Pankl: End-to-End Quality Assurance in Assembly Thanks to Shuttle Storage System and Innovative Work Stations
Pankl Racing AG, headquartered in Austria, is part of the international KTM group and specializes in aerospace, racing and high performance components. Pankl High Performance Systems is a division of Pankl Racing AG and produces high-quality drivetrains for motorsports.
In 2016, a state-of-the-art production facility was built in Kapfenberg, Austria to manufacture the high-performance KTM drivetrains. All of the areas involved in value creation – from research and development to production and testing facilities – were brought together at this site to meet the daily challenges of motorsport applications with passion and enthusiasm. To automate the assembly area at their new site, Pankl chose a storage solution with innovative work stations for quality assurance during assembly.
You are currently viewing a placeholder content from YouTube. To access the actual content, click the button below. Please note that doing so will share data with third-party providers.
More InformationAutomation to implement zero-error strategy
The high demands for production performance meant that the entire value chain needed to be brought under one roof. Automation, therefore, was crucial for Pankl in order to meet their high production standards.
Pankl’s requirements for the solution
The KNAPP team understood what we needed very quickly and the automated storage system is growing along with our production numbers. KNAPP also developed customized assembly work stations. The system integrates seamlessly into our concept of a fully personalized and traceable production process.
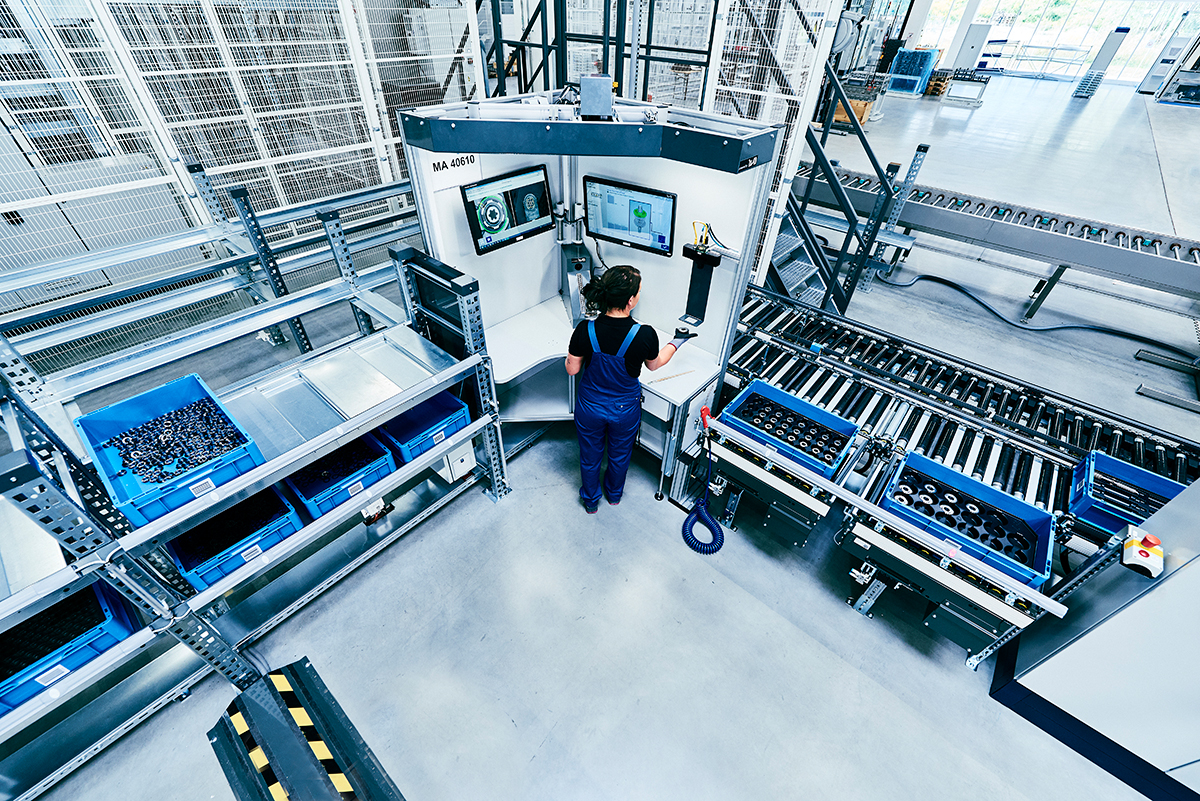
Automated small parts warehouse and innovative work stations
The combination of an automated small parts warehouse and innovative vision smartdesk work stations ensure that assembly is error-free and is optimally supplied with the required parts.
