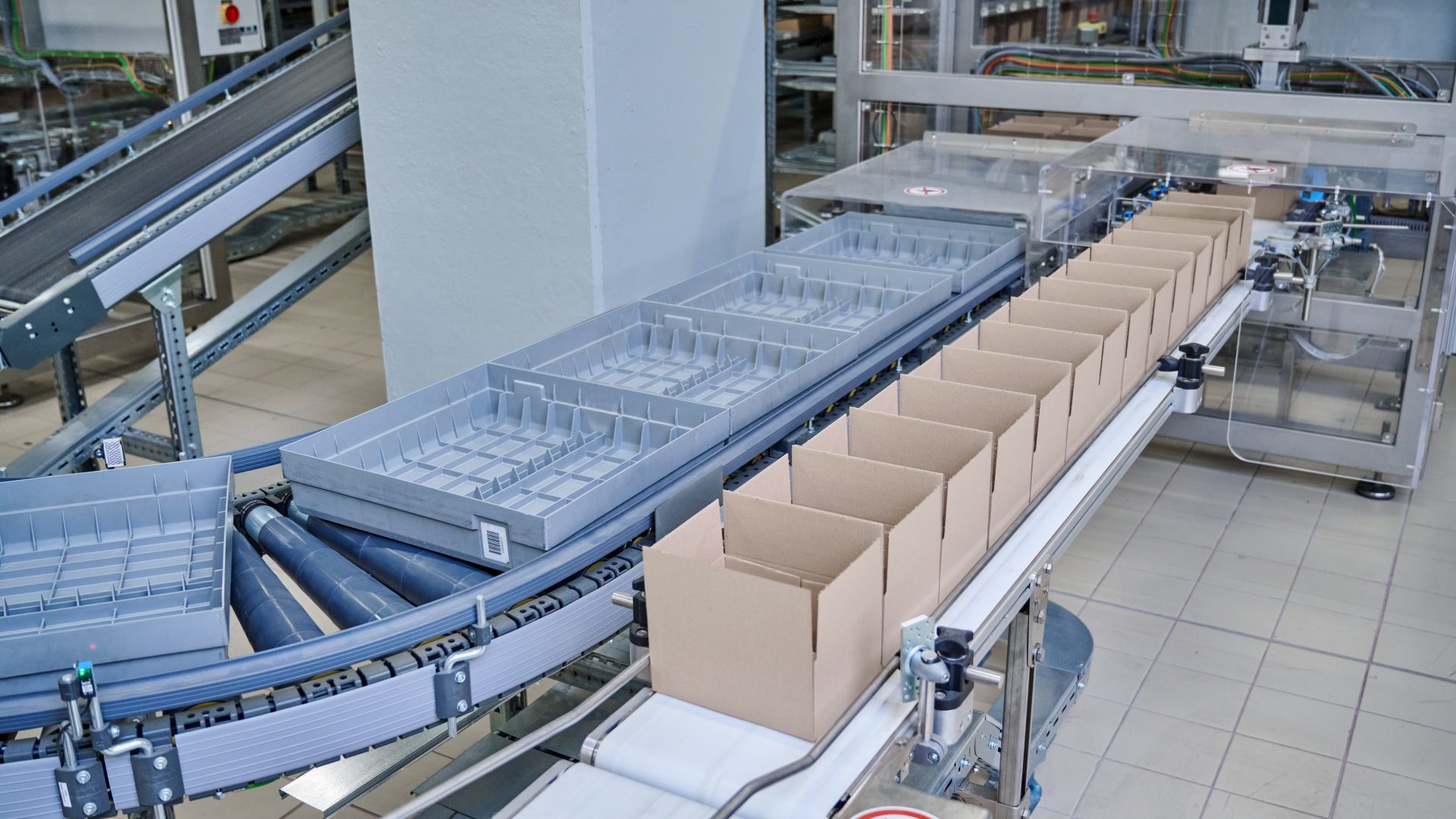
Picking
For picking, a carton in the right size is conveyed to one of the 19 goods-to-person work stations. These work stations are ergonomically designed, making it easy for Luxottica employees to pick orders efficiently. Items that are in high demand are placed into order cartons in the manual picking area.
