Véhicule autoguidé approvisionne la production chez Digmesa
La société suisse Digmesa développe, fabrique et distribue des débitmètres pour les liquides depuis 38 ans déjà. En raison d’un regroupement du site des deux sociétés sœurs, les processus et la production des deux entreprises ont été restructurés et transférés dans une nouvelle halle. Dans le cadre de ce déménagement, l’objectif était d’automatiser les processus de transport pour l’approvisionnement des automates de montage. En seulement quatre mois de réalisation, une nouvelle solution véhicule autoguidé a été mise en place. Nous avons discuté avec les dirigeants Stefan Schneider et Dominik Huber de la nouvelle solution flexible.
Vous êtes actuellement en train de consulter le contenu d'un espace réservé de YouTube. Pour accéder au contenu réel, cliquez sur le bouton ci-dessous. Veuillez noter que ce faisant, des données seront partagées avec des providers tiers.
Plus d'informationsDans quels domaines la société Digmesa est-elle active et quels changements ont eu lieu au fil du temps ?
Stefan Schneider : « Digmesa est typiquement une petite et moyenne entreprise et nous développons, produisons et distribuons des débitmètres pour les secteurs les plus divers. Dans presque toutes les machines à café du monde est monté un débitmètre venant de chez nous. Le boom des machines à café et la digitalisation des dix dernières années nous ont donné un nouvel élan. À mes débuts chez Digmesa, nous produisions 100 000 débitmètres par an. Nous en sommes actuellement à 10 millions. Une telle quantité n’est plus comptable à la main. Nous avons donc commencé tôt à automatiser ».
Dominik Huber : « La société Polyform Kopp AG a été reprise en 2013 par Digmesa et a changé de nom. Nous sommes des transformateurs sous-traitants classiques et produisons des composants plastiques pour Digmesa mais également pour d’autres clients. Nous devons investir en permanence et adapter nos processus pour pouvoir sortir de telles quantités. L’année dernière, nous avons regroupé les sites et introduit un système de gestion commerciale. De plus, avec le système KNAPP, nous avons franchi une étape supplémentaire dans la collaboration des deux entreprises ».
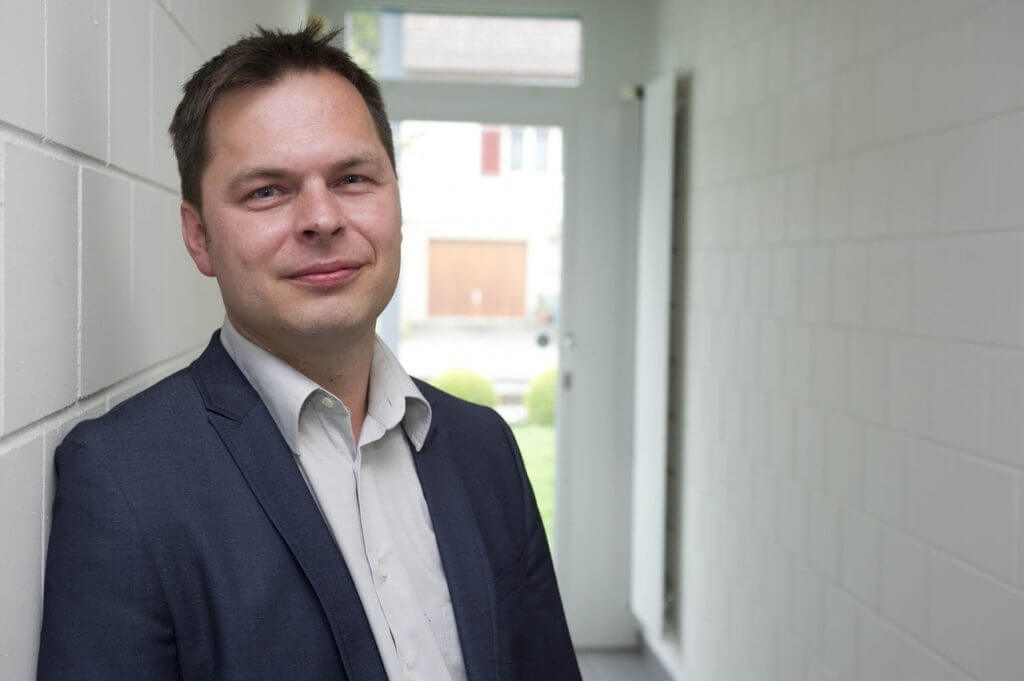
Stefan Schneider est CEO de Digmesa AG. Il est dans l’entreprise depuis 19 ans – d’abord comme développeur produit et depuis trois ans et demi comme directeur général.
