Terberg: Shuttle-Lagersystem als hocheffiziente Lösung zur Produktionsversorgung
Terberg Benschop ist Spezialist für den Bau von Terminal-, RoRo- und Werfttraktoren sowie ähnlichen Fahrzeugen. Der Familienbetrieb ist weltweit in über 100 Ländern im Einsatz und setzt als Trendsetter im Nischenmarkt auf ständige Weiterentwicklung und Innovation. Um eine höhere Anzahl an Aufträgen mit mehr Effizienz und Flexibilität abarbeiten zu können, installierte Terberg ein Shuttle-Lagersystem.
Die neue Lösung dient der automatischen Versorgung von Arbeitsplätzen und Fertigungslinien. Sie wurde im laufenden Betrieb umgesetzt und schafft die Basis für ein künftiges Unternehmenswachstum.
25.000 Stellplätze
Steuerung der Lösung
Sie sehen gerade einen Platzhalterinhalt von YouTube. Um auf den eigentlichen Inhalt zuzugreifen, klicken Sie auf die Schaltfläche unten. Bitte beachten Sie, dass dabei Daten an Drittanbieter weitergegeben werden.
Mehr InformationenAutomatisches Kleinteilelager schafft mehr Lagerkapazität
Um eine höhere Anzahl an Aufträgen mit mehr Effizienz und Flexibilität abarbeiten zu können, war es für Terberg notwendig, das Produktionslager für den Karosseriebau und die Linienversorgung der Fahrzeugmontage sowie das weltweite Ersatzteillager in einem neuen Gebäude zu zentralisieren. Die im vorhandenen Palettenhochregallager gelagerten Kleinteile mussten in ein neues automatisiertes Kleinteilelager (AKL) siedeln, um mehr Platz für Großteile zu bekommen. Diese Herausforderung musste im laufenden Betrieb, ohne Unterbrechung der Produktion, umgesetzt werden. Terberg entschied sich für ein Shuttle-Lagersystem in Kombination mit ergonomischen Arbeitsplätzen, die mit einem Pick-to-Light System ausgestattet sind.
