PC Electric ist eines der weltweit führenden Unternehmen im Bereich der Entwicklung und Produktion von Industriesteckvorrichtungen mit einer Exportquote von über 80%. Trotz umfangreicher Automatisierung in der Produktion erfolgte der Leerbehältertransport in den letzten 20 Jahren manuell. Um diesen Leerbehältertransport zu automatisieren, hat sich PCE für die Implementierung von Open Shuttles entschieden. Dafür wurde eigens ein spezielles Lastaufnahmemittel für den autonomen mobilen Roboter konstruiert. Die neue Automatisierungslösung mit FTS vereinfacht die Prozesse, das ergonomische Arbeiten und spielt Ressourcen für wertschöpfende Tätigkeiten frei.
Wir sprachen mit Daniel Lechner, Bereichsleiter Automatisierung und Tobias Aichinger, Abteilungsleiter PLC-Programmierung und Robotik, beide PC Electric (PCE), über die Entwicklungszusammenarbeit und die neue Lösung.
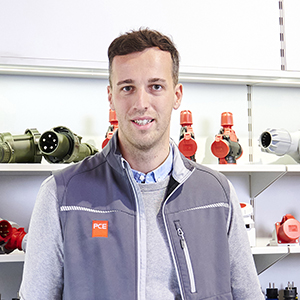
Bereichsleiter Automatisierung
PC Electric
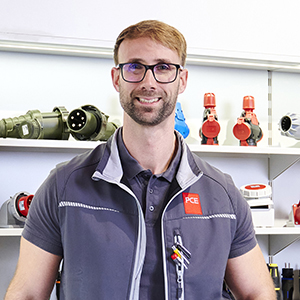
Abteilungsleiter PLC-Programmierung und Robotik
PC Electric
PC Electric setzt auf die Verbindung von Technik und Mensch
PC Electric ist ein österreichisches Unternehmen mit einem Sortiment von mehr als 22.000 Artikeln. Die Exportquote liegt bei über 80%. Was macht PC Electric weltweit so erfolgreich?
Lechner: Unser Erfolg liegt in der kurzen Durchlaufzeit von einer Woche in der Produktion. Das macht uns am Markt sehr stark. Die Stückzahlen sprechen für sich. Am Standort St. Martin in Oberösterreich produzieren wir mit eigenen hochautomatisierten Produktionsanlagen rund 700.000 Steckvorrichtungen pro Woche. Darunter fallen CEE-Steckvorrichtungen, Schuko-Artikel, Wandverteiler, also alles, was die Stromverteilung beinhaltet. Mit unseren Tochterfirmen an sechs weiteren Standorten verkaufen wir artverwandte Artikel. Österreich ist dabei zentraler Dreh- und Angelunkt. Auch die Forschung und Entwicklung sind hier angesiedelt.
Was ist die Strategie des Unternehmens? Was steht bei PC Electric im Fokus?
Aichinger: PCE ist ein familiengeführtes Unternehmen mit einer flachen Hierarchie. Wir haben sehr hohe Ansprüche an unsere Produktqualität. Ebenso liegt uns die Sicherheit der Mitarbeiter:innen sehr am Herzen. Ergonomisches Arbeiten steht immer im Fokus, genauso, wie wir jetzt vermehrt auf Nachhaltigkeit achten. Wir wollen Prozesse automatisieren, die Technik mit Menschen verheiraten und das Arbeiten angenehmer gestalten. Die eingesetzte Automatisierungslösung ist ein perfektes Beispiel für die Optimierung von schweren Tätigkeiten und den daraus resultierenden Benefits für die Mitarbeiter:innen.
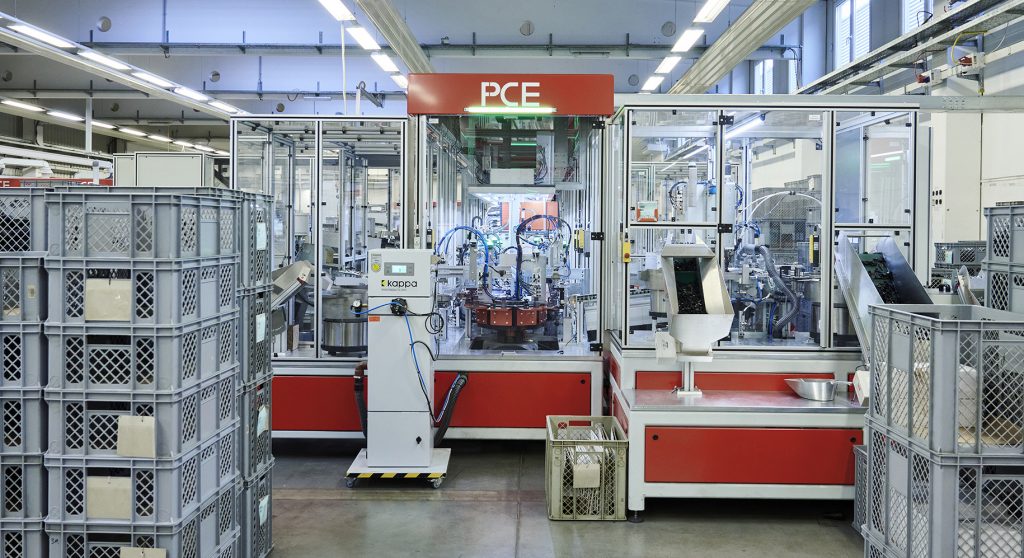
Open Shuttles als neue Automatisierungslösung: flexibel und platzsparend
Was waren die Herausforderungen in der Produktion, die eine neue Automatisierungslösung notwendig gemacht haben?
