Warehouse Automation for Manufacturing
Warehouse automation is the key to more competitiveness in manufacturing because the production of the future is intelligent, flexible and interconnected. Our efficient solutions optimize your production supply and internal transport processes.
Intelligent production logistics for increased performance
An intelligent production logistics system, finely tuned, plays a central role in keeping manufacturers competitive when contending with the sector’s typical challenges. New approaches are required to succeed in the face of changing environmental and market conditions, skilled labor shortages, a lack of space and ever-increasing complexity. Here, warehouse automation is the key to increasing your company’s performance.
Looking for dynamic, highly interconnected systems with security of investment and maximum flexibility as requirements change? Our warehouse automation solutions are ready to boost quality, profitability, efficiency and ergonomics in your company’s operations. With new approaches and a mix of innovative and proven technologies, we are opening up new opportunities for the manufacturing sector. Our mission:
Understanding your business so our solutions provide the added plus in flexibility to your processes.
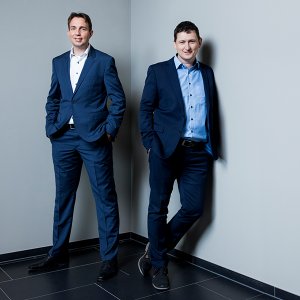
Do you have any questions? We are always glad to help you!
Stefan Lechner & Christian Brauneis
Vice Presidents Business Unit Industry
Email: kin.sales@knapp.com
“Process reliability is crucial for production, which is at the heart of every company, so we see it as our mission to develop the best possible solutions using our expertise. By using innovative technologies and intelligent software, processes are interconnected, optimally meshing and designed for high adaptability. With our all-in-one solutions, we make smart production a reality.“