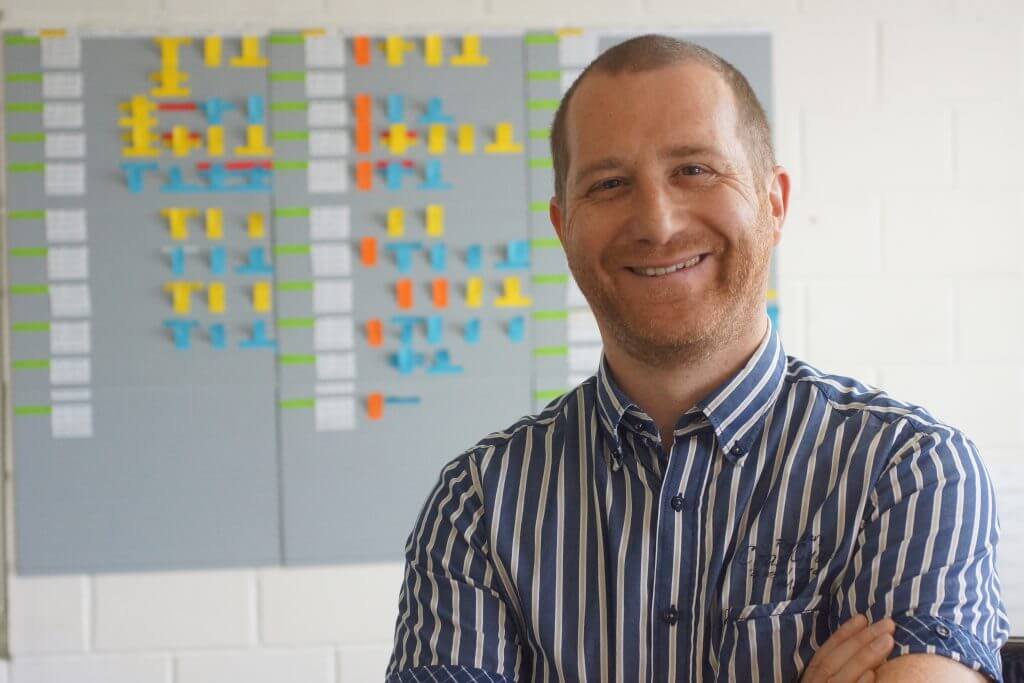
Dominik Huber est depuis 2015 CEO de Digmesa Polyform AG. Chez Digmesa depuis quinze ans, il était auparavant en charge des achats.
L’automatisation logistique vous intéresse aussi ?
Faites-vous conseiller par un de nos experts.
Un Open Shuttle assure l’approvisionnement des presses d’injection
Chez Digmesa Polyform, un véhicule autoguidé a été installé pour l’approvisionnement en conteneurs vides des presses d’injection et l’évacuation des pièces finies. Le point de départ de la solution est un rayonnage dynamique : il sert de zone de stockage temporaire avec une stratégie de stockage FIFO (First-in-First-out). Le pilotage de la solution s’effectue entièrement au moyen d’une application PLC de KNAPP sans aucune connexion au système Host. Le niveau de remplissage des différentes goulottes est contrôlé grâce aux capteurs optiques sur le rayonnage.
