Robotics and AI in Logistics
Robotics. Artificial intelligence. Machine learning. Networked technology. These terms are increasingly vital to logistics. Problems such as the lack of resources are solved by using robotics throughout the supply chain, which simultaneously increases quality and the profitability of the processes. Humans and machines do not compete, but rather complement each other: A robot never gets tired and can carry out tasks over a long period of time with consistently high quality. By comparison, a human can respond quickly and flexibly to new requirements. Together, humans and technology make a great team for implementing logistics requirements in the most effective and efficient way. The use of artificial intelligence opens up the range of applications for robots, turning them into high-performance, economical assistants.
We offer an extensive selection of industrial robot solutions for various processes in production and the warehouse: robots for bin picking, robots for fully automatic full-case picking, and autonomous mobile robots for transport tasks.
More than single-item picking: Pick-it-Easy Robot
Pick-it-Easy Robot is the right choice, not just for automatic single-item picking but also for the induction of articles in pre-picked batch containers into overhead or sorting systems. Various grippers, AI-based object recognition – the so-called Covariant Brain – and grip point specification mean that the Pick-it-Easy Robot can handle a broad article range, for many applications in diverse sectors. Even when goods have reflective surfaces, the Pick-it-Easy Robot knows exactly where to hold them and gently places them exactly where they belong. Machine learning means that the system is continuously learning and improving itself.
Want to know more?
Three good reasons to choose the Pick-it-Easy Robot
With the Pick-it-Easy Robot, we combine cutting-edge technology with comprehensive logistics expertise. It’s not just the artificial intelligence that makes the fully automatic robot station special, it’s how well it can be integrated, and what it adds through its high performance.
• Handles a wide variety of goods
• Smart fulfillment strategies
• Jumps in when there’s a shortage in personnel
• Automatic troubleshooting
• High-quality components
• Fast and easy intelligence transfer
You are currently viewing a placeholder content from YouTube. To access the actual content, click the button below. Please note that doing so will share data with third-party providers.
More InformationPick-it-Easy Robot in action: The proven industrial robotics solution
At Würth Industrie Service, robots play an important role at the Bad Mergentheim location, as they fill orders fully automatically. This compensates for demographic change and relieves employees from strenuous tasks, allowing them to take on more value generating processes. Pick-it-Easy Robot is highly versatile, picking various types of single items reliably. Helmut Eisenkolb, Head of Logistics & Member of the Board of Directors at Würth Industrie Service, provides insight.
You are currently viewing a placeholder content from YouTube. To access the actual content, click the button below. Please note that doing so will share data with third-party providers.
More InformationRobotics plays a significant role in Würth’s strategy. We want to secure future growth, maximize productivity and reduce the strain on our employees. […] We have opted for robotic solutions because we are convinced that they will future-proof our business.
Intelligent integration of Robotics and AI
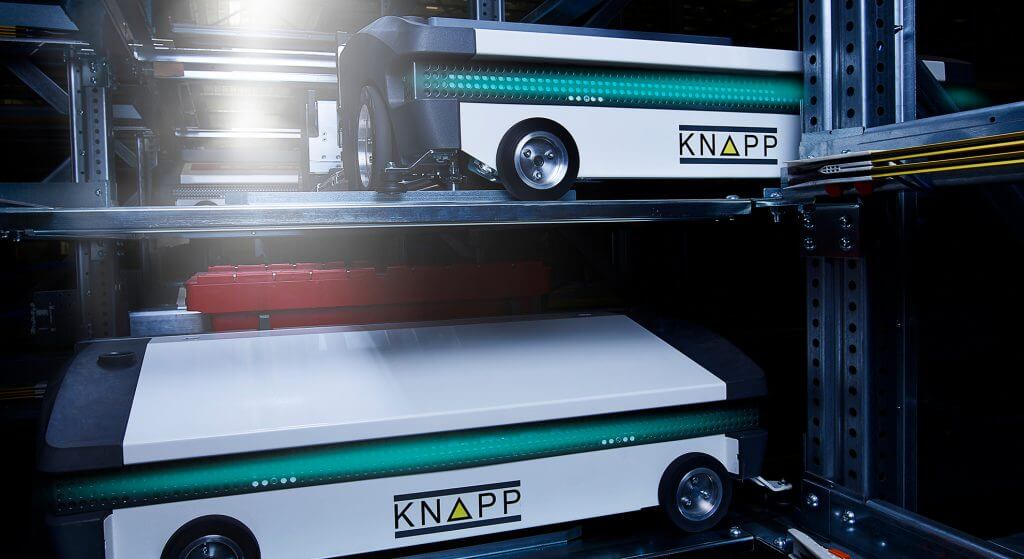
Pick-it-Easy Robot + OSR Shuttle™
The combination of a fast shuttle system and a reliable picking robot creates an efficient, fully automatic goods-to-robot picking process.