Christian Brauneis
Vice President Business Unit Industry
Are you interested in automating your company’s warehouse?
Find out more about our solutions and customer references!
Solutions for warehouse automation in manufacturing
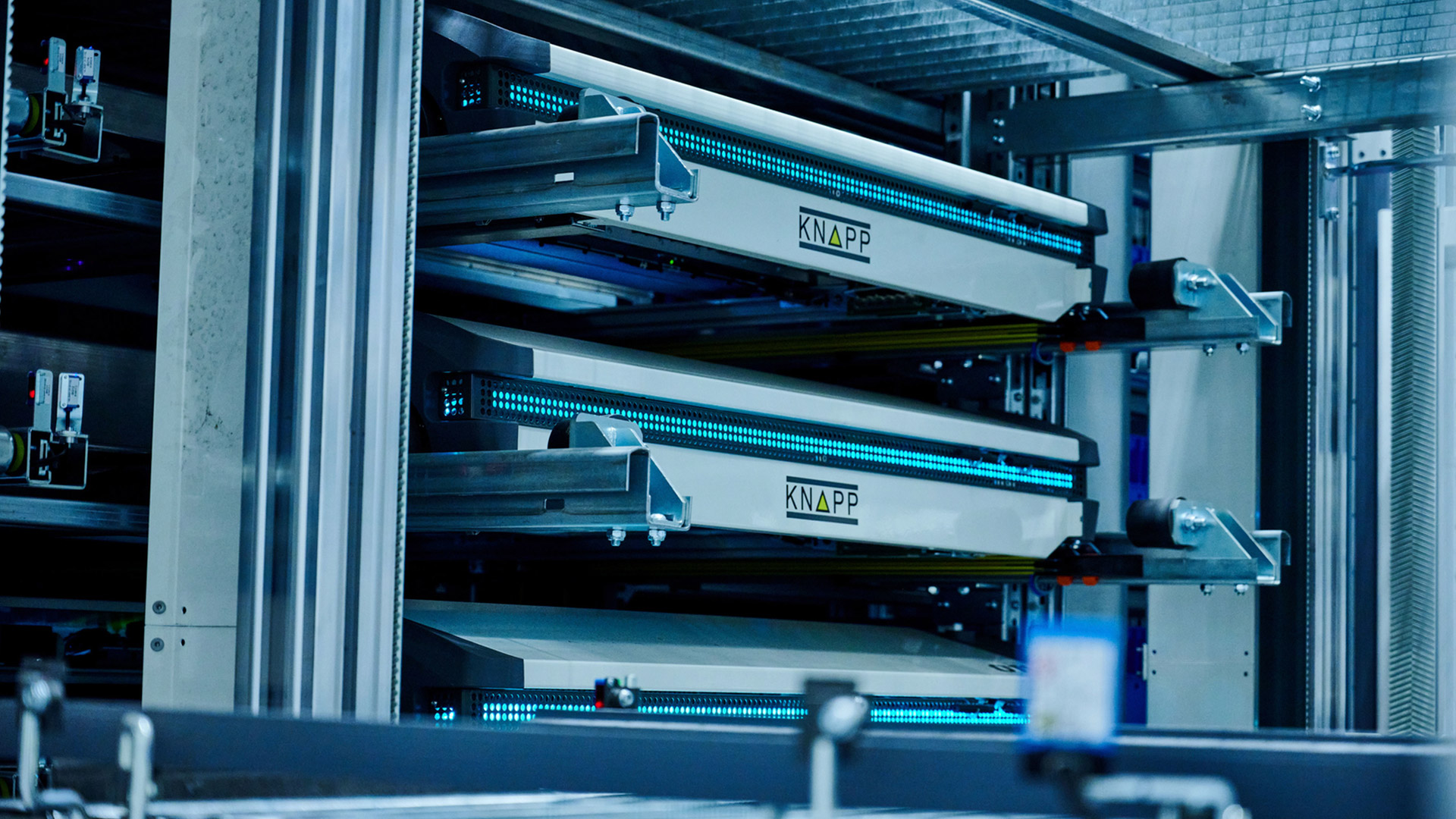
Automated storage systems for efficient production processes
Whether automated small parts warehouses, stacker cranes or buffer towers, we have the optimal logistics solution for every requirement. Our storage systems support processes such as picking, buffering, sequencing of both goods and orders as well as supplying work stations. Find out more about our smart solutions:
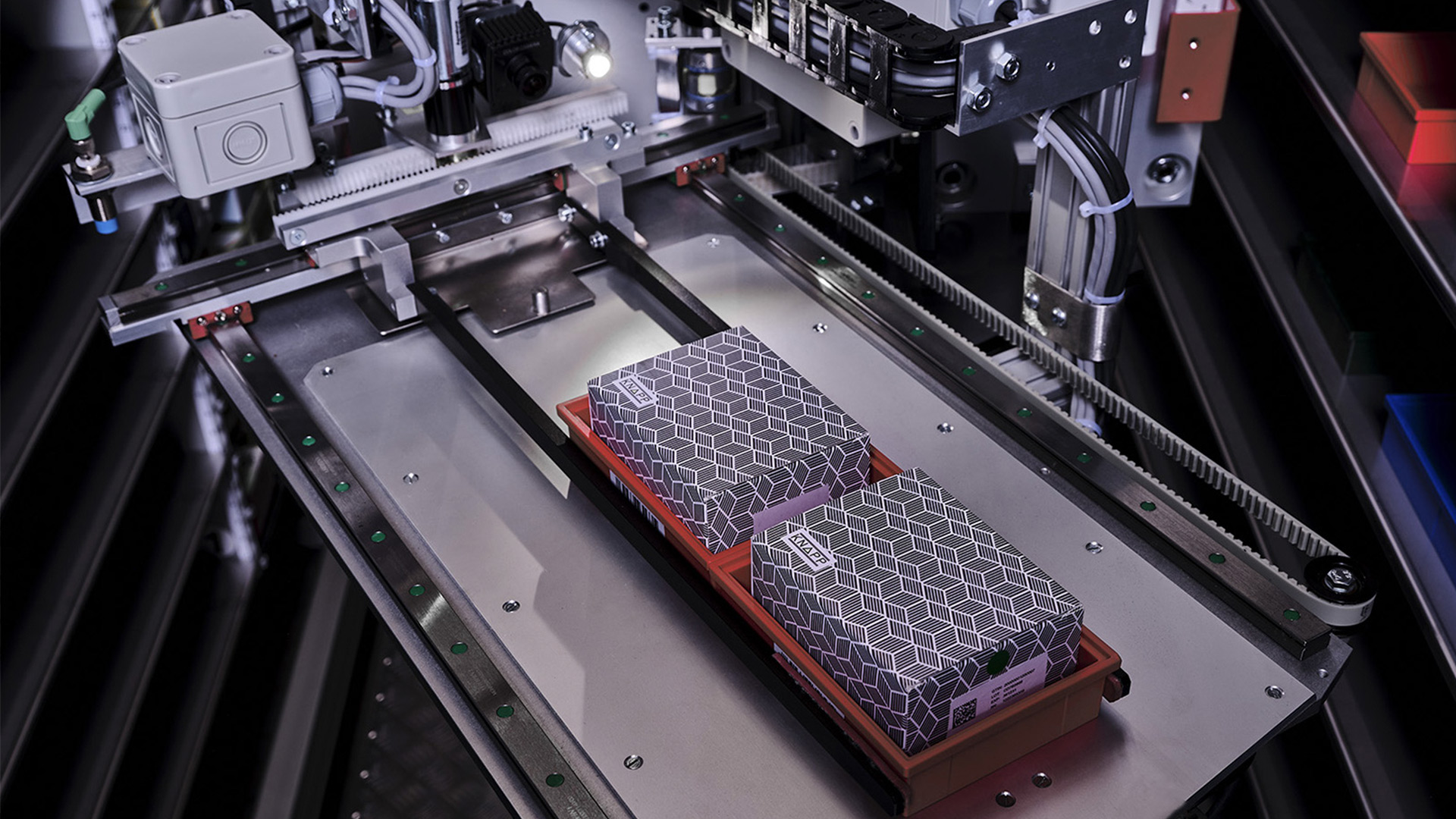
Automated storage and picking system for higher performance
The automated storage and picking system InduStore is an ideal solution for industrial applications, especially for stockpiling individual items, supplying production or storing spare parts. Discover more about the system:
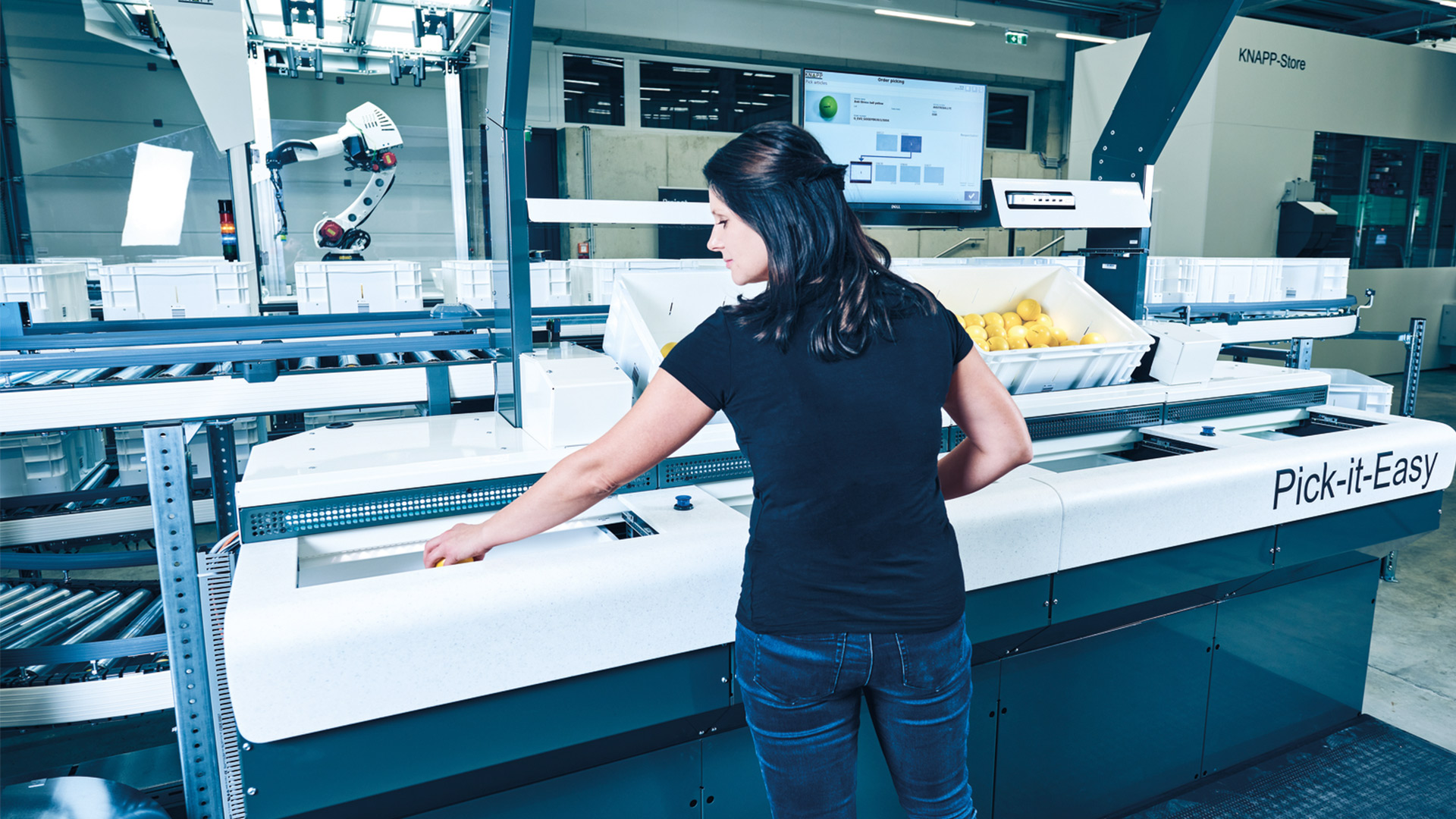
Ergonomic, intelligent work stations
Our work stations combine ergonomics, efficiency and quality. They utilize the goods-to-person principle, which means optimal order processing and satisfied employees. Work stations combined with an intelligent camera system ensure end-to-end quality control. Find out more about our products:
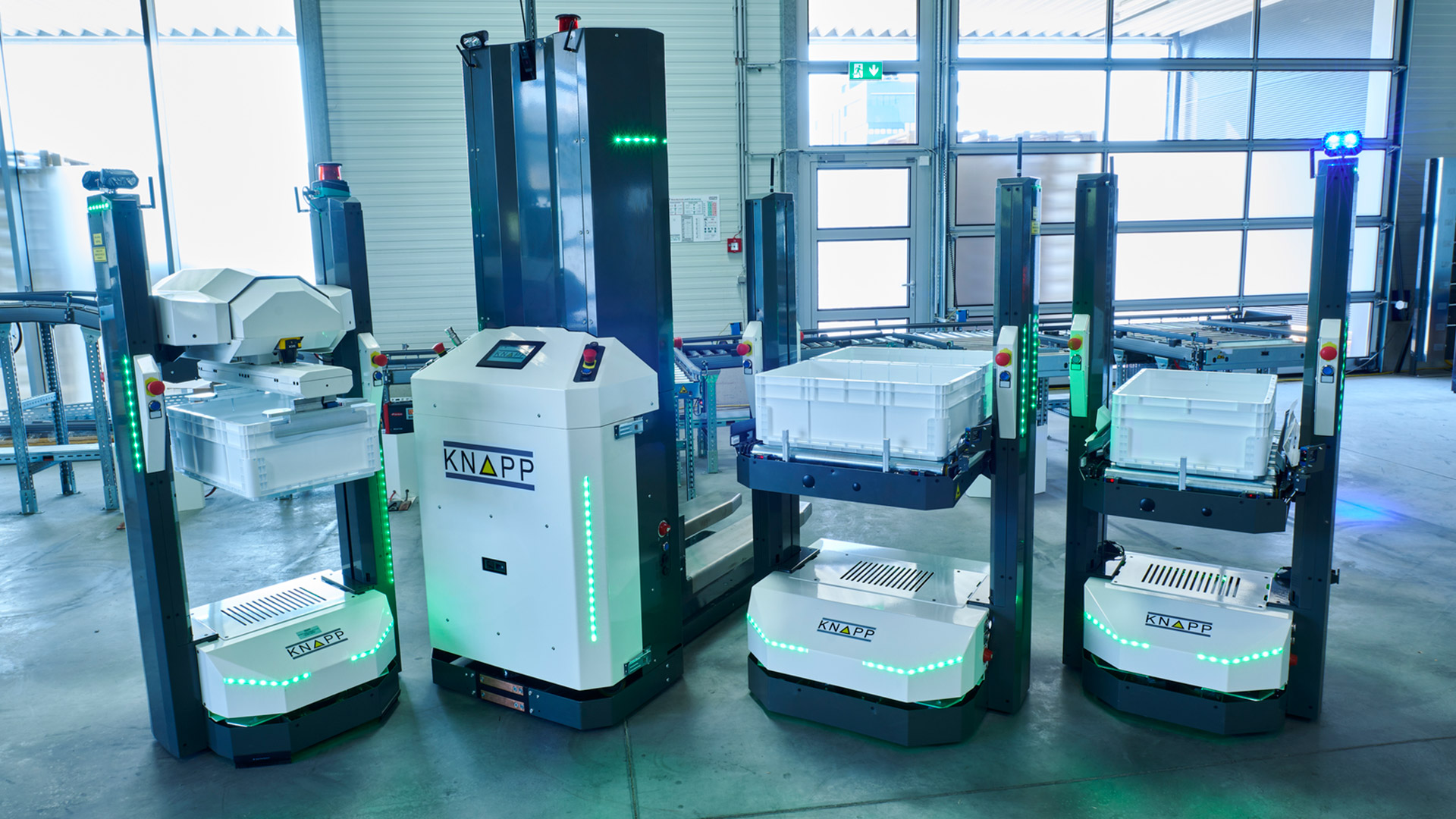
Automated mobile robots for increased flexibility
Our intelligent automated mobile robots allow you to design your logistics processes flexibly. They automate internal transport and efficiently connect different production areas.