Quality control and invoice insertion
Every carton is automatically weighed and its contents are recorded using an RFID scanner and additionally checked if necessary. Then the invoices are added and the cartons closed, all fully automatically. For smaller cartons, the invoice is applied to the outside of the carton using a special process.
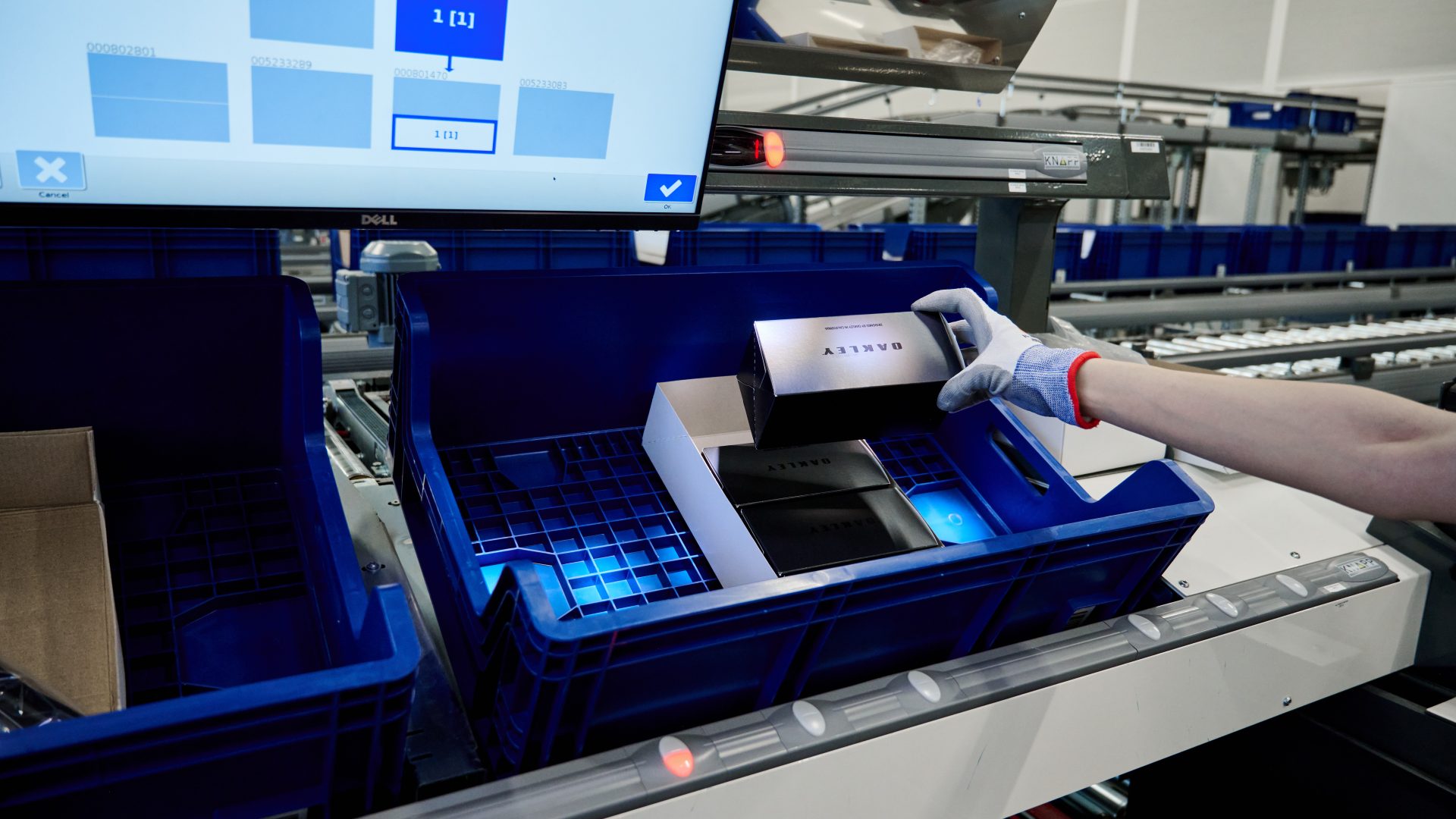
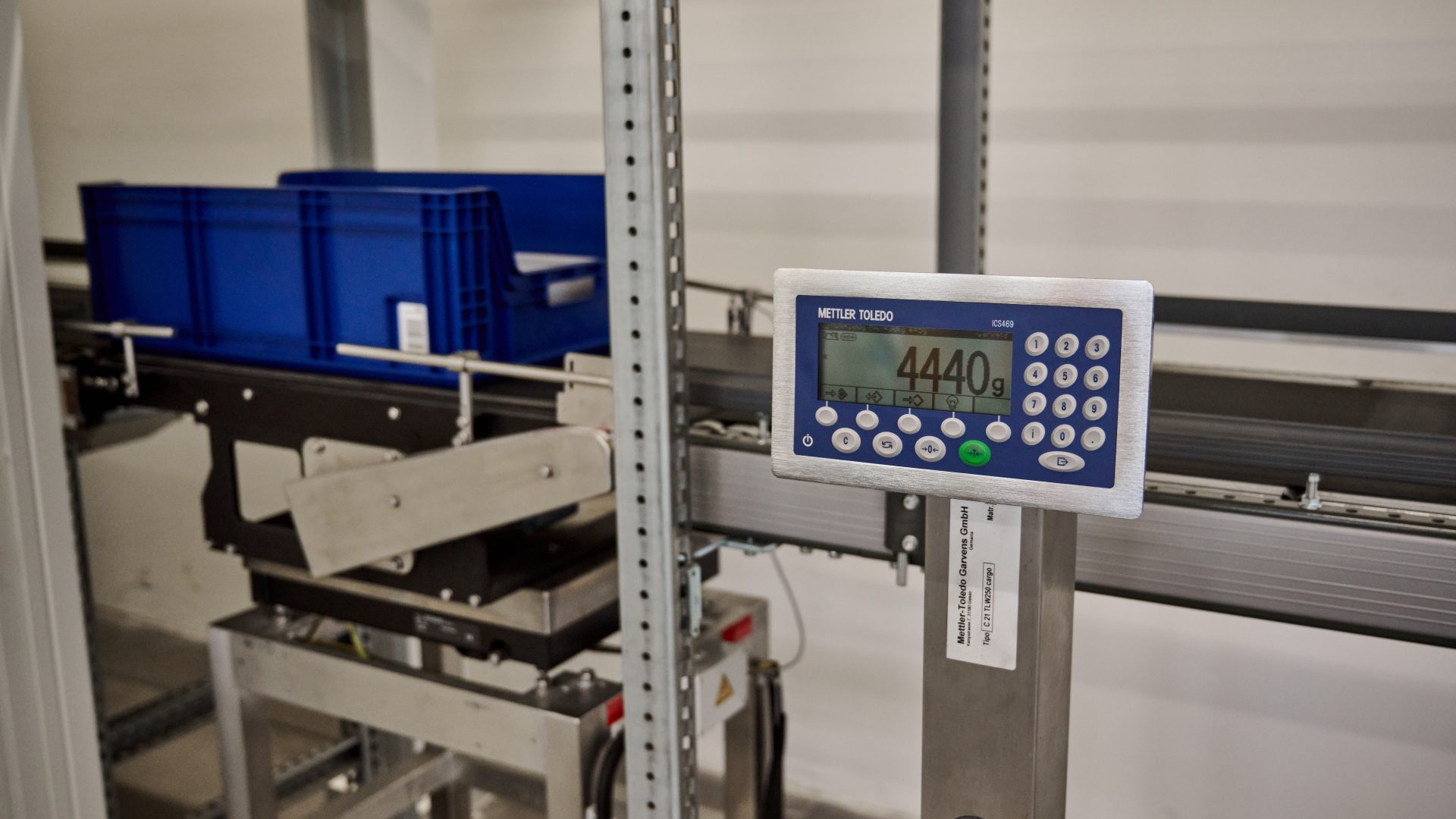
Shipping preparation
Express orders are buffered in the INDU-Store, our fully automatic warehouse system for single-item handling, which keeps the items secure and accelerates the delivery of online orders.