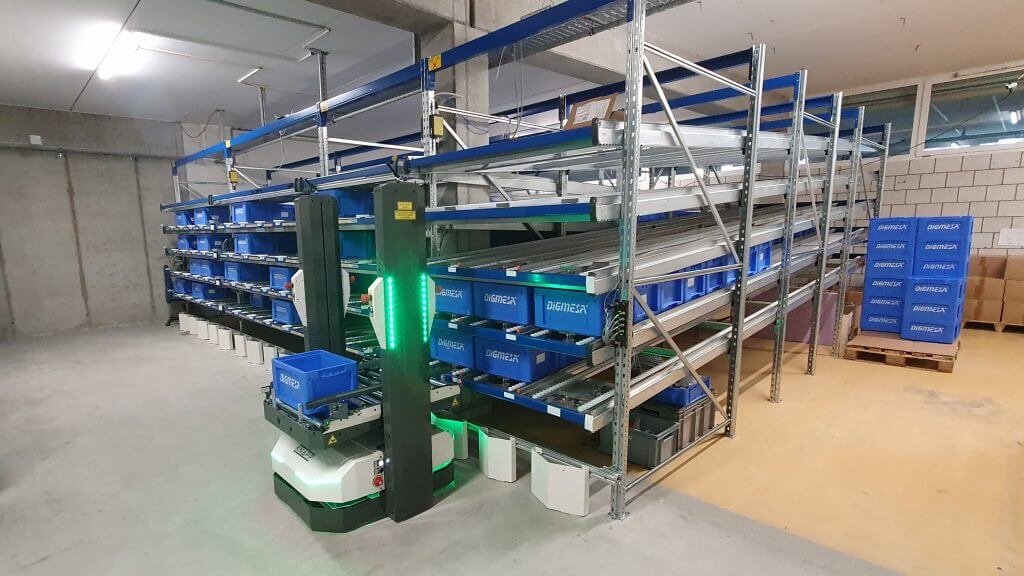
Aperçu de la solution Open Shuttle
3 goulottes pour l’assurance qualité, 12 goulottes pour conteneurs vides
À quoi ressemblait le processus avant l’utilisation de l’Open Shuttle ?
Dominik Huber : « Nous utilisions de simples installations de remplissage qui remplissaient les pièces en plastique dans des cartons. Ceux-ci étaient ensuite pesés au moyen de balances de comptage, comptés et les cartons étaient étiquetés à la main. De plus, un chauffeur devait emporter trois fois par semaine les cartons sur le site de Digmesa. Là-bas, les pièces étaient soumises à un nouveau contrôle qualité avant d’aller alimenter les automates de montage. Les cartons nous revenaient ensuite. Grâce au passage à l’Open Shuttle, nous avons pu optimiser les processus et économiser des ressources ».
Stefan Schneider : « La décision de regrouper les deux sites nous a ouvert de nouvelles perspectives. Au moyen de la cartographie des chaînes de valeur, nous avons pu concevoir de manière optimale la nouvelle construction et les processus de flux de matières, de l’approvisionnement en matières premières à la sortie des marchandises. Nous parlons ici de 10 millions de pièces du même type de produit. Ceci concerne le fonctionnement en continu des presses d’injection, les équipes 24h/24 7j/7 au niveau de nos automates de montage et là il est important que le flux de matières soit optimal et que nous ayons le moins d’arrêts de fonctionnement possibles. C’était la raison principale pour le choix d’un système autonome qui entre en stock au bon endroit, sans présence humaine ».
Grâce à l’Open Shuttle nous avons pu optimiser non seulement les processus mais aussi les quantités stockées.
Pourquoi avez-vous choisi un véhicule autoguidé ?
Stefan Schneider : « En fait, nous avons cherché des moyens qui allaient pour transporter aussi simplement que possible des pièces d’une presse d’injection à l’entrepôt. Nous avons envisagé les solutions d’automatisation les plus diverses. Nous sommes arrivés à la conclusion que ce véhicule autoguidé (VGA) pouvait se charger de manière autonome de toutes ces tâches. Et la durée de mise en œuvre était également décisive. Le nouveau bâtiment était planifié et nous avions besoin d’une solution qui convienne. Le système « simple » que nous avons maintenant comprend trois composants : un entrepôt, un Open Shuttle et des positions de dépose. La simplicité du système et la mise en œuvre du projet par KNAPP de façon compétente ont rendu cela possible ».
Dominik Huber : « Je ne peux qu’approuver M. Schneider. Le gros avantage est que l’Open Shuttle a déjà le dispositif de levage intégré. C’est assurément un avantage décisif du VGA de KNAPP. J’ai vu quelques systèmes lors d’expositions et aucun n’avait de dispositif de levage ».
