Terberg: Shuttle Storage System Forms High-Efficiency Solution for Production Supply
Terberg Benschop is a specialist in the manufacture of terminal, RORO and shipyard tractors and similar vehicles. The family-run company operates in more than 100 countries worldwide, and as a trendsetter in a niche market, focuses on development and innovation. To be able to process a greater number of orders with more efficiency and flexibility, Terberg installed a shuttle storage system.
The new solution automatically supplies the work stations and production lines. The system was implemented during ongoing operation and forms a solid foundation for the company’s future growth.
25,000 storage locations
You are currently viewing a placeholder content from YouTube. To access the actual content, click the button below. Please note that doing so will share data with third-party providers.
More InformationAutomated small parts warehouse creates more storage capacity
In order to process the increasing number of orders efficiently and flexibly, Terberg needed to centralize the production warehouse so that bodywork construction, the line supply for vehicle assembly and the global spare parts warehouse were all together in a new building. The small parts stored in the existing high-bay racking system for pallets needed to move to a new automated small parts warehouse to make room for large parts. And this all had to take place during ongoing operation, without interrupting production. Terberg opted for a shuttle storage system combined with ergonomic work stations equipped with a Pick-to-Light system.
Terberg’s requirements for the solution
For Terberg, opting for an automated solution was a major step. It was especially important for us to work with a supplier who has successfully implemented their systems around the globe and who also offers local support and servicing.
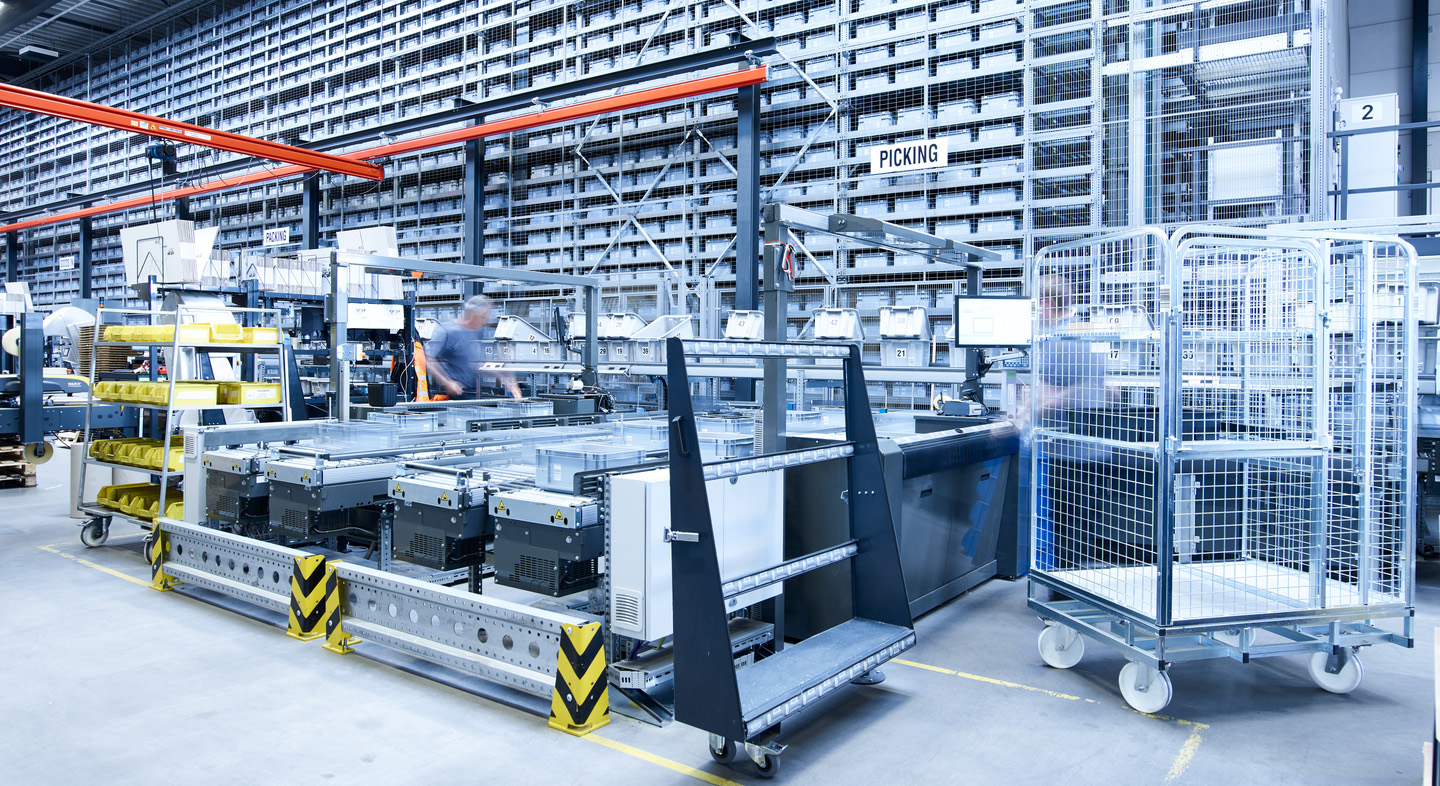