Die Anforderungen von Terberg an die Lösung
Für Terberg war die Entscheidung für eine automatisierte Lösung ein großer Schritt. Uns war die Zusammenarbeit mit einem Lieferanten wichtig, dessen Systeme sich bereits weltweit bewährt haben, der aber auch lokale Unterstützung und Wartung anbietet.
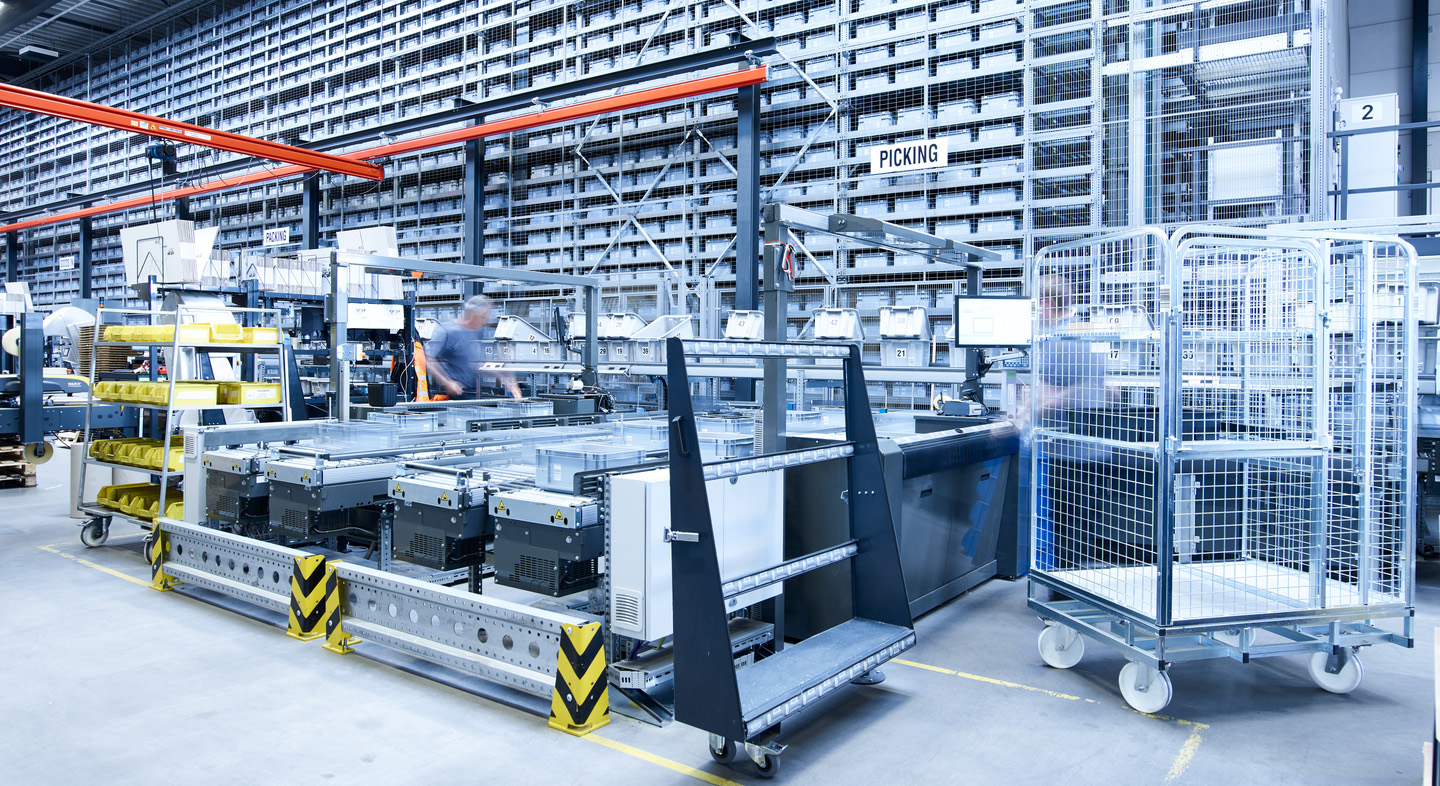
OSR Shuttle: Maximale Effizienz & Flexibilität
Basierend auf den Rahmenbedingungen wurde eine flexible, automatisierte Lösung umgesetzt, die Terberg höchste Verfügbarkeit in der Produktion ihrer Fahrzeuge ermöglicht und ein künftiges Wachstum sicherstellt. Herzstück ist das Shuttle Lagersystem OSR Shuttle, das unterschiedliche logistische Anforderungen höchsteffizient abwickelt.
Das AKL ist direkt an den Wareneingang, den Versand und der Qualitätskontrolle angebunden. An den Arbeitsplätzen werden die einzelnen Artikel im Ware-zur-Person-Prinzip in ergonomischer Höhe zugeführt. Der Kommissionierbereich besteht aus zwei multifunktionalen Pick-it-Easy-Arbeitsstationen. Hier erfolgt die Kommissionierung in Kanban-Regalen, in Rollcontainern und die Ersatzteilkommissionierung. Im Hintergrund sorgt die Softwarelösung KiSoft One mit Webservices Schnittstelle zum Kundensystem für einen reibungslosen Ablauf.
Einblicke in die Lösung von Terberg
Die neue Automatisierungslösung ist seit 2019 bei Terberg Benschop in Betrieb und sichert Kapazität und Leistung bis 2027. Ausschlaggebend ist ein skalierbares und flexibles System, das Arbeitsplätze und Fertigungslinien vollautomatisch versorgt.