Find out more about our autonomous mobile robots (AMRs):
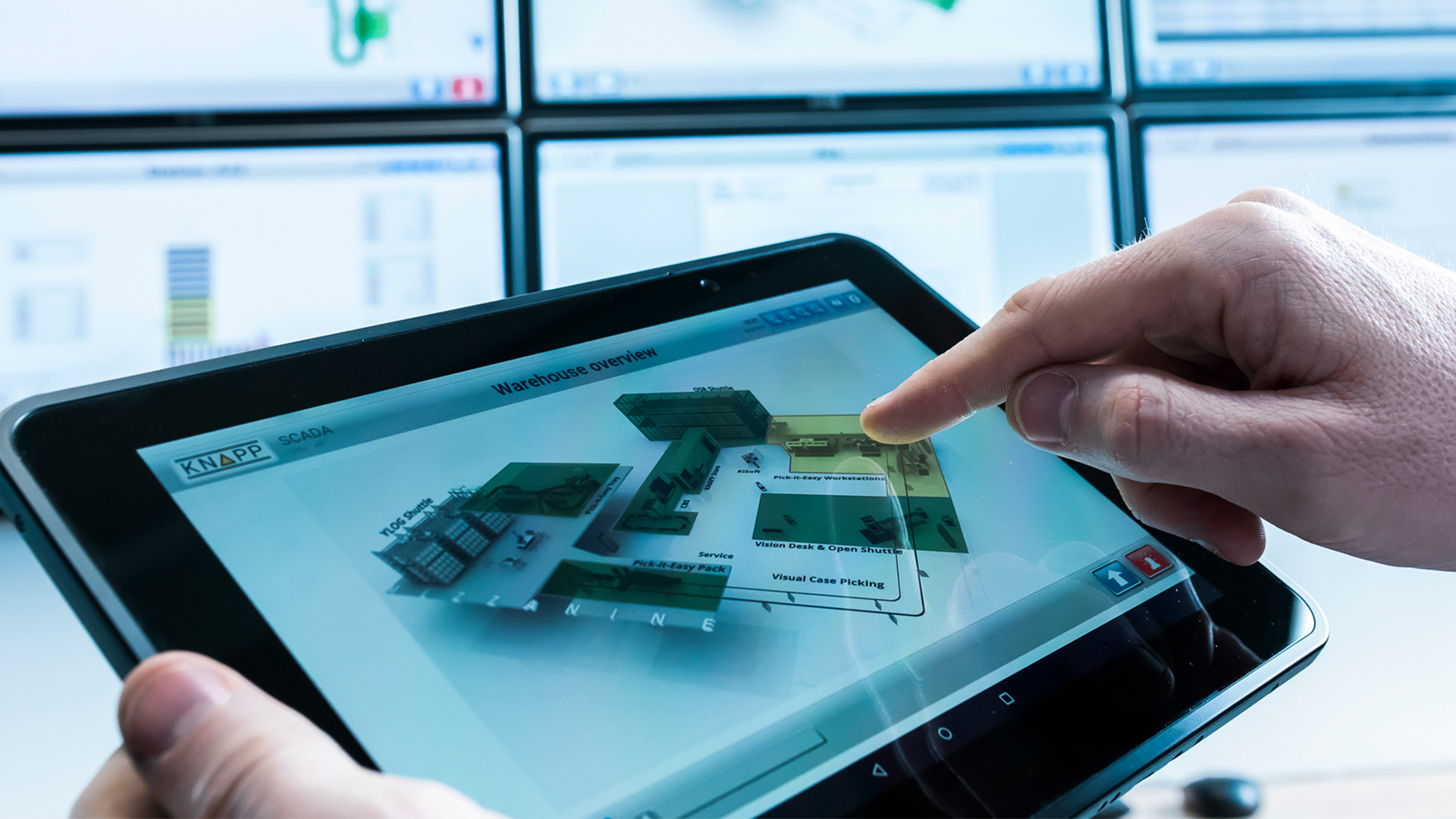
Software for warehouse automation
The heart of any warehouse automation is its software. As a value chain tech partner, we offer all-in-one software solutions, intelligent fleet control software, resource planning software and much more. We cover processes with our KiSoft and SAP® EWM by KNAPP product lines as needed.
Learn more about our comprehensive software solutions:
The gains for production logistics
Automating production logistics offers manufacturers many advantages:
References:
Our solutions for warehouse automation in manufacturing
Companies around the globe depend on collaboration with KNAPP. We help you optimize your production processes, storage space and in-house transport. Our solutions speak for themselves:
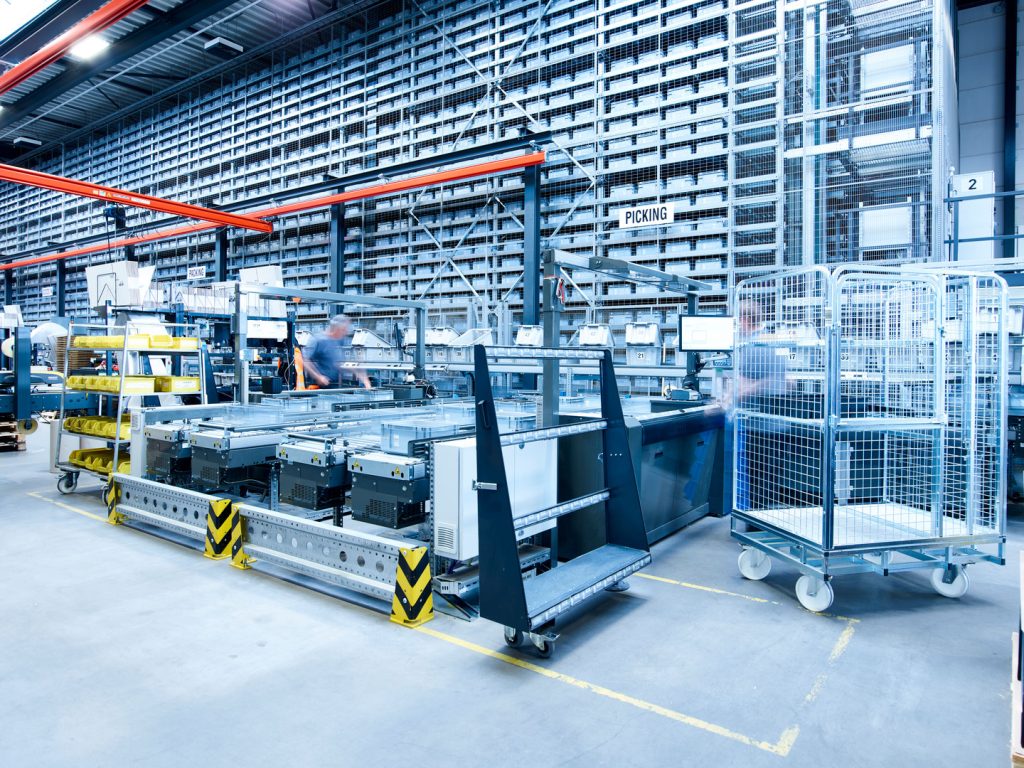
Terberg Benschop B.V.: New solution creates basis for future company growth
To handle the increasing number of orders, several processes at Terberg Benschop B.V. were centralized in one automated storage system. Picking orders are fulfilled for manufacturing, the assembly line, or for the shipping of spare parts. Supply is as needed and just in time.