OSR Shuttle for maximal efficiency and flexibility
Terberg implemented a flexible, automated solution that provided the highest availability in their vehicle production and that could be expanded to handle growth in the future. The heart of the solution is KNAPP’s OSR Shuttle, a shuttle storage system that efficiently executes many different types of logistical tasks.
As an AS/RS, this system connects directly with goods-in, shipping and quality control. At the work stations, individual items are added to the system, a task carried out at an ergonomic height. The picking area consists of two multifunctional Pick-it-Easy work stations, where items are picked to fill kanban racks and roll containers. Spare parts are picked here as well. Behind the scenes, the software solution KiSoft One with a web service interface to the customer’s system keeps processes running smoothly.
A glimpse inside the Terberg solution
The new automation solution has been operating at Terberg Benschop since 2019, with capacity and performance ensured until 2027. The pivotal factor is a scalable, flexible system that supplies the work stations and production lines fully automatically.
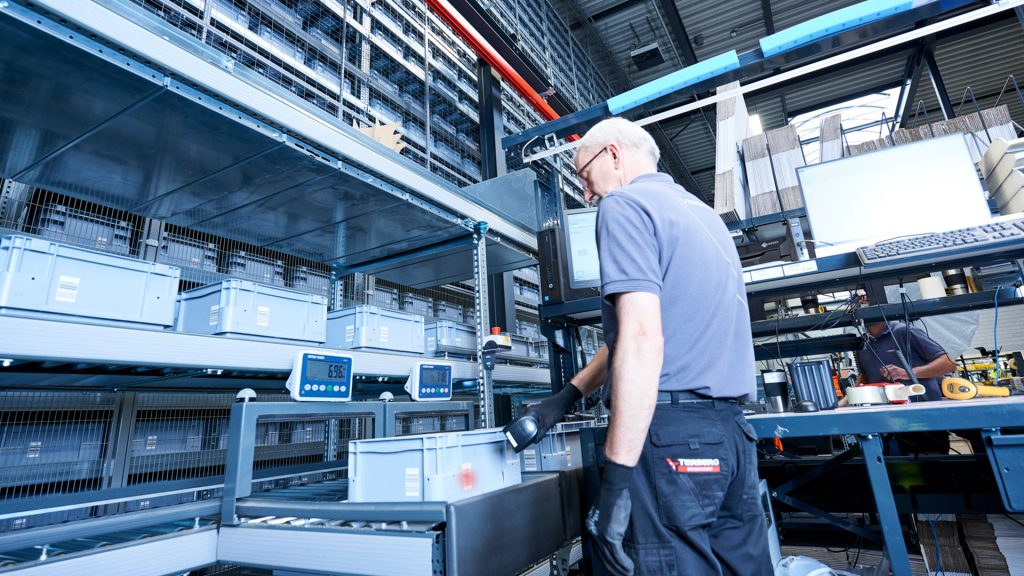
1 I Goods-in
Prior to storage in the OSR Shuttle, the goods are repacked at decanting work stations. The employees identify the individual items in the customer system, sending advance information to the KiSoft software. Depending on the size of the items, two sizes of storage containers are available. To keep the picking process efficient, KiSoft indicates the suitable container size to the employee at the station. The decanting stations are equipped with check scales to ensure that the containers do not exceed the maximum permissible weight of 50 kg (110 lb) per container. The storage process verifies that the maximum load per channel is not exceeded and follows an ABC storage strategy.