Stefan Schneider : « Avant tout, c’est la fonctionnalité de la navette qui nous a convaincus. En comparaison avec d’autres systèmes, nous avons la possibilité avec l’Open Shuttle de déposer et de récupérer à différentes hauteurs. C’est indispensable pour nous et seul le VGA de KNAPP peut le faire. Lorsque nous avons commencé à discuter avec les gens de KNAPP, j’ai très vite remarqué à quel point cette entreprise était flexible, dynamique et aussi compétente. Nous avons été très impressionnés et très vite, nous avons eu une grande confiance dans cette solution ».
La flexibilité que ce système permet est tout simplement inestimable. Dans la production, rien n’est monté de manière fixe. Il n’y a que les chemins dont l’Open Shuttle a besoin et rien d’autre.
Grâce au dispositif de levage intégré de l’Open Shuttle, la dépose et la prise de supports de manutention pour petites charges est possible à des hauteurs comprises entre 550 mm et 1 500 mm. Pendant le trajet, le véhicule autoguidé adapte automatiquement la hauteur au lieu de prise et de dépose.
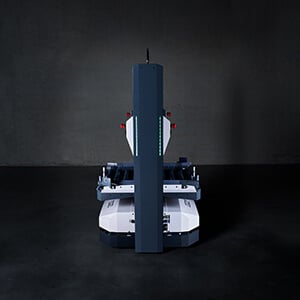
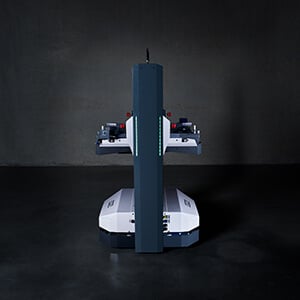
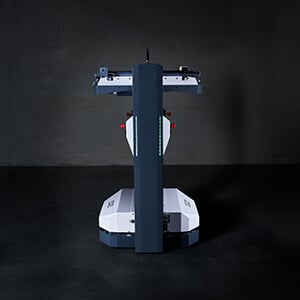
Vous voulez en savoir plus sur Open Shuttle ?
Cliquez ici pour découvrir les robots mobiles autonomes.
L’automatisation devient de plus en plus importante en termes de croissance d’entreprise. Cependant, elle est souvent accusée de détruire des emplois. Qu’en pensez-vous ?
Stefan Schneider : « L’homme est un élément essentiel de la culture d’entreprise de Digmesa. Notre objectif est de continuer à vivre ces valeurs dans le futur et de donner aux employés la liberté dont ils ont besoin pour s’épanouir. Il est certain que l’automatisation crée des emplois dans certains domaines et au pire, en détruit dans d’autres. Dans notre cas, je vois les choses ainsi : sans l’automatisation, nous serions incapables de produire de telles quantités. Et surtout pas sur le site en Suisse. Nous n’aurions aucune chance d’exister en tant qu’entreprise. Sans l’automatisation, nous emploierions nettement moins de personnes. Je vois les choses comme ça : nous avons la chance de pouvoir développer des produits toujours nouveaux et des innovations et donc de créer de la croissance et des emplois ».
Dominik Huber : « La tendance est bien sûr à la spécialisation du personnel au détriment des emplois non qualifiés. Mais avec les quantités que nous produisons, l’automatisation permet aussi de décharger nos employés. Des processus comme porter des caisses, emballer ou encore empiler peuvent être automatisés facilement. L’homme a une place à part et je souhaite l’employer là où cela est intéressant et pas pour des tâches qui peuvent être automatisées vraiment bien».
Un véhicule autoguidé comme trait d’union entre deux entreprises
À la suite d’un petit sondage, le nom de « Knappi » a été choisi pour l’Open Shuttle parmi plusieurs propositions. Knappi est maintenant le trait d’union entre les deux entreprises.
L’Open Shuttle est en service depuis quelques mois déjà. Quel est votre bilan ?