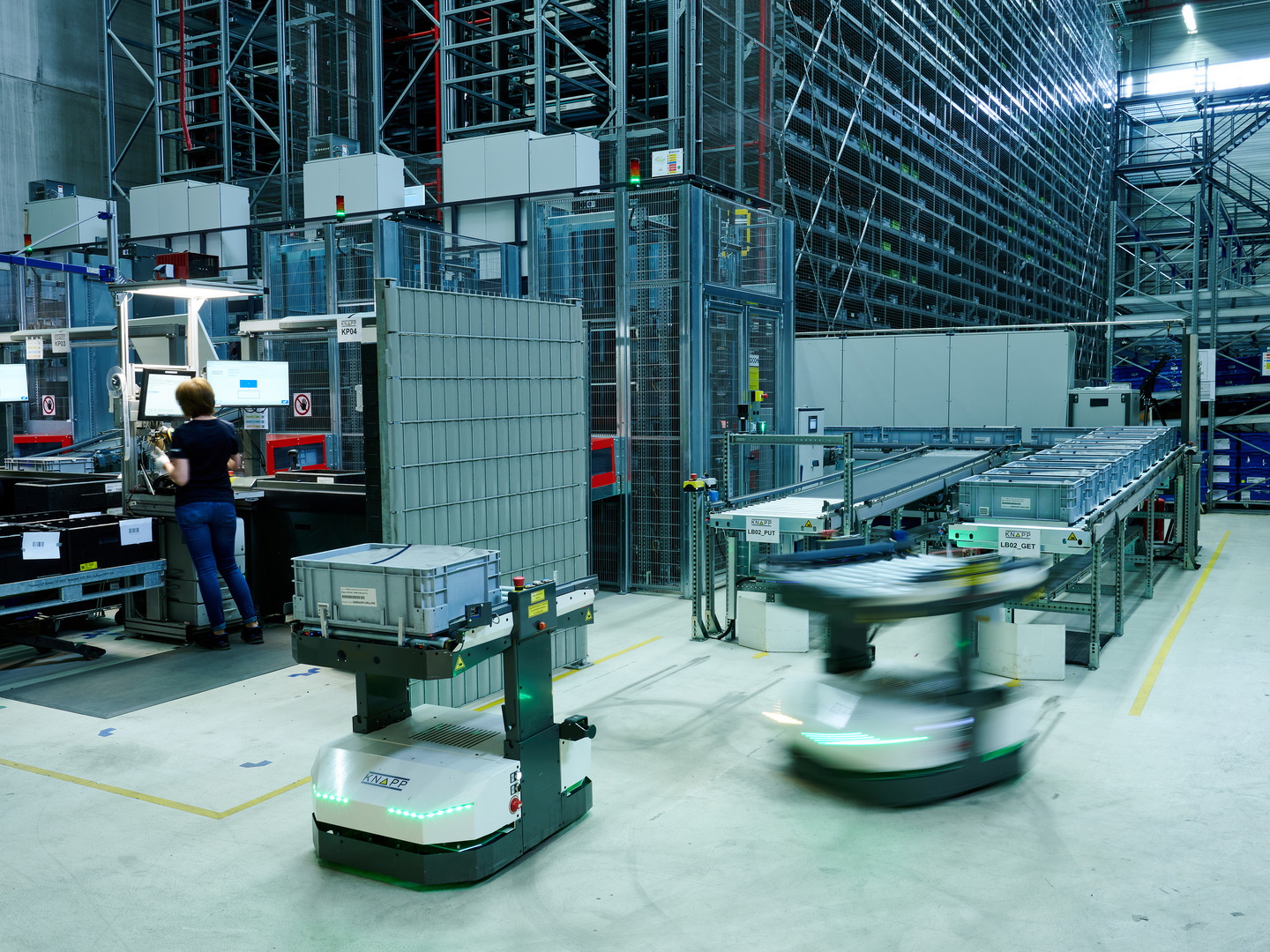
Magna Spiegelsysteme: Optimizing supply to production and assembly
Thanks to the automated solution by KNAPP, Magna achieved faster availability of parts, a reduction in internal transport and hands-free warehouse operation. The foundation for all of this is the multifunctional shuttle system combined with autonomous mobile robots.
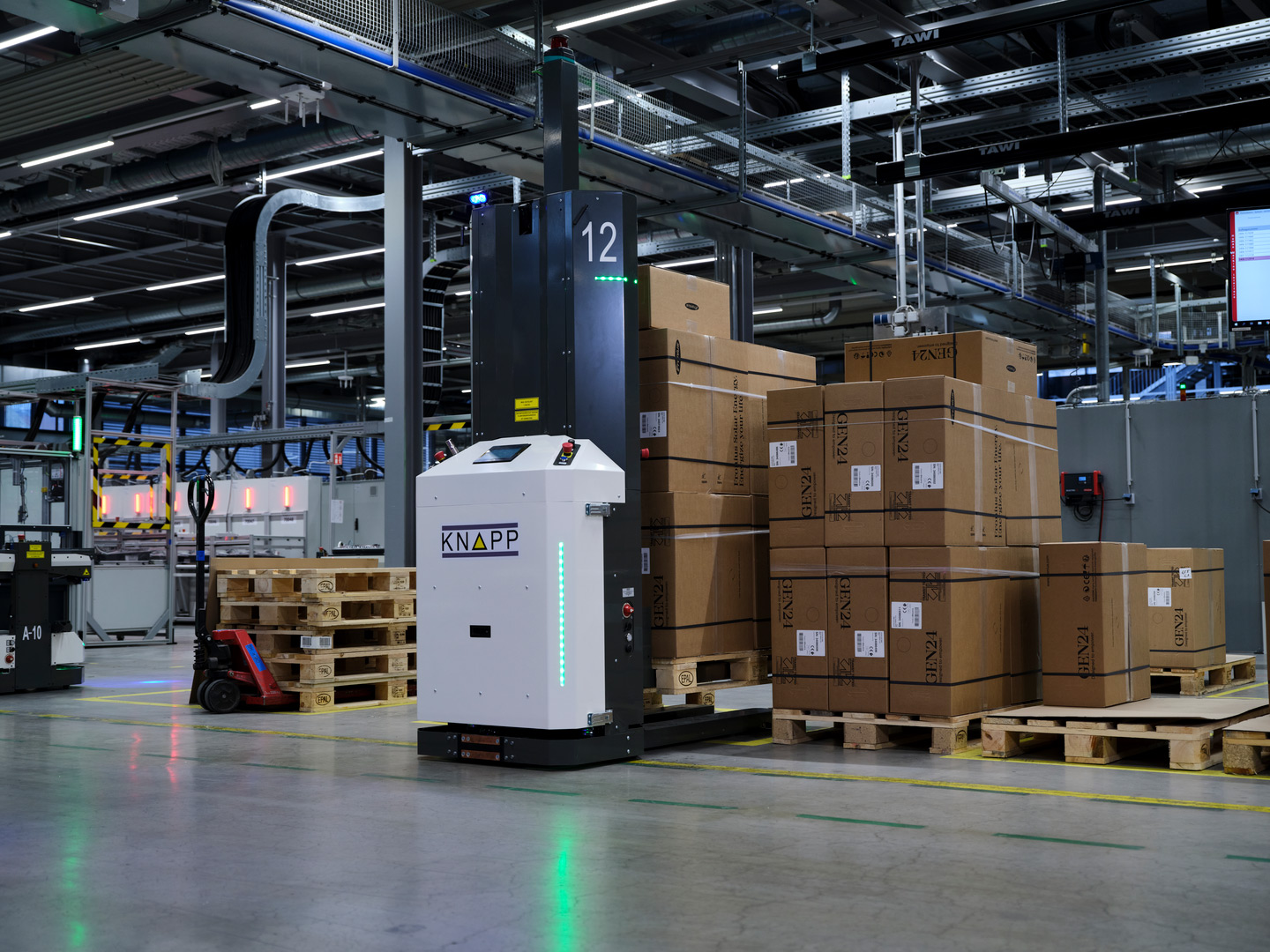
Fronius: AMRs provide flexible, automated pallet transport for production supply
The innovative Open Shuttle Fork has automated production supply and internal transport at Fronius. The new solution gives the company the necessary autonomy to flexibly make changes as needed and to manage both manual and automatic transport orders in the same system.