The box-in-a-box concept boosts efficiency: The software clusters orders according to their destination or allocates smaller cartons to larger cartons to make sure the items are secure during shipping.
Shipping
Our palletizing robot stacks the cartons onto pallets for shipping. In the process, the robot takes into account various predefined criteria to create a solid, stable stack. In addition, the cartons are secured for shipping and receive a shipping label.
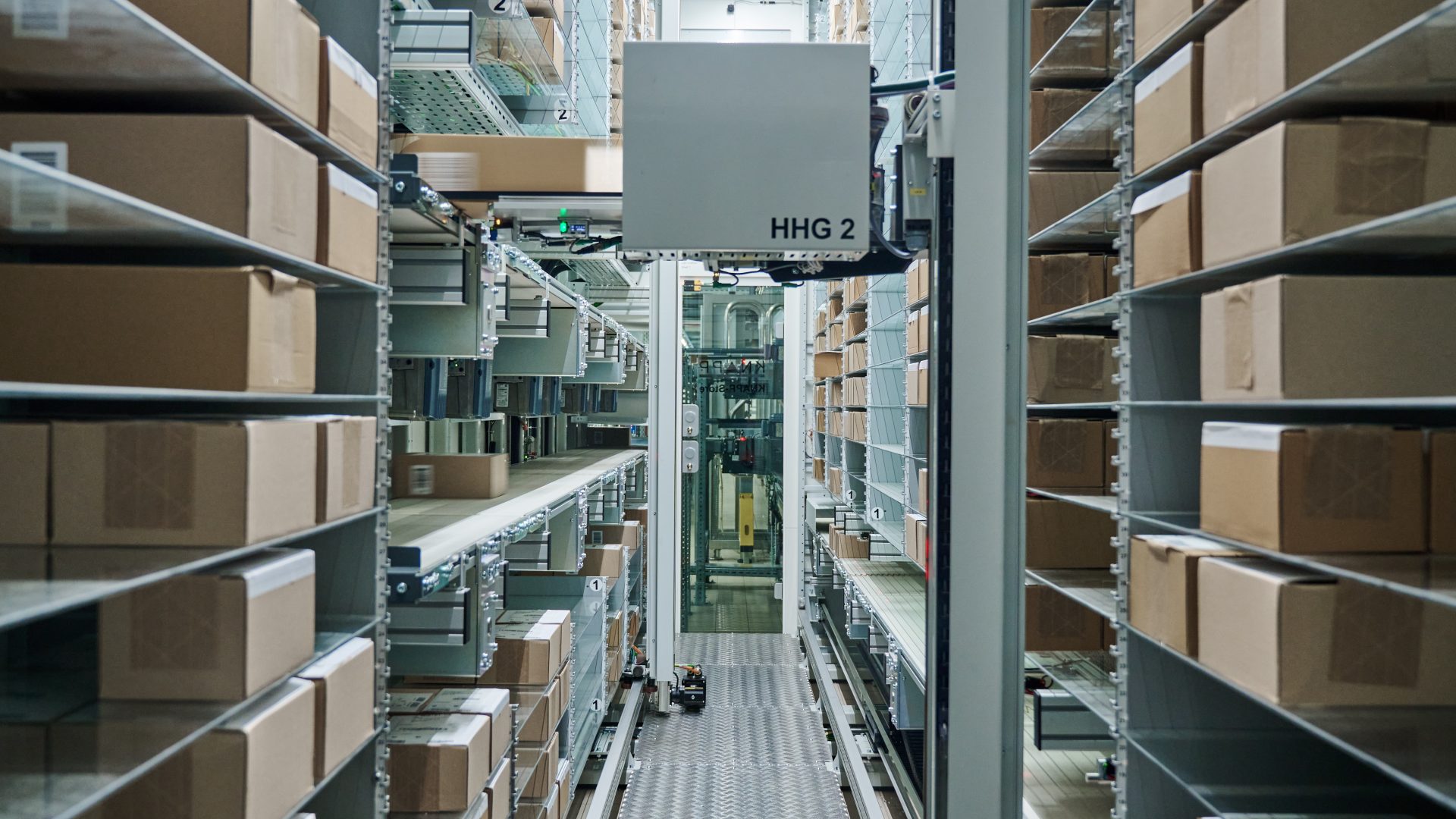
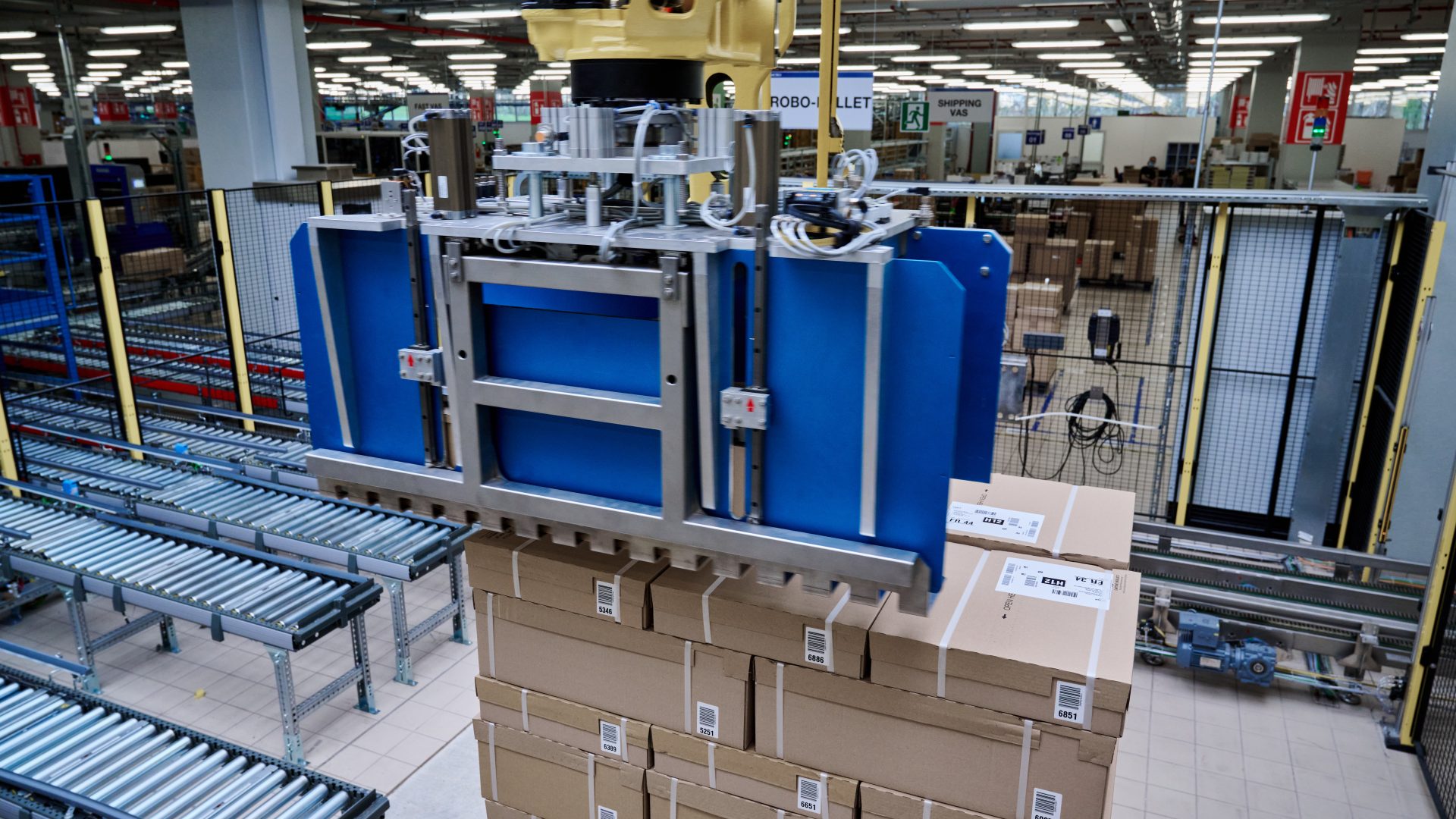
KNAPP’s KiSoft WMS controls the entire installation. What’s special about it is that we can adapt the software to our needs by changing individual modules. This allows us to control all processes ourselves.