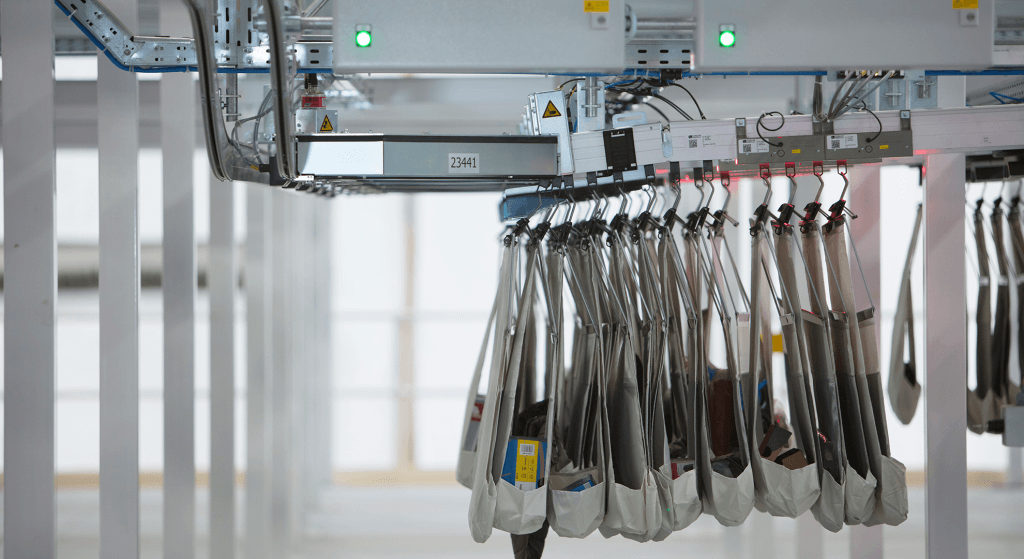
Pick-it-Easy Robot + Pocket Sorter
Combining the powerful pocket sorter system and the Pick-it-Easy Robot results in an efficient solution for multi-channel applications, especially in the fashion and retail sectors.
Fully automatic full-case picking in food retail: RUNPICK
RUNPICK – short for Robotic Universal Picker – takes store delivery up to a whole new level. Specially developed for food retail, the system processes and palletizes large handling units for brick and mortar retail fully automatically. The robot is capable of store-friendly picking and handles both fresh and shelf-stable goods on pallets and roll containers. Multiple item picking allows several items to be deposited at the same time in just one cycle, leading to a considerable increase of performance.
Want to know more?
Three great reasons to opt for RUNPICK
RUNPICK provides higher throughput, shorter container transit times, and adaptability for food retail. With its intelligent packing algorithm, selectable picking criteria and its combining of different pack unit types, the robot is an ace at store-friendly delivery.
• Combination of different items per cycle
• Easy system expansion
• Scalable, modular solution
• Selectable picking criteria
• Reduces personnel costs
• No physical strain on employees
RUNPICK in action: Integration into omnichannel models and solutions for store delivery
RUNPICK can ideally be integrated in solutions for brick and mortar retail as well as in omnichannel models.
The omnichannel solution connects all logistics processes within a warehouse: e-commerce, brick and mortar retail, as well as a combination of both. In the fully automatic version, our intelligent robots take on the work: Pick-it-Easy Robot processes single items while RUNPICK processes large handling units, both fully automatically.
In our blog we talk about how RUNPICK is revolutionizing food retail warehousing.
The big advantage that RUNPICK offers is that it can handle a variety of pack unit types and processes them fast and efficiently with the help of multiple-item picking. This significantly increases performance compared to existing systems.