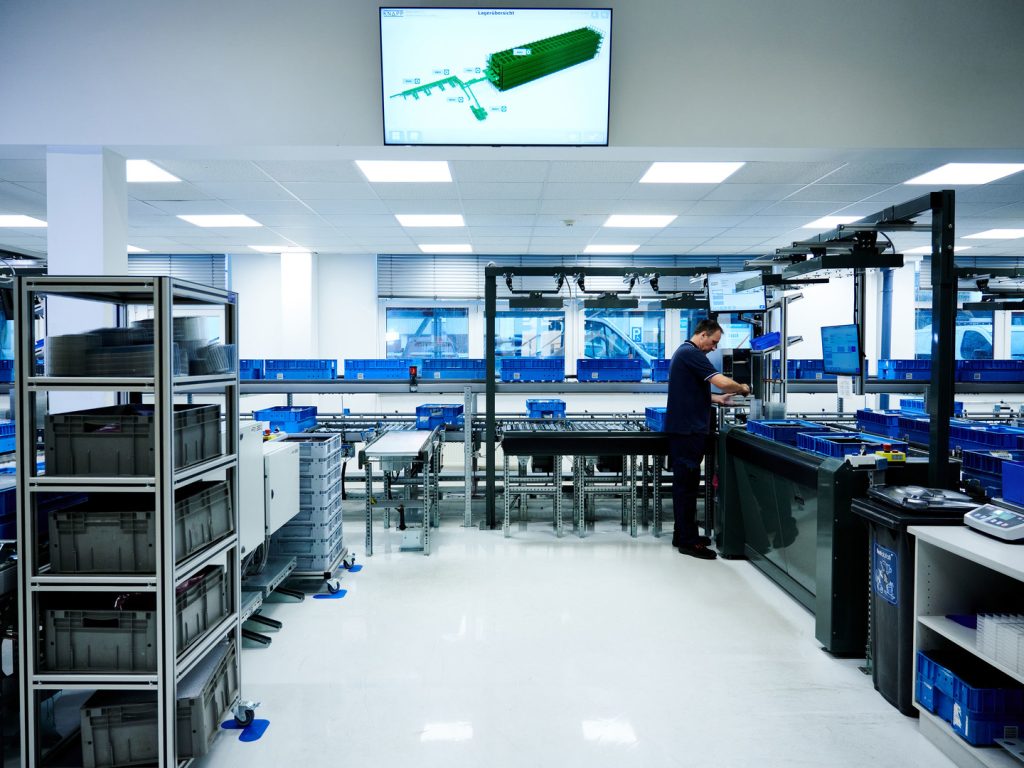
Knorr-Bremse: Process optimization thanks to customized system
Knorr-Bremse increased the performance of their small-parts warehouse by a factor of three. This was made possible by a multifunctional shuttle system combined with picking work stations and a conveyor system mounted to the ceiling. Discover more about the solution and how it efficiently covers the various processes.
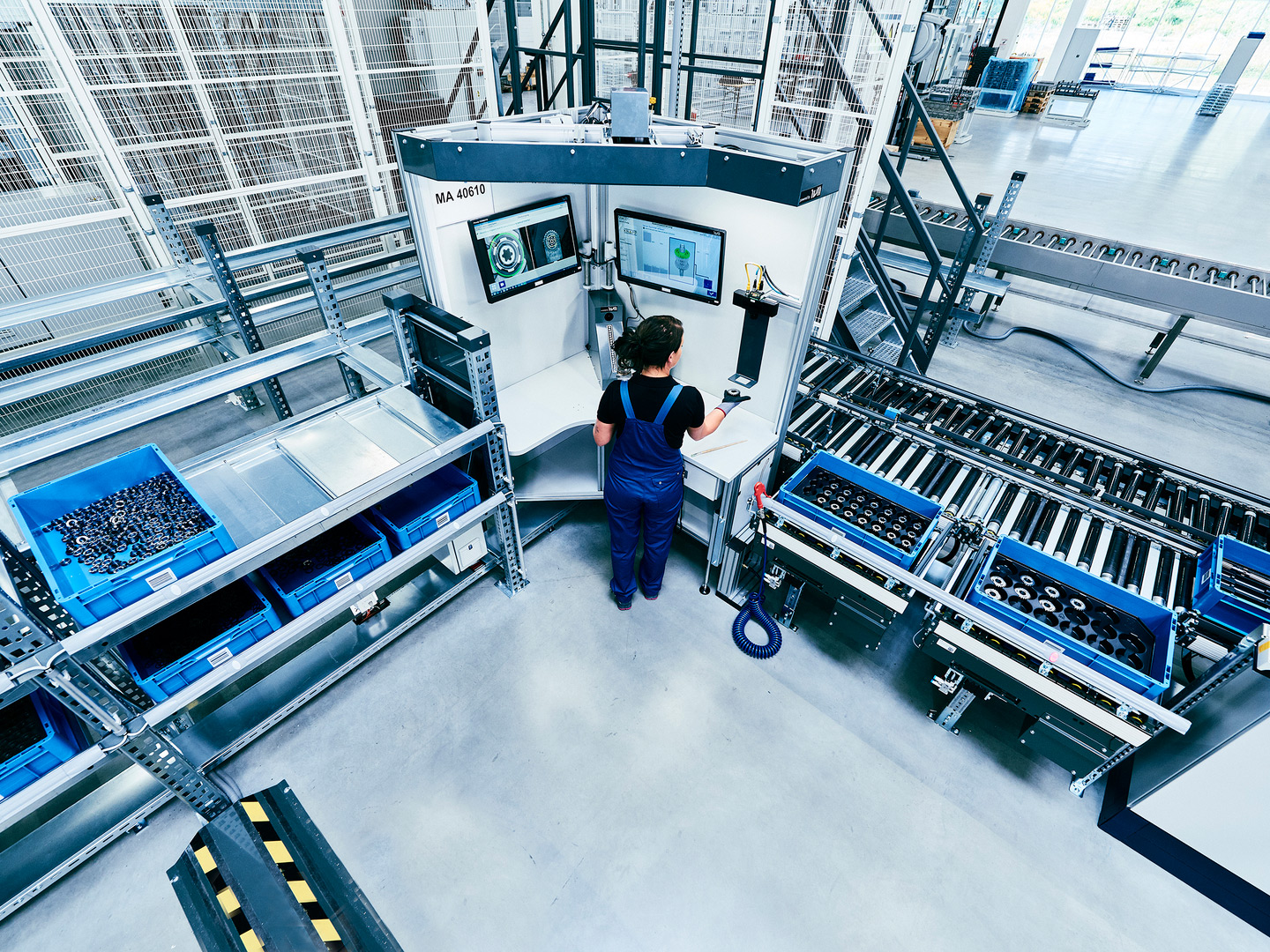
Pankl Racing AG: Zero-error strategy covers all production processes
An automated small parts warehouse supplies Pankl’s assembly work stations according to the goods-to-person principle. Modern image recognition and processing technologies check each step of work, which results in error-free assembly and seamless traceability. Pankl’s manufacturing logistics is a textbook case in smart production.
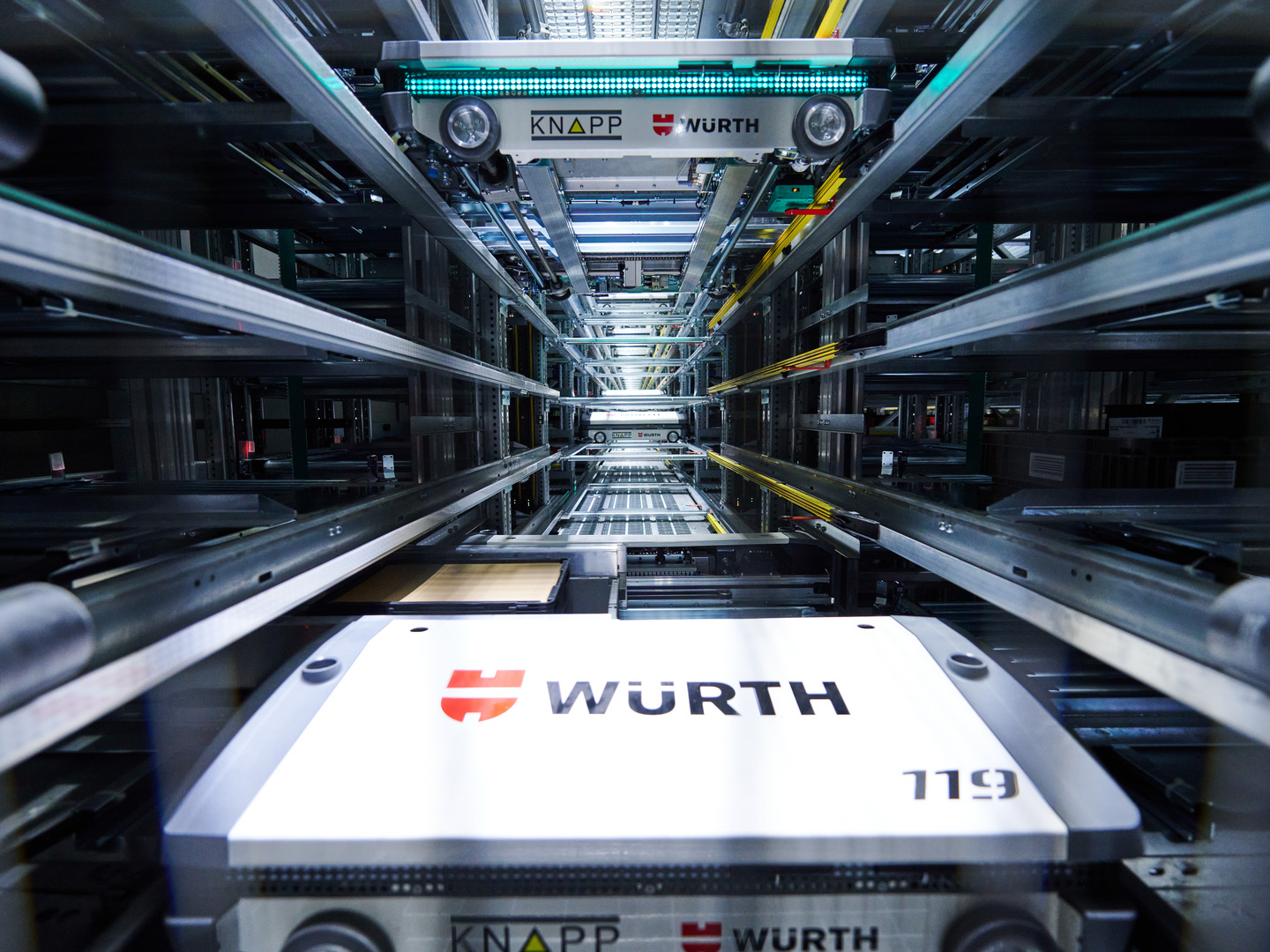
Würth: Intelligent automation in logistics
Würth is using the very latest robot technologies at their warehouse. These technologies fully automate logistical processes ranging from storage to picking and shipping, including internal transport. We have partnered with Würth for many years, continually developing the technologies they use.