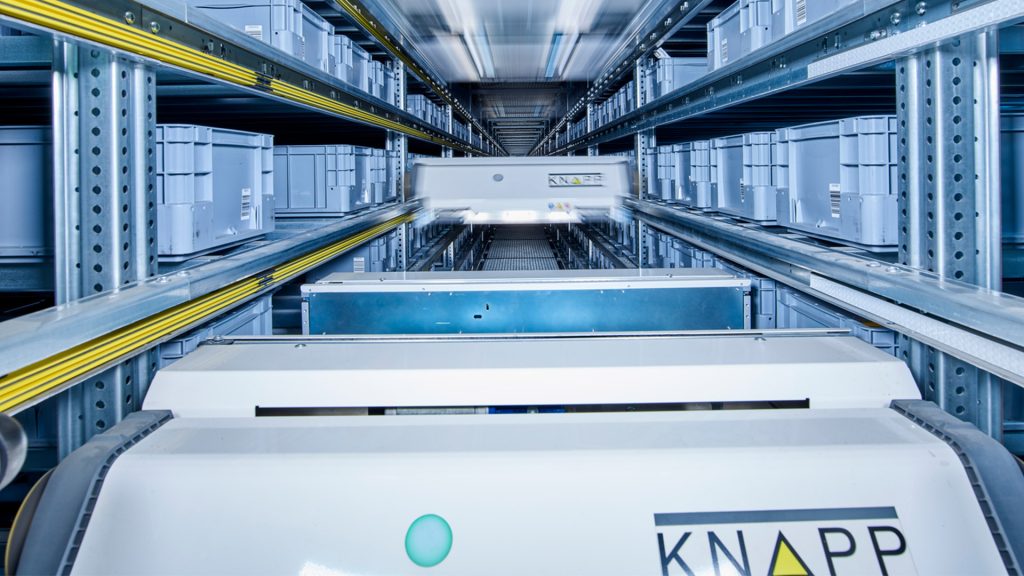
2 I Order start and storage
Terberg’s customer system prioritizes and sorts the orders before forwarding them to KiSoft. This way, orders for spare parts with an earlier shipping date can be prioritized and processed rapidly. All small parts are stored in the OSR Shuttle and are retrieved when required at the production lines or for shipping as spare parts. Thanks to dynamic quadruple-deep storage, the system has a storage capacity of 14,250 locations for containers measuring 600*400 mm (24*16 in) or 28,500 locations for containers measuring 400*300 mm (16*12 in).