Smart combination of technologies

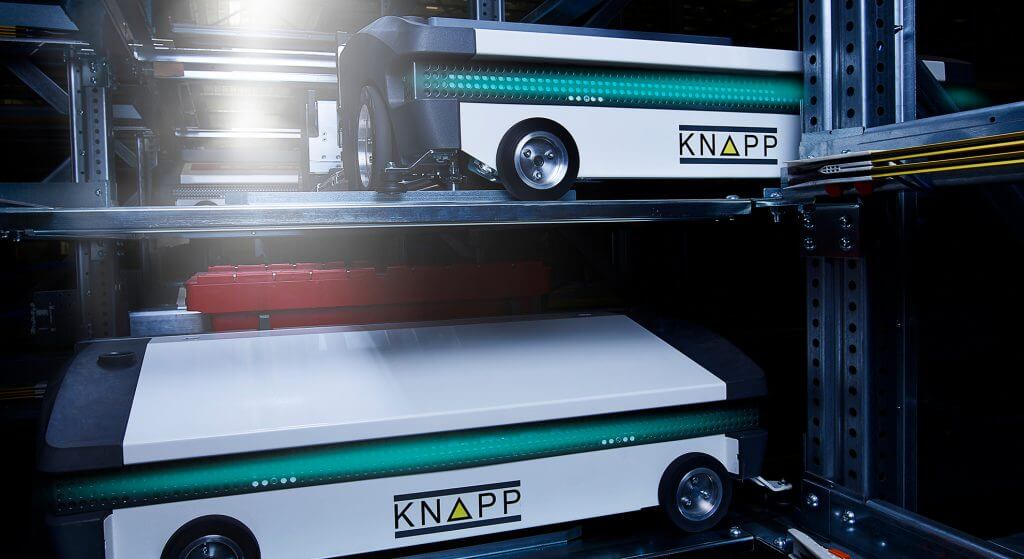
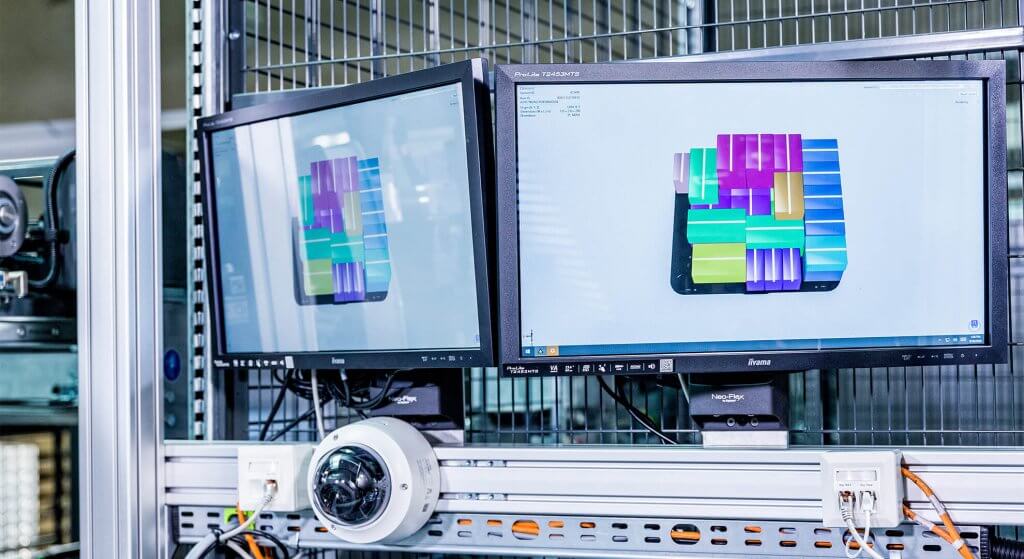
RUNPICK + OSR Shuttle™ Evo + KiSoft Pack Master
The RUNPICK solution is always a combination of our Evo Shuttle, KiSoft Pack Master software and the picking and palletizing system.
Optimizing processes with robotics: Automatic palletizing and depalletizing
Loading and unloading pallets is a physically strenuous task for employees because of the heavy lifting involved. This is where robots can really lighten the load as part of innovative automation solutions. In goods-in, they depalletize fully automatically and prepare the articles for storage. In goods-out, they assemble stable pallets for shipping. Robots can also stack and destack cartons and standard handling units, and load dollies, all of that fully automatically. This full automation both takes the strain off employees and increases efficiency.
Want to know more?
Automatic palletizing and depalletizing brings flexibility and performance
Whatever your business model, robot solutions for palletizing and depalletizing deliver the required flexibility and performance. Robots function extremely well in various processes:
- Depalletizing various handling units and loading them directly into storage containers
- Palletizing store containers or empty handling units layer by layer
- Stacking and destacking cartons and standard handling units
- Loading various container types onto dollies
- Mixed case palletizing of cartons or store containers
You are currently viewing a placeholder content from YouTube. To access the actual content, click the button below. Please note that doing so will share data with third-party providers.