References:
Our solutions for warehouse automation in industry
Companies around the globe depend on collaboration with KNAPP. We help you optimize your production processes, storage space and in-house transport. Our solutions speak for themselves:
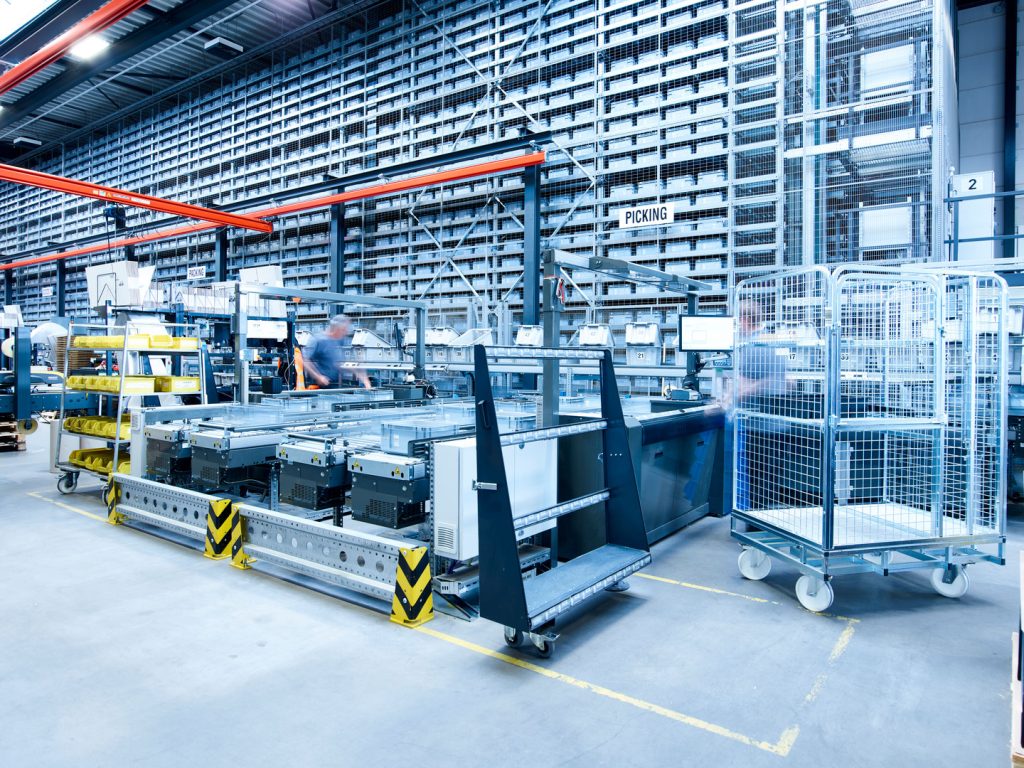
Terberg Benschop B.V.: New solution creates basis for future company growth
To handle the increasing number of orders, several processes at Terberg Benschop B.V. were centralized in one automated storage system. Picking orders are fulfilled for manufacturing, the assembly line, or for the shipping of spare parts. Supply is as needed and just in time.
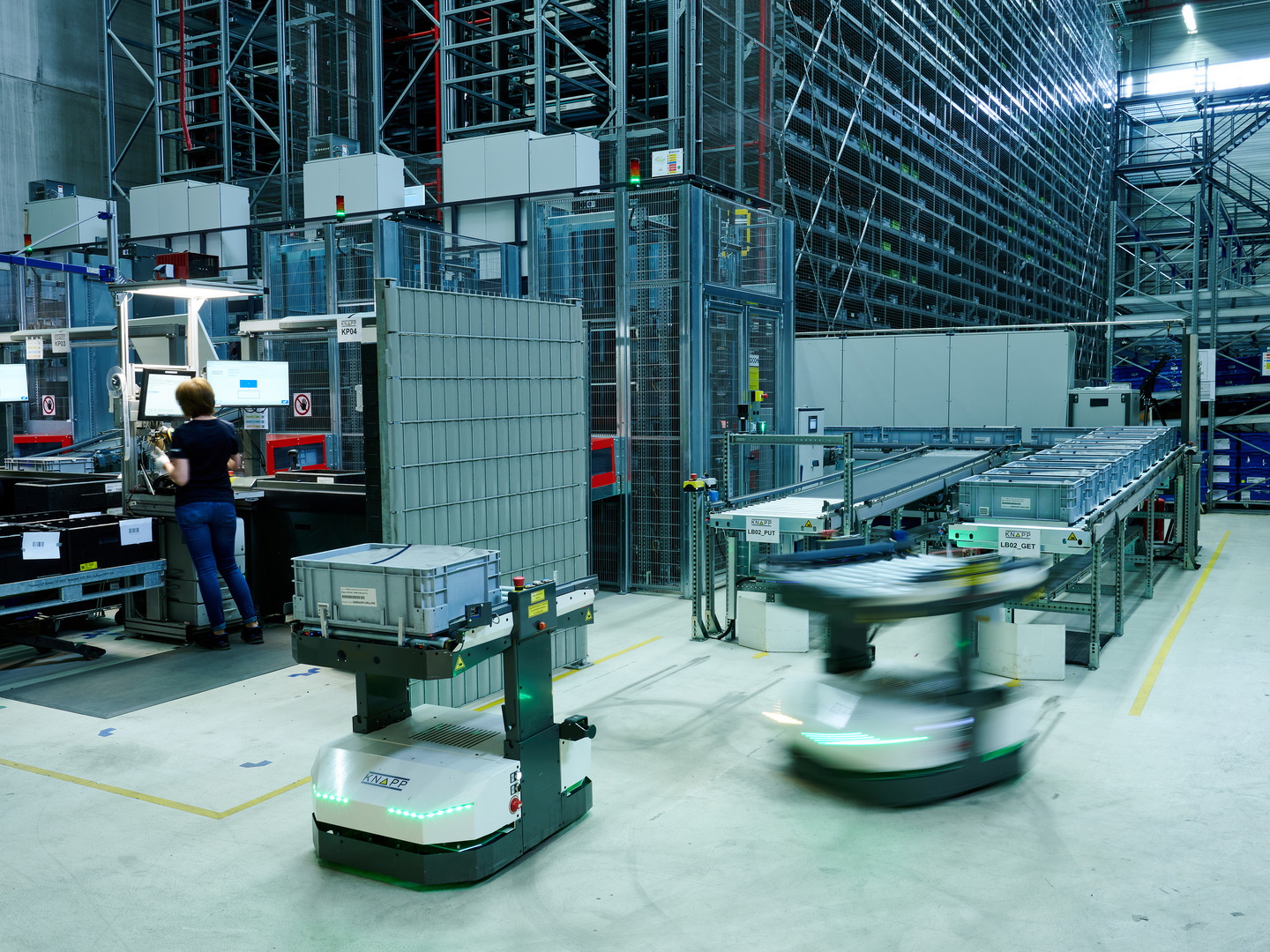
Magna Spiegelsysteme: Optimizing supply to production and assembly
Thanks to the automated solution by KNAPP, Magna achieved faster availability of parts, a reduction in internal transport and hands-free warehouse operation. The foundation for all of this is the multifunctional shuttle system combined with autonomous mobile robots.