Andrea Lombardo
Head of EMEA Logistics and Distribution
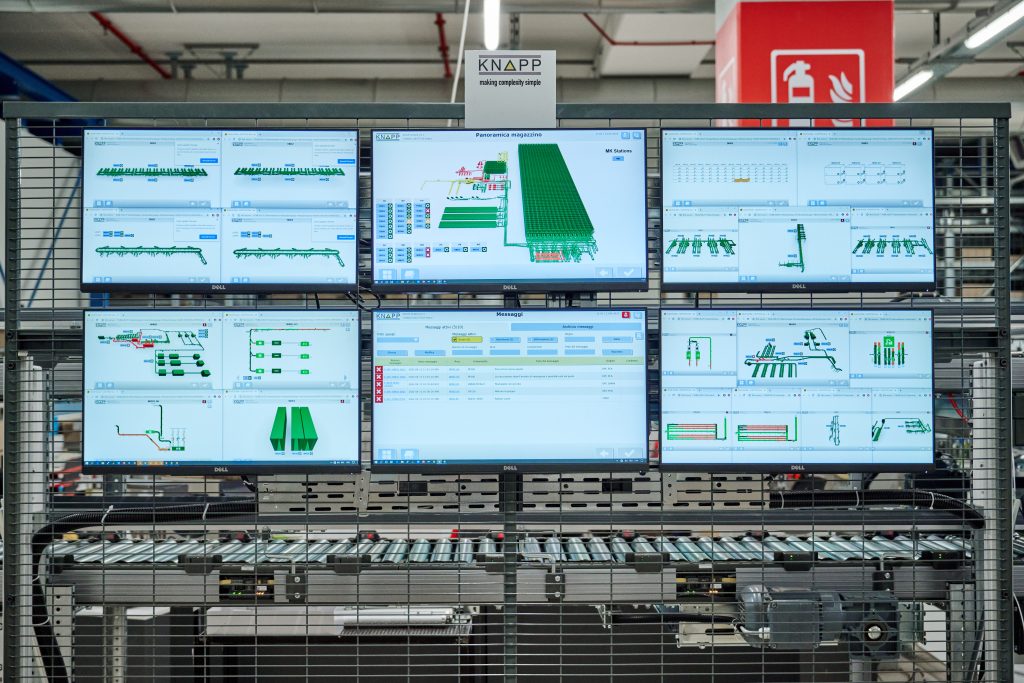
items per day
storage locations
shuttles
percent correct deliveries
square meters of storage space
order lines per hour
33,000 packages per day
With our KiSoft software, Luxottica is able to optimize their fulfillment processes and ship 33,000 packages a day. The powerful software encompassing warehouse management, warehouse control and machine control ensures maximum transparency and efficiency while offering flexibility and scalability according to the packages’ destination – whether a distribution center, store (B2B) or end customer (B2C). In a single shift of 7.5 hours, Luxottica’s DC processes 205,000 items. Thanks to continuous software updates and life cycle support, the solution stays future-proof and proves its worth as an investment over the long term.