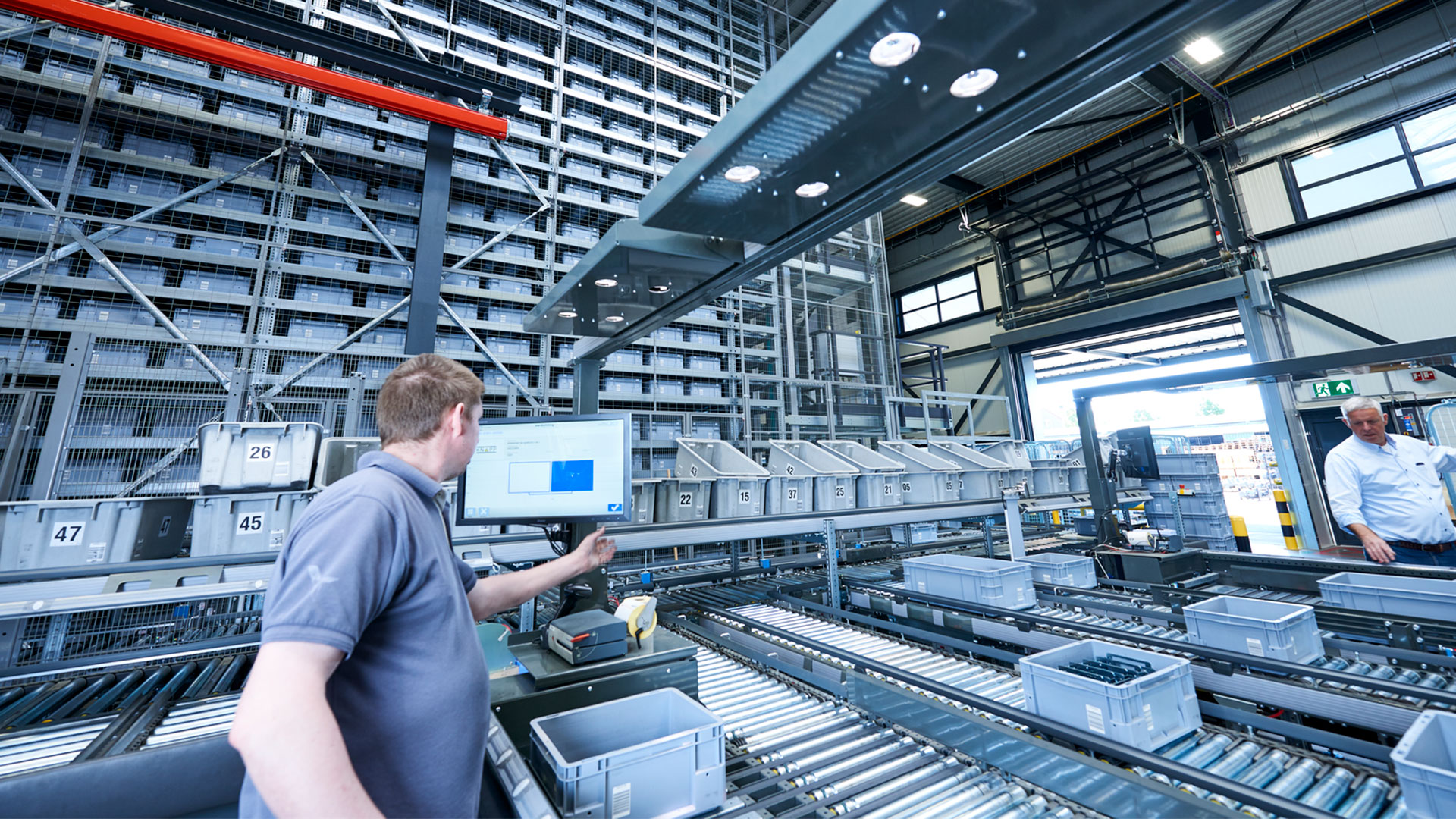
3 I Goods-to-person picking
The picking area includes two Pick-it-Easy work stations for goods-to-person picking. The containers with the required parts are retrieved from the OSR Shuttle and are supplied to the work stations at an ergonomic height. A Pick-to-Light system assists the employees with picking. Three types of picking are carried out at the work stations: picking to kanban racks, to roll containers and spare parts picking.