Lechner: In den letzten 20 Jahren wurde der Leerbehältertransport von der Verpackung retour in die Produktion nicht angepasst. Der Transport der Behälter erfolgte aufgrund der Gangbreite erst ab der Hälfte der Strecke mit einem Stapler. Auf der ersten Streckenhälfte mussten die Mitarbeiter:innen den Behälterstapel auf einer nicht elektrisch angetriebenen Rollenbahn weiterschieben. Das Auftragsvolumen ist jedoch deutlich gestiegen und beläuft sich aktuell auf 1.200 Boxen pro Tag. Man kann sich ausrechnen, wie hoch der Aufwand für den manuellen Transport der Behälter war.
Uns war es wichtig, den Prozess des Leerbehältertransports zu vereinfachen, ergonomisches Arbeiten voranzutreiben und Ressourcen freizuspielen. Darum haben wir den ganzen Transport optimiert, und in dem Fall mit KNAPP.
Sie haben sich dazu entschieden, den Leerbehältertransport mit den Open Shuttles abzuwickeln. Warum haben Sie sich für diese Lösung entschieden?
Lechner: Wir haben uns überlegt, wie wir den aufwändigen Prozess des Leerbehältertransports vereinfachen können. Auch über ein Förderband, das durch die ganze Montage geht, haben wir nachgedacht. Allerdings wachsen wir sehr schnell, die Hallen werden immer wieder neu gebaut und auch der Montagebereich wurde bereits gesiedelt. Aus diesen Gründen wäre ein Förderband zu unflexibel gewesen. Wir wollten eine flexible und platzsparende Automatisierungslösung für die Zukunft.
Automatisierungslösung mit FTS - Übersicht der Lösung
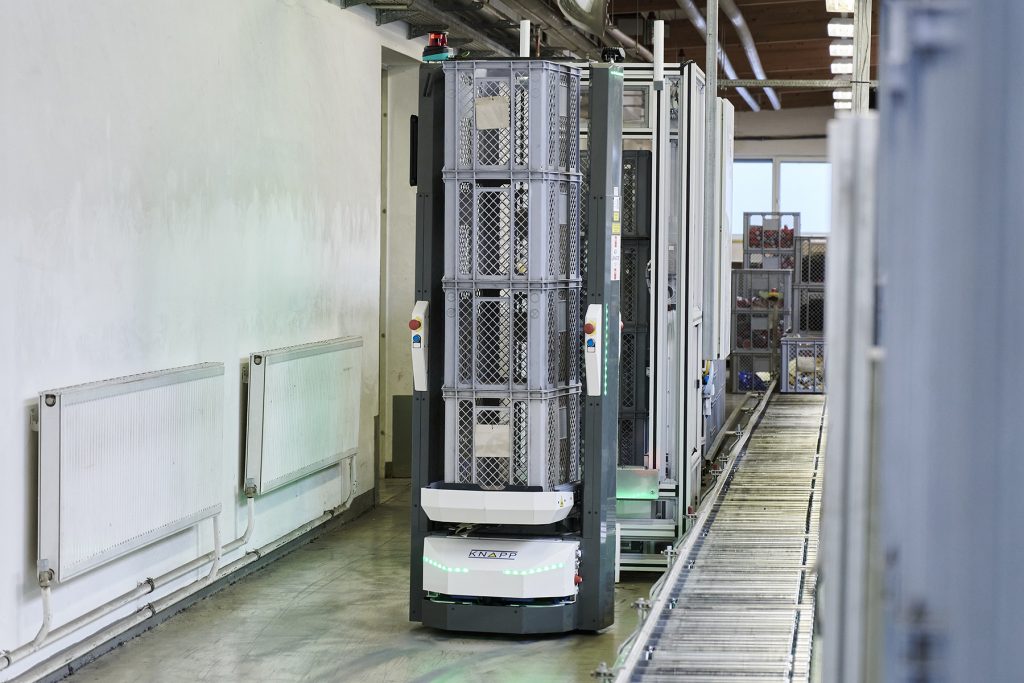
Entwicklungspartnerschaft für optimale interne Transporte
Das neue fahrerlose Transportsystem bietet Ihnen nun ein hohes Maß an Flexibilität. Sie haben die Möglichkeit, das System permanent zu erweitern und auch neue Prozesse einfach und selbst hinzuzufügen. Darüber hinaus wurde in enger Entwicklungszusammenarbeit eine eigene Lösung für den Leerbehältertransport konstruiert. Wie sieht diese aus?