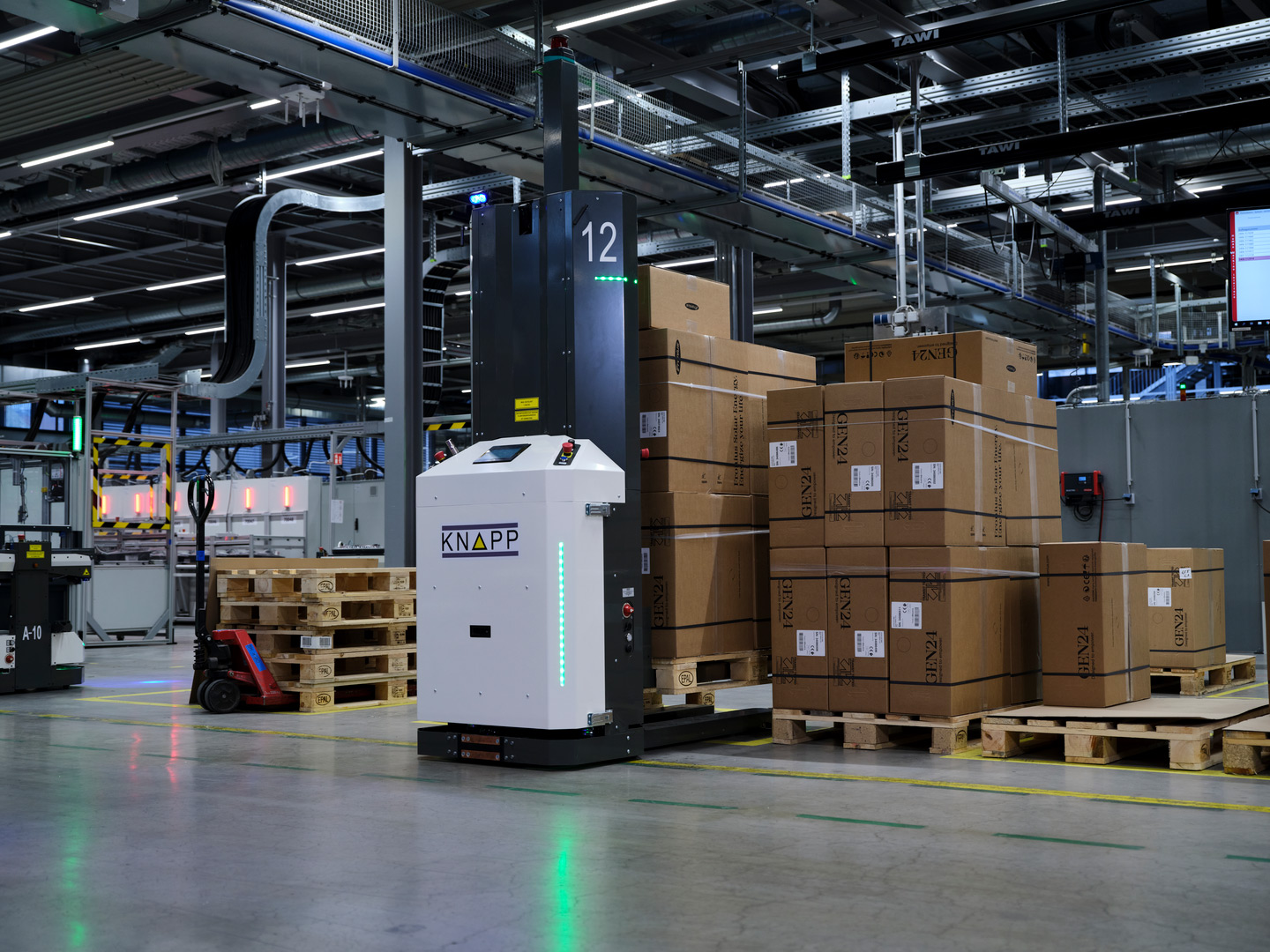
Fronius: AMRs provide flexible, automated pallet transport for production supply
The innovative Open Shuttle Fork has automated production supply and internal transport at Fronius. The new solution gives the company the necessary autonomy to flexibly make changes as needed and to manage both manual and automatic transport orders in the same system.
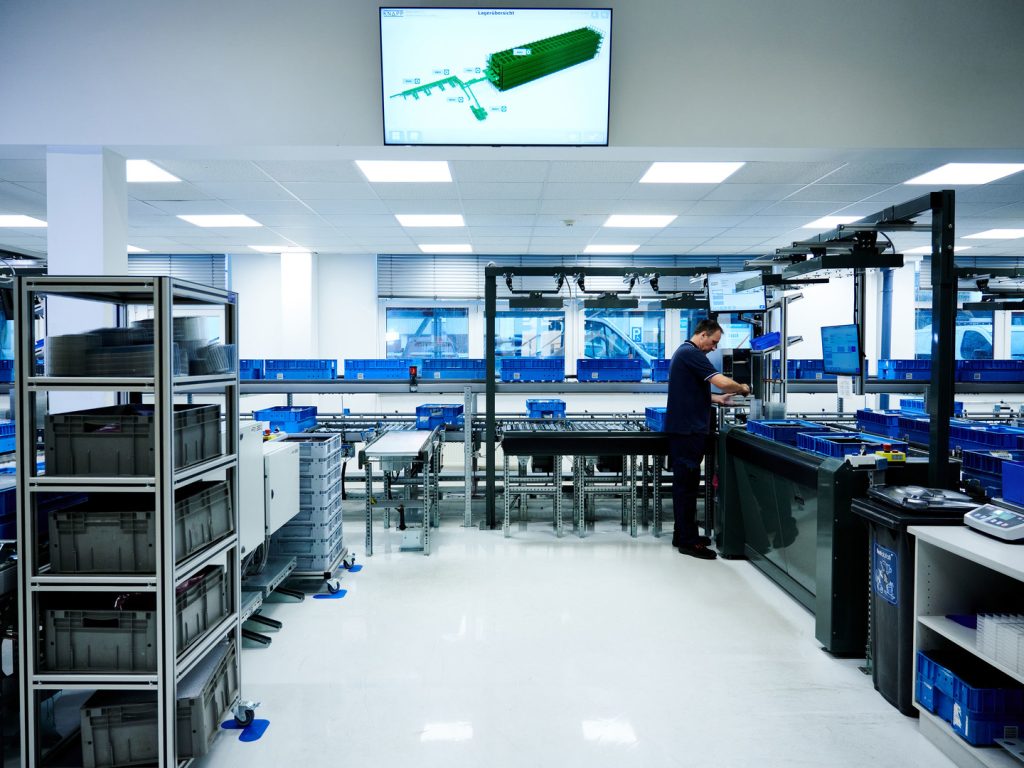
Knorr-Bremse: Process optimization thanks to customized system
Knorr-Bremse increased the performance of their small-parts warehouse by a factor of three. This was made possible by a multifunctional shuttle system combined with picking work stations and a conveyor system mounted to the ceiling. Discover more about the solution and how it efficiently covers the various processes.