More InformationPalletizing and depalletizing solutions: Robotics at Dior
The exclusive perfumes and cosmetics giant Parfums Christian Dior uses KNAPP robot solutions for their manufacturing location in Saint-Jean-de-Braye, France. Automation is what makes efficient omni-channel fulfillment possible. Smart robots handle most of the work, boosting distribution performance.
Head over to our blog to find out more about the solution at Parfums Christian Dior.
This project turned out to be quite an adventure for me. We worked closely with the KNAPP team to realize the project successfully within 18 months. The key to our success was open communication and professional, cordial collaboration in every project phase.
Fully automatic palletization – Intelligently integrated
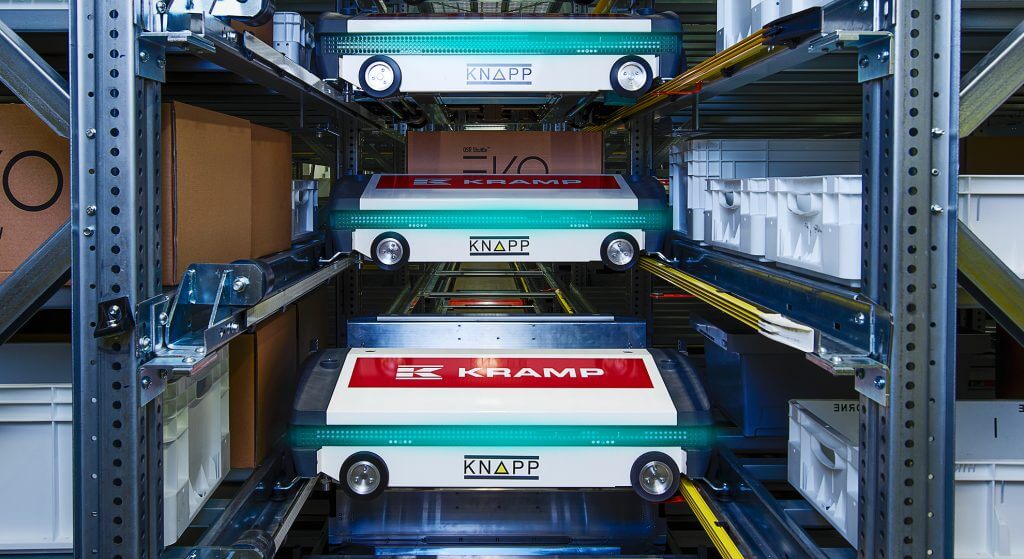
Robot solutions for palletizing and depalletizing + OSR Shuttle™ Evo
The Evo Shuttle takes care of the processes before and after. After automatic depalletization or destacking, the articles are stored in the Evo Shuttle until they are needed. Later, the Evo Shuttle retrieves the handling units in the correct sequence, so that the end result is a stable shipping pallet.
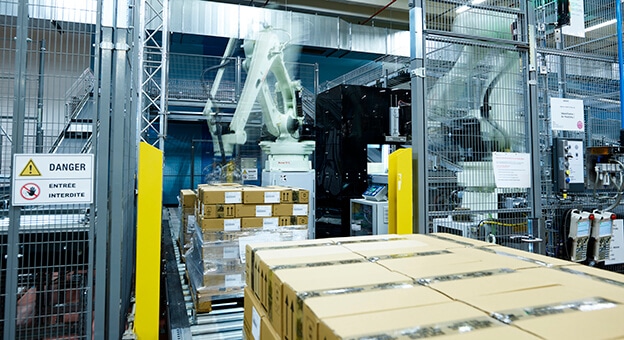
Robot solutions for palletizing and depalletizing + KiSoft Pack Master
The robots need to know where on the target load carrier to place the cartons or handling units – this intelligent software works in the background to provide this information. KiSoft Pack Master calculates the perfect packing pattern, determining the sequence in which the articles are retrieved from the Evo Shuttle.
Autonomous mobile robot for transport within facilities: Open Shuttle
Can transport processes within a facility run flexibly? Of course they can. With the Open Shuttles, it’s easy. These autonomous mobile robots connect different areas within facilities quickly and efficiently, bringing goods, raw materials and components to where they need to be. Taking different kinds of load carriers from A to B is a breeze for the Open Shuttles. Thanks to their innovative technology, they act with complete autonomy, they don’t need any aids, and they are 100% safe for people. What’s more, they are flexible and easy to integrate.