Lechner: Die Entwicklungsabteilungen von KNAPP und PCE haben bei diesem Automatisierungsprojekt eng zusammengearbeitet. Für den Leerbehältertransport wurde ein spezielles Lastaufnahmemittel (LAM) mit Kippschutzvorrichtung für das Open Shuttle entwickelt. Damit kann der autonome mobile Roboter Leerbehälter bis zu einer Höhe von 1,6 m gestapelt transportieren.
Wie läuft die neue Lösung mit dem Open Shuttle? Wie zufrieden sind Sie mit dem neuen System?
Aichinger: Der Prozess ist sehr stabil. Bei der Inbetriebnahme wurde der Prozess laufend optimiert und es sind regelmäßige Updates eingeflossen. Jetzt sind wir an einem Punkt, an dem wir sagen können, dass es ein sehr gutes System ist. Unsere Herausforderung liegt jetzt mehr darin, wie wir noch weitere oder andere Prozesse mit KNAPP realisieren können.
Lechner: Wir haben gesagt: Machen wir ein Leuchtturm-Projekt, wo wir alles gut abstecken und nicht viele Einflussfaktoren von der Umwelt kommen können. Der Transport der Leerbehälter war perfekt, weil die Boxen von A nach B befördert werden mussten. Es war einfach, die Strecke war überschaubar und die Gangbreiten waren vorhanden. Wir haben das System mit einem Shuttle erfolgreich getestet. Das zweite ist bereits geordert und zukünftig werden es wahrscheinlich noch mehr werden.
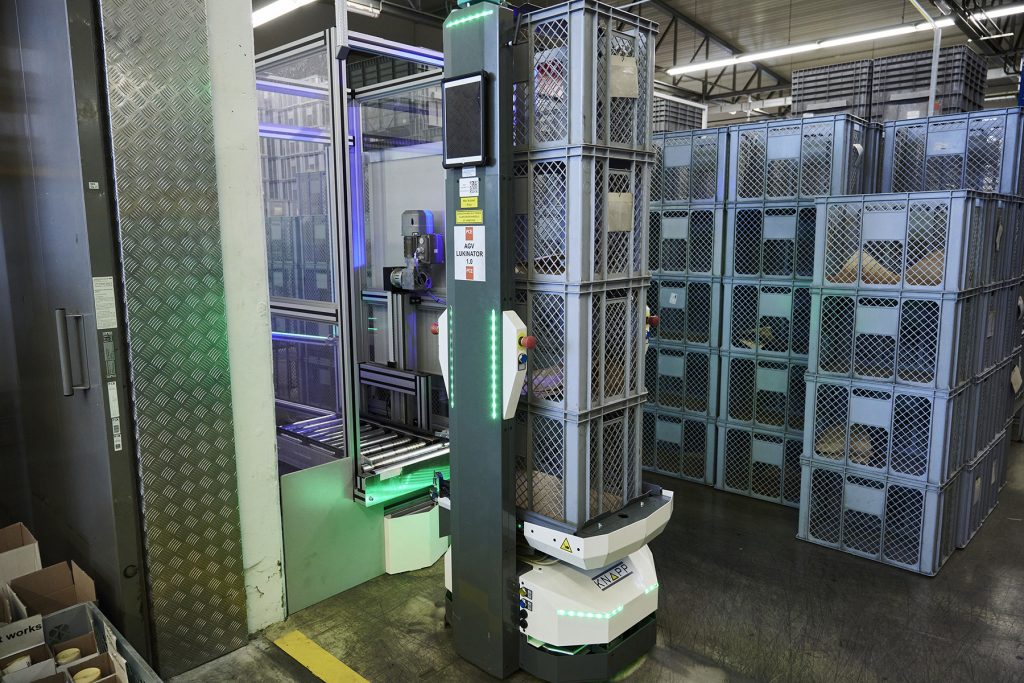
Eine Automatisierungslösung mit FTS für das große Ganze
Es gibt viele Anbieter von fahrerlosen Transportsystemen am Markt. Warum hat sich PCE für ein Logistiksystem von KNAPP entschieden?