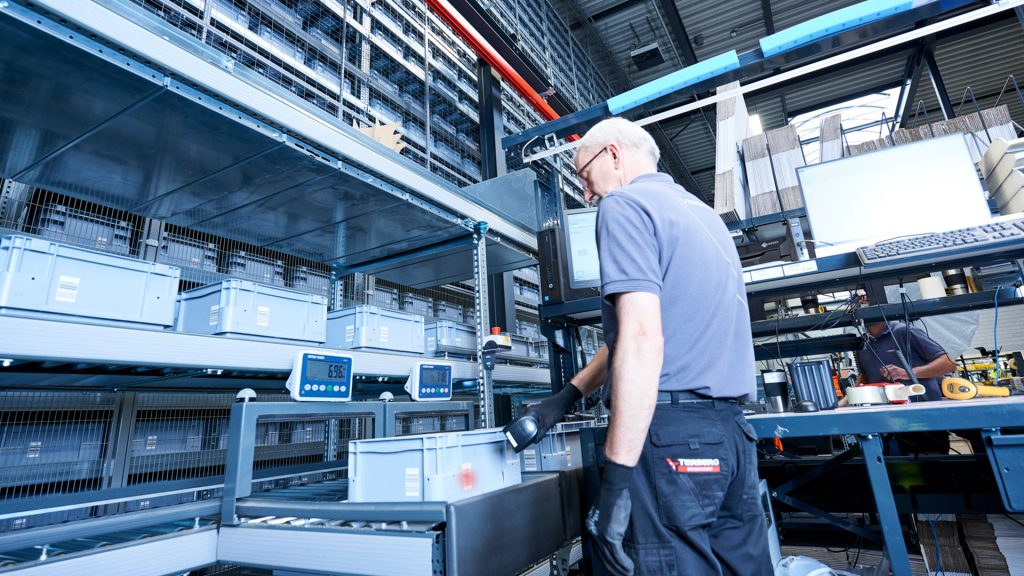
1 I Wareneingang
Vor der Einlagerung in das OSR Shuttle werden die Waren an Decanting-Arbeitsplätzen umgepackt. Die Mitarbeiter:innen identifizieren die einzelnen Artikel im Kundensystem und senden damit eine Aviso-Information an die Software KiSoft. Je nach einzulagernder Ware stehen 2 Behältergrößen zur Verfügung. Um einen effizienten Kommissionierprozess zu sichern, gibt KiSoft dem Personal an der Station die passende Behältergröße vor. Um das maximal zulässige Gewicht von 50 kg pro Behälter zu kontrollieren, sind die Decanting-Arbeitsplätze mit einer Kontrollwaage ausgestattet. Bei der Einlagerung wird eine maximale Last pro Kanal berücksichtigt und eine ABC-Einlagerungsstrategie verfolgt.
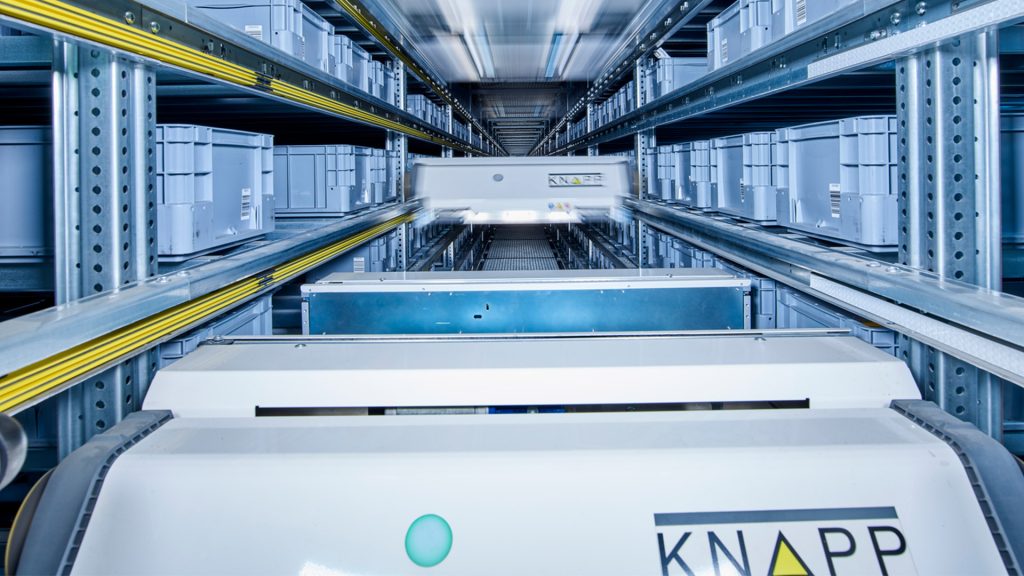
2 I Auftragsstart und Lagerung
Die Aufträge werden von Terbergs Kundensystem priorisiert und sortiert an KiSoft weitergegeben. Dadurch können Aufträge für Ersatzteile mit früherem Versandzeitpunkt vorgereiht und zügig abgearbeitet werden. Alle Kleinteile lagern zentral im OSR Shuttle und werden ausgelagert, wenn diese an der Produktionslinie benötigt oder als Ersatzteile versendet werden. Durch die dynamische bis zur vierfach-tiefe Lagerung, ergibt sich eine Lagerkapazität von 14.250 Stellplätzen bei 600*400 mm Behältern bzw. 28.500 Stellplätzen bei 400×300 mm Behältern.