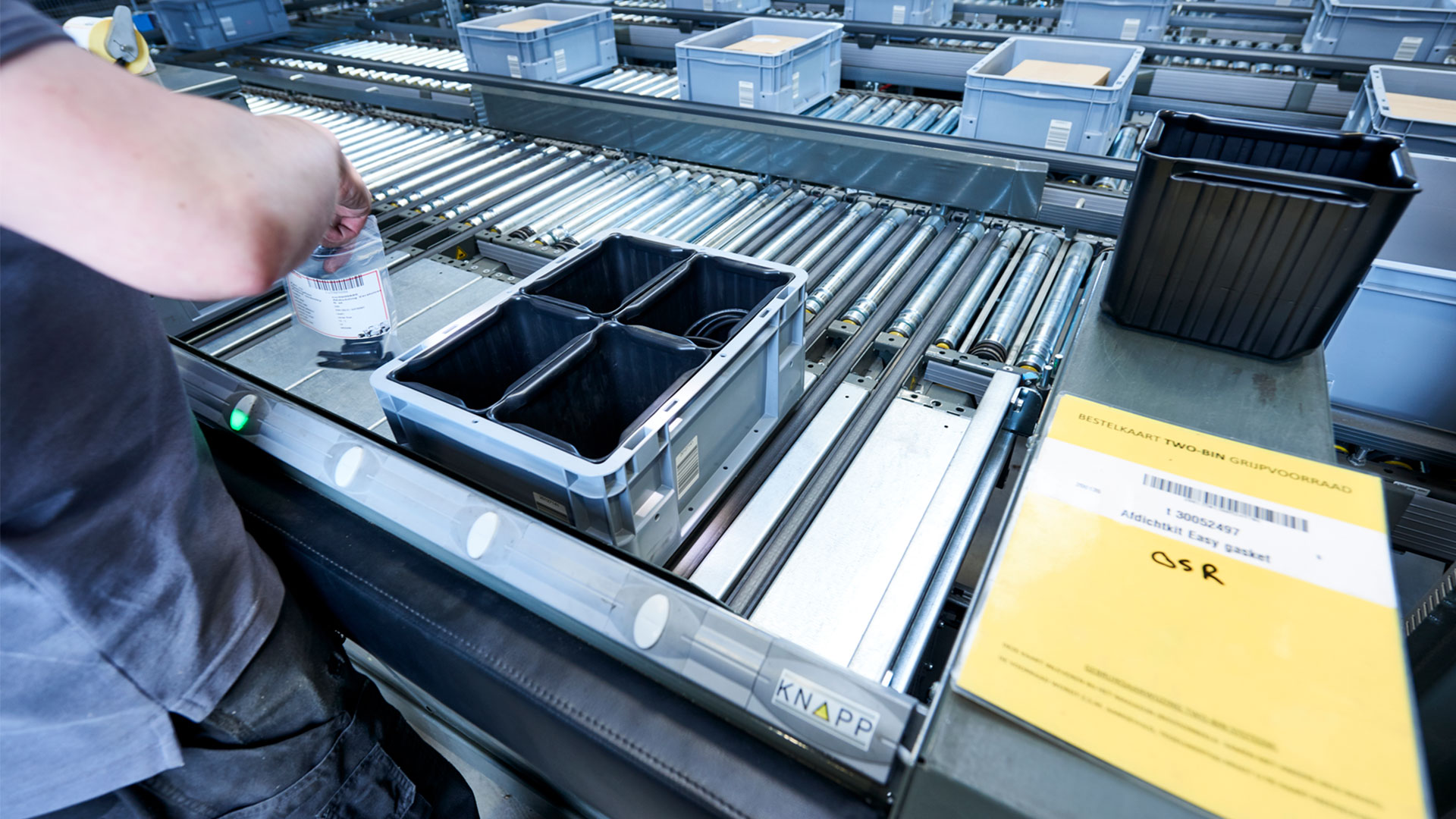
4 I Spare parts picking
Here, spare parts are picked that will be shipped directly to customers. The Pick-to-Light displays inform the employee which items and how many of each item they should remove from the source containers. After the picking order is completed, an address label is printed and applied to the container. The containers are then automatically conveyed to the shipping area. The source containers are automatically weighed before storage and are then stored in the OSR Shuttle with the updated weight.