Lechner: Der große Vorteil war, dass man bei KNAPP das große Ganze gesehen hat. Shuttlesysteme von Startups findet man überall, aber diese Unternehmen verkaufen nur das Shuttle ohne Support und ohne Lösung. Das ist für uns nicht der richtige Ansatz. Wenn man ein Shuttle installiert, hat man keine Erfahrung, was funktioniert und was nicht. Wir wollten eine renommierte Firma mit gutem Service. Bei KNAPP haben wir alle Informationen erhalten, die wir gebraucht haben. Die Zusammenarbeit hat bestens funktioniert. Wir haben von Beginn an auf einer gemeinsamen technischen Ebene kommuniziert. Und nur so kommt man zu richtig guten Lösungen. Aus diesem Grund haben wir dann die Entscheidung getroffen, dass KNAPP der richtige Partner für die Umsetzung der Lösung ist.
Für uns war es wichtig einen Partner zu haben, auf den wir uns auch nach Projektabschluss verlassen können. KNAPP ist eine renommierte Firma, die uns Stabilität und Sicherheit gibt.
Wie würden sie die Zusammenarbeit mit KNAPP beschreiben? Wie war der Projektablauf?
Lechner: Man hat gemerkt, dass wirklich ein Projektmanagement dahinter steht. Wir hatten einen Ansprechpartner und es war klar definiert, an wen wir uns wenden müssen. Es ist ein großer Vorteil, wenn Prozesse und Schnittstellen klar definiert sind. Sicher hat es da und dort ein paar Komplikationen geben, aber wir sind nie im Stich gelassen worden. Bei einem Projekt zählen schlussendlich der Erfolg und die Leistung.
Aichinger: Service, Betreuung und Support sind bei KNAPP auf jeden Fall umfangreich vorhanden und wir sind sehr zufrieden.
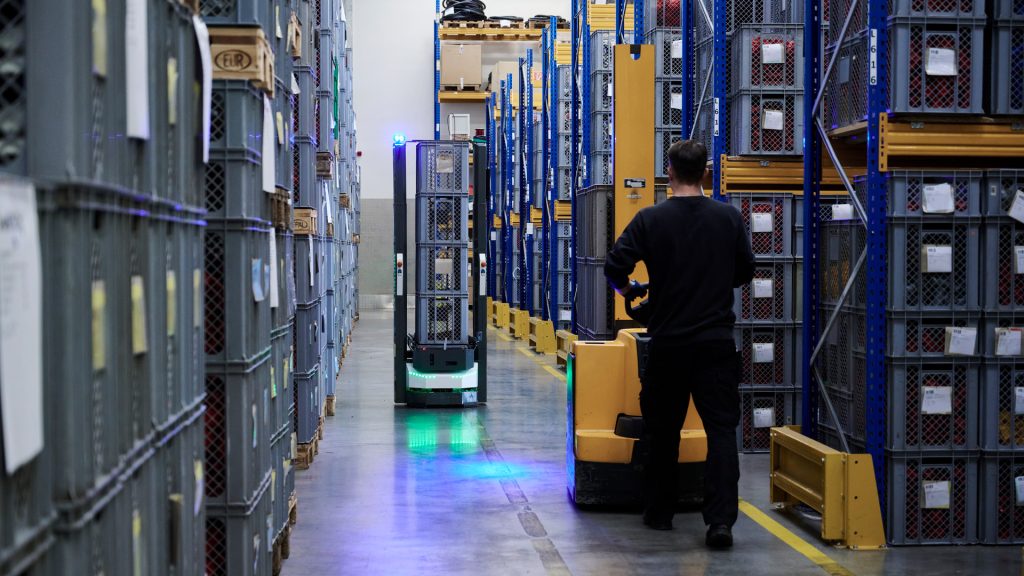
Weiterführende Leseempfehlungen


Digmesa, Hersteller von Durchflussmessern, automatisiert die Produktionsversorgung mit Open Shuttles. Erfahren Sie mehr über die flexible Lösung im Interview mit den Geschäftsführern der Digmesa-Gruppe.

Gerade in Zeiten wie diesen, spielt die Versorgung eine wichtige Rolle. Welche Trends und Marktentwicklungen beeinflussen die produzierende Industrie? Wie kann auf diese Herausforderungen reagiert werden? Im ersten Teil des Beitrages „Intelligente Produktionsversorgung“ gehen wir genau darauf ein.