3 I Ware-zur-Person-Kommissionierung
Der Kommissionierbereich besteht aus zwei Pick-it-Easy-Arbeitsstationen und erfolgt im Ware-zur-Person-Prinzip. Die Behälter mit den benötigten Teilen werden vom OSR Shuttle ausgelagert und an den Arbeitsplätzen in ergonomischer Höhe zur Verfügung gestellt. Ein Pick-to-Light-System unterstützt die Mitarbeiter:innen bei der Kommissionierung. An den Arbeitsplätzen werden drei Arten der Kommissionierung durchgeführt: die Kommissionierung in Kanban Regalen und Rollcontainern und Ersatzteilkommissionierung.
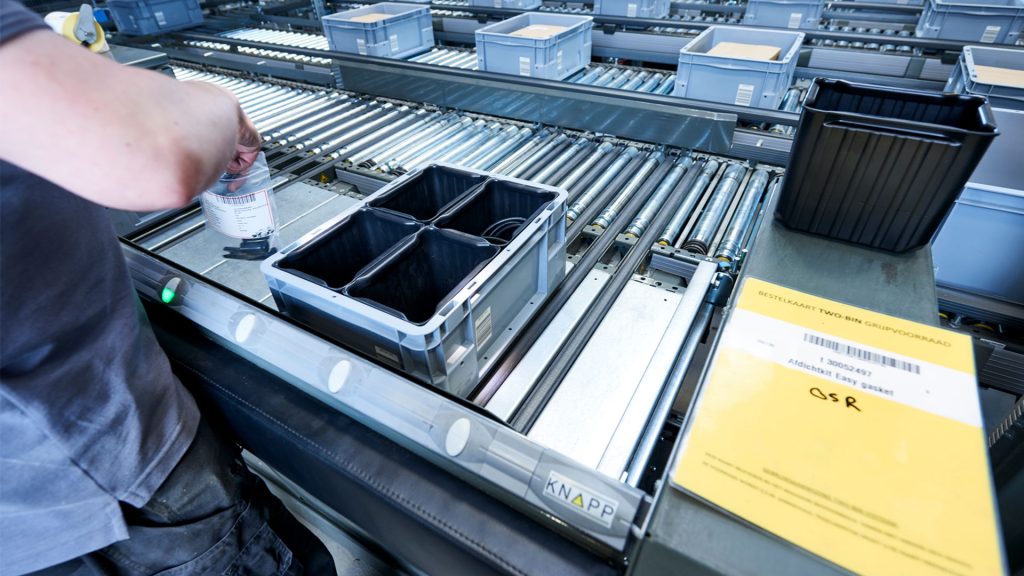
4 I Ersatzteilkommissionierung
Hier werden Ersatzteile für den direkten Versand kommissioniert. Die Pick-to-Light-Anzeigen informieren den:die Mitarbeiter:in, welche und wie viele Stück aus den Quellbehältern entnommen werden müssen. Nach Abschluss des Kommissionierauftrags wird ein Versandlabel gedruckt und aufgeklebt. Danach wird der Behälter automatisch in den Versandbereich transportiert. Die Quellbehälter werden vor der Einlagerung automatisch verwogen und mit dem aktualisierten Gewicht in das OSR Shuttle eingelagert.