Dominik Huber : « Nous avons beaucoup travaillé avec l’Open Shuttle et notre expérience est positive. Au début, nous avons eu quelques problèmes à le positionner mais cela avait à voir avec le nouveau bâtiment. Mais ensemble, avec M. Schneider et avec vous, nous avons pu les résoudre rapidement. Depuis, nous sommes vraiment enthousiasmés par toutes les possibilités qu’il nous offre ».
Est-ce que vous changeriez quelque chose au projet ?
Stefan Schneider : « En ce qui nous concerne, oui. Tout s’est fait en même temps. L’emménagement dans le nouveau bâtiment, l’installation du système, la mise en service des machines et aussi celle du système KNAPP, le changement de la routine de commande, et le tout alors même que la production devrait continuer. On a vraiment traversé une phase difficile. La mise en service des presses d’injection s’est faite en même temps que la mise en service du VGA. On aurait pu gérer mieux le calendrier. Mais en ce qui concerne le déroulement du projet lui-même avec KNAPP, cela a bien fonctionné, des deux côtés ».
L’Open Shuttle est devenu le trait d’union entre les deux entreprises. On voit tous les jours comment il trace une droite reliant les deux zones.
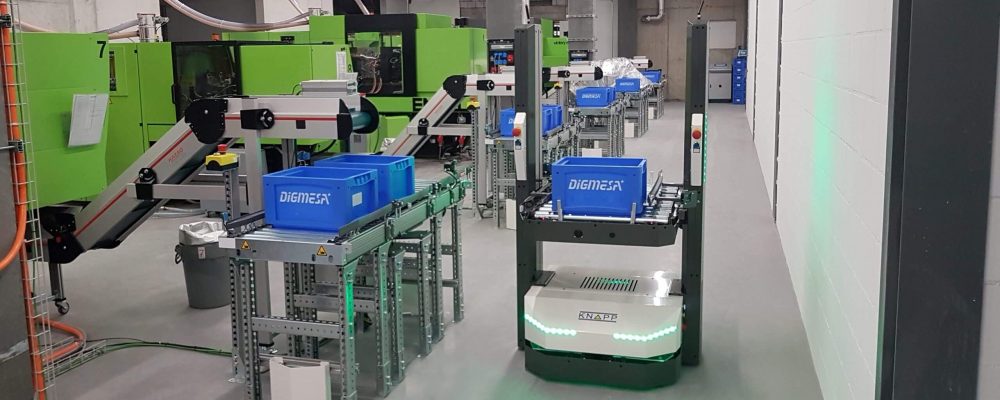
Quels sont vos projets pour l’avenir ?
Stefan Schneider : « En premier lieu, nous devons digérer et terminer le déménagement et l’intégration opérationnelle des deux entreprises. En termes de culture d’entreprise, il nous reste du travail. Cela concerne aussi l’amélioration de l’intégration technique et des processus. De plus, nous ressentons la pandémie très fortement. Tout le monde est en télétravail et s’est acheté au moins une nouvelle machine à café (il rit). Nos carnets de commandes sont bien remplis et il faut maintenant créer des capacités. Des capacités en ce qui concerne le moulage par injection mais aussi le montage. Nous avons prévu des investissements très élevés, rien que pour pouvoir faire face à cette demande. Nous voulons de plus continuer à faire évoluer notre entreprise, à être innovants et à développer de nouveaux produits ».
Dominik Huber : « Le regroupement des deux entreprises sur le site d’Ipsach et la connexion des productions grâce à l’Open Shuttle, c’était la première étape. Maintenant, l’intégration en termes de culture d’entreprise doit encore se dérouler sans encombre. Quels projets vont en découler et bien, l’avenir nous le dira ».
Voyez-vous d’autres possibilités d’application pour l’Open Shuttle dans votre entreprise ?
Stefan Schneider : « À vrai dire, j’ai bien quelques petites idées (il rit). Actuellement, le véhicule autoguidé apporte de manière automatisée les pièces dans l’entrepôt. Là, nous allons les chercher manuellement et nous les apportons à un automate. Il s’agit là encore d’un processus de transport d’un endroit clairement défini vers un lieu de réception clairement défini dont se charge actuellement un employé. Nous pourrions automatiser ce processus. Il y a sûrement un potentiel là ».