The 3D-capable shuttle system stores all parts needed to assemble the drivetrains. With 12 different drivetrains, there is an enormous number of parts that all have to be provided to the vision smartdesks in just the right sequence.
Innovative image processing technology accompanies employees through the assembly process and provides them with feedback on each individual work step in real time.
Quality control thanks to end-to-end software-guided assembly
The vision smartdesk is equipped with a real-time feedback system that monitors drivetrain assembly in order to ensure zero errors and end-to-end traceability in the assembly process. In accordance with our zero-defect philosophy, the vision smartdesk image recognition and processing system records each component used in assembly and verifies each work step in real time.
Next to the vision smartdesk are six Pick-to-Light storage locations, which provide common parts, such as plain washers and retaining rings. On the other side of the work station, a conveyor supplies shafts and toothed wheels in just the right sequence.
The monitors at the work station display an exploded view of the drivetrain in question (showing how it is supposed to look) next to a camera image (how it actually looks). The different drivetrain parts now need to be assembled in real life so that the camera image matches the ideal image.
As soon as the assembly process is completed, the employee presses a button to begin the final check by the feedback system. The result of the check is shown on the monitor. Green means everything is correct, while red means that there is an error. Possible errors are displayed on the monitor so they can be corrected immediately.
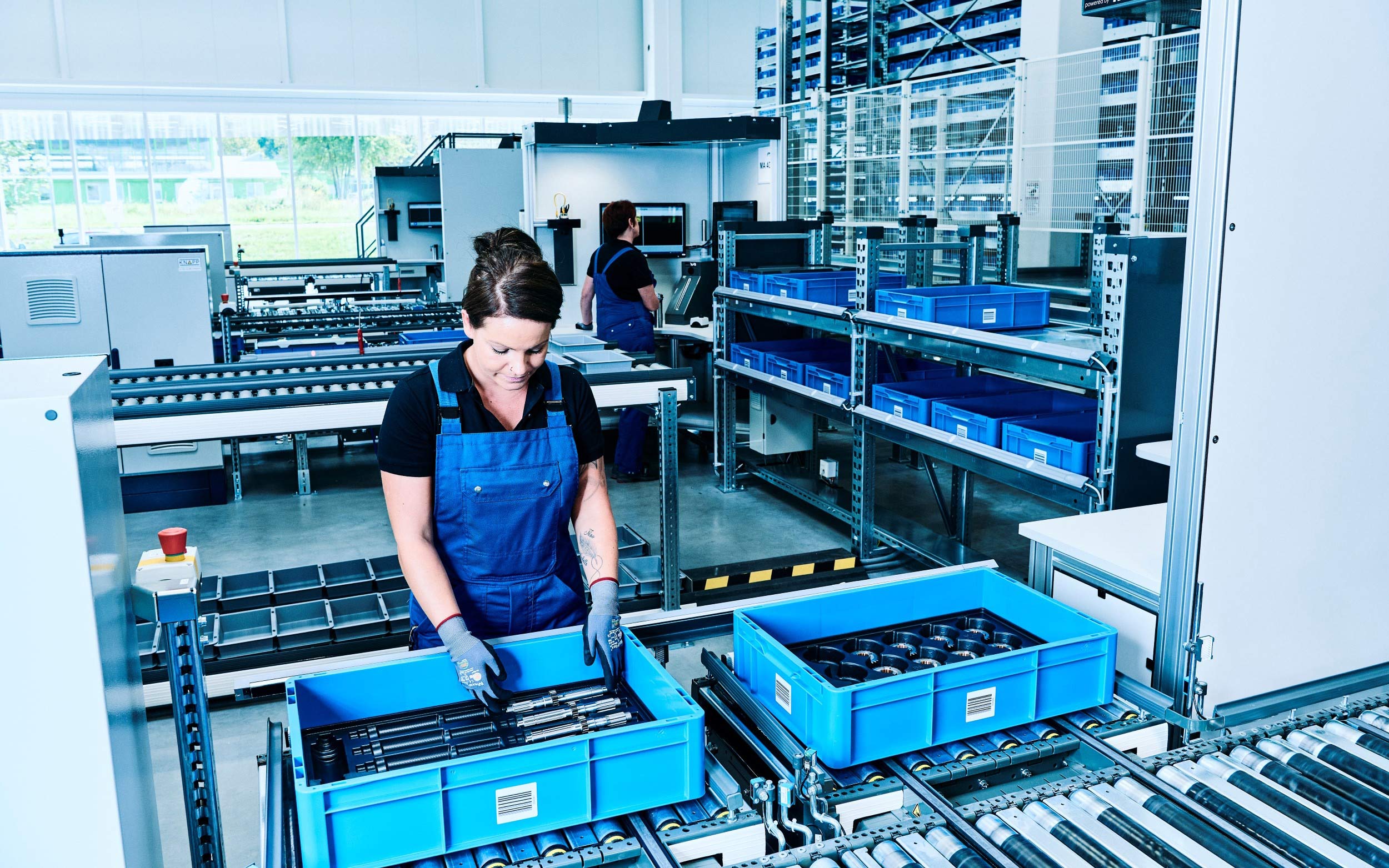
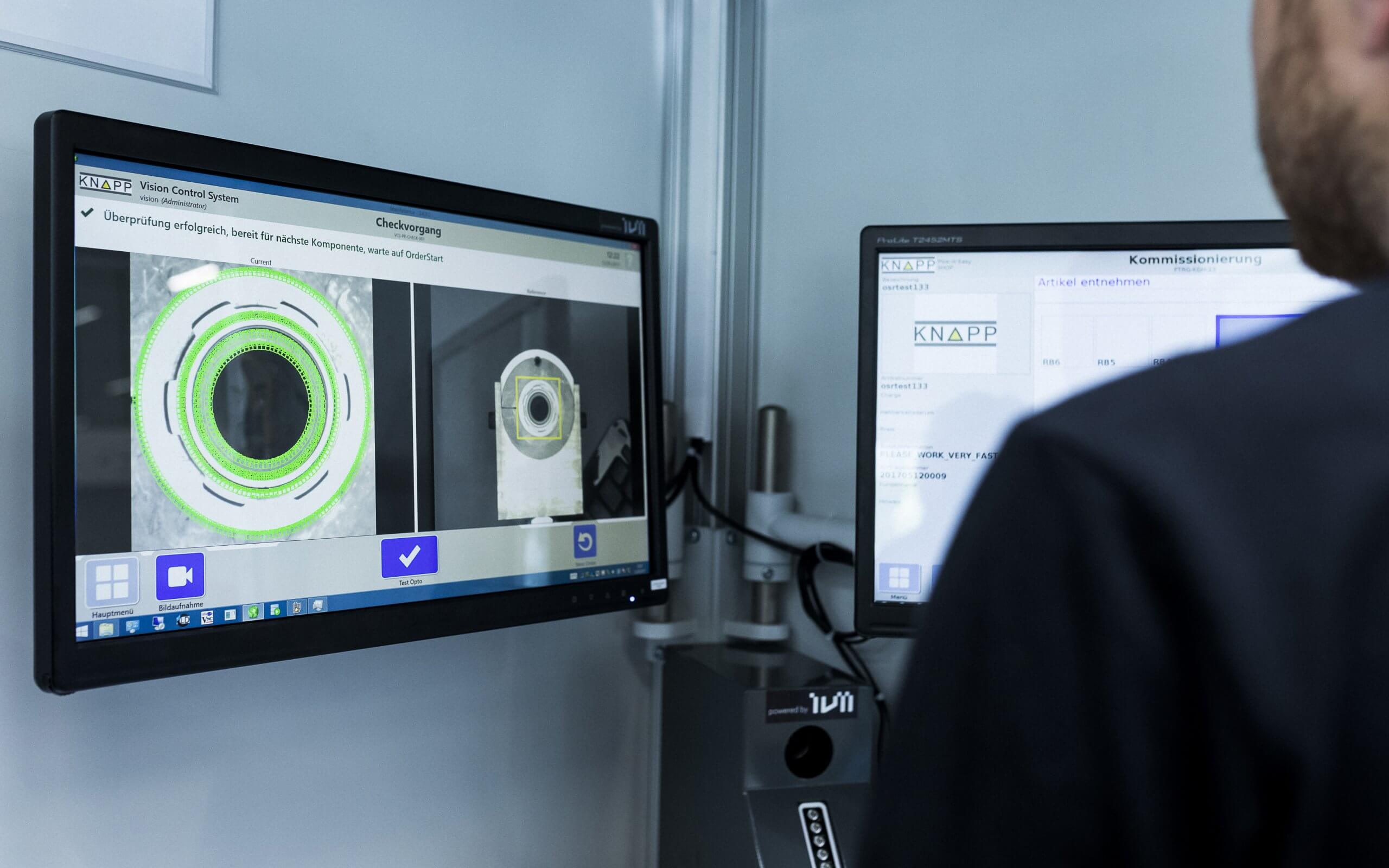
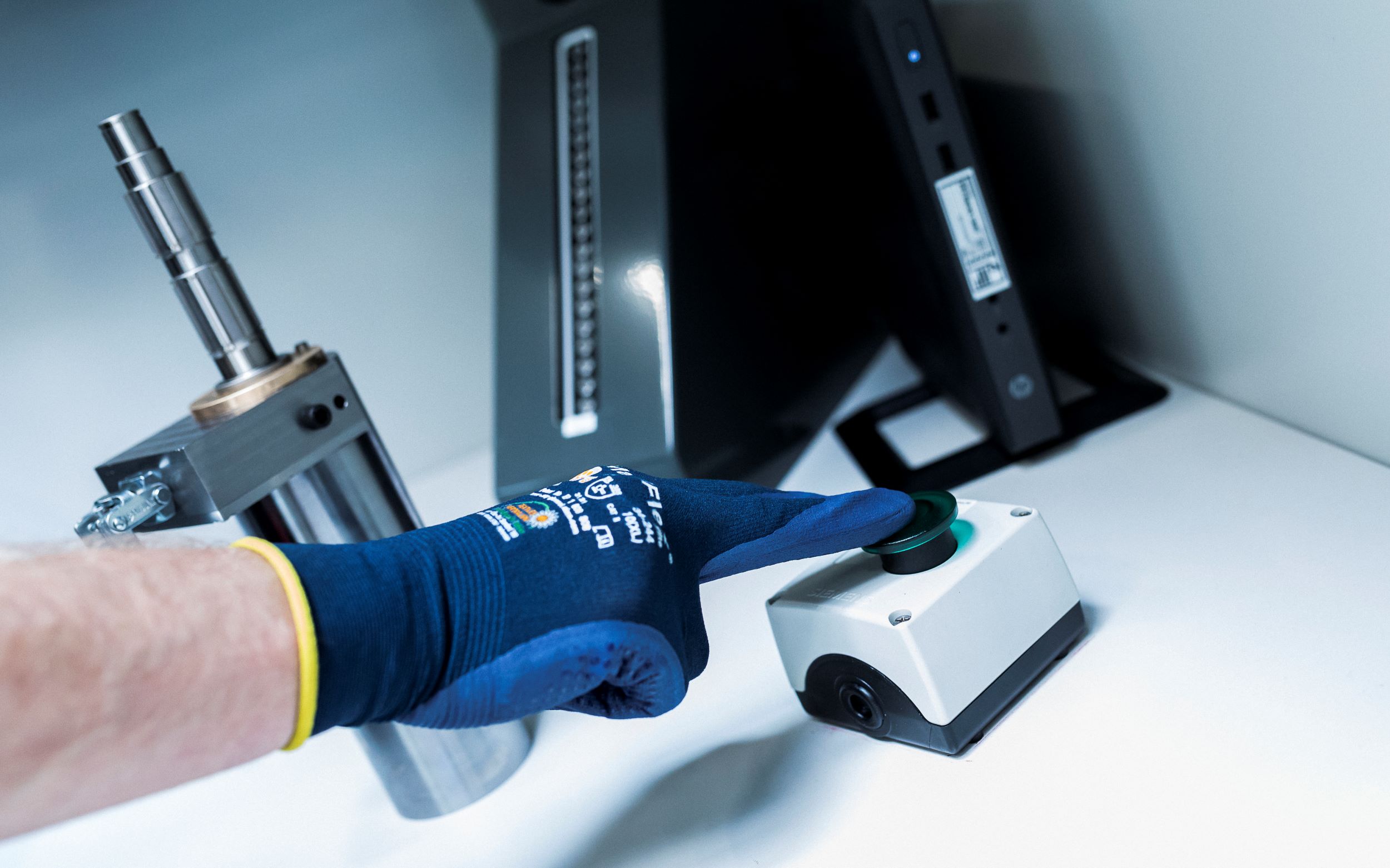
Using the vision smartdesk is tremendously motivating for our personnel. Interacting with the system is almost like playing a game. Our employees don’t view the feedback system as surveillance, but see it as welcome support for achieving the best possible quality in their work in the quickest possible time in order to achieve our goals.