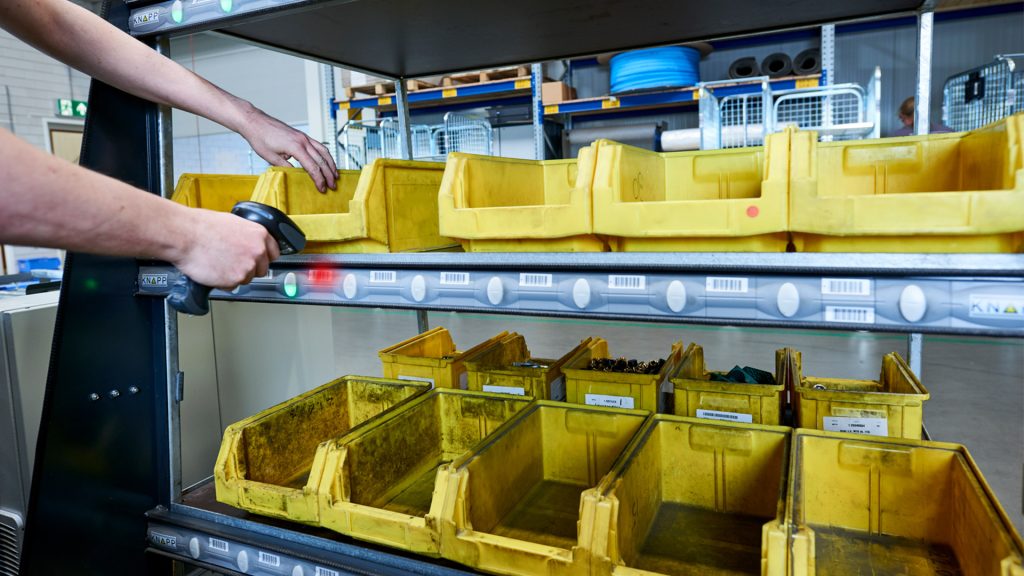
5 I Kommissionierung in Kanban-Regal
Für das Bestücken von Kanban-Regalen, die für die Montage und Produktion benötigt werden, steht ein spezieller Kommissioniermodus zur Verfügung. Das Kanban-Regal wird dazu hinter ein spezielles Gestell mit Pick-to-Light-Anzeigen positioniert. Die Pick-to-Light-Anzeigen führen das Personal durch die Kommissionierung. Sind alle Aufträge auf einer Seite des Regals abgearbeitet, dreht der:die Mitarbeiter:in das Regal und bestückt die andere Seite des Kanban-Regals nach Vorgabe. Nach Befüllung des Regals wird es wieder an die Montage- und Produktionslinie transportiert.
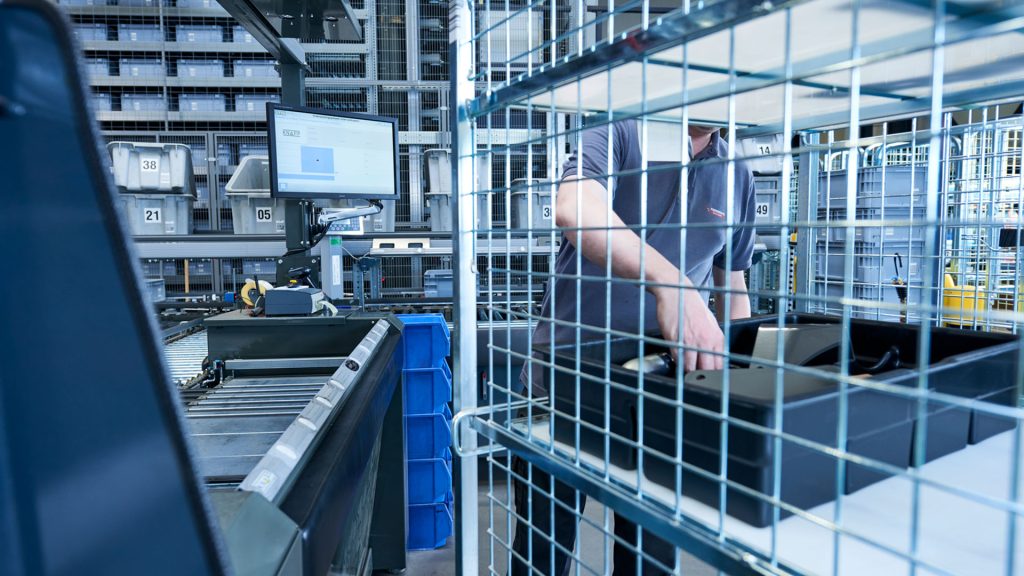
6 I Kommissionierung in Rollcontainer
Artikel, die an der Montage- und Produktionslinie benötigt werden, werden manuell in Rollcontainer kommissioniert. Mitarbeiter:innen bringen diese Rollcontainer anschließend in andere Lagerbereiche, um weitere Großartikel hinzuzufügen oder direkt zur Montage- und Produktionslinie.