Three top reasons to choose Open Shuttles
Open Shuttles are so flexible that various logistical challenges are a breeze for them, whether they are deployed as a stand-alone solution or as part of an all-in-one solution. The autonomous mobile robots act as an intelligent swarm and are easy to configure.
• Intelligent route planning
• Intelligent management of orders and resources
• Easily adapted
• Quickly integrated
• Scalable fleet size
• Handles every kind of transport task
You are currently viewing a placeholder content from YouTube. To access the actual content, click the button below. Please note that doing so will share data with third-party providers.
More InformationOpen Shuttle in action: Flexible manufacturing supply
The Swiss flow meter manufacturer Digmesa adapted the transport processes in manufacturing after merging locations. An Open Shuttle is now responsible for supplying injection molding machines with empty containers and for taking finished parts to buffer storage. Stefan Schneider, CEO Digmesa AG, talks about the decision for an Open Shuttle:

What really convinced us was the shuttle’s functionalities. In comparison with other systems, with the Open Shuttle, we can pick up and deliver at various heights. This is something we needed that only the KNAPP autonomous mobile robot could fulfill. Talking to the KNAPP employees, we also quickly realized how dynamic, flexible and competent the company is. This was very impressive, so we soon had a lot of confidence in the finished solution.
Open Shuttles – Intelligent integration
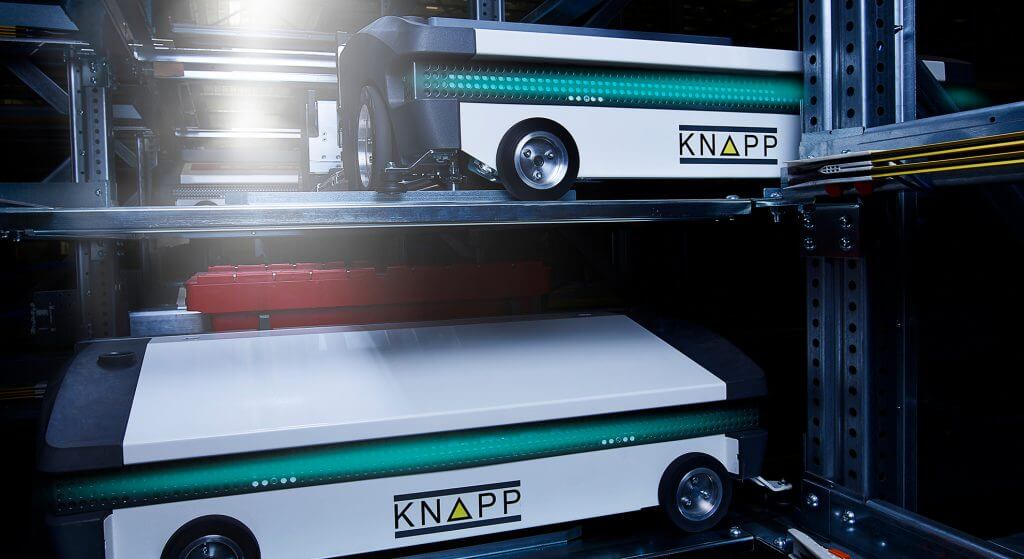
Open Shuttles + OSR Shuttle™ Evo
Perfect flexibility meets perfect performance: Together, the Evo Shuttle and the Open Shuttle are even more powerful as a smart system solution – the Evo Shuttle. Goods, raw materials, overstock, buffered orders – everything is stored centrally in the Evo Shuttle. The Open Shuttles supply different work stations in diverse warehouse areas directly from the Evo Shuttle just-in-time.
More about our autonomous mobile robots

You are currently viewing a placeholder content from YouTube. To access the actual content, click the button below. Please note that doing so will share data with third-party providers.
More Information
You are currently viewing a placeholder content from YouTube. To access the actual content, click the button below. Please note that doing so will share data with third-party providers.
More Information
Would you like to know more?
More on robotics and AI in Logistics

Autonomous mobile robots (AMRs) facilitate flexible, efficient transport processes. Whether deployed in manufacturing, food retail or in distribution logistics – their range of use is wide. Discover more about this future-oriented technology.

How can rethinking logistics solution design create added value for you? We show you three new perspectives on software. Read them here!

Is the fully automated dark warehouse the right so-lution for prevailing personnel shortages? Find out here!