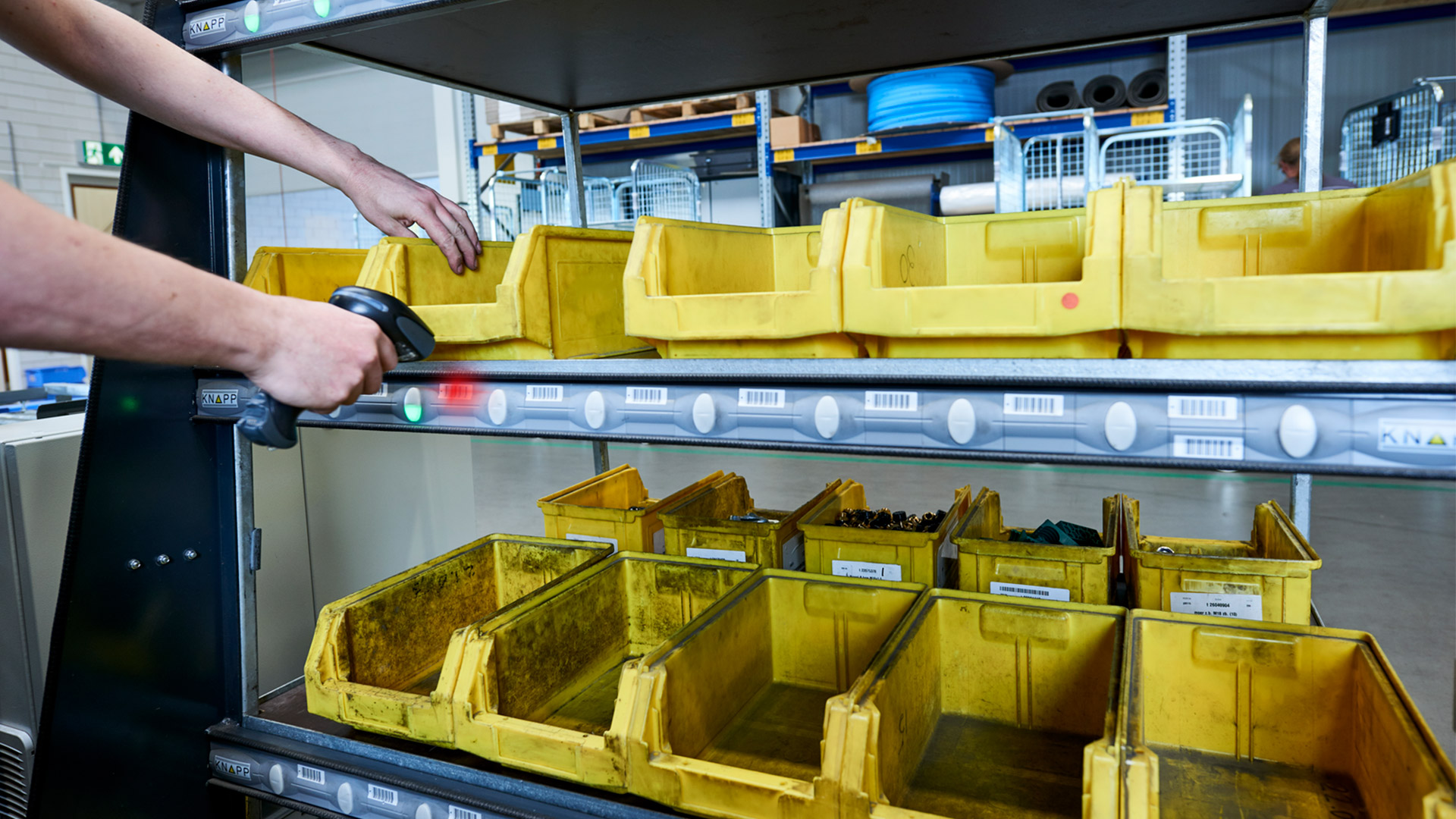
5 I Picking into kanban racks
There is a special picking mode for filling kanban racks, which are required for assembly and production. The kanban rack is positioned behind a special frame with Pick-to-Light displays. The Pick-to-Light displays guide the employee through the picking process. When all orders on one side of the rack have been processed, the employee turns the rack and fills the other side of the kanban rack as required. After the kanban rack has been filled, the rack is transported back to the assembly and production line.