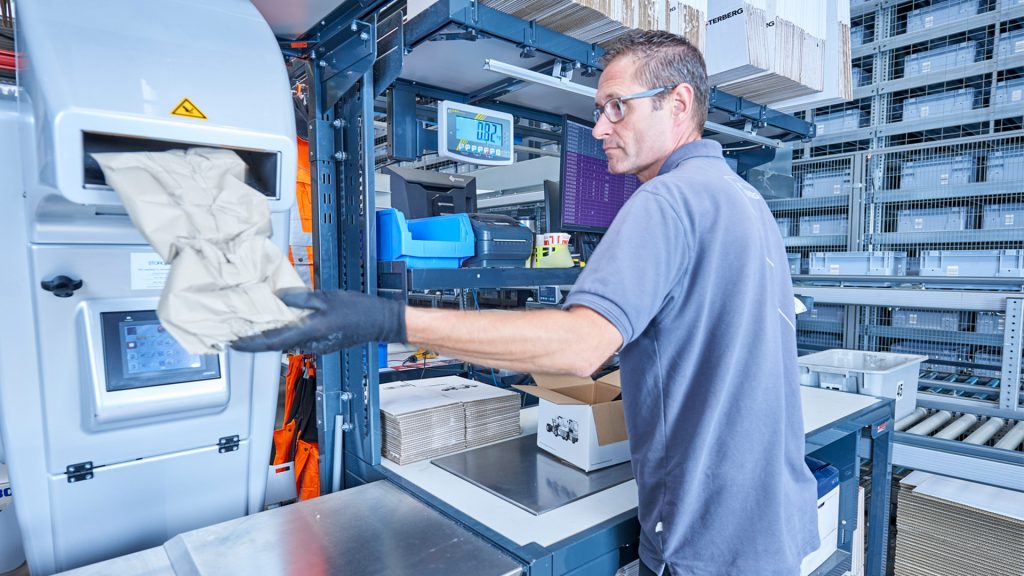
7 I Versand für Ersatzteile
Sobald die Ersatzteilkommissionierung abgeschlossen ist, werden die Ersatzteilaufträge in den Verpackungsbereich überführt. Kleinteile aus dem OSR Shuttle sowie größere Teile aus dem Hochregallager werden hier zusammengeführt und zum Versand vorbereitet. Dafür stehen zwei Versandarbeitsplätze inklusive Verpackungsmaschinen zur Verfügung. Die verpackten Teile werden auf eine Palette gelegt und manuell von einem Stapler zum LKW transportiert.
Das Ware-zur-Person-System bietet natürlich eine höhere Kapazität, weil die Wegzeiten im Lager wegfallen. Weitere Vorteile sind die Unterstützung des Personals durch das Pick-to-Light-System, wodurch Fehler bei Art und Stückzahl der Artikel vermieden werden. Auch kann das FIFO-Prinzip besser umgesetzt werden, weil eingehende Ware immer in einem neuen leeren Behälter eingelagert wird.
Vorteile: Shuttle-Lagersystem für Terberg
Einfachheit und Flexibilität
Die neue Lösung, eine Kombination aus automatischem Kleinteilelager und ergonomischen Arbeitsplätzen, ermöglicht eine effiziente Bearbeitung der gestiegenen Auftragszahlen. An den multifunktionalen Pick-it-Easy-Arbeitsplätzen können flexibel verschiedene Kommissionierarten abgewickelt werden. Ein Pick-to-Light-System und die easyUse-Benutzeroberfläche der Software unterstützen das Personal bei der Kommissionierung.
Erweiterbarkeit
Das OSR Shuttle ist ideal für Hochleistungsanwendungen und ermöglicht auch ein zukünftiges Wachstum. Das Lager ist in Größe, Leistung und Funktion skalierbar. Ebenso können Arbeitsplätze nach Bedarf hinzugefügt werden. Die Lösung wächst mit den Anforderungen mit.
Maßgeschneidert
Basierend auf den Anforderungen von Terberg, wurde eine maßgeschneiderte Lösung realisiert, die dem Unternehmen höchste Verfügbarkeit in der Produktion ihrer Fahrzeuge ermöglicht. Dazu gehört auch die sequenzierte Bereitstellung von konsolidierten Teilen in der Produktion, die Möglichkeit der Kommissionierung in Kanban-Regale und eine speziell für den Kunden entwickelte Lösung zur Lagerplatzoptimierung.