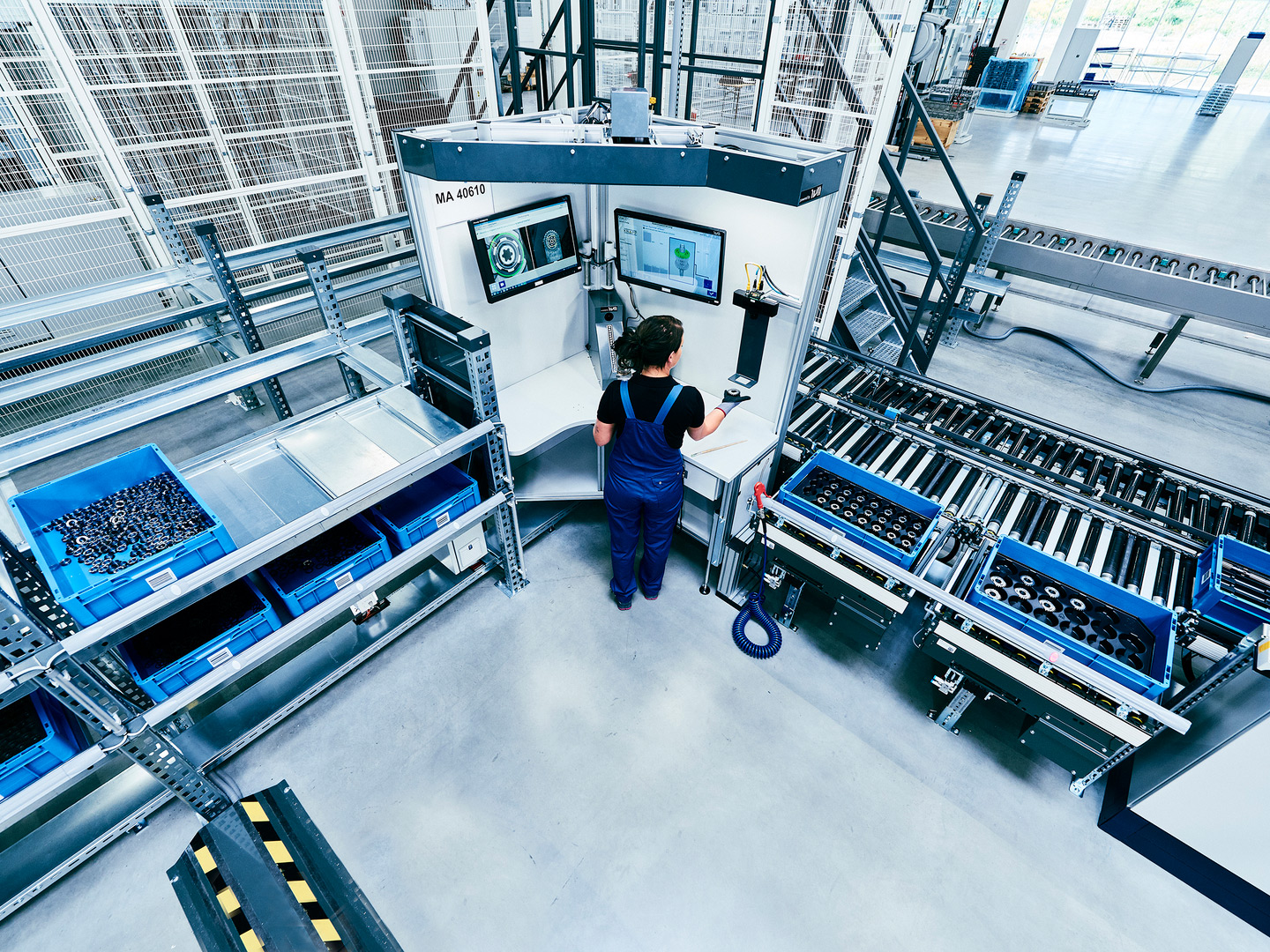
Pankl Racing AG: Zero-error strategy covers all production processes
An automated small parts warehouse supplies Pankl’s assembly work stations according to the goods-to-person principle. Modern image recognition and processing technologies check each step of work, which results in error-free assembly and seamless traceability. Pankl’s manufacturing logistics is a textbook case in smart production.
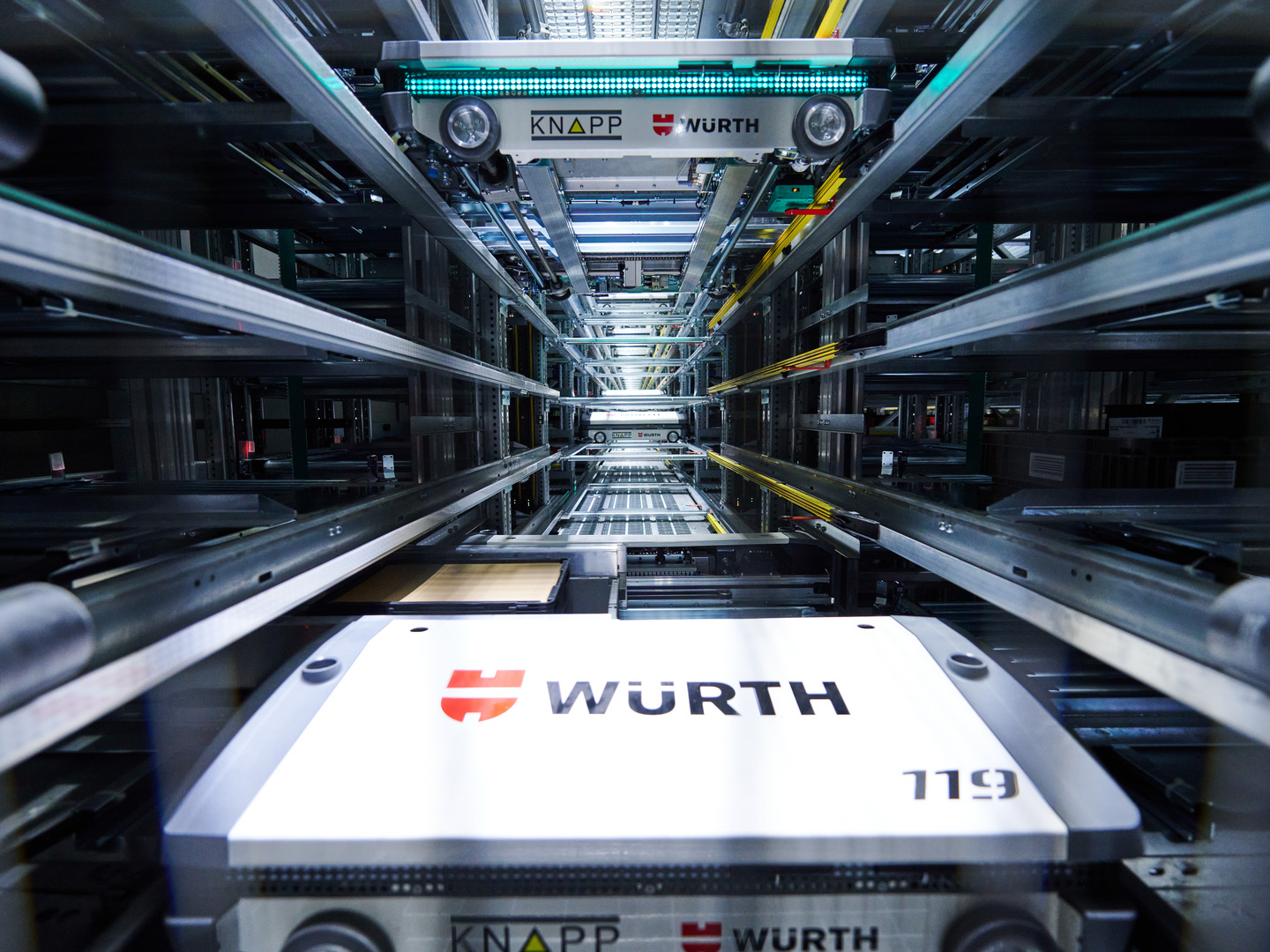
Würth: Intelligent automation in logistics
Würth is using the very latest robot technologies at their warehouse. These technologies fully automate logistical processes ranging from storage to picking and shipping, including internal transport. We have partnered with Würth for many years, continually developing the technologies they use.
Global service network and reliable partner
Our International Customer Service looks after your logistics system – around the globe, around the clock, 365 days a year.
Discover more about our services, from seamless support to optimizing your system!
Warehouse automation for manufacturing –
our customers trust us:
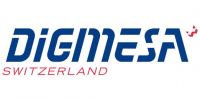
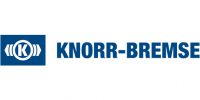
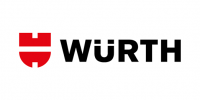
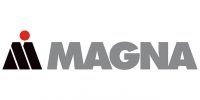
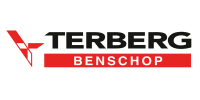
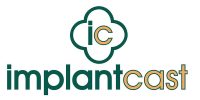
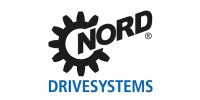
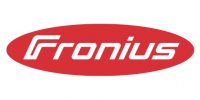
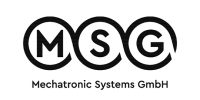
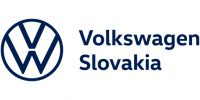
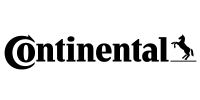
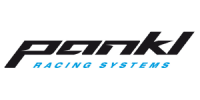
Are you curious about our solutions for warehouse automation for manufacturing?
We’re happy to tell you more!
Explore our blog posts on
warehouse automation and the value chain:

Autonomous mobile robots (AMRs) facilitate flexible, efficient transport processes. Whether deployed in manufacturing, food retail or in distribution logistics – their range of use is wide. Discover more about this future-oriented technology.

What does the smart factory of the future look like? Find out more about our vision for smart manufacturing!

Is the fully automated dark warehouse the right so-lution for prevailing personnel shortages? Find out here!