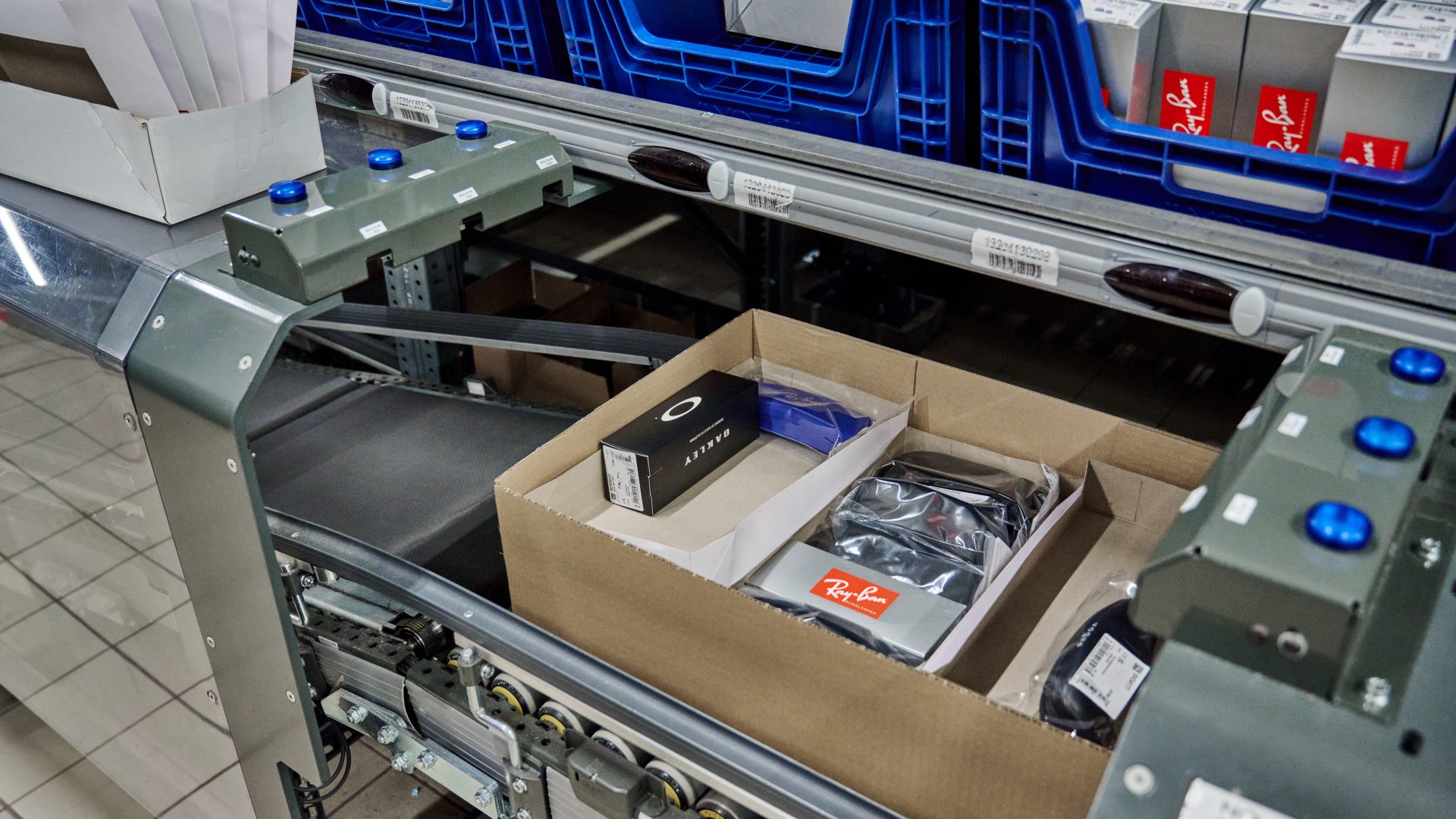
Joint success. Successful partnership.
Luxottica has been working together with KNAPP since 2006. “Our long-standing partnership was a major reason for us to implement the project in Sedico together with KNAPP,” explains Andrea Lombardo in an interview. Thanks to the strong foundation of trust between the two companies, they have always been able to find good solutions even in difficult times or when the issues at hand were complex. Patrick Tona, Project Manager at Luxottica focusing on logistics, also regards the collaboration with KNAPP as highly beneficial. For Luxottica, cutting-edge technology plays a vital role in improving their internal processes, which is why Mr. Tona sees opportunities for deepening the partnership with KNAPP in the future.