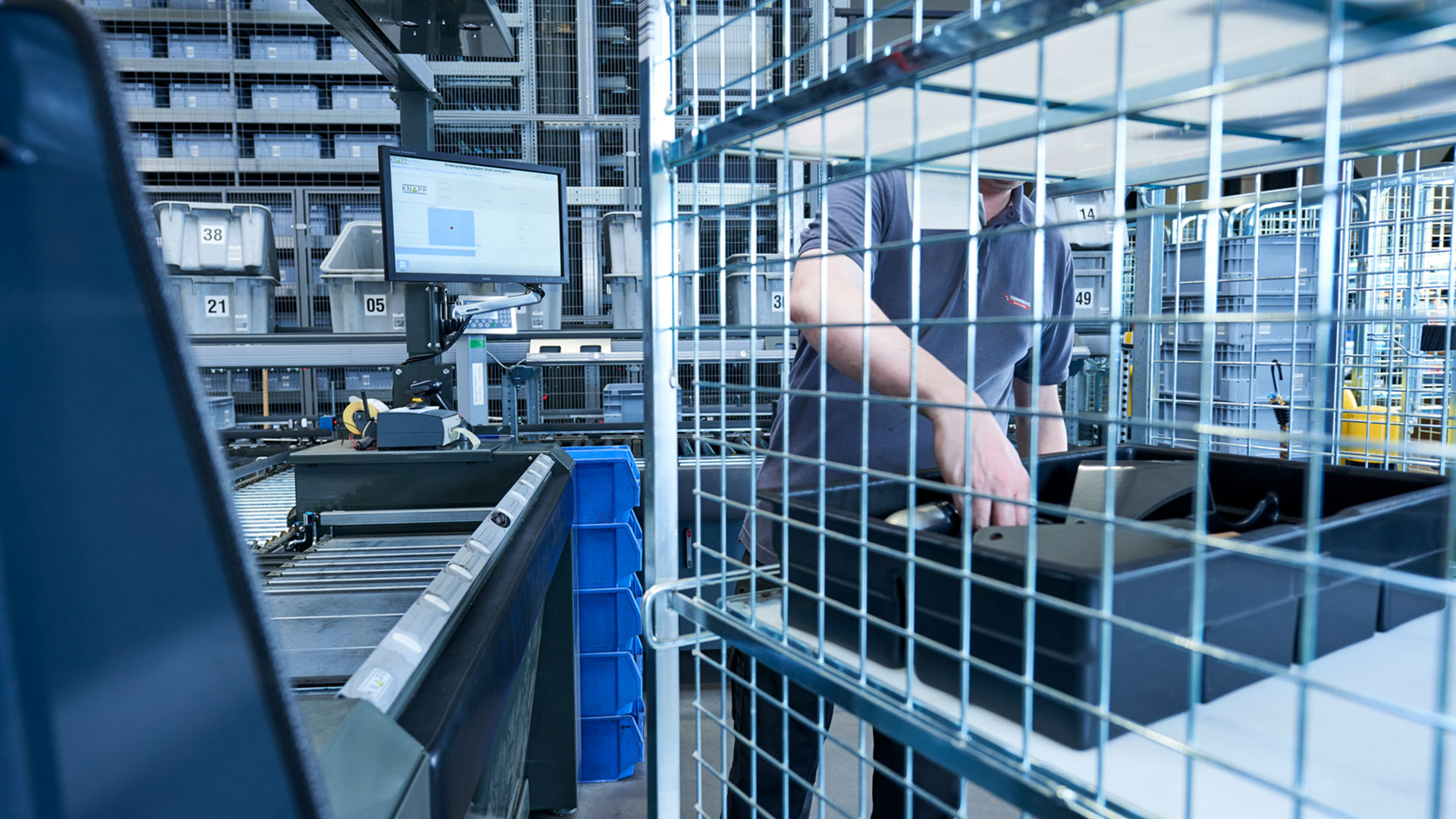
6 I Picking into roll containers
Items that are required at the assembly and production lines are picked into roll containers manually. Employees then take the roll containers to other warehouse areas where large items are added or bring them directly to the assembly and production lines.
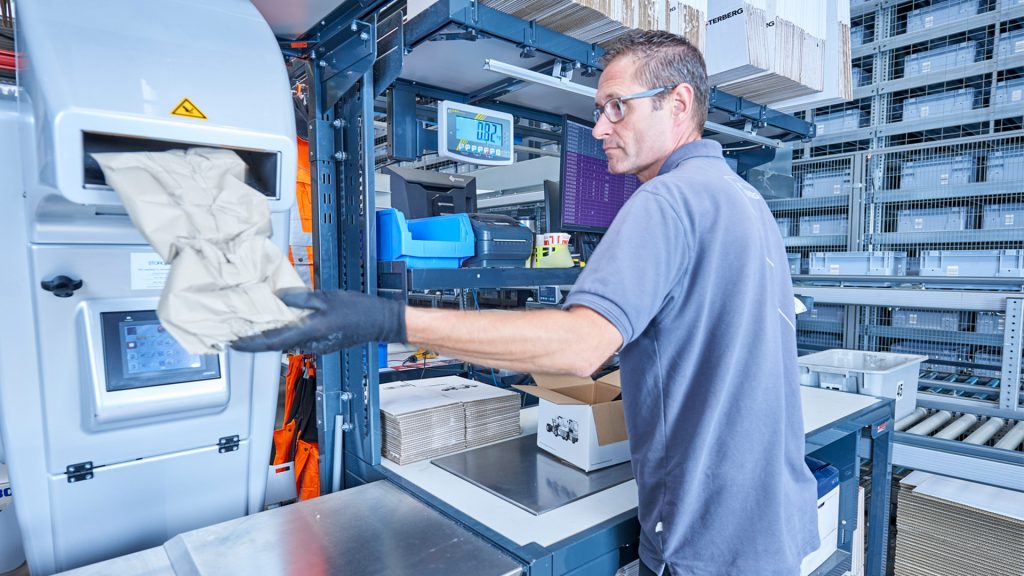
7 I Shipping of spare parts
As soon as the spare parts have been picked, the spare parts orders are conveyed to the packing area. Here, small parts from the OSR Shuttle are merged with larger parts from the high-bay racking and are prepared for shipping. Two shipping work stations with packing machines are available for this purpose. The packed parts are placed on a pallet, which a forklift manually transports to the truck.
Of course the goods-to-person system means a much higher capacity since walking times are eliminated. Other advantages include the Pick-to-Light system, which supports employees as they work, reducing picking errors and quantity errors. The FIFO principle can also be easily implemented since incoming goods are always stored in a new, empty container.
How Terberg benefits from a shuttle storage system
Simple and flexible
The new solution, a combination of an automated small parts warehouse and ergonomic work stations, allows the company to efficiently process their rising number of orders. Employees can flexibly change from one type of picking to another at the multifunctional Pick-it-Easy work stations. A Pick-to-Light system in combination with the easyUse software interfaces give the employees the support needed for top performance.
Expandable
The OSR Shuttle is perfect for high-performance applications and can easily accommodate future growth. The system is freely scalable in terms of size, performance and function. Work stations can also be added as needed. The solution grows along with demand.
Customized
Based on Terberg’s requirements, a customized solution was implemented that enables the company to achieve maximum availability in the production of its vehicles. This also includes providing consolidated parts to production in sequence, the option of picking into kanban racks and a storage space optimization solution specially developed for the customer.